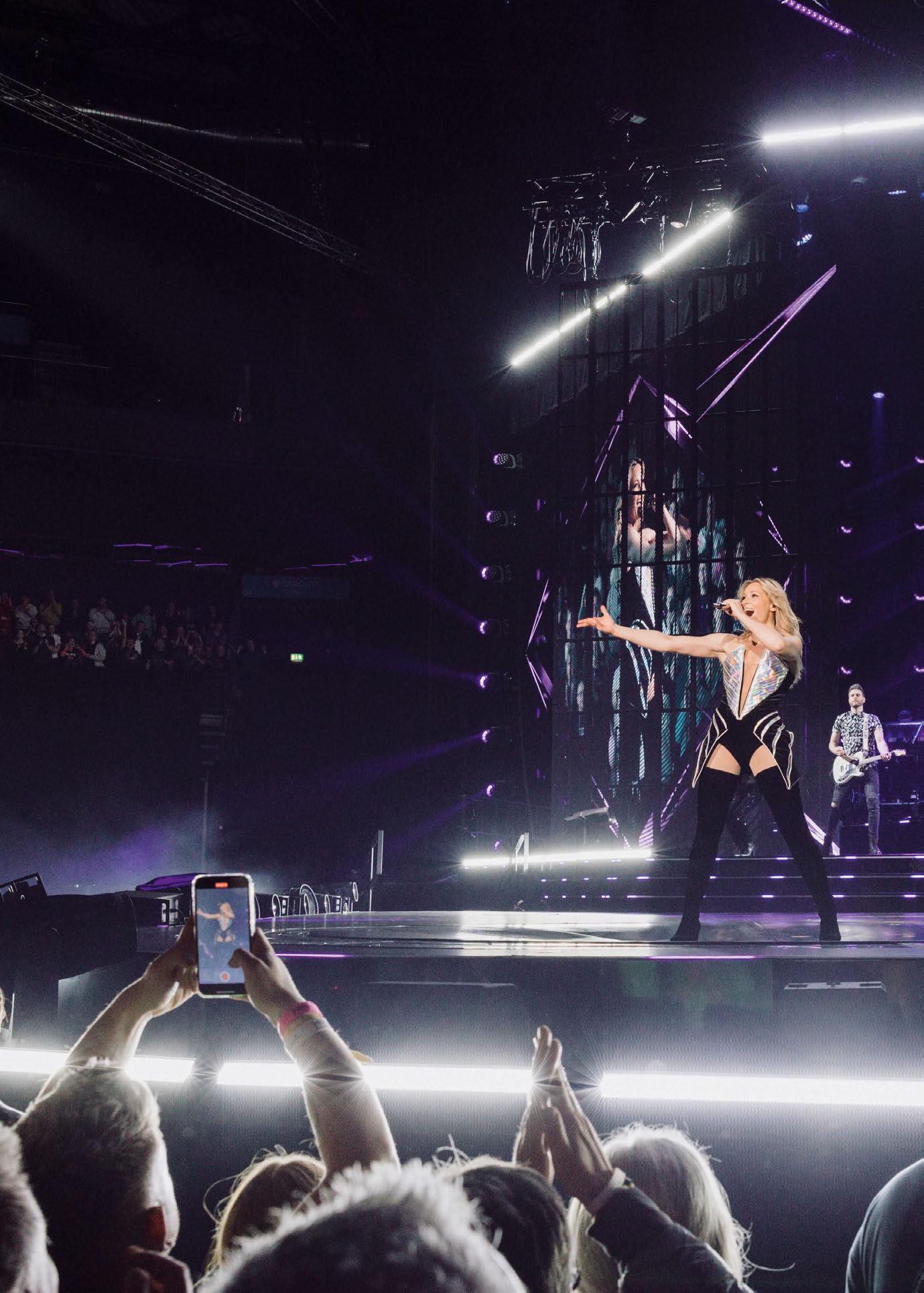
9 minute read
HELENE FISCHER: LIVE 2023
TPi travels to the German capital to witness one of the country’s most popular artists take to the stage and the air. With Cirque du Soleil assuming the creative lead, this production boasts spectacular moments and cutting-edge technology in abundance.

