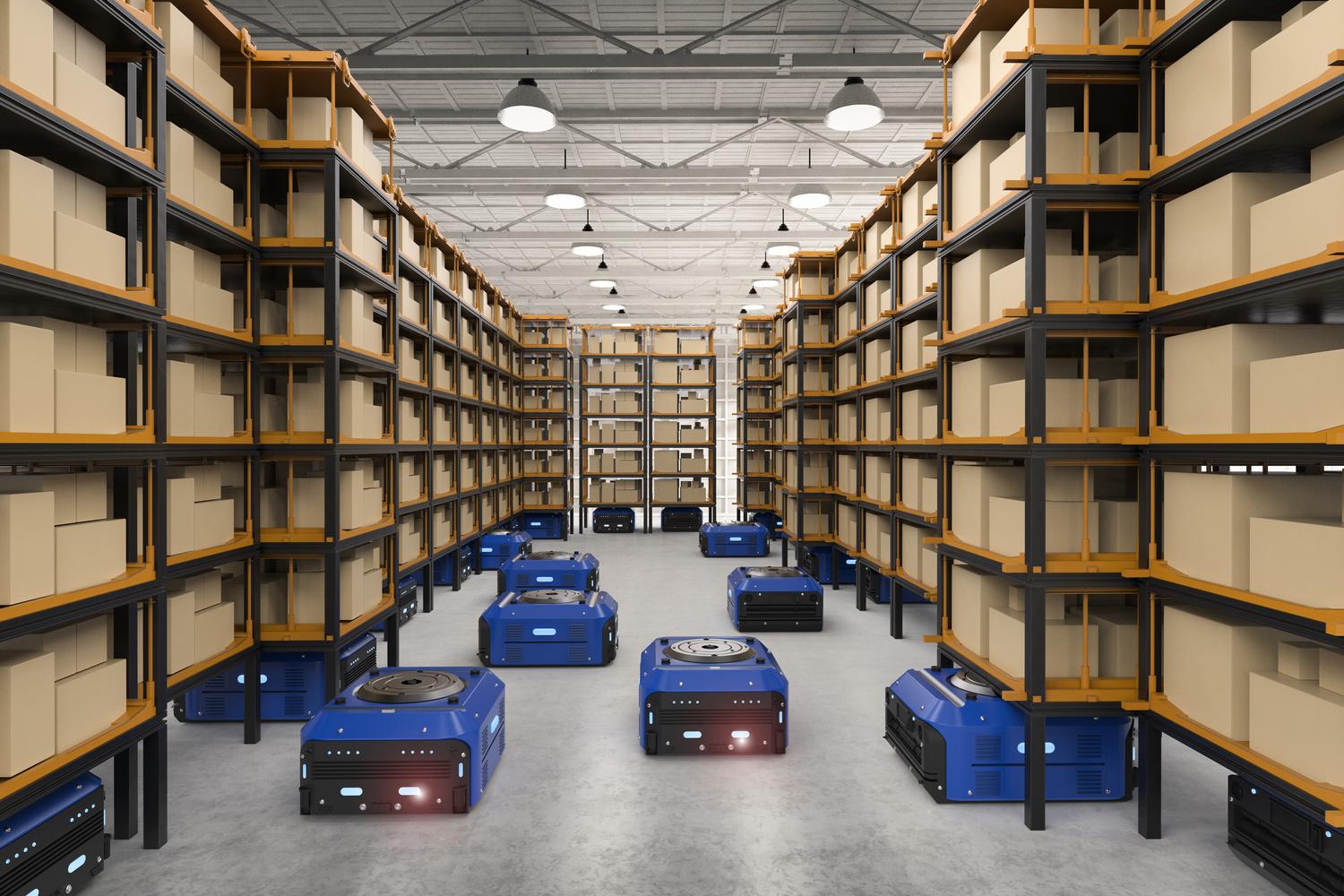
3 minute read
ECOMMERCE FULFILMENT TRENDS
By Rob Gamage, Managing Editor at Modern Retail
Ecommerce is a continuously evolving industry, and developments in fulfilment and logistics play a significant role in developing the online retail landscape of the future. Modern Retail spoke to Edward Hutchinson, Managing Director of BITO Storage Systems, to get his take on today’s ecommerce fulfilment trends…
Advertisement
MR: What recent improvements have we seen in ecommerce fulfilment?
