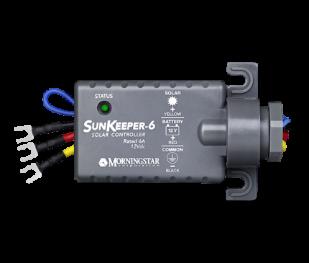
8 minute read
Morningstar solar controllers for protecting oil & gas operations and making mining operations safer
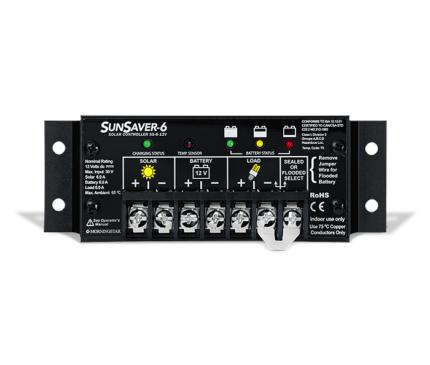
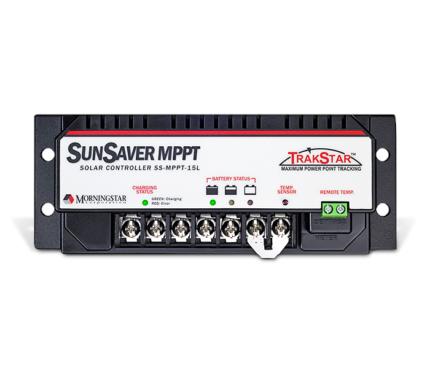
Advertisement
The fossil-fuel industry, particularly oil and gas, depends on the renewable energy industry for many aspects of extraction, production and transportation. Pumping and mining operations are often far removed from access to the electrical grid, and using generators is often prohibitively expensive and impractical. At the well, renewables are called upon to power injection pumps, lighting equipment, and monitoring devices. Along the pipeline, renewables are often the only means of providing cathodic protection to prevent corrosion and ensure pipeline integrity. Renewable energy provides costeffective, dependable electricity for mission-critical communications, data acquisition, metering, site security, and much more.
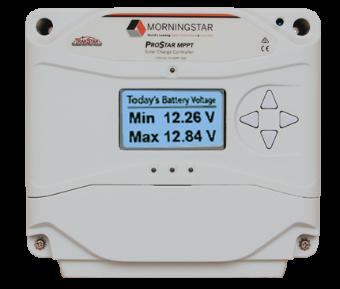
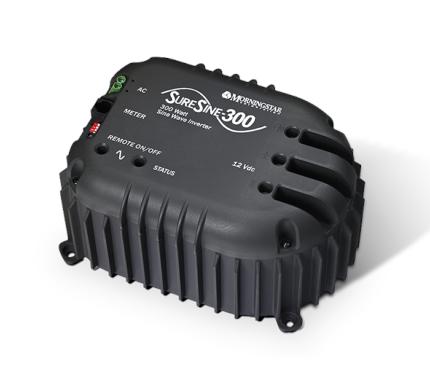
Cathodic protection is primarily used to protect steel structures buried in soil or immersed in water and offers many advantages for corrosion protection. Electronic cathodic protection must maintain constant voltage and current to be effective. Therefore, it is important for these sites to maintain good charging control and communications typically via satellite or other wireless communications.
