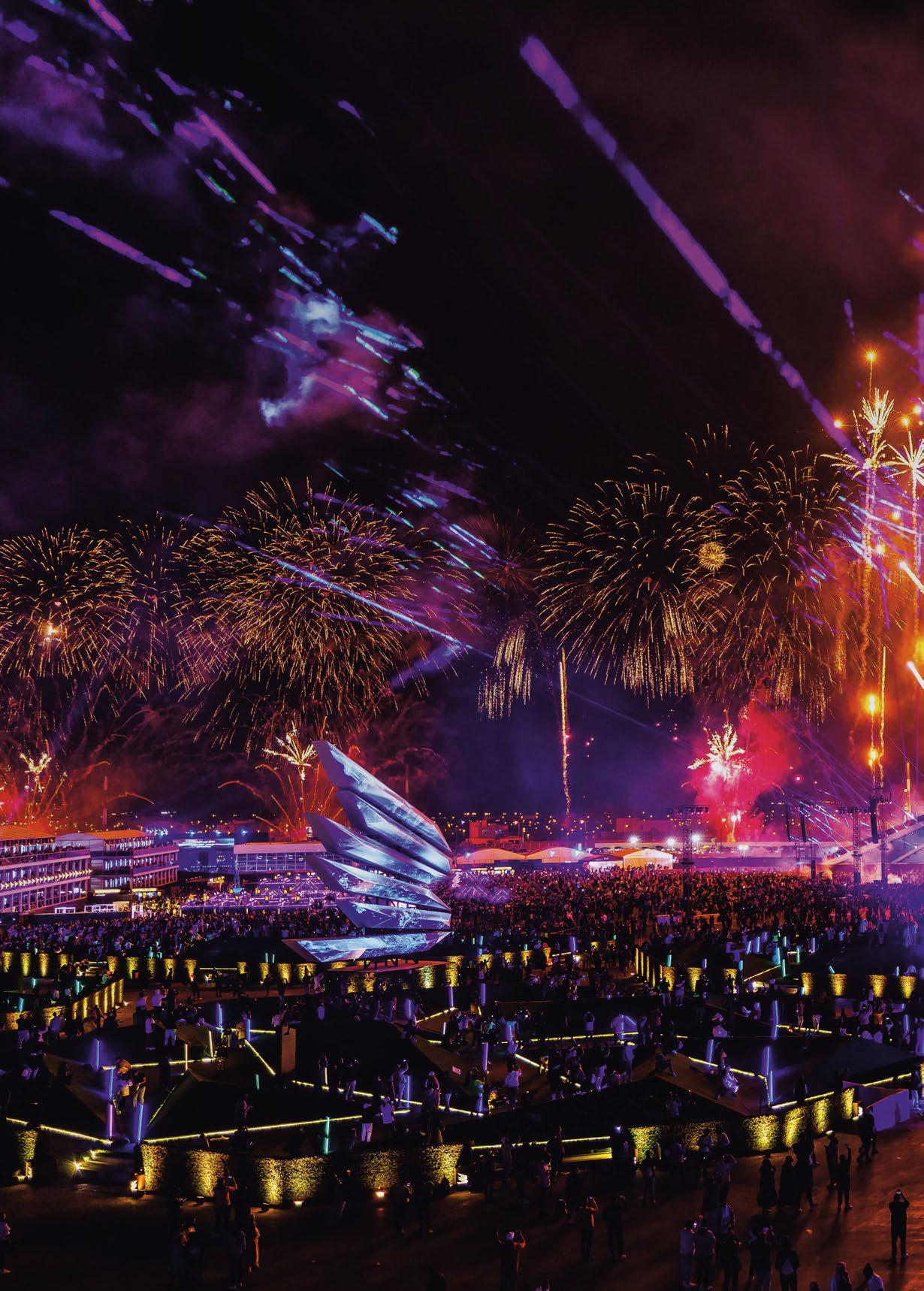
18 minute read
MDLBEAST SOUNDSTORM
ONE OF THE WORLD’S BIGGEST EDM FESTIVALS MAKES A TRIUMPHANT RETURN, WITH MORE THAN 200 ARTISTS, 730,000 VISITORS AND A RECORD-BREAKING STAGE.
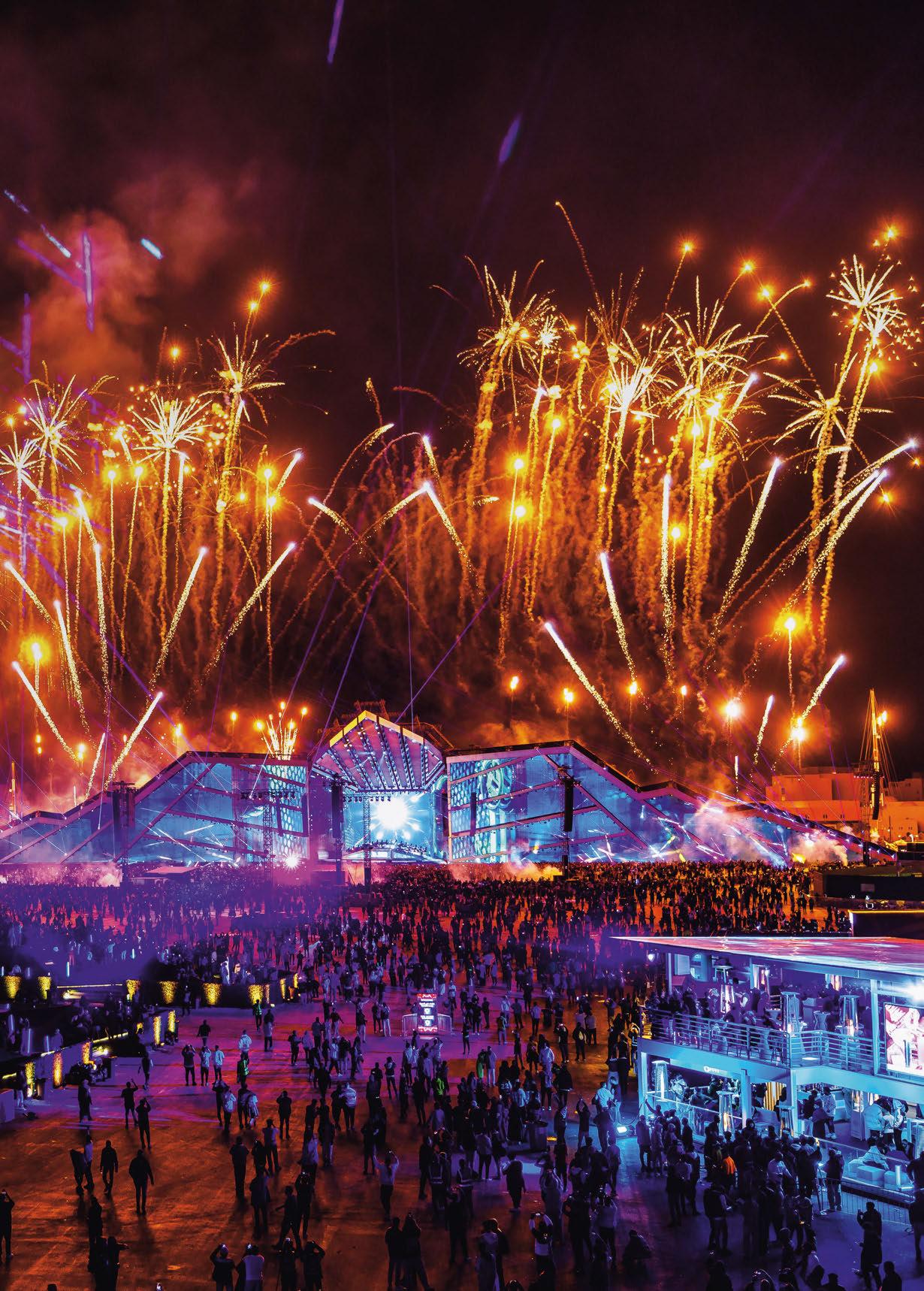
Back in December 2019, MDLBEAST burst onto the region’s festival scene, bringing one of the largest EDM events on the planet to Saudi Arabia. Two years later, with the world recovering from the COVID-19 pandemic, MDLBEAST returned with Soundstorm – one of the biggest music festivals to take place in 2021, with over 200 global and regional acts, including Steve Aoki, David Guetta, Tiësto and DJ Snake, as well as Nancy Ajram, Tamer Hosny, Amr Diab and Elissa. The event attracted 730,000 visitors across eight stages and four days, and even gained a new Guinness World Record for the ‘tallest (temporary) stage’, measuring 250m wide and 41.2m tall.
Experiential agency, Production Glue called upon a vast array of suppliers to help fulfil this mammoth project. “We were ecstatic when MDLBEAST asked us to pull off the impossible,” stated Production Glue. “They were looking for a team to transform a desert landscape, 40km outside of Riyadh, into a kick-ass festival ground that could host the biggest, boldest, music festival Saudi Arabia has ever seen.
“We leapt at the chance and got to work developing the incredibly complex, semipermanent, festival site plan, which included civil engineering and public works projects, stretching across a 5.3 sq km area. For over four months, our teams were on the ground tackling the unimaginable, building what few dare to dream.”
The record-breaking ‘Big Beast’ main stage was delivered by PRG, which supplied a full turnkey solution, including audio, lighting, video, comms and rigging. The company mobilised its global workforce, with 130 members of crew onsite from PRG’s offices in Saudi Arabia, the UAE, the UK, Belgium, Germany, and Spain, working over 3,000 man-days.
