6 minute read
Stick with it
from MPN EU Issue 52
by MPN Magazine
Next Article
SIMON DEARING, MANAGING DIRECTOR OF MANUFACTURER EUROBOND ADHESIVES DISCUSSES SOME OF THE CHALLENGES MEDICAL DEVICES PRESENT MANUFACTURERS WITH.
THE CHALLENGE Medical devices present manufacturers with a unique challenge. As well as being health-compatible, the materials used within these devices must allow high-precision production and permanent joining as well as withstanding various sterilisation methods. It is particularly important to consider all of these factors when choosing which adhesives to use for the assembly of medical devices.
ADHESIVES Medical grade adhesives can be used to bond medical products such as syringes, dialysis filters, blood bags and tube connections. These medical products are usually made from a range of synthetic materials such as plastics that are hard to bond e.g. PolyEther Ether Ketone (PEEK), PolyEthylene (PE) and PolyPropylene (PP). On the other hand, common plastics such as PolyVinyl Chloride (PVC) and Acrylonitrile Butadiene Styrene (ABS) are well suited to bonding.
DISPOSABLE MEDICAL PRODUCTS Disposable medical products are often produced in large quantities. It’s important for adhesives to possess mechanical bond strength, as well as being able to be rapidly cured. When adhesives have both of these properties high volume production can be ensured.
For transparent and UltraViolet (UV)-permeable materials, UV-curing medical grade adhesives can be used. For UV-impermeable substrates we recommend Light Emitting Diode (LED) curing, and for visual quality inspection, fluorescent versions of medical grade adhesives are also available. One such product is Vitralit UV 4802 which has been developed by German adhesives manufacturer Panacol and is supplied to UK businesses via Eurobond Adhesives.
REUSABLE MEDICAL PRODUCTS For reusable medical products, durability and the ability to withstand frequent sterilisation play a vital role. Cured acrylate adhesives have a high resistance to sterilisation by autoclaving, gamma radiation and
ethylene oxide. These sterilisation methods therefore have no measurable negative impact on Panacol’s medical grade adhesives.
Additionally, electron-beam sterilisation has even been shown to improve the adhesion of some medical grade adhesives of the Vitralit series. This is thought to be due to an increase in the degree of polymerisation of these products.
EXAMPLES Eurobond Adhesives supply USP class VI and ISO 10993 medical grade adhesives to manufacturers of medical disposable devices. These organisations use the adhesives Euorbond Adhesives supply to manufacture many disposable items.
Vitralit UV 4802 is a one-component acrylic system that cures very fast when exposed to light. Eurobond claim the system demonstrates excellent adhesion to many plastics such as PEEK, PolyEthylene Naphthalate (PEN) and Thermoplastic PolyUrethane (TPU). These plastics are all typically hard to bond with conventional adhesives. This adhesive also adheres very well to ceramics and glass. Tests have shown that the adhesive is highly resistant to heat and is able to keep its soft and flexible characteristics even after being exposed to temperatures of 150°C for seven days. As a result of its high flexibility the adhesive is perfectly suited for bonding thin and bendable PEEK plastic materials.
Vitralit UV 4802 is pink in colour and cures within seconds under a UV or visible light source. Both high pressure gas discharge lamps and LED curing systems are suitable for curing the adhesive. Once cured, the adhesive fluoresces which enables inspection of the bond line under black light.
For reusable medical products, durability and the ability to withstand frequent sterilisation play a vital role.
