
8 minute read
AL INVEST → Energy storage systems and coolers from Břidličná
Energy storage systems and coolers from Břidličná
Text: Luděk Vokáč, photo: AL INVEST
The aluminum semi-finished products by AL INVEST Břidličná are used to make a wide array of products. Among them are fuel tanks for trucks along with all types of coolers, including those used in cars. Their production is very specific, the manufacture of foils for coolers even requires the use of unusual technology.
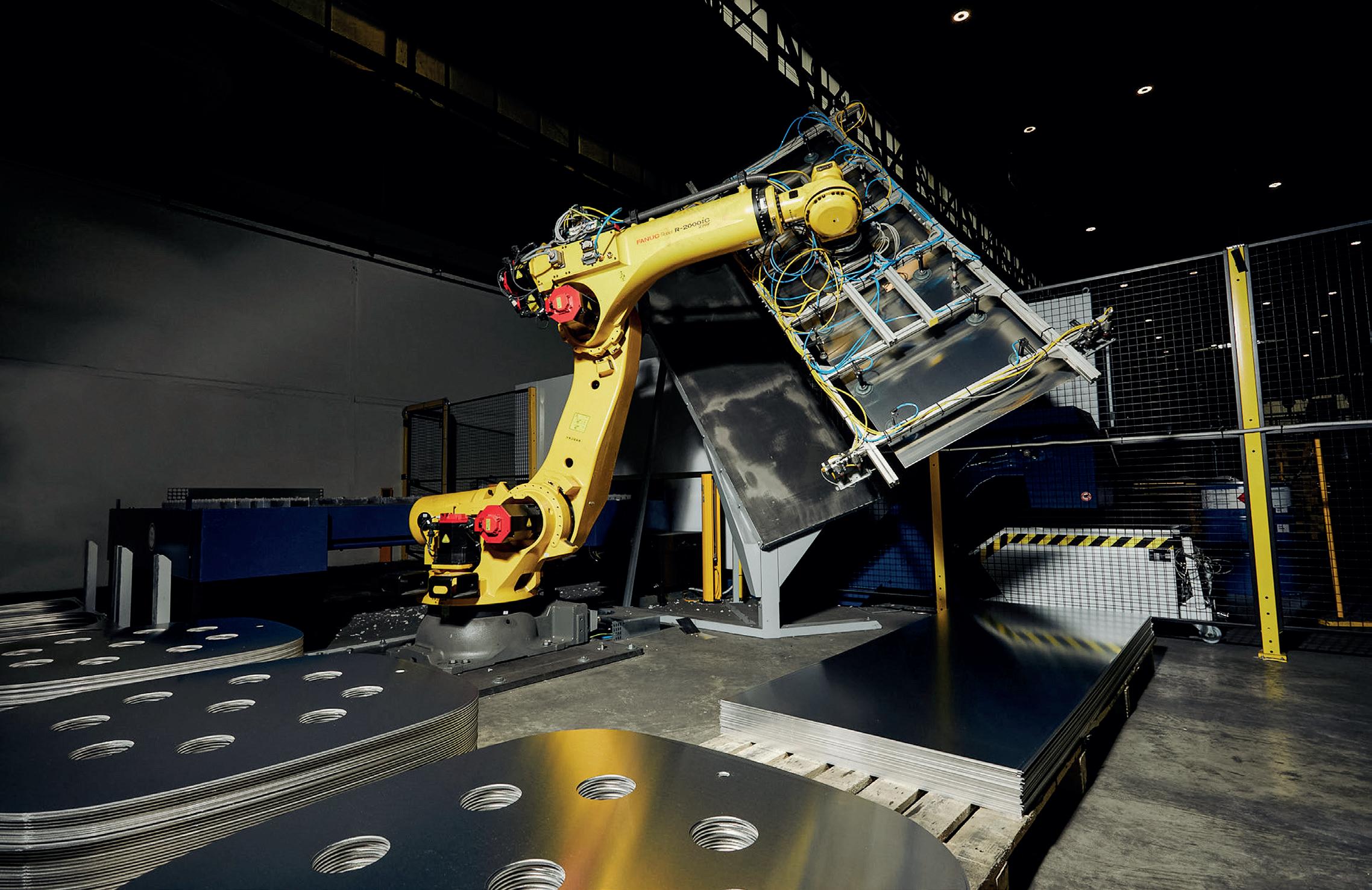
Aluminum foils, strips, sheets, plates and laser cutouts are transformed into various products. And all of this is done in Břidličná. The specific composition and production process of each semi-finished product determines how they will be transformed into a finished product. Whether it’s packaging materials, foils for finstocks or sheets, each product has unique prerequisites. For example, the way finstock foils for car coolers are produced in AL INVEST Břidličná is rather unusual. These foils are made using continuous casting, which is not especially common. Typical continuous casting is not suitable for producing thin foils that are then soldered into cooling-medium pipes. During continuous casting, a relatively thin coil is produced, which is then cold rolled into thin sheets.