Equipment was deployed from PRG’s newly established Riyadh warehouse, and this was then supplemented with kit from various European depots. In all, PRG delivered almost 600 tonnes of technology over the course of seven months of continuous prep and planning and almost three months of set-up on site.
The huge continuous LED screen was made up of over 4,000 sq m of LED, and around 70 million pixels. For the screen’s centre, PRG supplied 2,200 sq m of its brand-new Titan-X panels, which were developed by PRG and INFiLED. This was supplemented with ROE Visual MC-7H for the mid-wing sections and CB5 for the DJ riser. To cater to the mass of stock, weight, power, and pixel considerations that come with such a large single screen project, PRG designed a comprehensive control system, delivering a large yet flexible sync network solution for all artists.
The main stage lighting rig included over 1,000 fixtures, with 130 universes of DMX, six 400a supplies and 26km of cable. Fixtures included GLP impression X4 Bar 20s and JDC1s, Robe Pointes, hybrid fixtures and LED Bars.
For audio, PRG supplied and distributed an L-Acoustics K-Series system comprising K1s, K2s and KS28s across the main stage and delays, which ran using L-Acoustics LA12X controllers and were monitored using P1 processors. Carrying it all were PRG’s master riggers, who deployed 3.3km of truss and 410 hoists.
As well as the Big Beast, PRG also supplied various other parts of the festival site, including the ‘VIB’ (Very Important Beast) Entrance Gate, a site-wide evacuation system and projection mapping onto the iconic MDLBEAST sculpture located in MDL Town, which used Panasonic PTDZ31K projectors equipped with ultra-long-throw lenses via synchronised servers.