THE COMPLETE COATING SERVICE FOR YOUR DEVICE BOOTH 1425
ASTUTE ® ANTI-THROMBOGENIC COATING
ASSIST TM HYDROPHILIC COATING
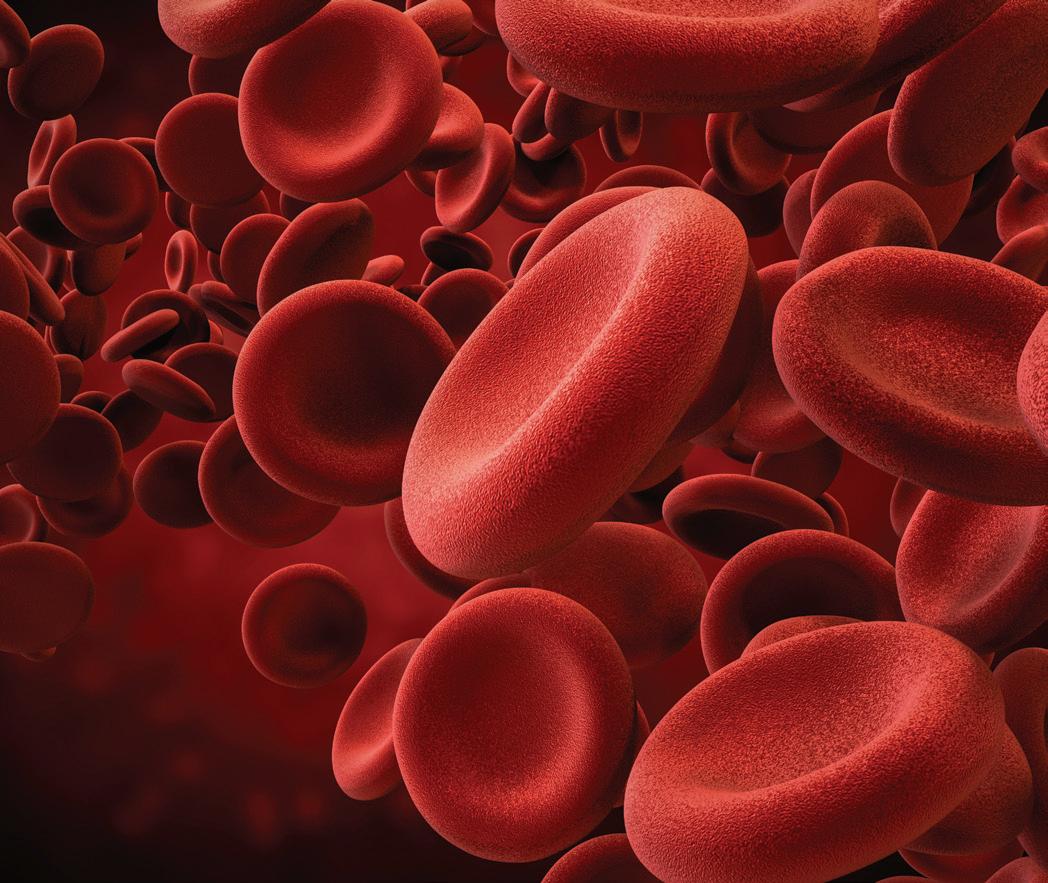
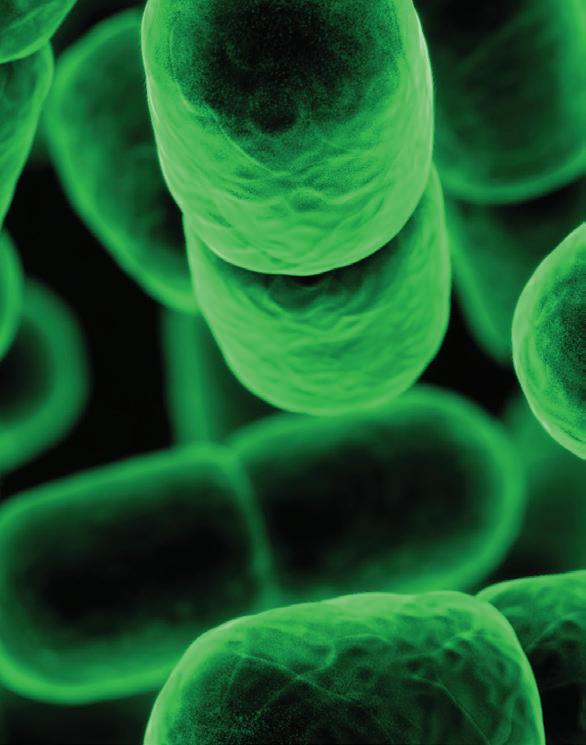
AVERTPLUS TM ANTIMICROBIAL COATING
Get your coat
OUR EDITOR LAURA HUGHES SAT DOWN WITH ARJUN LUTHRA, COMMERCIAL DIRECTOR, BIOINTERACTIONS, TO FIND OUT MORE ABOUT THE COMPANY AND FUTURE SECTOR PREDICTIONS.
