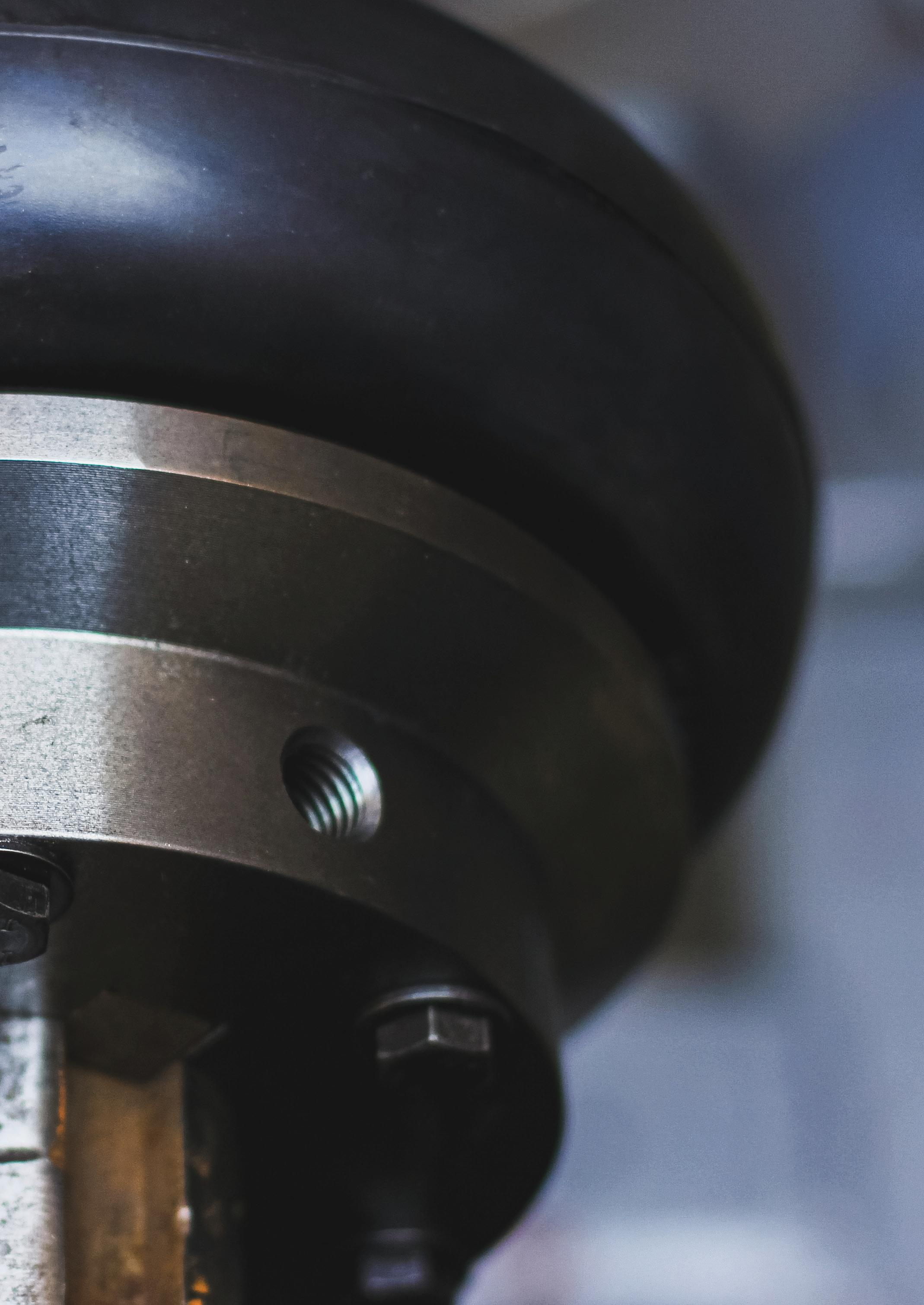
5 minute read
Coupling selection for wastewater applications
By Stephanie Nestor, Assistant Editor, Pump Industry Magazine
Selecting the best coupling for wastewater applications can make all the difference when it comes to installation, reliability and maintenance.