Although German superstar Helene Fischer may not yet be an international household name, it is likely that if you work within the live events sector, you’ll be familiar with her work due to the incredibly ambitious production levels on her live shows. The singer has featured in TPi Magazine several times – most recently during her 2018 tour with a focus on the production’s dynamic staging automation and set build. So, when we discovered that her upcoming tour would see Cirque du Soleil taking the creative lead on a 270° production, we couldn’t book our tickets quickly enough. Suffice to say, we were not disappointed.
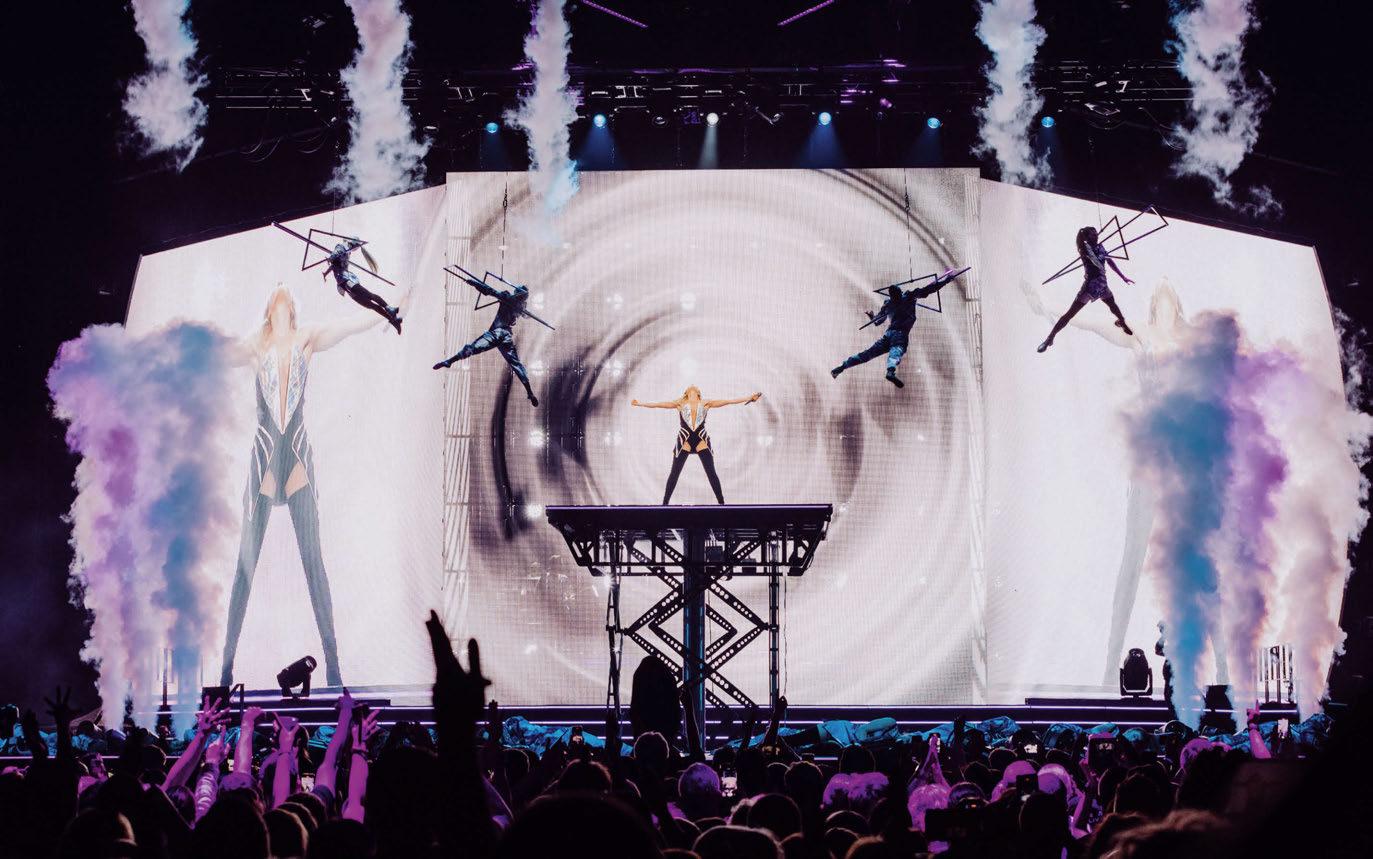
The production seemed to have a new gag up its sleeve with each song, from aerial acrobats appearing from the mother grid and an impressive water feature that could create images within the falling liquid, to a robot that had the singer spinning around the floor of the Mercedes Benz Arena among the crowd – and that is just scratching the surface.
