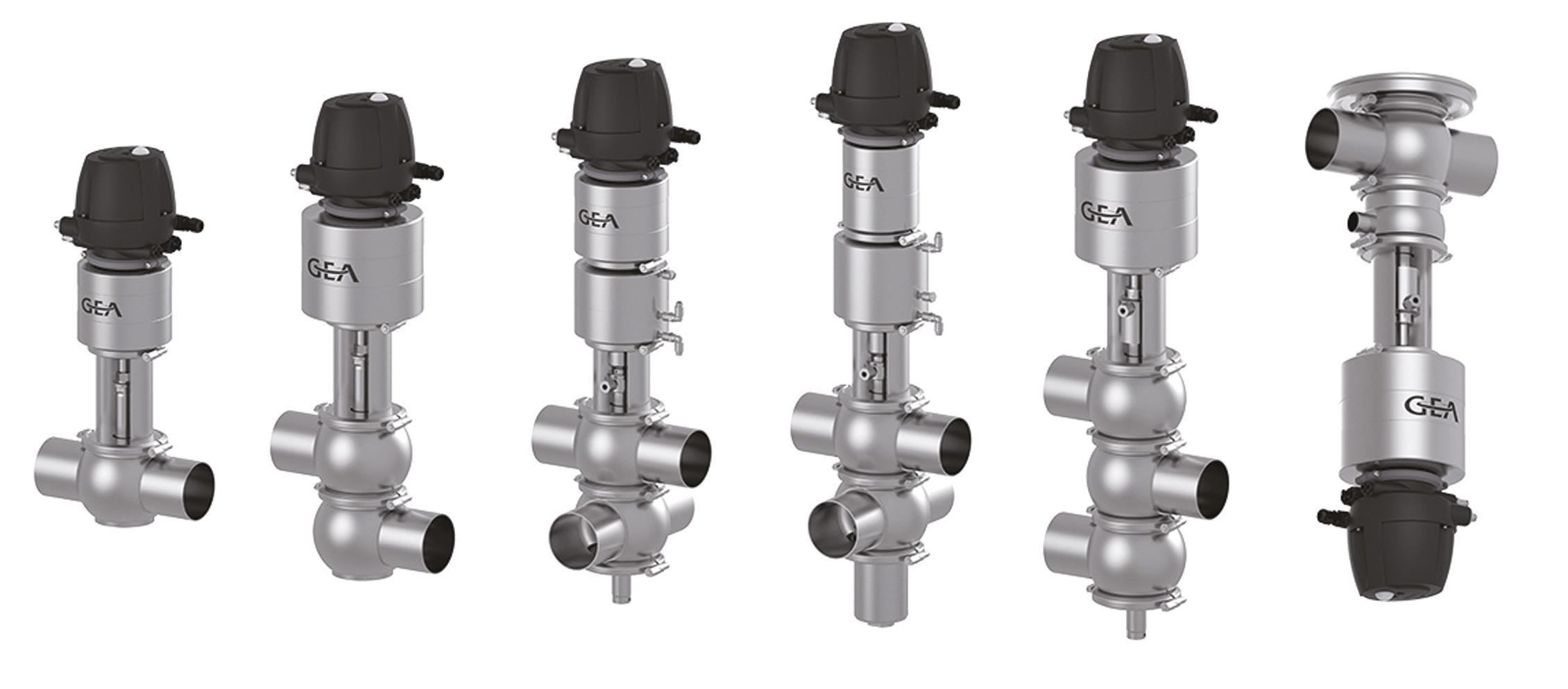
3 minute read
How to secure a stable but adaptable plant operation
For process operators, changes in the use of their plant entails greater failure and error risk. GEA’s Varivent valve portfolio ensures stable plant operation with robust technology, efficient automation and well-positioned service, supporting important production sectors like the food, dairy and beverage industries.
Hygienic valves control liquid processes at all process stages, and are utilised by the dozens found in valve blocks for filling, emptying and cleaning tank farms.
GEA's new valve design is well-known for its ability to withstand loads beyond the stresses of everyday use.
An equally robust, FEM-optimised sealing concept ensures the hygienic safety of valve technology, even under heavy-duty use, and during food and beverage processing. The innovative shape of the groove in the valve disk gives the seals a precise hold during switching operations, also in the event of high-pressure differences. The metallic stop ensures a defined deformation. This means that the seal remains reliable over exceptionally long service periods.
The added robustness pays off when established operating procedures are restricted or skilled workers are not available to the usual extent, as may be the case during a pandemic. “The care we invested in the technology concept from the outset is bringing stability where it is needed most,” explains Annika Burmeister, product manager for hygienic valves.
EASY ADAPTATION OF PROCESSES AND CAPACITIES
While recipe changes are often the order of the day in liquid processes, batch cycles are currently adjusted with some frequency, owing to crisis-related supply or delivery bottlenecks. With the standard automatic control of all Varivent valves, changes in the process programme are simple and safe. The valves are connected via their standardised digital control top to the central process control system, which coordinates all opening and closing operations according to the selected programme. Fail-safe monitoring is ensured by the novel feedback technology built into GEA’s current control top models. If a control top has to be reconfigured for this purpose, factory personnel can do this without special training. With the latest models, a push of a button is all that is needed.
“Users that harness the possibilities offered by valve automation are better prepared to cope with changes as well as for tomorrow,” Bernd Porath, product manager for valve automation technology sums up. “The digital, network-enhanced future of processing plants has already begun. Our technology provides users with the security and efficiency that is now increasingly essential.”
PRECISE RETROFITTING AND EXPANSION
If the plant is to be converted or expanded so that it can continue to serve its purpose or meet changed objectives, GEA’s Varivent modular system holds the key. Just over a million configuration options ensure exactly the right equipment or upgrade options to optimally support stable operations. Existing valve units and entire valve blocks can be retrofitted with precision to meet future process tasks by replacing individual components.
If, for example, a company aims for a stronger position in terms of sustainability, the Leff technology (Low Emission Flip Flop) in the latest valve control tops can save up to 90% of clean-in-place media. Other components in the GEA portfolio support substantial water and energy saving. The Varicover system is based on the valve concept, which recovers valuable product residues from piping and minimises the amount of rinsing water for pipe cleaning.
MANUFACTURING QUALITY & ONGOING PROGRESS
Varivent users gain security for their operations not least thanks to the exceptional manufacturing quality of each valve. All valves in the GEA's premium family are manufactured exclusively at the GEA plant near Hamburg, Germany where the mix proof double-seat valve was invented more than 50 years ago. It still represents the foundation for mix proof process valve technology today. Besides, the GEA Varivent family has decisively driven progress with the introduction of the first mix-proof valves in PMO-certified design for the US market. •
GEA – www.gea.com