“The great thing about working with the 360° from PRG is that each department can draw upon its own wealth of expertise and resources,

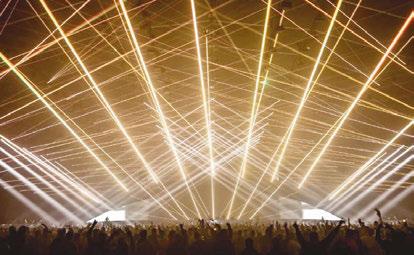

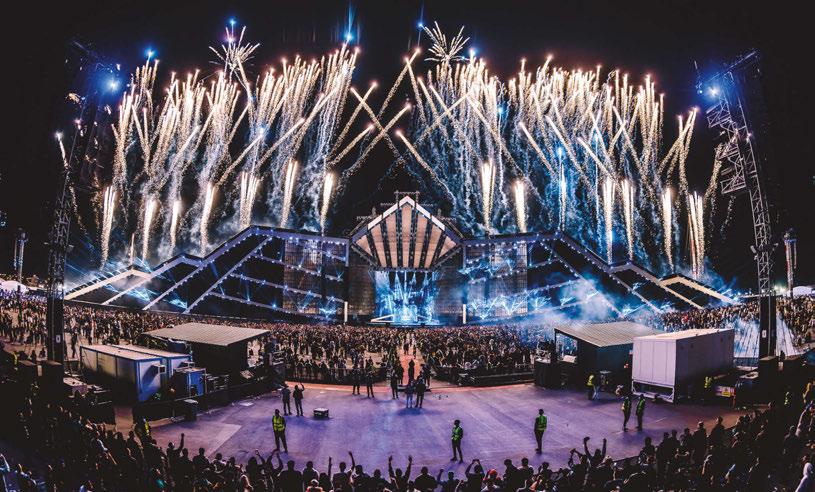
ER PRODUCTIONS - PROUD TO SUPPLY LASERS, SFX AND PYRO TO 7 STAGES AT SOUNDSTORM 2021
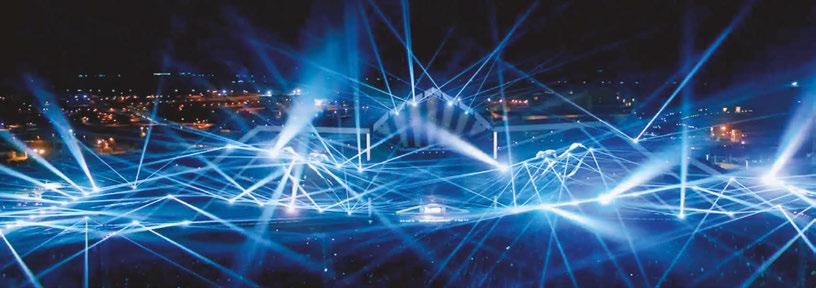
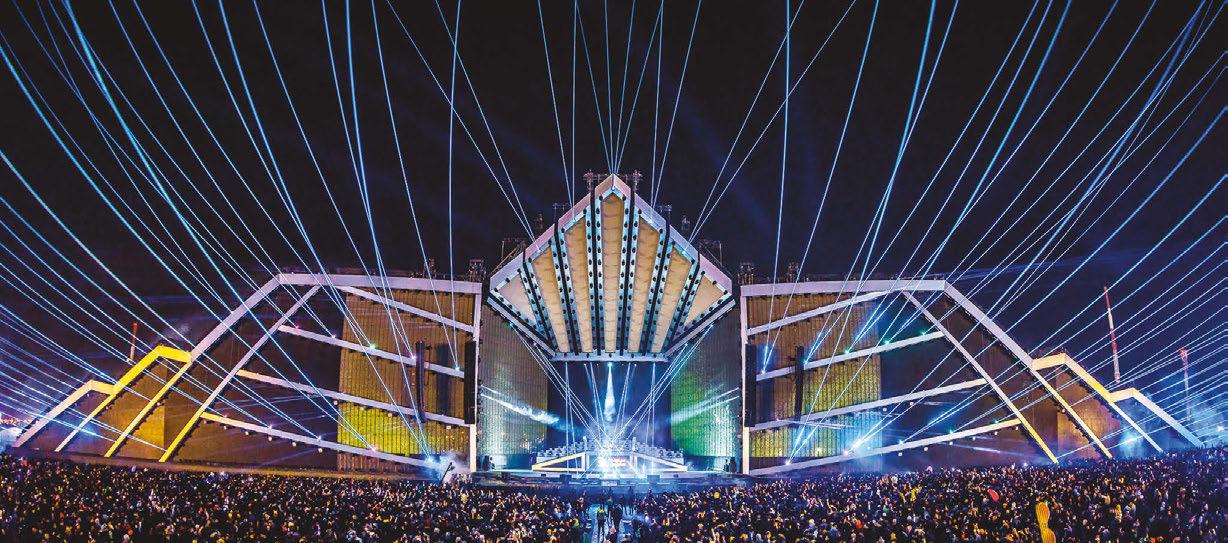
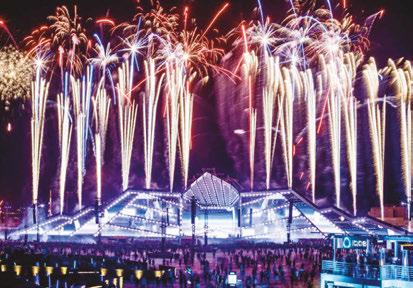
430 lasers, 100 smoke machines, 80 Stadium Shot Extreme and Stadium Shot II, 60 x Stadium Blowers, 20 x Stadium Flames, 20 x Wave Flame, 20 x G-Flames, 20 x Flameblazer and 11,000 pieces of pyro.