A few hours before doors opened for the singer’s third night in Berlin, TPi was greeted at the stage entrance by Production Manager, Sebastian Pichel and Production Coordinator, Jeremias Klein. Before I had a chance to grab my dictaphone and camera, Pichel asked: “Are you good with heights?” After confirming I didn’t have an issue, despite being slightly bemused by the question, I was shepherded into the arena. However, instead of heading to the comfort of the production office, we made our way to a lift at the rear of the stage. Before I knew it, we were walking on the flown mother grid, several metres up. With sweaty palms, I clicked ‘record’ and began this unusual interview.
Pichel explained that he was “wearing two hats” for the show – Production Manager and Live Nation representative. “It has been advantageous with my knowledge from the Live Nation side as I know all the venues very well,” he stated, highlighting the logistics of overseeing the enormous set as it moved from city to city. “Helene falls into the genre of Schlager and it’s quite common for promoters to also produce the show.”
This was not the first time that Fischer had worked with Cirque du Soleil, although it marked the first time the company assumed a much more all-encompassing involvement in the creation of the performance. “Once they had a design, we sat down to select suppliers to help bring the show to life,” stated the PM. “Although this is a local show with dates in Germany, Austria and Switzerland, we were keen to select international suppliers used to dealing with large-scale productions.”
The show included a staggering 31 trucks and a mother grid structure that came in at 74 tonnes – the maximum that most German venues can accommodate without the need for ground support.
“Solotech made a lot of sense as a global supplier of audio, lighting and video,” continued Pichel. “We also had suppliers providing their own crew rather than the production bringing on all the personnel. It means that if anyone must leave, each supplier is responsible for replacing them, which makes life much easier for us.” He went on to express how happy he’d been with the “high-calibre international touring personnel” involved in the show.
WICREATIONS provided staging and automation, ER Productions supplied special effects, Crystal oversaw the deployment of a unique water feature, with Dart Rigging and Lüz Studio providing video content and ShowTex providing draping. Pieter Smit supplied coach services, while EFM Global aided with logistics.
One advantage the production had in its favour was that Fischer was playing multiple nights in each venue as most crew agreed that a back-to-back schedule simply would not work with this scale of production.
“Our local crew call is 100 for our load-in and out,” emphasised Pichel, who reported that so far, all venues have been able to meet these numbers of local crew – something that has been a struggle across the globe in recent months. “On each load-in day, we tend to start at around 11am and it’s around a 12-hour build,” he described. “It’s also a five-hour load-out before we move to the next city.”
Working hours were a major concern for the PM. “This is a tough gig for the crew, so from Wednesday to Friday when the stage is set, we don’t tend to want them back until 2pm most days, meaning that we don’t go over a 60-hour working week.”
Back on terra firma, TPi caught up with the familiar face of Tour Manager, David Salt. “I got the gig after four Zoom calls last year,” explained Salt, admitting that initially he hadn’t comprehended the scale of the production. “There are a lot of moving parts. When we started rehearsals at AED Studios, there were around 185 people on-site. There was only so much accommodation at AED, so we had to work out the logistics of getting everyone on and off site, which was a job in itself.”