Advertisement
There are two main categories for couplings: rigid and flexible. Rigid couplings are commonly used in vertical turbine, vertical in-line and short set pump applications, they provide precise alignment and adjustable pump lift, but they do not allow for misalignment. However, flexible couplings can accommodate movement or misalignment between the driver and driven shafts. Flexible couplings are commonly used in horizontal, base plate mounted pump applications, as they are ideal for applications where there is unavoidable movement, vibrations, or misalignment.
While all couplings are designed to connect two pieces of equipment together, in many cases due to vibrations and other factors during operation, equipment can become misaligned.
There are three types of misalignment: 1. Axial: when the shafts are parallel to each other but too close or far apart 2. Radial: when one shaft is higher than the other 3. Angular: when the shafts are at different angles to each other
Rigid couplings may be able to transmit more power to the pump than flexible ones, but they cannot handle any misalignment without causing damage to the coupling, shaft, seals or bearings as they cannot accommodate any vibrations or thermal expansion. On the other hand, flexible couplings are designed to absorb vibrations and thermal expansion without damage to either the coupling or other components.
Rigid and flexible couplings can also be further categorised as elastomeric and metallic.
When it comes to selecting a coupling, the most common type is elastomeric. Elastomeric couplings are non-lubricated, non-metallic flexible couplings which typically use rubber, urethane and other composite materials to transmit torque.
These couplings allow for both transmitting torque and accommodating misalignment between shafts, by flexing one or more elements to compensate for shaft misalignment.
Elastomeric couplings are divided according to how their elastic element transmits power, with the three types being: compression, shear or a combination of both.
In compression types, torque is transmitted by compressing the elastic elements, whereas in shear types, it is through elastic elements absorbing force by twisting and stretching. Combination types function similarly to gear couplings, which transmit torque through two flexible joints that are connected to a spindle or third shaft. Using elastomeric couplings in wastewater applications
Elastomeric couplings are commonly used because of their easy installation, low maintenance needs, and ability to absorb shock, misalignment and end float. Given that wastewater treatment is considered critical infrastructure, this is especially beneficial to prevent interruptions to services.
Elastomeric couplings are less expensive than metal ones, require no lubrication, and are designed to wear out, in order to save metal components from requiring constant maintenance, which in turn reduces the need for ongoing maintenance or replacement.
Being flexible, elastomeric couplings are able to accommodate some misalignment.
They can handle higher vibration and dampen shock load because they are made from elastic materials. This makes them best suited for wastewater applications because they are malleable enough to take on pressures from excess materials passing through shafts during filtration.

However, elastomeric couplings come with their own limitations. The build-up of heat exposure, environmental factors, chemical contamination and loading fatigue can all impact elastomeric couplings.
Water can affect how an elastomeric coupling works if there is a lot of water ingress or exposure. While some materials are more water resistant, such as rubber, not all can cope with high amounts of water.
Additionally, being made of rubber or plastic makes elastomeric susceptible to damage and degradation from chemicals and high temperatures.
Elastomeric couplings are also prone to hysteresis. Hysteresis occurs in elastic materials when the difference between the strain energy needed to generate stress and the material’s elastic energy increases. This energy is then lost as internal friction or heat as the material dampens these vibrations, causing the material to melt.
Choosing the right material

It is important to consider the capabilities of not just the type of coupling, but also the material it is made of, as different materials have different advantages and disadvantages which do not always suit a particular application.
Especially in wastewater applications, it is imperative to use a coupling that is both water resistant and highly durable.
The pumped product has an impact on the life of the coupling when it causes degradation over time, which means environmental controls are necessary to prevent damage from water, the sun or chemicals.
For flexible couplings, common materials used can include urethane and rubber.
Urethane is a highly durable and stiff material, but is not suitable for high temperatures and can be prone to hydrolysis in moisture-rich environments.
Whereas, rubber is water resistant and can handle extreme temperatures, but is a softer element and prone to cracking in sunlight.