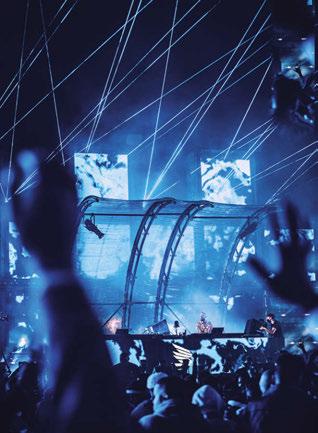
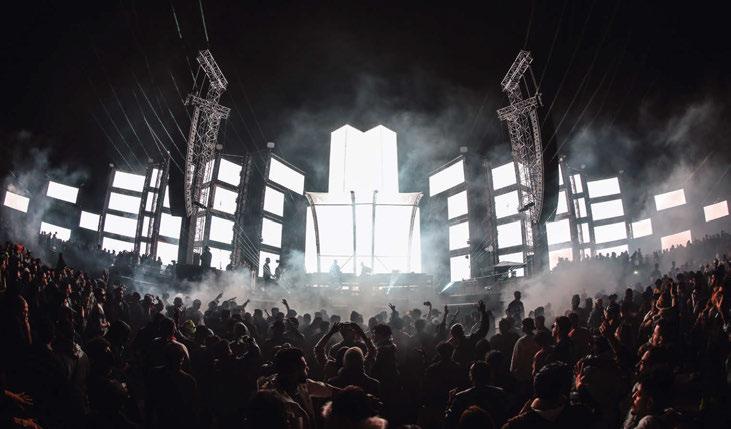
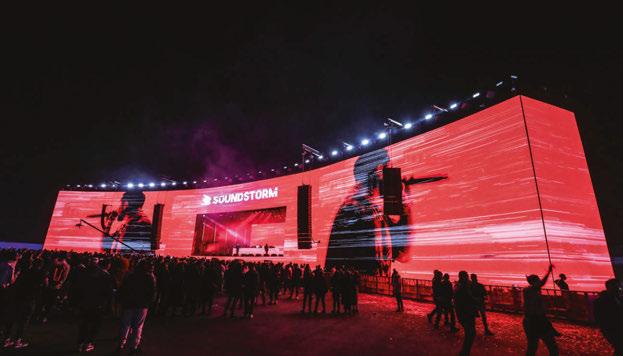
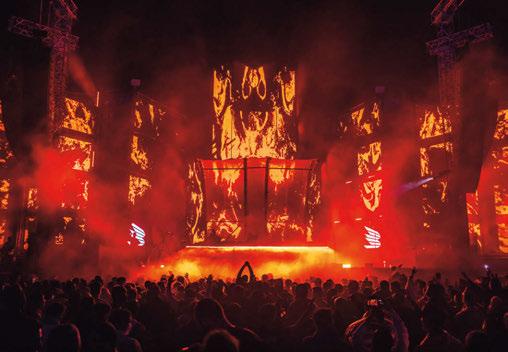
and each team comes together to deliver one exceptional event,” commented PRG Sales Director (Music), Yvonne Donnelly Smith. “This is a bespoke project, and so PRG built a bespoke team. Such a vast production needed the internal workings and conversations between all our technicians to develop solutions smoothly.”
The project came at a time of massive growth for Saudi Arabia, with PRG among the many companies establishing a local presence in the country. Michael ‘Curly’ Jobson, Executive Director – Events and MDLBEAST, explained why in-country development is so important as the Saudi Vision 2030 begins to take shape.
“We’re at the very forefront of the formation of the entertainment industry in Saudi Arabia,” he commented. “We’ve insisted that our vendors have a Saudi Arabian presence because we can’t continue to support events unsustainably. We have to get going here and everyone has shown a willingness to do this.”
PRG Middle East Managing Director, Bruce MacLean added: “Part of our drive within Saudi Arabia will be to make sure that we are enabling, empowering and recruiting local Saudi resources and training them to ensure that they develop the skills to help deliver events of the scale that we put on. That’s one of the key drivers where we’ve been aiming our expansion within Saudi over the past three years.”
‘AN INTENSE, INTIMATE VIBE’ Aside from the Big Beast stage, the site also hosted several other performance areas, including ‘Dance Beast’ and ‘Down Beast’, which were delivered by MediaPro International, as well as four ‘Underground’ stages, which were supplied by Colour Sound Experiment.
For MediaPro International, this was the first time working with MDLBEAST, having not been involved in the first edition. “We were extremely pleased and proud to be appointed as the technical supplier for two stages for the biggest EDM festival in the world,” stated MediaPro International COO, Shaam Pudaruth. “The brief from the client was very clear and detailed. MDLBEAST is an extremely professional entity, and it was a delight working with both them and Production Glue, who share the same values as us as a company.”
With work for the project proposal starting back in February 2021 and the final green light coming in July that year, this project was a long time in the making for Pudaruth’s team. “From the award of the project, we were straight into pre-production work, interacting firstly with the MDLBEAST team and Production Glue, before moving to the various Stage Designers, including Chris ‘Squib’ Swain from Cassius Creative for Down Beast and Ian Tomlinson from High Scream for Dance Beast,” he outlined. “We also consulted with Trevor Burk from Visual Noise, who was handling the overall content of the site, as well as the audio consultant, health and safety, and the complete logistics team from Ginger Owl.”
MediaPro International supplied turnkey solutions across both the Dance Beast and Down Beast stages, as well as site-wide lighting and projection for three entry gates. The supply
included L-Acoustics K-Series audio systems, almost 3,500 panels of Absen 4.8mm LED and a plethora of lighting fixtures, including Robe BMFL Blades, MegaPointes and Spiiders, as well as Ayrton Magic Blade FXs, GLP JDC1s and SGM Q-7s. “Most of the gear had to come from our HQ in Dubai as it required a huge quantity of each element and specific rider-driven kit,” Pudaruth noted, adding that around a quarter of the kit came from the company’s Saudi branch.
Pudaruth enjoyed working with the huge incoming team. “It was a delight to interact with all of the creative team involved in the overall project – their vast experience in their respective fields and professionalism was very refreshing,” he reflected, listing Production Glue, as well as Silent House, ElectricFly, Clockwork Production, Cassius Creative, High Scream, Visual Noise, Clair Global, One Three Right Studios, The Hive, Peritus, Hidden Road Studios and ER Productions. “It’s been a while since we had such a collaboration of creative minds working simultaneously on stage design and the results were mind-blowing.”
Recalling “one of the smoothest load-ins we have ever had”, Pudaruth was full of praise for the organisers. “The MDLBEAST team invested a lot of time and effort into planning and pre-production to ensure that they had the solutions to any challenges a supplier could possibly face,” he said. “To be involved in such a project is a real honour, and thankfully, we were up to the task. From the long months in pre-production to the load-in days, finally seeing the stages come to life was incredibly satisfying.”
Colour Sound Experiment was tasked with delivering four stages across the Underground Zone. “The brief was quite simply to build the biggest and most awesome rave ever!” said Managing Director, Haydn Cruickshank, adding that over 1,750 crew days from 50-plus people were required to deliver this project. “We dedicated a whole management team to the project for six months to deal with logistics, assets, crew, custom fabrication, lighting and video delivery,” he added.
The Colour Sound team worked with the lighting designer’s original plans for the stages, integrating them with the structural drawings and collaborating with other suppliers through many revisions. “The build for us started six weeks before doors, with a small team working with structural construction and custom fabrication,” Cruickshank described. “An advance production team started installing some lighting and LED four weeks out, main load-in started two weeks before the show, and final elements such as cameras, directors and operators came in three days before doors opened.”