Due to the scale of the show, moving equipment from Cirque’s Canadian HQ to Belgium for rehearsals in AED was quite a task – as was transporting the custom costumes made for the singer that had to be sent to a hotel in Munich. Jack Swildens, Project Manager for
Bringing water on stage
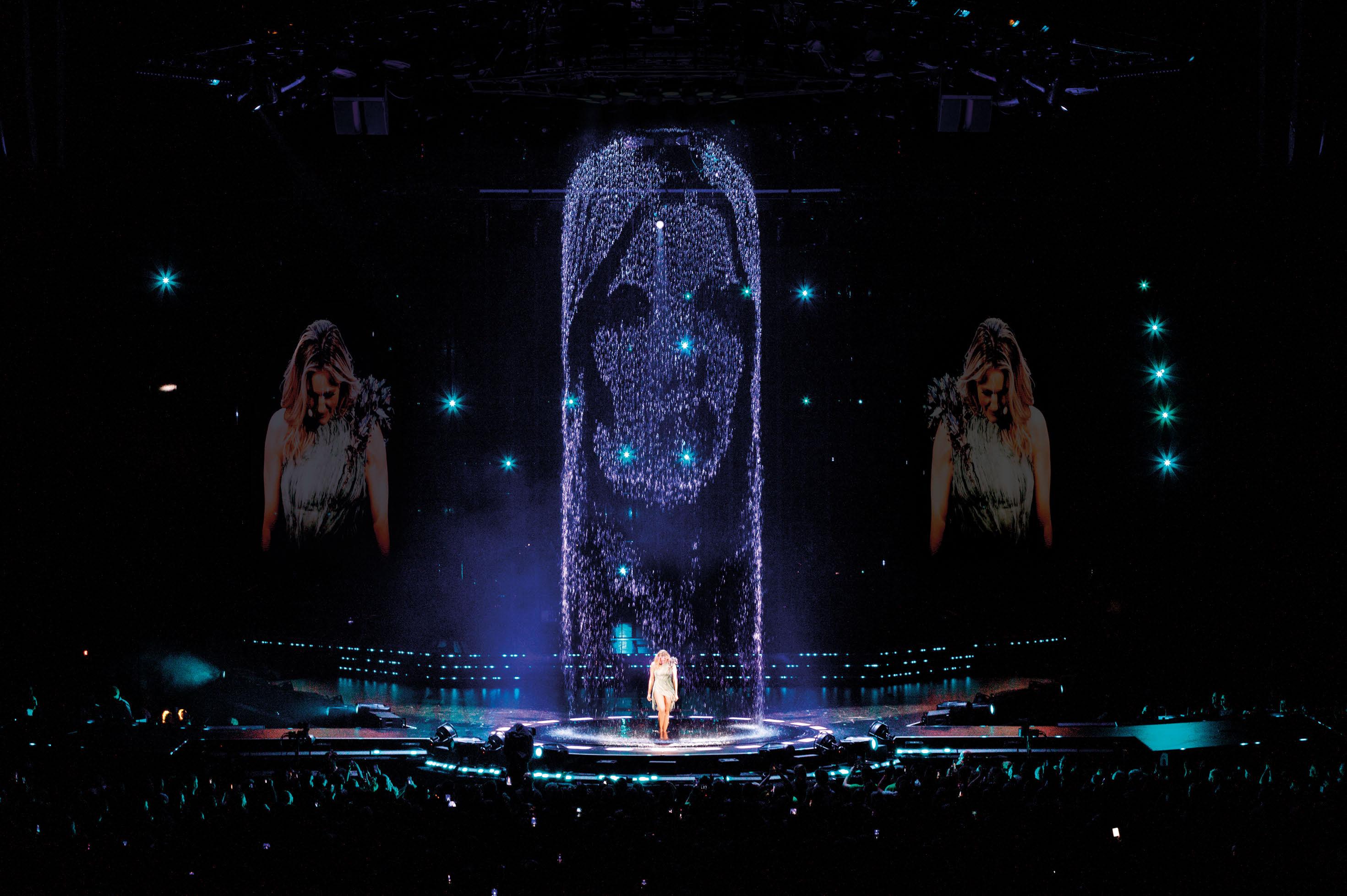
EFM Global, commented on the company’s part in the move. “Working to an explicit schedule, we flew the tour freight to Belgium and the show apparel to Germany. Helene Fischer was in Munich for a matter of hours, so it had to be at the hotel waiting.” EFM then returned the costumes to Canada where they were adjusted for the tour.
