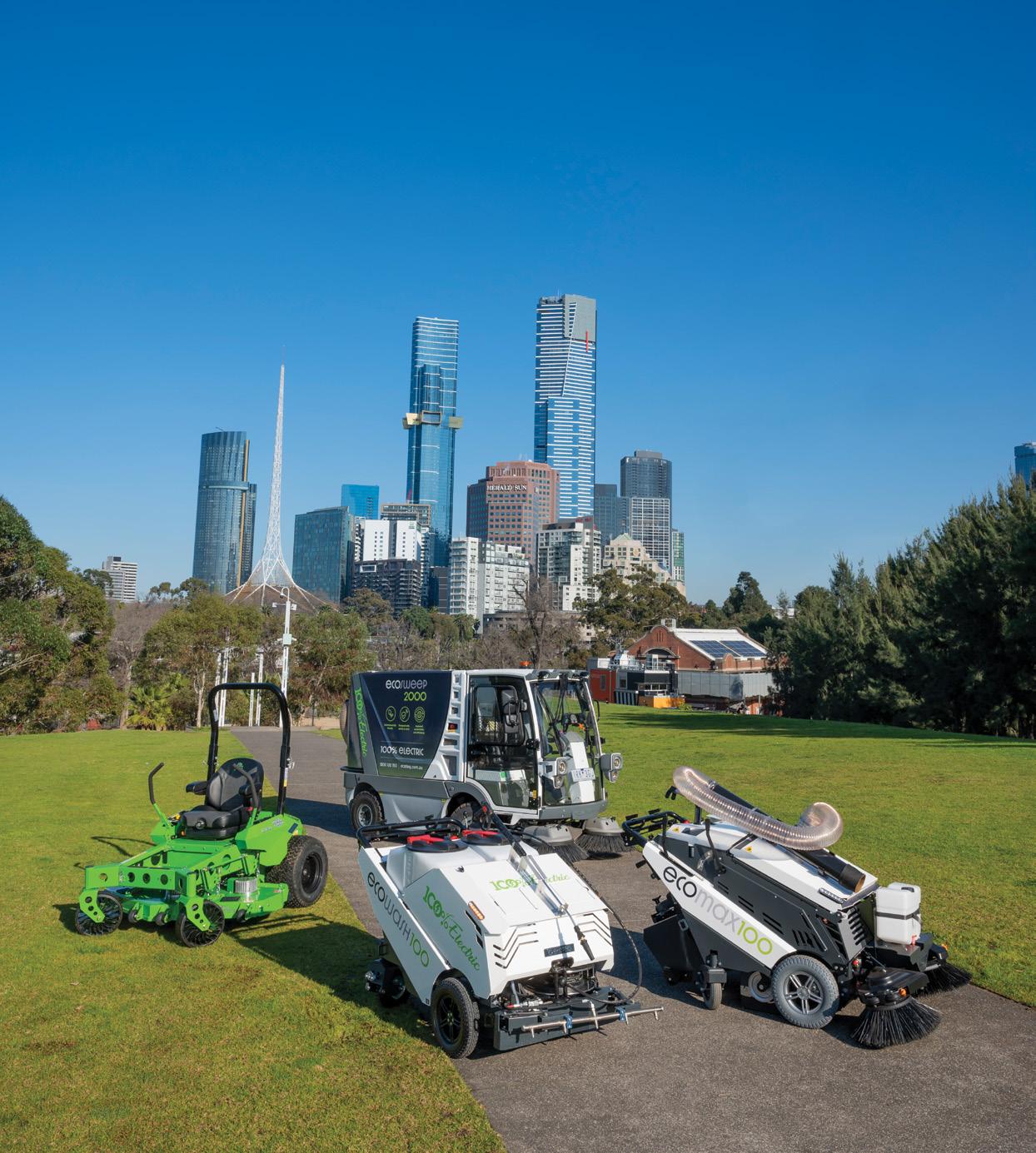
2 minute read
How-to guide: ADOPTING ELECTRIC MAINTENANCE VEHICLES
With their low maintenance costs and lack of carbon emissions, electric vehicles and maintenance equipment are a clear path forward for councils striving to reduce their carbon footprint and reach net zero. But how does the total cost of ownership compare to traditional machinery, and how do councils go about adopting a more sustainable solution?
In the context of a looming climate crisis, local government continues to demonstrate its commitment to the cause, with many councils considering – or on their way to –transitioning their vehicle and maintenance fleets to electric.
Advertisement
Despite the preconceptions some hold regarding electric machinery, the reality is that electric maintenance vehicles do provide an option that is both economically and environmentally sustainable.
The First Step
For councils contemplating making the switch to electric, a crucial first step is considering the total cost of ownership, which refers to the entire cost of owning and operating a vehicle across its lifetime.
Some of the factors to consider when calculating the total cost of ownership include the upfront cost, machine maintenance and fuel requirements as well as replacement and disposal costs.
Electric vehicles and equipment often have a higher initial purchase price than traditional machinery, due to the costs of the battery and electric powertrain, however this should not deter councils from considering electric as a viable option.
An Investment For The Future
Due to their electric parts, electric maintenance vehicles have lower fuel and maintenance requirements than their petrol-powered counterparts, reducing costs and resulting in more operational time for the machinery.