Across the four stages, a huge 2,000 sq m of LED was supplied, including Leyard CLM6 and ROE Visual CB5. More than 3,000 lighting fixtures were also deployed, with GLP JDC line 1000, impression X4 Bar 20 and JDC1, as well as Ayrton Huracán-LT, Karif-LT and Eurus, and Claypaky Xtylos, Sharpy and Mini-B fixtures featuring throughout the rigs.
The unique nature of all the structures involved meant a lot of bespoke engineering and structural calculations were required. “Managing information flow across the many individuals and organisations involved was a challenge,” Cruickshank revealed. “However, the team we had on the project were outstanding – despite the scale and complexity of the project, everything felt very smooth. The intensity of the show was
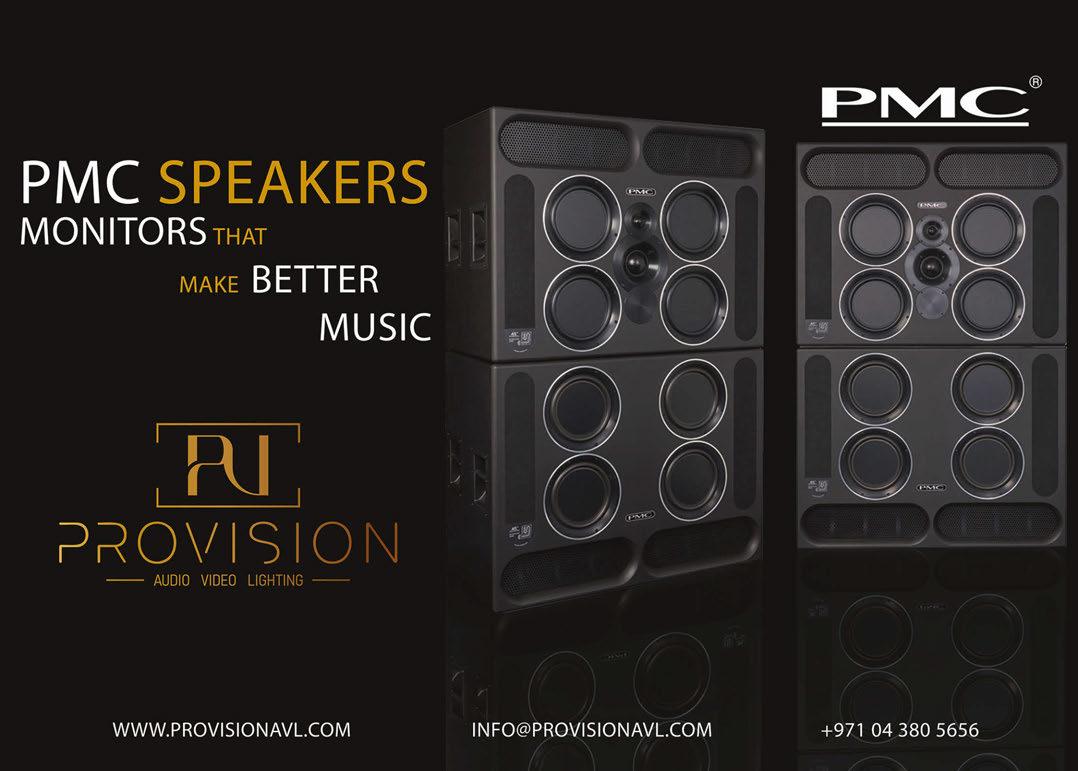
incredible; it’s hard for a large-scale, outdoor show to maintain an intense, intimate vibe, but the vibe was present throughout.”
‘SKILLS AND VISION’ Aggreko was appointed as the principal supplier of primary power for all technical aspects of the stage production. With the venue spread over more than 5 sq km and all stages using large quantities of LED, lighting and audio, the enormity of the task was clear for all to see.
“In total, we had 32 generators providing primary and backup power for the stages, with all the tech equipment backed up so there was no chance of losing power during the show,” said Matt Anany, Events Manager KSA.
The reverse current generated by the sheer size of the LED screens also provided a challenge. “This was all managed by a team of one project lead, three generator engineers, four stage leads (two of them doubling as site coordinators), six stage technicians and two technicians dedicated to monitoring diesel usage and ensuring diesel levels were maintained,” he explained.
“What pleased me the most was having a team of people from different parts of the world, working together to achieve a common goal, putting heads together to solve problems and finding workable solutions,” he concluded. “Watching a plan come together to make a successful event was extremely satisfying.”
Byrne Equipment Rental provided temporary buildings for staff offices across the site, as well as ablution units and sewage management facilities. The company supplied high-spec VIP ablution units in the required areas, illuminated the parking area with mobile lighting towers and provided a fleet of power generators for use across the entire site.
With boots on the ground from mid-October, Showforce provided stage crew, climbers, follow spot operators, crew chiefs and crew managers for the build, show days and de-rig. Working with both Stageco and Production Glue, there were more than 200 Showforce crew on site during peak periods and overall the team amassed an impressive 56,412 man hours onsite.
Work began with the build of The Big Beast stage. Working alongside Stageco, a team of almost 50 Showforce crew, including 10 experienced UK climbers handpicked specifically for the project, worked alongside local crew. A senior crew manager was in Riyadh throughout the build to ensure the smooth running of the project, liaising with the office-based operations team throughout. The 30-day build of more than 120 containers of kit made it a logistical challenge, but careful planning and the correct selection of crew ensured that everything flowed smoothly from the outset and the stage was completed a week ahead of schedule.
From the start of November, Showforce’s crew to support Production Glue arrived on-site and the unloading, preparation, distribution, and assembly of all departments’ kit began. This included over 400 lighting fixtures, 850 sq m of LED and 72 projectors. The crew also assisted departments at various locations across the site, including artist lounges, delay towers and projection structures. Showforce crews remained on hand to meet any further needs from all departments, including unloading backline equipment, assembly of stage risers and the general upkeep and safe storage of empties.