Demanding technology is more efficient
And therein lies the pitfall of the technology in general. “In order to roll the coils, we have to regulate temperature during continuous casting in a way so that all the melt elements solidify simultaneously. The material has to drop several hundreds of degrees Celsius on a production area of just a couple of centimeters,” explains David Jaklin, Senior Sales Manager at METALIMEX for Business Unit FOILS & AUTOMOTIVE. While this is not so difficult in food packaging production, it’s much more difficult with high-alloy (with high content of additives) aluminum for automotive or construction. The “8079 aluminum alloy” with high drawability is a great example of this. Drawability is something continuously cast products don’t have. “But we are able to make products using continuous casting that have it, perhaps even more than hot-rolled products do,” says Jaklin. The clients use this alloy to make plate heat exchangers for heat recuperation units used in industrial applications as well as in households. Another very specific alloy is Zirkal (modified 3003 alloy), which allows us to make thin foils for passenger-car coolers. Products made from this alloy are then shipped to clients who supply car coolers on the Volkswagen group’s MQB platform. The third type of AL INVEST finstock foil is made from the 8011 alloy. These foils are used for rotary heat exchangers (again, used for HVAC), which require the material to be very strong and thin at the same time.
“Hot-rolled aluminum can be rolled as thin as 0.5 millimeters, but continuous-cast finstock aluminum can be rolled as thin as 0.05 millimeters for automotive use and up to 0.035 millimeters for HVACs,” David Jaklin explains. Having such a thin material has several benefits. Using approximately the same amount of input material, you get a foil with greater surface area, so using it is more efficient. Also, coolers with thin fins are lighter, which helps cars reduce their carbon footprint and energy consumption.
The foils from Břidličná have made their way into state-of-the art coolers used in the most demanding of situations. “Coolers made from our materials have been used in Bugatti cars and in Formula 1,” boasts Jaklin. “Our R&D department, headed by Mr. Dvořák, plays a big role in the success of our foils,” he remarked in praise of his colleagues.
Cutouts can save costs
The automotive industry also uses our hot-rolled plates and strips. Our clients, such as Magna or SAG, use these products to make fuel tanks for Mercedes, MAN, Scania, Volvo, DAF, and Iveco trucks and buses. Hot rolling is more expensive and, unlike continuous casting, the metal isn’t cast directly into coils, but is first cast into slabs and then hot-rolled into coils.
AL INVEST Břidličná uses this to make cast plates, which can then be made into laser cutouts. That’s something we’ve been doing since 2020. “Our clients demand high drawability, so the sheets are deep-drawable. We are the only ones who can provide this level of quality for our clients,” says David Nalevajka, another member of our D3 Aluminum METALIMEX division sales team.