EH: Through continuously optimised capacity planning, it has become possible to react more quickly in the event of bottlenecks. The use of software and greater productivity have led to increasing warehouse capacities as well as greater transparency of data. There has been an increase of digitalisation and automation through the use of robots, cobots and AGVs to, for example, automate picking and packing processes and general internal logistics.
AI can increase productivity and minimise errors in a wide range of processes including product demand forecasting, inventory management, transport capacity planning, controlling AGVs and robots, and optimising picking processes.
The Internet of Things (IoT) where sensors on devices report back information, creates a data highway in a company and is becoming more necessary for modern WMS. This might feature RFID scanners automatically recording the receipt of goods in the warehouse and passing the information to the WMS, which in turn informs robots of the specified storage location. Replacing barcode scanners with RFID scanners, which only have to be aligned in the direction of RFID transponders on the articles, makes multiple or bulk scans possible.
MR: What can we expect the ecommerce fulfilment processes of tomorrow to look like?
EH: Automating more of the intralogistics process will ultimately reduce cycle times, which will enable operations to extend order cut-off times, thus improving their service offering. Continual developments in modularity, sophisticated control systems and performance will increase warehouse automation’s practicality and flexibility for fulfilling omnichannel retail. This means automation is stepping closer into the economic justification zone for more operators who are juggling higher volumes, growing demand for faster order fulfilment and greater value on the one hand, with rising staff costs on the other.
These factors are merging into a trend that is seeing automated ‘goods to picker’-based order picking installations increasingly being integrated into intralogistics systems. While larger organisations grapple with the kind of robotic technology that can perform such dexterous tasks as picking individual items for ecommerce orders – which remain some way off from practical application – smaller operators have opportunities to benefit through simple and more attainable automation and robotic systems which are available now, as well as ‘mechanised’ solutions, such as live storage. Such systems provide a rapid payback because they do not require elaborate infrastructure or a large capital commitment, but they do provide a stepped approach towards fully fledged automation.
Some of the most exciting developments are likely to evolve from storage solutions created by companies that offer the requisite experience and expertise to address a specific customer need.
MR: How can advances in AI improve fulfilment?
EH: The rapid development of Artificial Intelligence (AI) is leading to the rapid development of process optimisation – ie, the task of analysing workflows, documenting them, uncovering weaknesses and developing an improved workflow. In addition to smoother processes and improved quality, cost savings can be a further goal.
There are many possible applications for optimising processes and workflows in a manual warehouse. Classic methods include value stream mapping, process mapping, total quality management, LEAN, Kaizen, and Six Sigma. In the context of digitalisation, however, new developments such as digital value stream mapping, process mining or motion mining are increasingly gaining ground. With the help of these applications, a large amount of data can be collected digitally, which means it can no longer be evaluated and interpreted manually using classic methods. AI solves this challenge. With the help of big data analysis, structures and dependencies in the data can be recognised and identified, which gives the planner, in addition to those responsible for operations, a variety of targeted options for action to optimise processes.
There are possible uses for AI applications such as process mining and motion mining in almost all areas of intralogistics. Examples include inplant transport (forklifts and other industrial trucks, as well as continuous conveyors), process analyses with corresponding performance and quality data, and motion analyses during picking and packing. Another essential aspect, in addition to the identification of quality defects and ‘waste’, is the improved ergonomic design of work processes. For this purpose, a virtual model of a warehouse is usually created. With the help of this ‘digital twin’, simulations of warehouse workflows and processes can be carried out to optimise storage locations.