Showforce crew stayed in situ to assist all departments, unloading backline equipment, assembling stage risers, and storing empty flight cases safely. Working on and around show days, the crew supported each department with their requirements, providing standby personnel, follow spot operators, ground spot operators and stage crew.
Under guidance from the stage manager, the stage crew assisted in stage turnarounds and setup for individual acts, culminating in the setting of Jason Derulo’s risers then replacing them with the headline DJ riser, which required
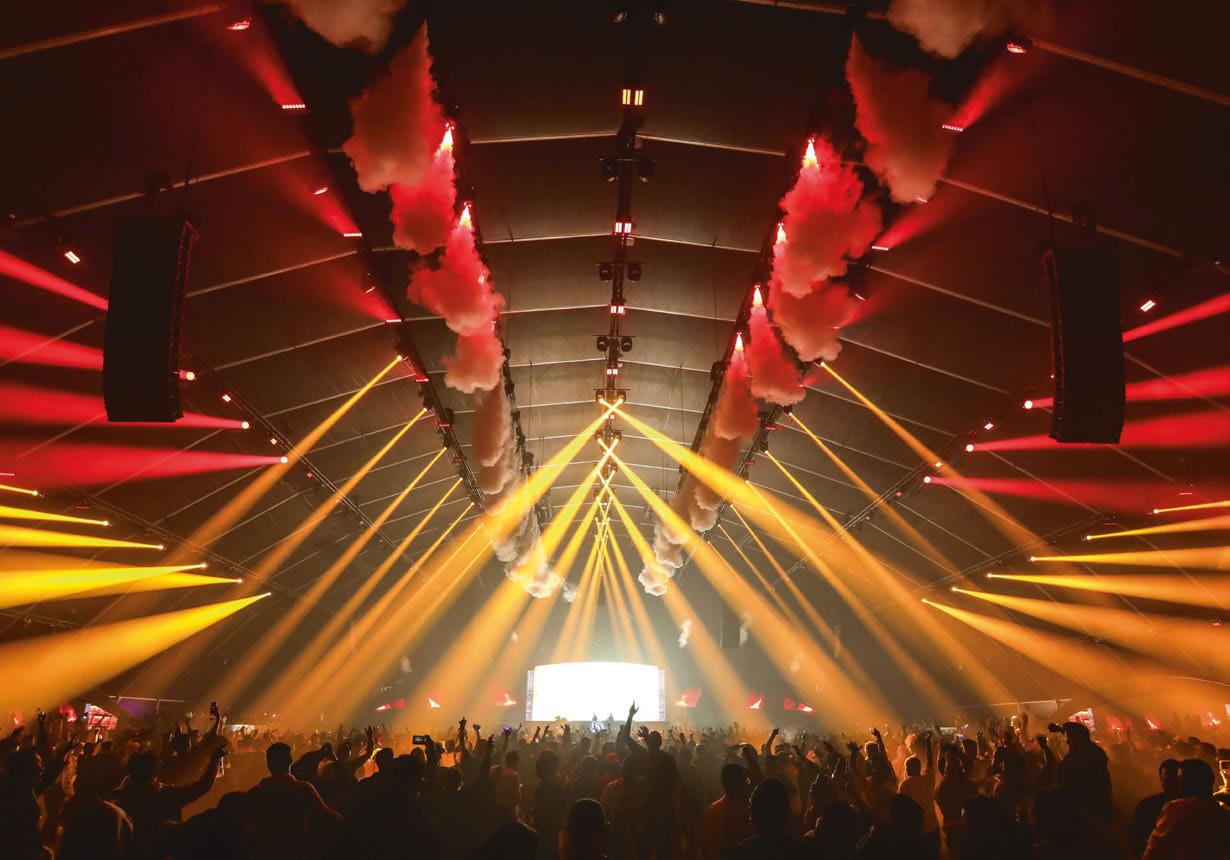
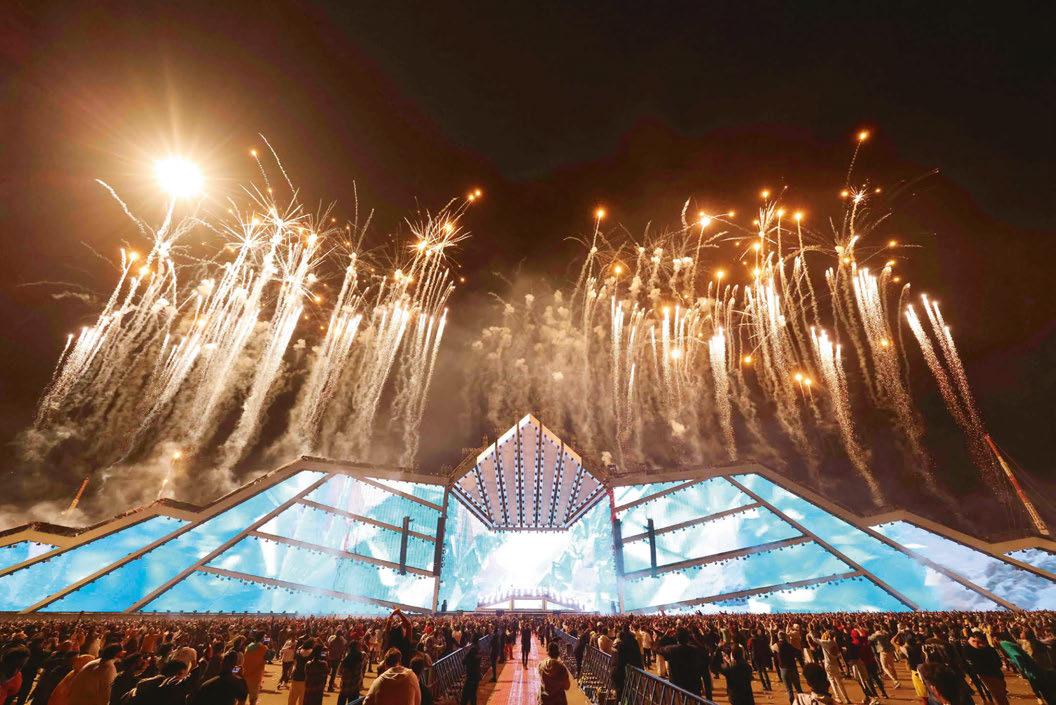
20 crew to manoeuvre. Crew also provided overnight assistance to the pyro department to help reload for the following show.
