
3 minute read
Sound planning and implementation, desired results
Powder X-ray Diffraction (PXRD) is regarded as a convenient technique in the Identification and quantification Of Crystalline Material In Rock Samples, where conventional techniques fall short. But it can only deliver the desired results through sound planning and implementation in the process of sample preparation.
By Jimmy Swira
Advertisement
Mining companies are in continuous pursuit of alternative methods that are safe, cost-effective and efficient in processes involving exploration to mine closure and rehabilitation. This is evident in the sampling of particulate materials, clays and other minerals, where X-Ray diffraction (XRD) has emerged and indeed is widely regarded as an alternative method.
If planned and implemented effectively, XRD offsets the limitations encountered with techniques such as optical microscopy, scanning Electron Microscope/Energy Dispersive Spectrometer (SEM/EDS), and Quantitative Evaluation of Materials by Scanning Electron Microscopy ((QEMSCAN™) in applications requiring rapid phase identification and quantification.
Identifying the diffraction patterns
In XRD, powder diffractometers, modern computer software and an extensive mineral database are used to identify the experimental diffraction patterns. Typically, analysis is performed on a pulverised sample, and then data is acquired for mineralogical (phase) analysis.
Ideally, sample preparation should be routine, without a few glitches, if any. However, as far as analysis goes, the accuracy of the mineralogical data obtained is as good as the effectiveness of sample preparation.
Fortunately, state-of-the-art technology has simplified some tasks, enabling rapid and accurate delivery of results. Nonetheless, technology does not solely offset the effects of poor preparation.
Hence, the significance of sound sample preparation should not be overstressed.
Significance of sound sample preparation
A few years ago, Dr Deshenthree Chetty, South Africa · Head - Research of the Mineralogy Division at Mintek, briefed this writer about the significance of sound sample preparation in XRD. She said XRD can only yield desired results only if correct procedures in sample preparation are followed, as well as if relevant instrumentation is utilised.
An an article from the University of Alberta in Canada, School of Science (Faculty of Earth and Atmospheric Sciences) echoes this point. It is titled: “Powder X-ray Diffraction (PXRD) Technique For Identification Of Crystalline Material In Rock Samples“.
Meticulous planning and implementation
Sound sample implementation entails meticulous planning and implementation. Specifically, the following steps are critical:
• Nature of the sample
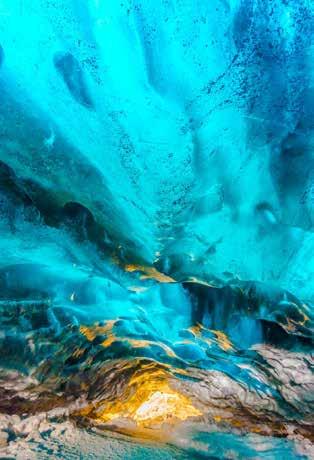
At the outset, special attention should be on the nature of the sample. As XRD is based on crystal structure, it is important to gather background information on the chemical composition of samples to be analysed. “Due to crystal structure, some minerals may show overlapping peaks and chemical composition would inform which mineral is present for instance, some samples will decompose on exposure to X-rays. Even more, highly hydroscopic samples that will expand or liquefy in the air are not recommended for X-ray diffraction analysis. Liquids that are not suitable are a no-no,” Dr Chetty stated.
The article from the University of Alberta expounds: “Some samples are easier to prepare than others. Depending on the hardness, habit, reactivity, etc. of the phase(s) in the sample different preparation techniques are required.”
Ideally, samples should be crystalline. While Amorphous can be determined, they cannot be identified.

• Sample height
It is paramount that the surface of the sample is level with the surface of the holder to maintain the geometry in the BraggBrentano set-up. This is because sample height impacts the peak positions in the diffractogram.
Granted, this can be corrected. However, it should be done correctly when mounting the sample.
Most importantly, the sample should be pulverised finely. Hence, micronizing is preferred to reduce micro-absorption effects and other artefacts on the diffractogram that could hamper mineral quantification.
Usually, a small particle size distribution is needed. “Ideally, the particle size should be as small as possible, for example, -10 µm, whilst ensuring that you do not start to destroy crystallites and reduce crystallite size,” Chetty indicated.
However, micronizing might take some practice. This is because samples can be composed of soft and hard minerals which will mill differentially. For this reason, the diffractograms should be inspected to determine the quality of the preparation.
Ultimately, the University of Alberta says proper grinding (finely powdering a sample) helps in achieving the following conditions to get good data:
1. Total randomness of crystallite orientations
2. Sufficient number of crystallites to get a representative intensity distribution for the sample
3. Sufficient diffraction intensity to meet satisfy counting statistics
• Instrumentation
Once sample preparation is complete and all boxes have been ticked, it is paramount that a suitable instrument is selected. This is because the instrument configuration and parameters impact the geometry of the beam and, by extension, the quality of the data.
In particular, the kind of application and the quality of data required will determine the instrument configuration to use. For industry projects, good detectors and versatile tubes are necessary. Changes can be made depending on the nature of the sample, for example, radiation used (Co, Cu, Fe tube), slit sizes, longer counting times, step size, and 2 theta range used.
Additionally, appropriate software to process the X-ray diffractograms and access to comprehensive structure databases for pattern matching or quantification routines is essential.
Accurate data, key decisions
All in all, from the foregoing, the significance of sound sample