1. Please tell me about your organisation, BioInteractions BioInteractions innovates high-performance, biocompatible coating technologies for the medical device industry. We have spent over 25 years in the industry tackling the variety of biocompatible challenges seen by medical device manufacturers. Our range of products aims to provide innovative and effective solutions to improve antithrombogenicity, device related infections and tissue damage at the device-body interface.
We have also improved our ability to support our customers’ developments through our commitment to care services. We are able to provide an optimised coating process for a specific device, in-house testing procedures and to provide supporting data and experience with regulatory submissions.
2. Which materials are you able to coat? Our technology works on a wide range of substrates and we have multiple techniques to improve the interaction between the substrate and the coating. Our application techniques enable us to coat a wider range of materials in order to ensure a consistent coating applied to the device to give long-term efficacy on the device.
3. You have developed a new antimicrobial which doesn’t release toxins into the body. How does this coating work? AvertPlus Antimicrobial is a non-leaching coating that eliminates bacteria and helps to reduce biofilm formation. The coating targets a broad spectrum of bacteria, without harming the patient’s cells.
The coating works by using a combination of components to provide a contact-kill mechanism. This multi-faceted approach significantly reduces the ability of bacteria to remain on the surface and colonise. This gives the coating significant advantages over alternatives for tackling device related infections.
4. Please can you tell me more about the antithrombogenic coating you have developed which is able to mimic the endothelial layer? The Astute Antithrombogenic Coating is a non-leaching coating that actively improves the haemocompatibility of a device by mimicking the natural endothelial layer. Astute enables a device to perform its intended function by preventing formation of a thrombus and reduces the risks of further complications from occurring in a patient.
Astute Antithrombogenic coating uses a multi-faceted approach to prevent thrombus formation and helps the device maintain its position for therapy. The coating interrupts the blood cascade mechanism as well as preventing blood components from interacting and depositing onto the surface. This innovative approach provides superior haemocompatibility to the surface and reduces significant risks of the device to improve the patient’s well-being.
5. What do you think are the main challenges when developing coatings for manufacturers? Our customers face a variety of challenges whilst they are developing their final product for the market. A significant change in the industry has come from the regulatory changes, such as MDR. This has had a significant impact on the way devices are being regulated and has impacted the pathways certain devices are able to take. BioInteractions have followed these changes closely and are able to assist our customers with their regulatory submission. 6. In the next five years, what are the key changes you predict within the coatings sector? The medical device regulations have been through significant changes recently. Therefore, the technologies will follow suit and have to catch up with these new regulations. This will take a significant amount of time but will also help to improve the overall quality of innovations and medical devices available.
In addition to this, there is a clear intent to introduce computer software and systems into more therapies. This will certainly change the way we are able to provide the therapies and the amount of data we are able to receive. This will in turn improve the therapies available to patients.
BioInteractions are committed to innovating and maintaining the highest standards for our customers in order to help provide innovative and effective medical devices for patients.
7. Which events can our readers find you at this year? We are exhibiting at the MD&M West 2020 show (Booth: 1425) and the MD&M East 2020 show (Booth: 733).
WEBINARS CREATE | ENGAGE | INSPIRE
Our webinars offer an insightful and professional means of connecting you with your target audience through thought leadership and direct interaction.
Our fully managed and hosted webinar service allows you to: • Showcase your expertise and industry knowledge • Raise brand awareness • Transform the way you engage with customers • Run a cost-effective and convenient alternative to conventional seminars • Gain more insights into your target audience • Attain clearly defined and qualified sales leads
To find out more contact Sarah Livingston tel: +44 (0) 1244 952 358 sarah.livingston@rapidnews.com
@MPN_Magazine