De-rig and load-out began immediately after the final act, with Showforce supplying crew to assist in the removal of priority kit and enabling works for the following morning shift. De-rig continued with all crew on hand to disassemble, pack down and load away all remaining kit. Crew also assisted Stageco in the removal of stage wings, front of stage access ramp and front of stage extension in preparation of the arrival of the working at heights-trained team. An additional team was supplied to assist IRMARFA at the Dance Beast stage, including IPAF operators, crew trained in working at heights and experienced ground crew.
Also contributing significantly to the crewing effort was Gulf Crewing Company (GCC), which provided 5,564 crewmembers, who worked a staggering 66,769 manhours between them over the course of the project.
“A significant amount of planning and preparation is required to ensure success for any event, but the ability to produce shows of this magnitude and at such a high level is testament to the skills and vision of the MDLBEAST team,” commented GCC Managing Director, Karen Beaton. “Saudi Arabia is an emerging market that is quickly becoming a staple on the Middle East tour circuit. Gulf Crewing is incredibly proud to be part of the Saudi journey and we couldn’t be prouder to be a part of these exciting projects.”
‘SHOOT FOR THE MOON’ It almost goes without saying that special effects and lasers are a vital part of any self-respecting EDM festival. So, it came as no surprise that Soundstorm pulled out all the stops in this regard, with ER Productions entrusted with delivering a complete SFX and laser package across all stages. “The thing that grabbed us immediately was the scale of the project – the saying ‘no expense spared’ has never been better placed,” opened ER Productions Creative Director, Ryan Hagan. “The producers were really putting their heart and soul into producing something incredible for the world to see and be in awe of.”
With the support of Pyrojunkies, which has recently become a part of the ER Productions Group [page 14] the ER Productions team designed the lasers and SFX for each stage with a “shoot for the moon” brief. “All our designs were produced in Syncronorm depence2, so we could present them visually to the lead creatives for each stage,” Hagan continued. “The bulk of what we produced, bar a few tweaks here and there, was what we saw on site. We certainly aimed high, and our priority was making sure that every stage felt individual.”
While the company has produced two Guinness World Record-breaking laser shows in the past, Hagan described Soundstorm as “our largest single show to date”. In all, 430 lasers, 100 smoke machines using 4,000 litres of smoke fluid, 140 confetti and streamer machines, 80 flame heads and 11,000 pieces of pyro were deployed. “We are known for manufacturing large quantities of lasers and producing more than 130 new units for this show was a proud moment for our technical team,” he said. “This included 100 of our AT-30 units, a 30W RGB white light head.”
Across all the stages, ER deployed 13 different laser fixtures, including the company’s new KINEKT AS – an audience scanning head fixture. With 32 of the fixtures used in total, six of the units were deployed on the indoor Underground 3 stage. “We needed a fixture that could be used safely in here as the effects shot all over the place due to the mirror clad-walls and ceilings,” Hagan explained, praising the design by Sam Tozer of Vision Factory.
In Dance Beast, the company deployed its new electric confetti blowers, which operate without the need for CO2. “It was great to be able to push on with a greener ethos in FX delivery,” he shared. “This has been a plan of ours for some
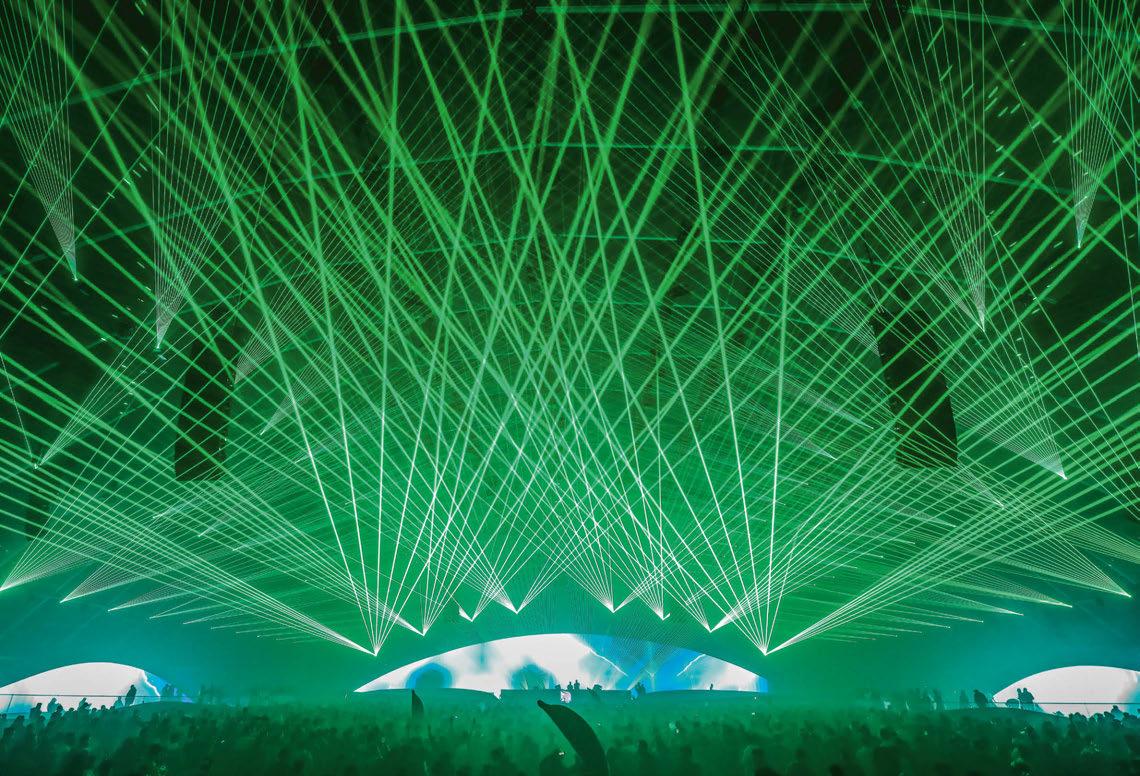
years now.” When it came to the Big Beast stage, Hagan stressed the importance of power and positioning. “It’s the biggest stage I have ever seen – it had the appearance of an eagle with its huge wings curling round the crowd stage left and right,” he recalled. “We wanted to give every audience member an experience, so spreading out fixtures across the space was critical.”