Over time, these savings offset the higher initial cost of electric maintenance vehicles. This means that in the long run, electric maintenance vehicles have a lower total cost of ownership than traditional maintenance machinery, making them a worthwhile investment.
This is all without considering the environmental benefits – many would be surprised to learn that a petrol-powered lawn mower emits the same amount of air pollution in a singular hour as a petrol-powered Toyota Camry driving from Melbourne to Canberra.
In comparison, EcoTeq’s commercial mowers, compact sweepers, high-pressure pavement washers and litter collection vacuums are 100 per cent electric, offering powerful torque, battery life and durability – all while producing zero emissions.
Unsurprisingly with the low total cost of ownership, electric solutions continue to gain popularity in local government.
For a successful transition to electric maintenance vehicles in a local government setting, there are a number of key steps and considerations.
Finding A Tailored Solution
Firstly, it is important to pinpoint the council’s specific needs and objectives and calculate the costs and benefits for both existing machinery and the proposed electric-powered maintenance vehicles, for comparison purposes.
The next step is to research and evaluate the available electric machinery and their features. At this stage, it is important to test drive wherever possible, and consider the charging infrastructure and requirements.
Then comes the establishment of clear procurement strategies, including selecting suppliers. Following this is the implementation and management of the procurement plan in which the electric maintenance vehicles are purchased.
Finally, once councils have successfully implemented electric-powered maintenance machinery, they must ensure compliance with the procurement policies and procedures, such as providing adequate training to staff and monitoring the performance and total cost of ownership of the new electric machinery.
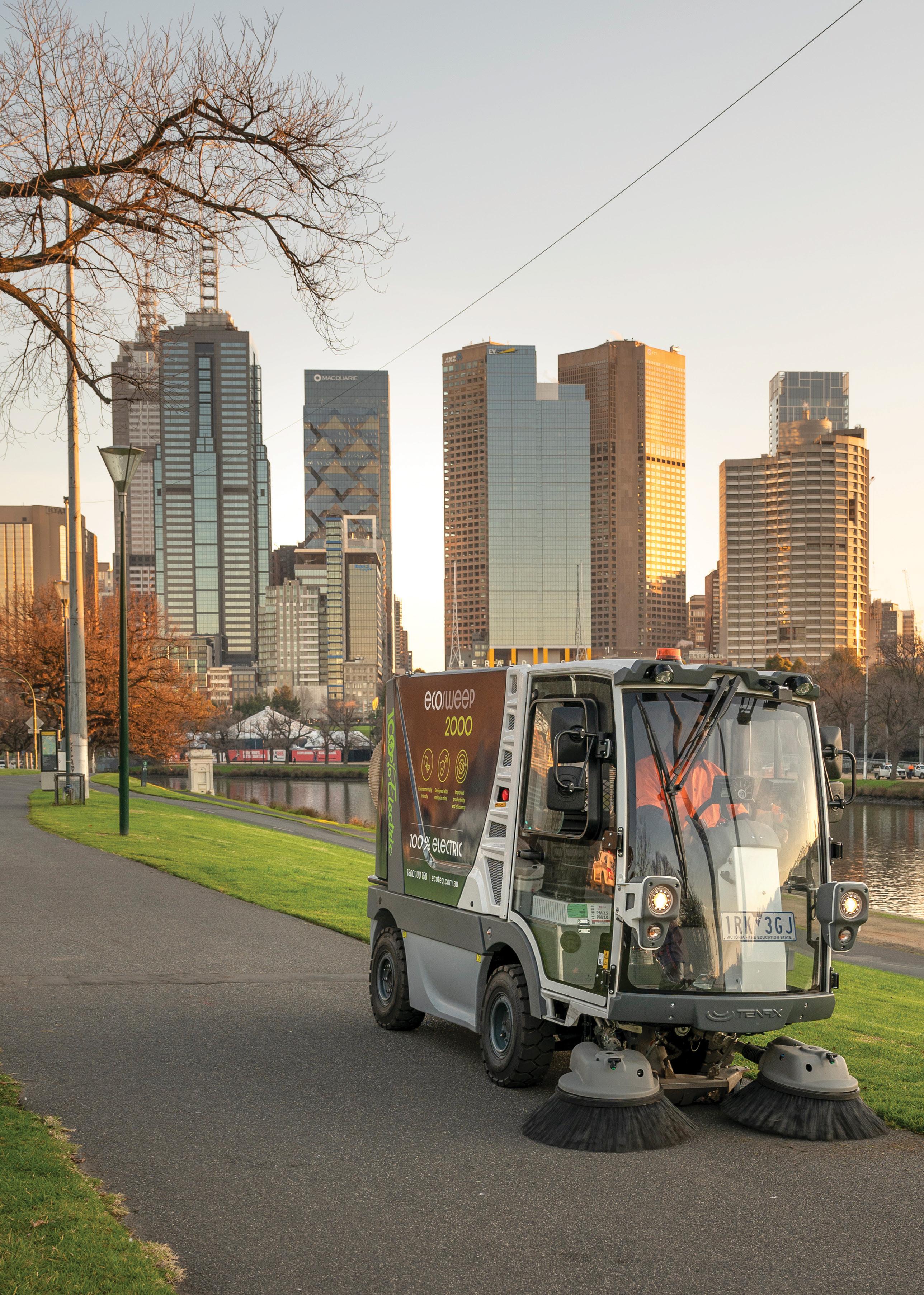