In mining, many of the same conditions apply. Far removed from grid electricity, mines require on-site electrical generation for critical safety systems and security systems. Often this electrical demand is on top of the already high power-consumption of an operating mine, which also has to take heavy mining,
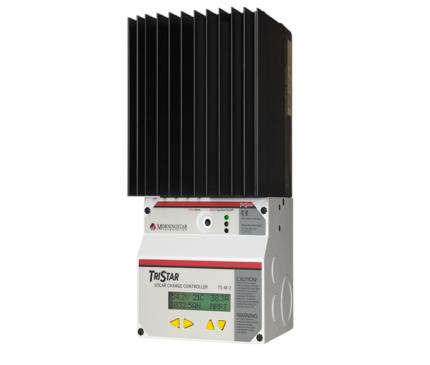
transportation and ventilation equipment into account. Solar electric-powered lighting towers are increasingly used to provide power generation for dispatch, data networks, data and lighting. For on-site lighting, mining operations often use mobile light trailer towers with high efficiency LED spotlights powered by batteries recharged with solar panels and sometimes a wind turbine-powered generator. The “heart and brains” of these solar electric systems is its solar controller. The solar controller provides proper battery charging, which will fully charge the batteries during the day while also protecting the battery, often the most expensive component, from overcharging.
By controlling the PV/solargenerated DC electricity flowing from the panels, or modules, into batteries for storage as well as sending on to run connected loads, the controller both manages the delivery and quality of the solar-produced electricity and maintains battery health. These controllers must operate in extreme high or low temperatures. Morningstar’s SunSaver, ProStar and TriStar families of solar controllers have all been used with off-grid cathodic protection systems. Higher power systems may utilize multiple TriStar or TriStar MPPT controllers in parallel to charge the battery bank. Cathod ic protection and lighting load control can include products from other manufacturers to provide constant voltage and/or constant current. These power supplies therefore can include DC-DC load control which may cause high current surges at times. Therefore, it is important to consider carefully whether Morningstar’s load control circuit can handle the type of surge capability for these loads. If the load current capability cannot meet the inrush current requirement for the load, Morningstar offers a Relay Driver to activate higher rated relays for LVD load control.
Communications for these sites to monitor not only the solar controller data but also the equipment data is critical. If the system shuts down, immediate intervention can prevent losses, downtime and damage. Morningstar offers both serial and Ethernet communications using industry standard MODBUS™ protocol with many different solar controllers including the ProStar and TriStar families as well as the Relay Driver. These systems often include an RTU with a MODBUS™ interface which is controlled and monitored by a central SCADA system. The RTU equipment at these sights will all be powered by the solar controllers which makes it even more critical to maintain power at these remote sites.
Selected Morningstar components are now also SNMP-compatible (Simple Network Management Protocol), an internet standard protocol that is used to manage and monitor devices on an IP network. SNMP is used in industrial applications within an existing network infrastructure, as an easy way to gather data from and accurately monitor network equipment assets on site. SNMP allows for a simple and convenient way to view and modify the status of critical system components on a private Local Area Network (LAN) or across a WAN (Wide Area Network) if so desired. Morningstar’s SNMP-enabled Ethernet MeterBus Converter EMC-1 provides this capability. Morningstar solar controllers offer unmatched reliability; reducing or even eliminating field-failure and downtime, and the need for difficult and costly replacements in remote locations. Because charge controllers handle high voltages they produce heat, which means thermal management is essential to prolonging system life. For this reason Morningstar has the industry’s broadest line of fanless charge controllers, including models that meet all US and International requirements for hazardous locations. The superior ‘fanless’ thermal design means no fans to fail, waste electricity, or shorten the life of the controller by blowing in dirt and debris. Both the SunSaver and SunKeeper charge controllers are approved for hazardous locations, meeting Class 1/ Division 2 Groups A-D requirements, and are ideal for use in oil & gas operations.