While most heat exchangers should never corrode, car coolers are a different story. The outer fins which are exposed to the elements are supposed to corrode in a controlled way, so they corrode earlier than the pipes. “The cooler will gradually decrease cooling efficiency long before the cooler pipes corrode and the fluids begin to leak,” David Jaklin offers an explanation of this unusual safeguard.
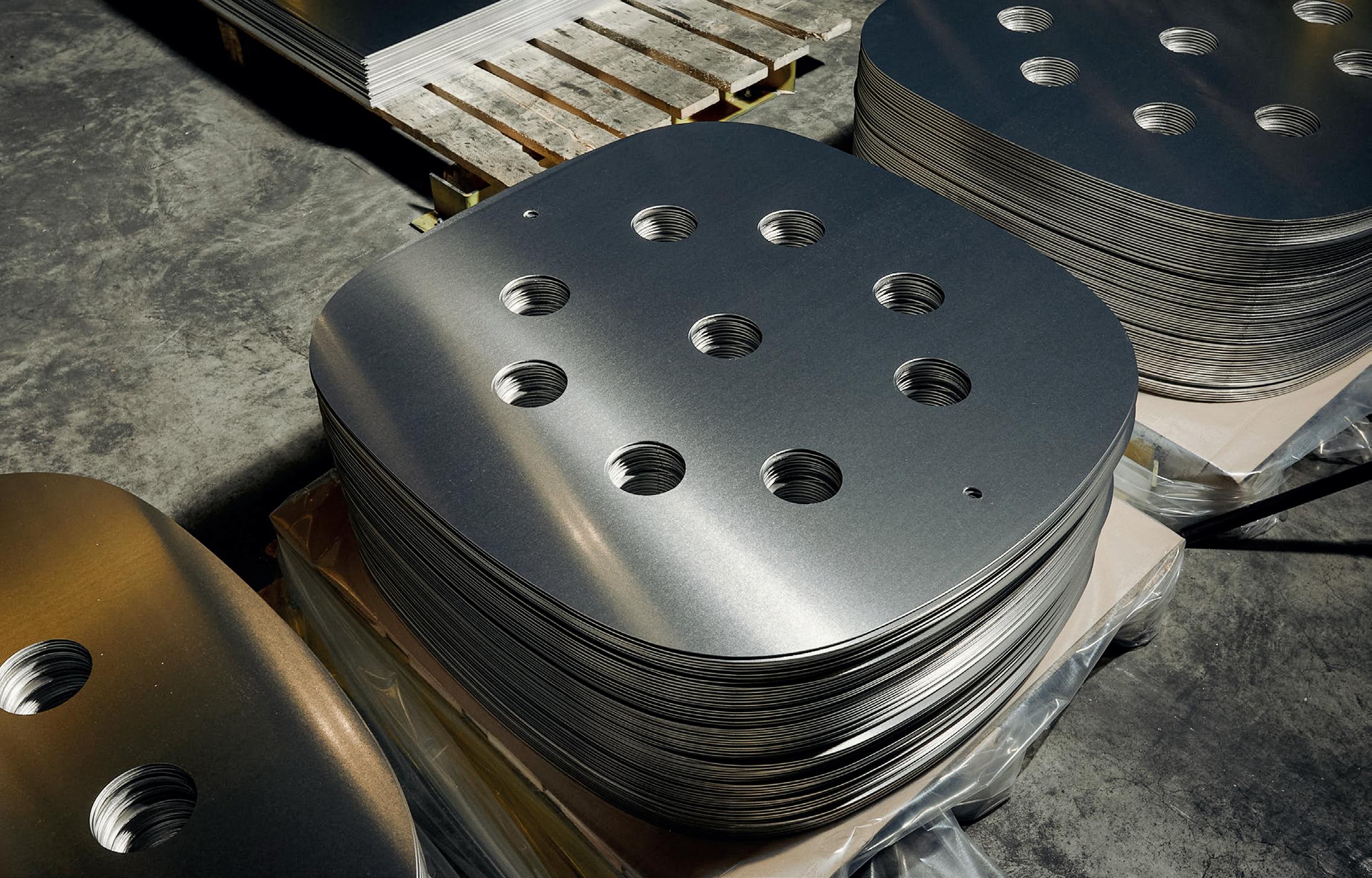
AL INVEST Břidličná and recycling
Aluminum is an easily recyclable metal. AL INVEST Břidličná is trying to always increase the amount of recycled materials (aluminum scrap). But it’s actually not an easy process. Usually, the amount of recycled materials in a product is determined by the customer. Until recently, the food industry required pure primary aluminum because of strict requirements on the health and safety impact of the material, which used to be guaranteed only when using pure primary aluminum. The recycled material can contain various undesirable impurities that can either change the physical properties of the product or mean that the product does not meet health safety requirements. At the same time, determining the amount of recycled material in aluminum can be rather difficult because aluminum scrap can be very diverse and contain many other elements.