For some elastomeric couplings, stainless steel hubs and shafts may be required to minimise rust and corrosion, which in turn helps with replacement and maintenance in the long run.
On the other hand, for rigid couplings, steel is the most common material used, with different types of steel better suited to different applications. For example, stainless steel is used for processes which involve frequently washing down components, whereas carbon steel is preferred in applications which require high shock and fire resistance.
Other materials used include brass, aluminium, and cast iron.
Finding the best suited coupling
When it comes to selecting a coupling to use in wastewater treatment, it is important to consider the benefits and limitations which come with using specific types and materials.
Suitable couplings must be durable, malleable, allow misalignment, require no ongoing maintenance and be water resistant.
Evaluating a coupling’s reliability using this criteria will ensure that the selected coupling will be the best equipment for the wastewater job.
Process Automation Solutions for Pressure, Level, Flow and Temperature
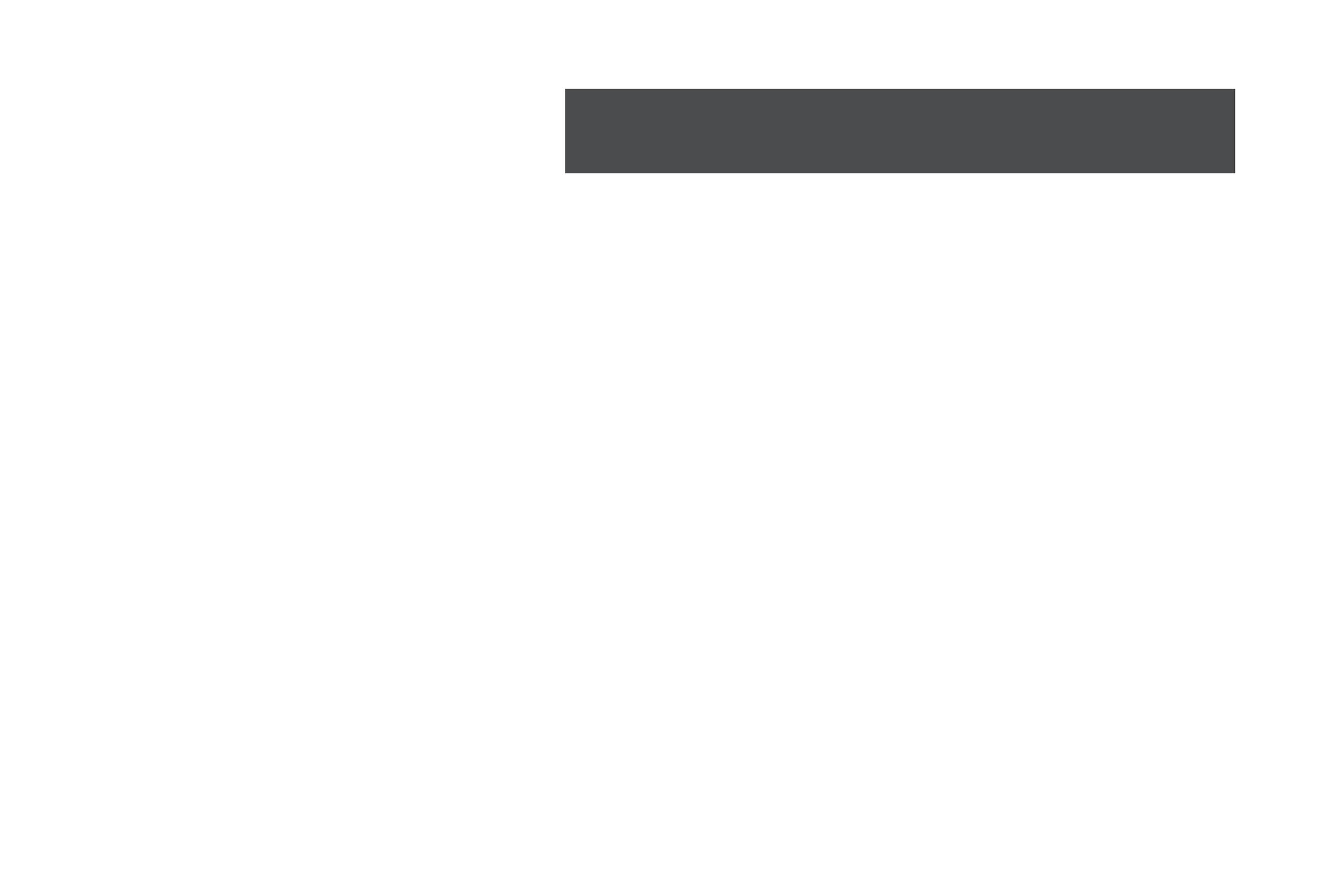
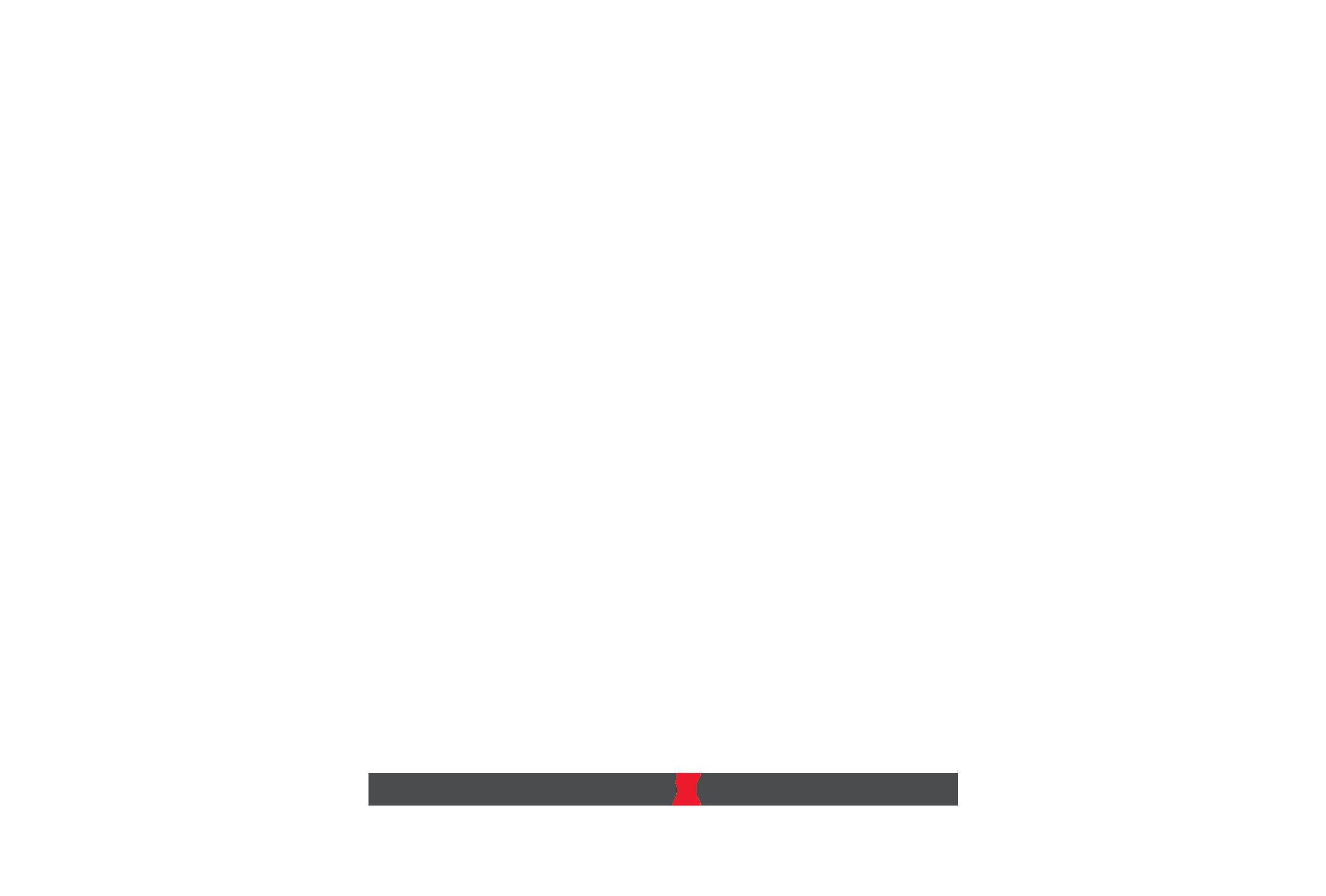
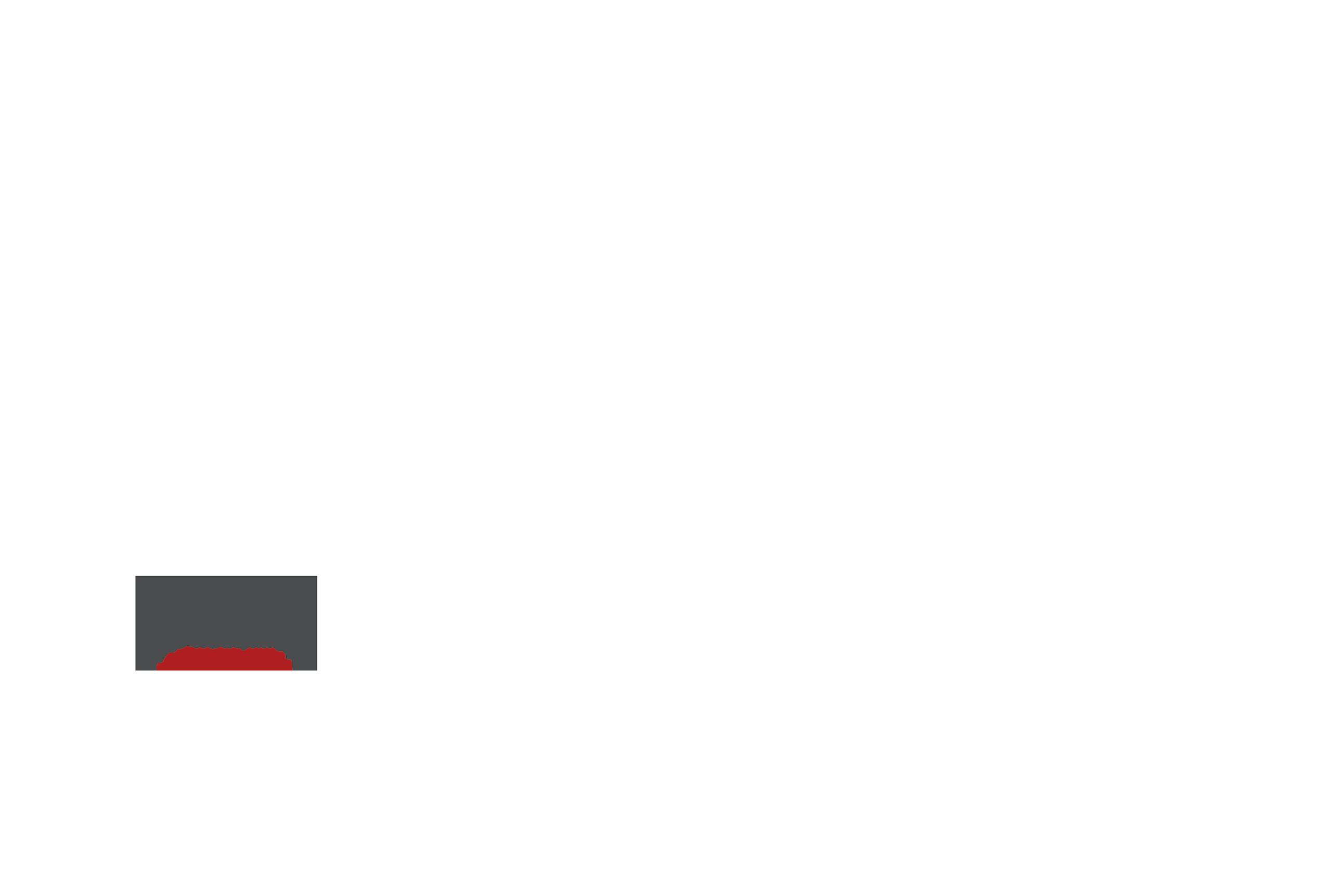
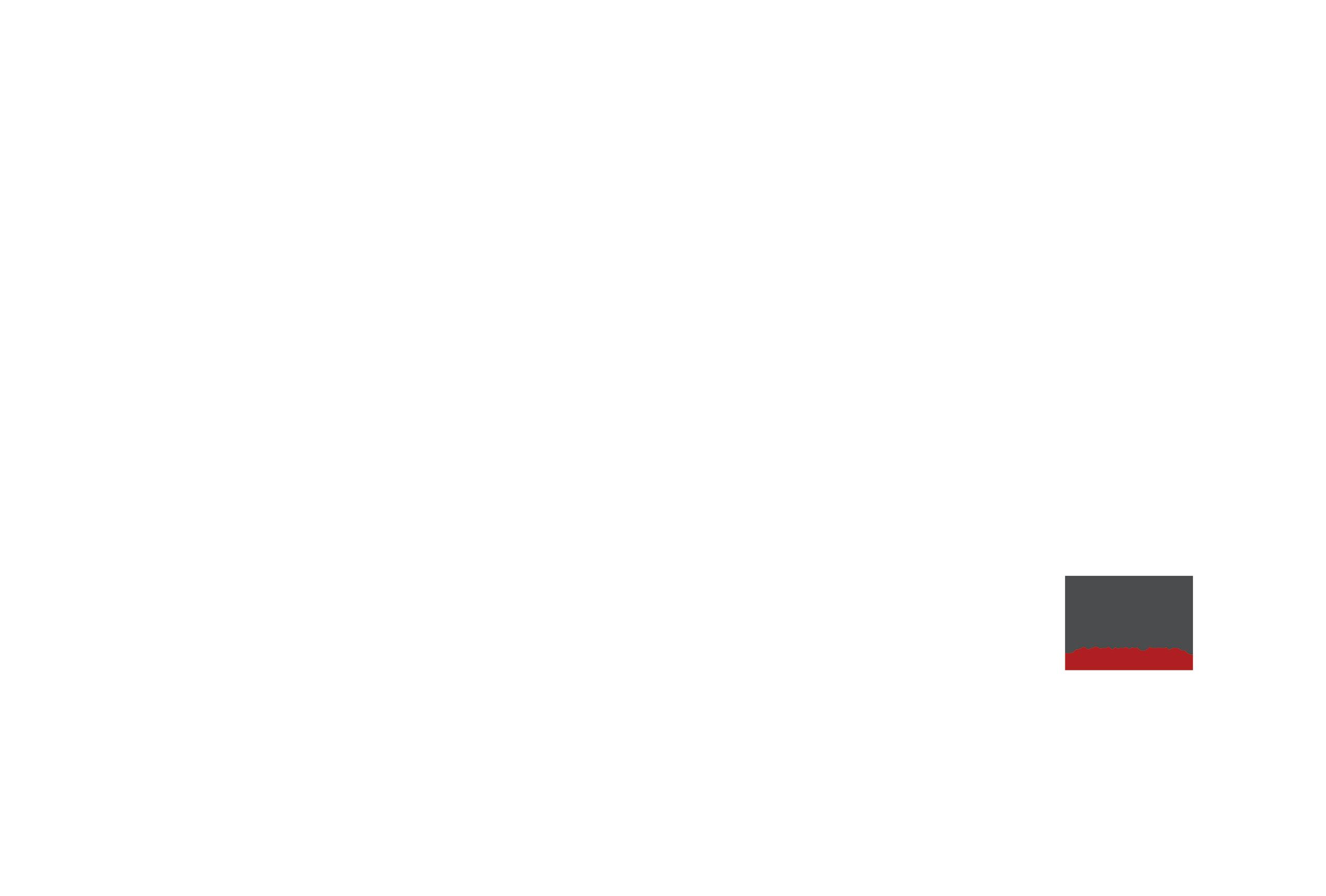
INSERTION ELECTROMAGNETIC FLOW TRANSMITTER