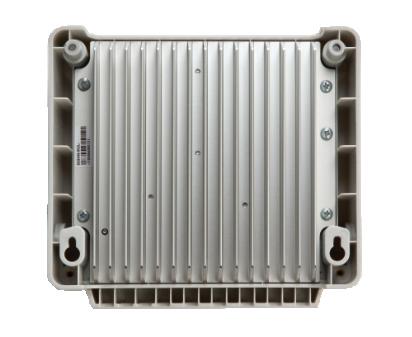
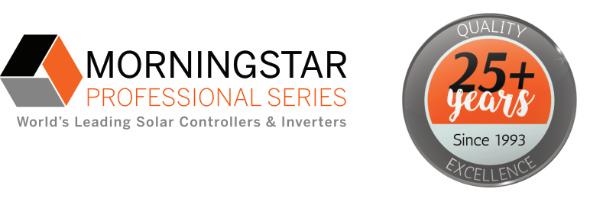
Quality Control and Risk Management
Australian headquartered online technology company Real Time Instruments (RTI) believes that strong demand for their AllScan Online PGNAA Analyser reflects a renewed focus on quality and processing efficiency by the mining and mineral processing sector. The AllScan is a newgeneration online elemental analyser that uses PGNAA (prompt gamma neutron activation analysis) technology to accurately measure the chemical composition of most bulk materials. The analyser combines practical operational features with sophisticated hardware and software resulting in an analyser that is easy to install,
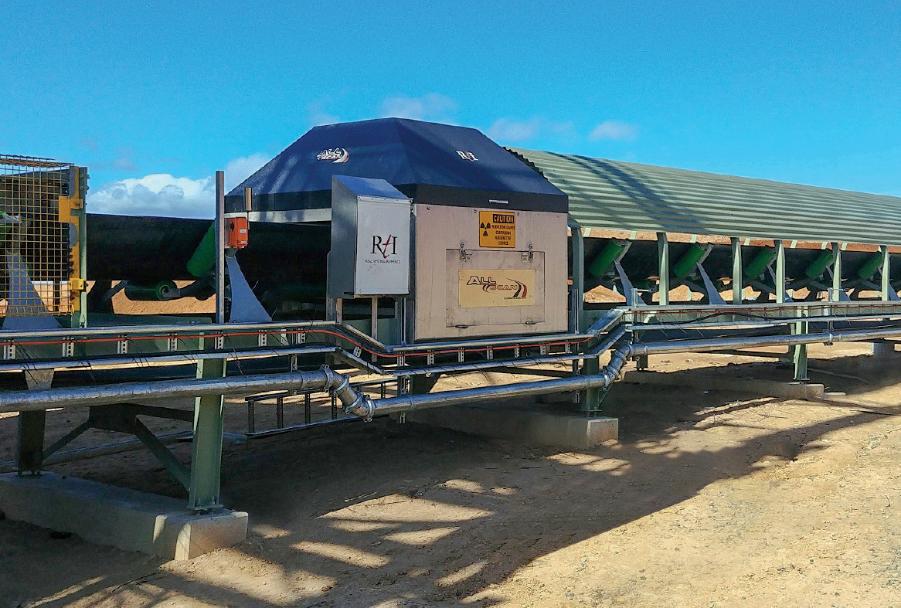
calibrate, and maintain, and above all, is extremely accurate.
CEO James Asbury said that “over the last few years demand for the AllScan has escalated, particularly in the coal, iron ore, bauxite, cement and copper industries. We’ve sold, installed and commissioned analysers in many countries including Australia, Mozambique, Guinea, USA, DRC, India, Brazil, Kenya, China, and Chile.”
According to the World Economic Forum (2017), more and more industries are searching for ways to use resources more responsibly through careful control and monitoring of ore grade quality. Some initiatives focusing on optimising resource utilisation and social responsibility as a key drivers and others due to stricter ore quality requirements. Reason being, poor ore quality has a negative impact on emissions when it is converted for example iron ore into steel or coal into electricity, etc.
More than 20 analysers have been purchased by the iron ore industry for a variety of quality control and processing efficiency purposes. For example, analysers have been installed on the ROM belt to monitor the iron content and overall quality of the ore direct from the mine.
Others have been installed
primarily to monitor the performance of the desanding modules in filtering and removing gangue material. The majority, however, have been installed on belts feeding stockpiles to facilitate sorting and blending and to provide an accurate determination of iron content in the final product.