However, AL INVEST Břidličná has developed a way to utilize recycled aluminum. Car manufacturers have increased their demand for recycled aluminum, but so has the food industry. All companies are trying to find ways to reduce their carbon footprint. “Using normal aluminum produces 8 kilograms of carbon dioxide and using so-called ‘green aluminum’ (made using renewable resources) produces only 4 kilograms. Using recycled aluminum, however, produces a negligible amount of carbon,” says David Jaklin, MTX Group Sales Manager. The greatest amount of emissions is released when mining bauxite and extracting the metal from it. Recycling means you don’t have to do that.
“On average, our regular foils contain up to 40% recycled material. However, we are also working on a new material called PurAl that contains up to 100% recycled materials,” says David Jaklin, explaining where AL INVEST stands in this regard. Making products with a high percentage of recycled materials means we can acquire new clients. Ensuring that the products with high recycled material content have the right properties is not the only challenge the AL INVEST team faces. It is also important to make sure the finished material behaves in the same way as its non-recycled counterpart during the production process. The key to this is carefully sorting the scrap metal, as well as the way it’s processed.
The laser cutouts AL INVEST makes from its sheets are another way we are improving production efficiency and reducing carbon emissions. “Supplying our clients with cutouts means less waste (tons of scrap metal) being transported all across Europe and back. “Scrap metal that would normally be produced by the tank manufacturers is produced in our factory. That allows us to recycle the material without moving it across large distances,” Nalevajka says, explaining the benefits of the cutouts. AL INVEST produces a semi-finished product with added value, all whilst saving money and reducing emissions. This alone saves 7.5 tons of carbon dioxide each year.
Interestingly, our clients also demand that the sheets used for fuel tanks look good on the surface. “We have to make sure the sheets aren’t scratched on the surface or have any other surface defects,” Nalevajka explains. But he thinks this demand is somewhat paradoxical. “You can probably imagine what a fuel tank in a truck looks like after a few kilometers. Reducing the demands on visual quality would make production more efficient," says Nalevajka
The portfolio is complementary
The upside of having a broad portfolio is that the individual products complement each other. “We’re not dependent on the automotive industry alone,” explains Nalevajka. “During the pandemic, car manufacturers reduced their demand, but flexible packaging and foil manufacturers increased theirs,” adds his colleague Jaklin. Both managers see finstock foils as the future for all types of coolers. “Both fossil-fuel and electric cars need coolers. Also, we have seen increased demand from the construction industry and other areas where heat recovery is a big trend,” Jaklin says.
AL INVEST Břidličná can react to these changes in demand in an agile way. “If necessary, we can reschedule our production program in two weeks to keep operating at full speed,” Jaklin says. Both managers agree this places high demands on all employees, including planning, sales, and production line operators. “Our employees help us a great deal through their conscientious approach. Their experience in this field is invaluable,” Nalevajka said in praise of his team.