Due to the 360° approach to the production, the fact that Live Nation was responsible for the whole tour meant that the in-house team dealt with everything from hotels to flights. “It really is planes, trains and automobiles in this office,” joked Salt, who was quick to praise the support of Assistant Tour Manager, Lizzy Winter and Backstage Coordinator, Fenja Möller. “Without them, this job would have been a nightmare.”
Af ter taking a break in the summer, the tour is due to resume in mid-August. “We’re pulling the pieces together in August, which also includes a period where the Cirque team has to do a process called validation,” explained Salt. “It takes a full day to make sure everyone from the acrobatic side is up to speed with the show then after a few dress rehearsals, we’re back on the road until October.”
Setting The Stage
Starting work on this project in January 2022, Simon Lachance, Technical Design Director, spoke to TPi about the early days of the design process after being contracted by Cirque du Soleil to work on the show.

“Cirque’s travelling shows are very different to rock ‘n’ roll touring, and it was an interesting collaboration, melding two approaches,” he began. “The goal with this show was always to push boundaries. Live Nation wanted to put something on that was extraordinary, whereas Cirque was keen to create something special for the concert touring world – something it has not done for some time.”

Although this might not be your standard Cirque show, Lachance explained how he enjoyed the challenges of working within a different field. “The creative process within Cirque is very different and it was amazing to take all its experience and filter it into this project. There are constraints when it comes to live touring, but constraints lead to creative solutions, and we managed to push the limits.”
Matt Horton, Head Acrobatic Rigging, picked up the story: “One of our biggest concerns is that the show’s mother grid stays consistent for all the venues,” he stated. “If the height were to change for whatever reason, the entire programme would have to change due to the nature of the stunts. Thankfully, we have an amazing rigging team who ensure the height of the show is perfect down to the last millimetre.”
Due to the variety of venue sizes, the production created three different staging options – an A, B and C rig – that all have different trim heights. “There are too many performance winches and acrobatic elements that everything has to stay consistent for the show height,” the PM chimed in.
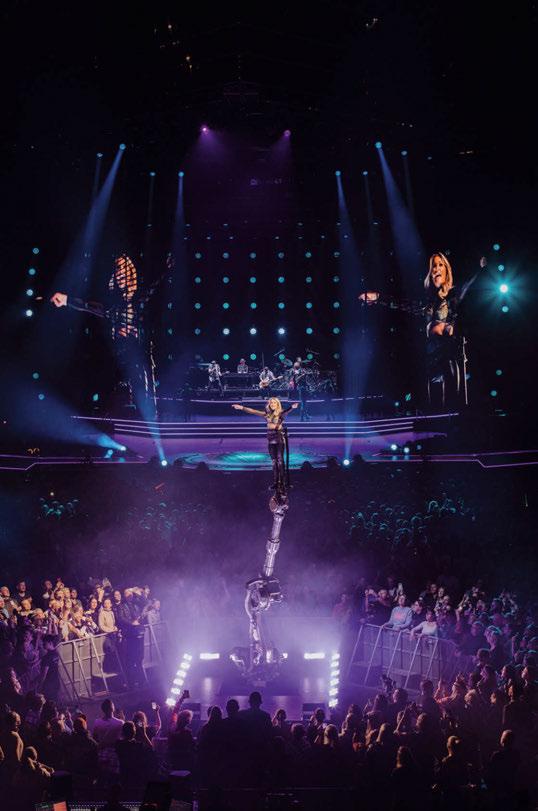
Horton outlined his daily schedule. “I come in at the top of the load-in and oversee the riggers hanging the heavy steel and stabilise everything to make sure it’s safe. When the catwalk is in place, my team and I busy ourselves with installing the ropes and Cirque systems. We then go about a rigorous test with the automation department to make sure we’re happy with the winches. Then we bring in the artist for validation. They then inform us if there is anything different from the previous show and we adjust accordingly.”