SERIES IEF PADDLEWHEEL FLOW SENSOR SERIES PFT SUBMERSIBLE LEVEL TRANSMITTER SERIES PBLT2 WET/WET DIFFERENTIAL PRESSURE TRANSMITTER SERIES 629HLP INDUSTRIAL PRESSURE TRANSMITTER SERIES 628
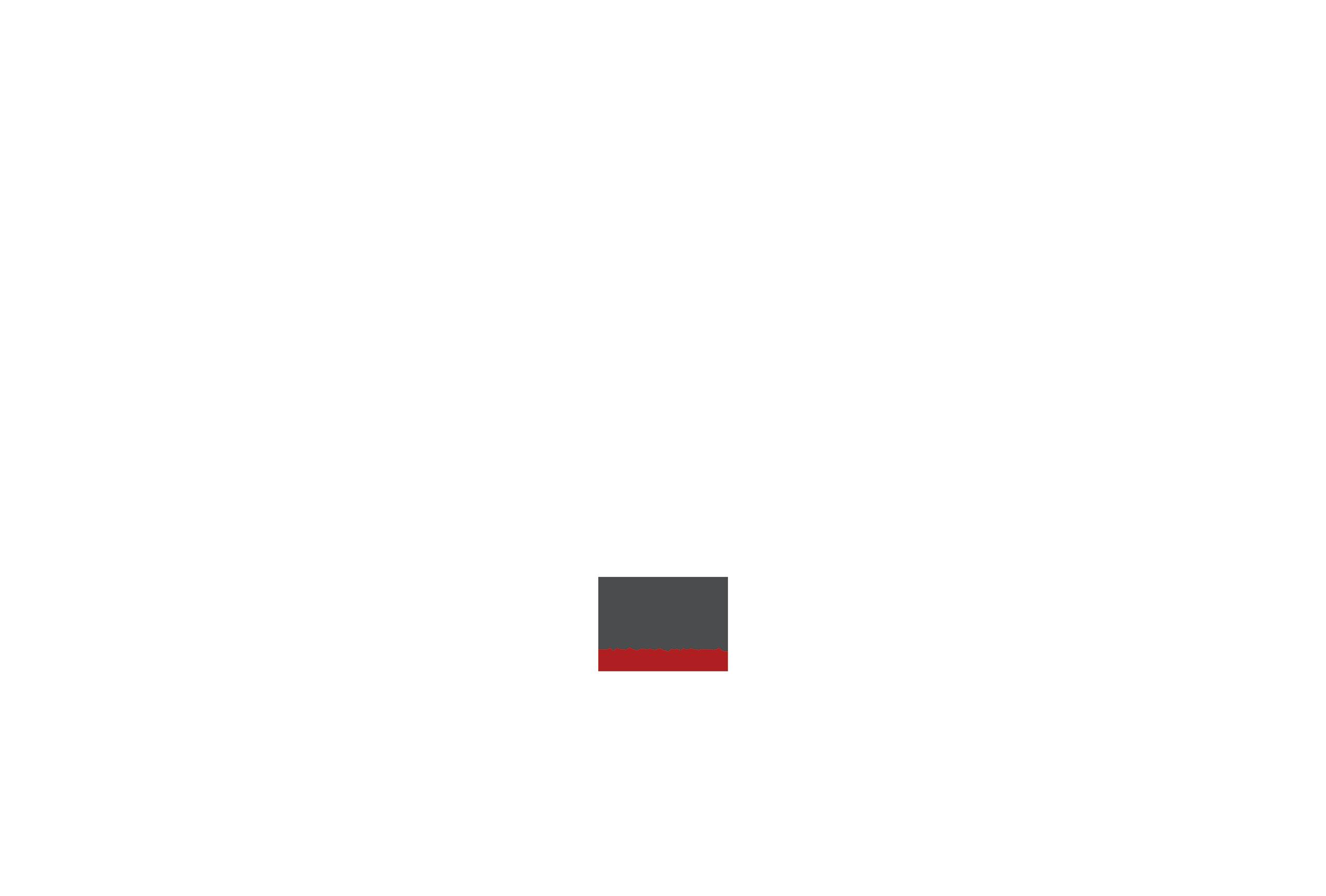

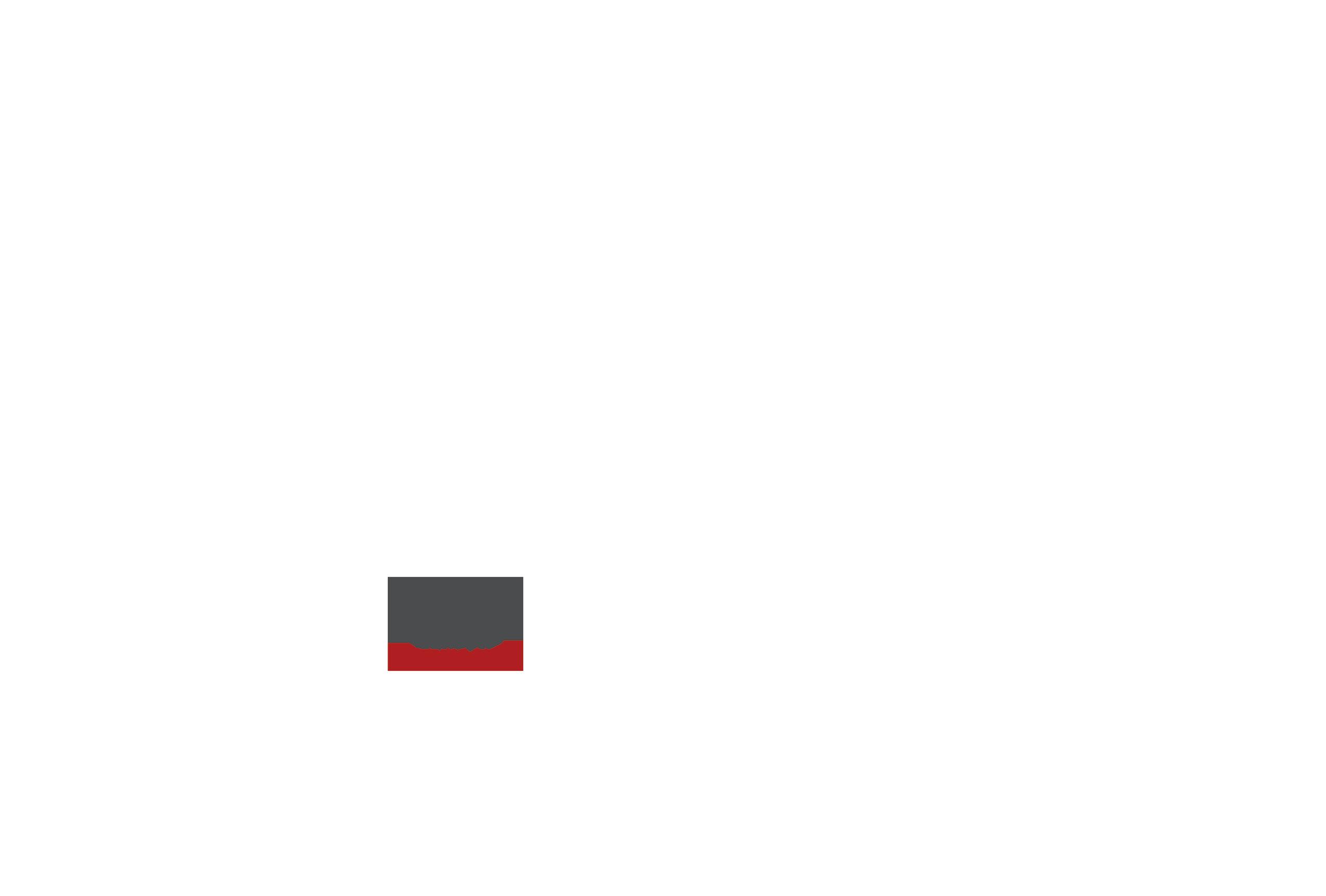