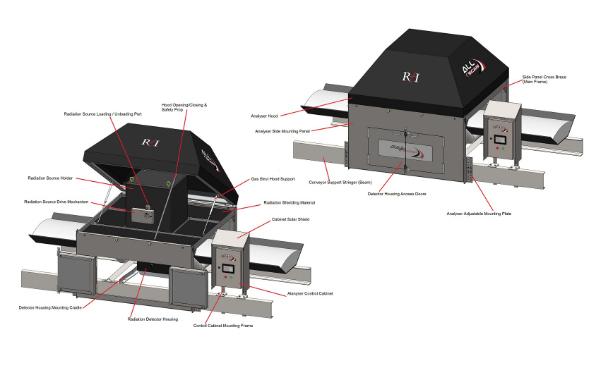
The cement industry has also purchased many analysers recently. There are two main applications for PGNAA technology in cement production. The AllScan is used in stockpile management to improve pre-blending performance through better utilisation of quarry materials. The AllScan is typically installed on the conveyor between the crusher and the stockpile. The AllScan continuously reports the elemental composition of the material on the conveyor belt. This information is used to keep track of the pile build-up and may optionally be used to direct haul trucks to different sections of the quarry in order to best exploit the quarry. The online data from the AllScan is used to build homogenous stockpiles with a lower variation in chemistry. Another application for the AllScan in cement is to optimize the feed to the Raw Mill. The analyser is used in conjunction with raw mill quality control software and placed on the conveyor downstream of the feeders and upstream of the raw mill. Data from the AllScan is used to reduce the variability in the raw mix product, and ultimately the kiln feed.
Over 40 AllScan analysers have recently been utilised in the coal and power industries in various countries. RTI has installed the AllScan at various locations along the coal value-chain from at the mine, at the preparation plant, transhipment points, and at the end-user including coal fired power stations. Collectively, the analysers are used for various purposes including monitoring ROM coal so as to direct extraction operations, monitoring the quality of feed coal to the wash plant to allow operators to better control of washability parameters, and measuring the quality of product coal from the wash plant. In all industries, product quality is ensured by operators responding to minute-byminute results and mine life increased by the use of more near-spec material. The risk of out of spec shipments is reduced. The AllScan analysers are maintained by a network of local agents, who are supported remotely by RTI’s engineers. A range of customed service and maintenance agreements ensure that each analyser’s performance is optimised at all times and any downtime is minimised. Please contact RTI’s African Sales Manager, Mr Michael Edwards, michaele@rtiaustralia.com., for more details.
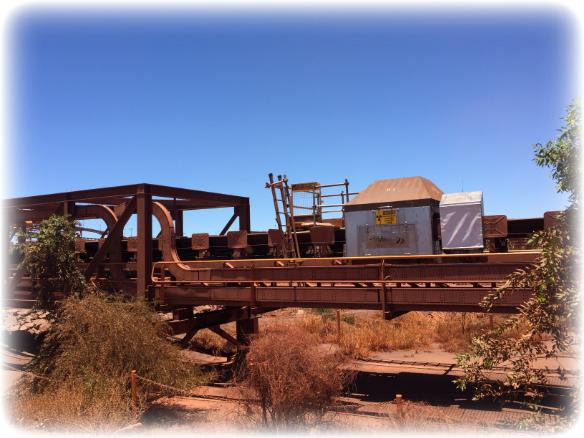
References:
World Economic Forum 2017, Digital Transformation Initiative Mining and Metals Industry, viewed 25 March 2020, https:// www.accenture.com/ _acnmedia/accenture/ conversion-assets/wef/pdf/ accenture-mining-and-metalsindustry.pdf
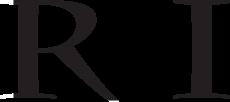
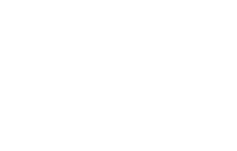