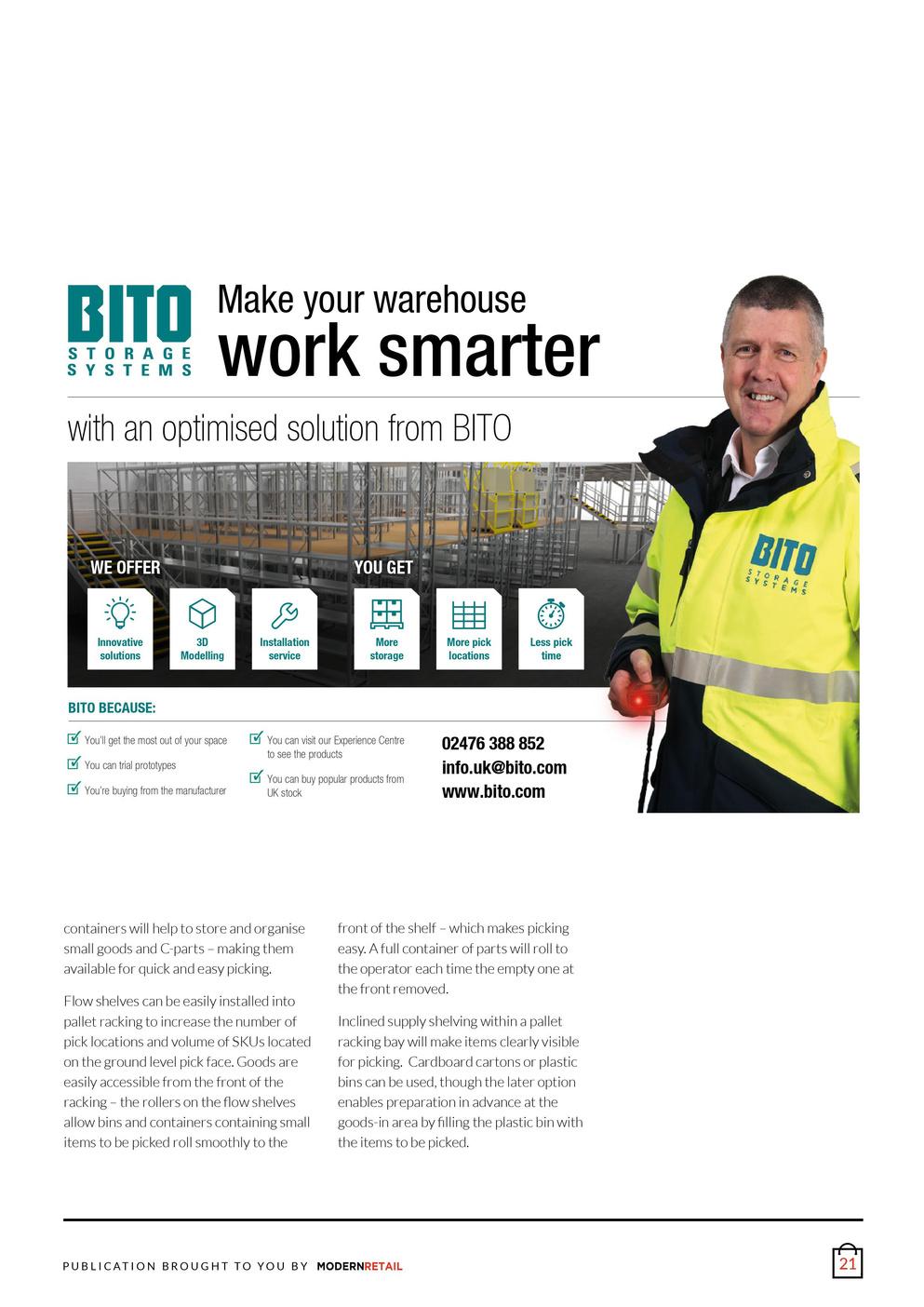