The AT-30 was the unit of choice for its pure power. “We had a lot of video and lighting to compete with, so we needed that kind of muscle,” he said of the fixture. “We opted for 66 of those, spread in layers across the stage. In between those layers, we then used smaller audience-friendly units.” The original plan was to use BB4 heads – “but Alex Reardon from Silent House, Lead Designer for Big Beast, was very interested in our KINKET AS units, so we swapped them for those instead.”
ER also increased its stock of Luminous Stadium Flames, with 18 on the main stage, spread across the width of the 240m structure. “To shoot all the pyro, we invested into the G2 Fire Control System from Sweden, purchasing 200 modules and five control desks.” Operation of each stage was varied, with some touring laser operators using timecode and some preferring to operate live. For those using timecode, two visualisation suites were set up. “This enabled us to programme for the artist or to allow their touring laser op to get their show up and running before hitting stage,” said Hagan.
“Having worked on the project from the beginning, I always love to see the result and see how our vision has been delivered, but more important than that is how it is received not only by the client, but by people around the globe commenting on social media and the festivalgoers there in the thick of it,” Hagan summarised, reflecting on the event.
“I remember one moment in particular at Dance Beast when a drop was coming during DJ Axwell’s performance. The blackout came and Alex [Oita, Laser Crew Chief, Dance Beast] turned on all 124 lasers and the cheer from the crowd gave me goosebumps.”
Hagan’s enduring memory of the festival remains the “simply impressive” Big Beast stage. “Everything about it left me with my mouth wide open,” he recalled. “I would often stand at the back of the stage and admire Stageco’s structure. It was an immense piece of engineering that we complemented with lasers, pyro, flames, confetti, streamers and cryo. The cheers from the crowd when hits of flame and pyro fire upwards and seeing our team smashing the cues out one after the other bang on time really is a great feeling. It’s moments like those that make me realise we’ve done our job properly.”
He concluded: “There are so many key people who worked on this project to acknowledge – too many to mention here – but we would like to thank Michael Jobson, Jim Digby and Matt Richman for entrusting us with this project and for having a vision to deliver one of the most spectacular events we have had the pleasure to be involved in, as well as the Saudi people, who made us feel so welcome.” Photos: MDLBEAST, Drew Ressler (www.rukes.com) Showforce, MediaPro, Amora Productions www.mdlbeast.com www.prg.com www.er-productions.com www.coloursound.com www.mediaproav.com www.showforce.com www.gulfcrewing.com www.aggreko.com
We’re proud to have delivered Stage Crew, Production Crew, Follow Spot Operators, Crew Chiefs and Crew Managers to MDLBEAST Soundstorm 2021
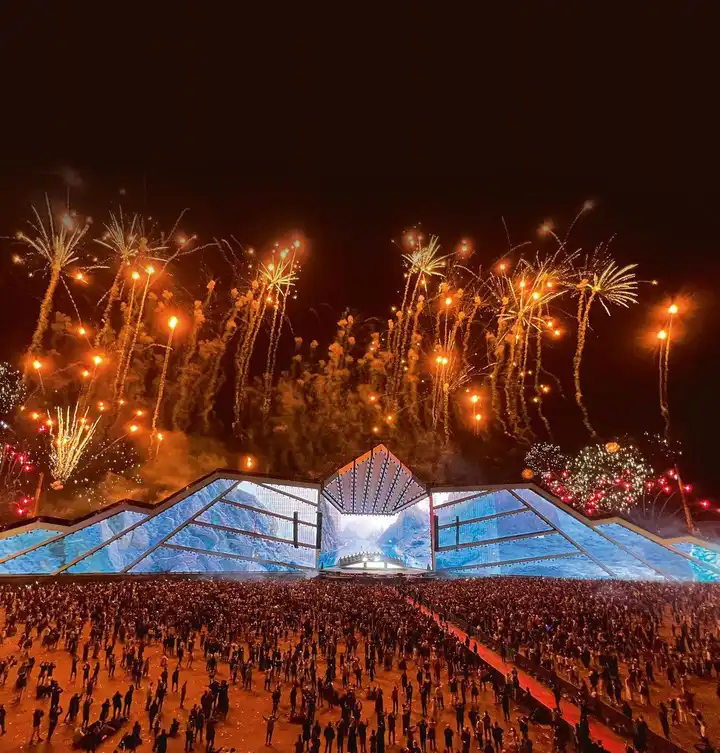
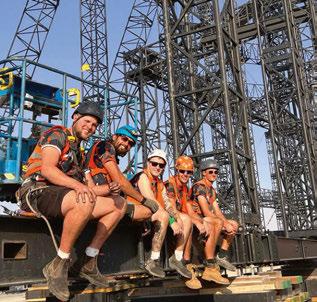
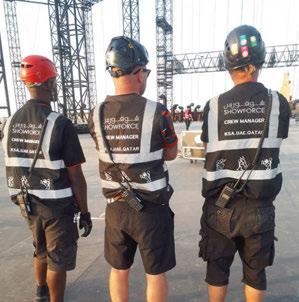
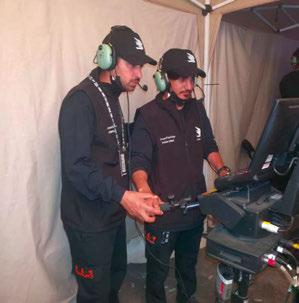
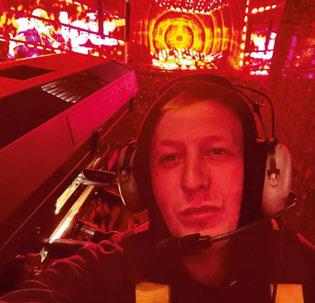