WICREATIONS was responsible for building this giant flown mother grid along with all staging and automation elements. “It was an interesting show for us in that although it was Cirque that first came to us with the request, we were dealing with three clients – Cirque, Helene’s Manager and Live Nation,” began Raf Peeters of WICREATIONS. “The production preferred to deal with one vendor due to the complexity of the show. In the same way Solotech were overseeing audio, lighting, and video, we were brought in to take care of all staging, automation and set elements. It also made things simpler for some inter-department collaborations such as the SFX elements with ER Productions along with working with Crystal incorporating the water effect in the mother grid and the stage.”
If t he show wasn’t complex enough, Peeters highlighted the difficulty touring a show through Germany and with the new regulations that are now in place in the country thanks to the new safety norms in the DIN EN 17206 legislation.
“T he new regulation has defined better what SIL3 requirements are needed for stage machinery and when it comes to automation you now need a very specific safety-related control system,” stated Peeters.
“T hankfully, our company has been working in accordance with these regulations for some time now, putting us in a good place. It also made us able to take care of some very specific requests from the Cirque.”
Crew Chief, Pieterjan ‘PJ’ Nouwynck was tasked with overseeing the build from day to day. Due to the scale of the show, PJ had a team of seven with two additional crew members aiding with the load-in and -out. “It’s a beast of a stage and everyone involved can be very proud of their contribution,” he remarked.
There were three different types of lifts – an upstage chain hoist lift, a mid-stage toaster and a downstage scissor lift. “The mid-stage personal lift needed to be compact and lightweight whereas the upstage lift needed to be able to deal with 1.2 tonnes of weight.”

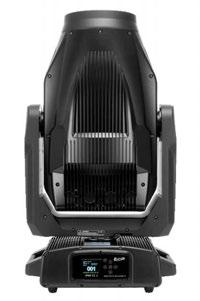
WICREATIONS also provided an automated video screen that functioned via an actuator system that revealed and hid the band as well as acted as an entrance for Fischer’s husband, who performed a few aerial acts with her.
Meanwhile, there were eight performance winches in the roof, along with a further five to move a kinetic ring element used in the opening act of the show. “We also have two winches downstage on the mothergrid for the B-stage for several moments,” explained PJ.
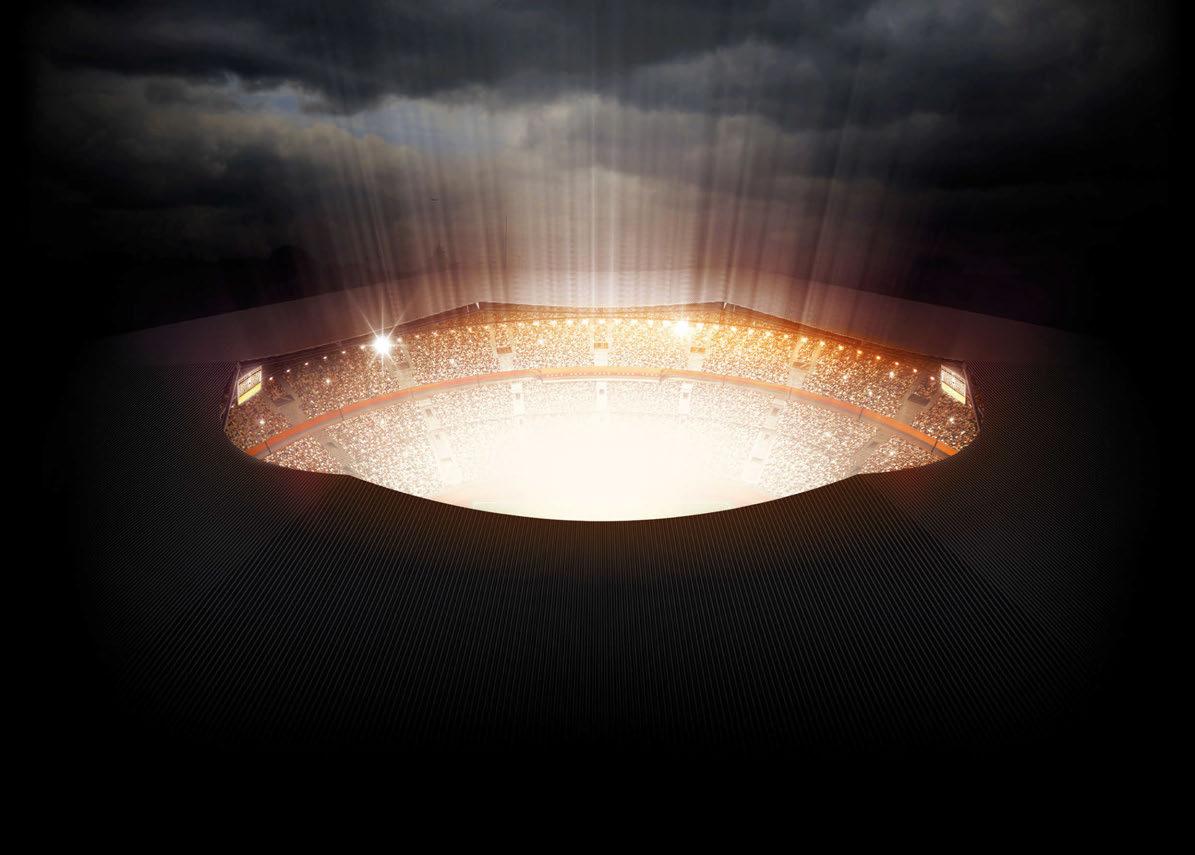
While PJ was going through the elements of the B-stage, TPi couldn’t help but ask, where exactly was the B-stage? “It is ‘created’ during the intermission of the show,” explained Peeters. “Cirque was keen for there to be a ‘human move’ where the B-stage would be built. It took a great deal of planning and coordination with the security staff to ensure we could move the stage into place, as it must be aligned perfectly with the roof. We’re happy with the outcome.”
The show marked a first for WICREATIONS in delivering everything as a total package. “Usually there is another vendor involved doing the staging or winches. WICREATIONS is not just a fabrication company but it has mechanical and structural engineers working full time. It is a different approach to others in that we can jump on any engineering issues immediately and give customers a confident answer to anything that involves the structural integrity of a show.”
Preparation Is Everything
Due to the complexity of this set build, the production drafted in the help of Wonder Works to aid in the technical drawings of the show. “Our first conversation was with Cirque du Soleil’s appointed Technical Design Director, Simon Lachance, to start creating CAD drawings for the show,” stated Rebekah Hanbury.
“W ith the three different highlight configurations, we ended up creating three different CAD packages for each. In these CAD drawings, we outlined not only set build but also all the aerial looks and SFX.”
Esteniah Williams oversaw the creation of these complex CAD drawings. “We ended up creating some large files showing all the various moves in the rig as it was useful for the entire team to see every moment during the show. It was an interesting challenge as there were a lot of ideas to bring together and it required constant communication.” As well as providing an imperative service in terms of visualising the look of the show, Wonder Works went one stage further using its animation team in the office to create a sneak preview of the show before it hit the road. “We took Esteniah’s CAD drawings and used Rhinoceros 3D: Rhino to give Live Nation a video file, so fans could see what was in store for this incredible production,” Hanbury said.
“B ringing in Wonder Works was one of the best moves we made,” enthused Lachance. “Their knowledge of the European market was vital and their detailed plans of all the key moments of the show was vital when it came to storyboarding to keep everyone in the loop.”
Let The Water Flow
Within the entertainment world, if there was a list of elements most productions would wish