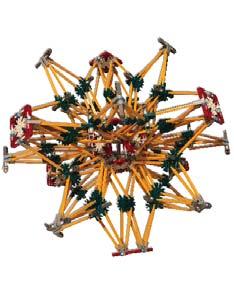
12 minute read
Transformable/ Deployable Structures: Caroline Yanson Video: https://youtu.be/AtUbnL-QS8c
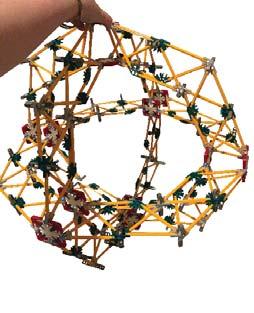

Advertisement
TRANSFORMABLE/ DEPLOYABLE STRUCTURES
CAROLINE YANSON
INTRODUCTION I am exploring the design of Transformable/ deployable structures by building a model of a Hoberman Sphere & 3D printing my own joints with the goal of understanding how these structures work via the “scissor hinge”. Transformable/deployable structures are expandable & contractable for storage, transportation, reuse, & adaptability (DeTemmerman, Roovers, Mira, Vergauwen, Koumar, Brancart, Mollaert, 2014). They evolved in history starting from their use as Egyptian hunter chairs & Mongolian nomadic yurts (mira, 2014) (Figure A). Today, applications of transformable/deployable structures are widely used in everyday objects: umbrellas, store gratings, tents, foldable furniture, & more (Figure B). Designer, Chuck Hoberman, increased the popularity of these structures from his creation of the Hoberman Sphere (Figure C). His work, among other designers’ work, have inspired more interpretations & developments of these structures.
FIGURE A: Transformable/ Deployable Structures in Historic Applications
Egyptian Hunting Chair (Pamperin, (n.d). Mongolian Yurts (Arneill, 2017).
FIGURE B: Everyday Applications FIGURE C: Designer, Chuck Hoberman Transformable/deployable structures apply today in many fields: the military uses them as shelters, NASA uses them in space exploration, the medical field uses them as temporary care units in disasters, etc (Merchan, 1987). The possibilities of such structures are endless! These, though complex & intricate, can be designed & produced in an easier manner via AEC technology, such as softwares, Rhinoceros & Grasshopper Plug-in, Karamba . AEC programs perform simulations, model structures, & calculate algorithms ensuring stability, geometry, & effectiveness. AEC allows the architect, engineer, or contractor to understand the structure & assembly. Then, they can either manually assemble or digitally fabricate the structure. Because transformable/ deployable structures have little available/ easy softwares for the general public (DeTemmerman, Roovers, Mira, Vergauwen, Koumar, Brancart, Mollaert, 2014)., I predict that there will be a future trend of easy-to-use software development aiming accessibility to a wider audience (Figure D). I also predict that transformable/deployable parts will be designed for mass production to make assembly more efficient.
FIGURE D: GARTNER HYPE CYCLE FOR AEC TECHNOLOGY
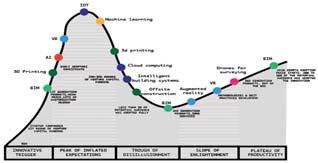
CASE STUDY 1: Universal Scissor Component, Workshop Led by Niels De Temmerman, London, 2011 (Mira, 2014) This is the development of a universal scissor component (USC) used in an icosahedron scissor dome made of wood. They used Rhino to create a parametric model & Karamba for structural analysis & mathematic algorithms. The parts were laser cut MDF boards manually connected to wooden struts by bolts. This design is reducing the number of materials, & therefore, waste, by designing for adaptability & structural reuse of the USC. In theory, scissor components in transformable/ deployable structures, are complex & generally designed for a single purpose. By creating the USC, it makes it simpler to design a transformable/deployable structure because the scissor component can be mass produced & applied to different shapes & sizes of such structures. The adaptability of a uniformed component will ultimately lower the production cost & make it easier & faster to set up & take down.
CASE STUDY 1: WOOD DOME ICOSAHEDRON

Full Scale Icosahedron Dome with the Universal Scissor Component (Mira, 2014).
Assembly of Universal Scissor Component - Contracted (Mira, 2014). Assembly of Universal Scissor Component - Expanded (Mira, 2014).
CASE STUDY 2: The Hoberman Arch, Chuck Hoberman, Salt Lake City Utah, 2002, ( Hoberman Arch, 2020). This structure is a motor operated aluminum arch with rigid covers that acts as a stage. It expands & contracts like an “iris of a human eye”. Hoberman employs his prior design of a scissor-hinge mechanism, but adapts it by angling the hinges in a ring & attaching 2 of the same angulated bars to a revolute joint. As a result, he created the largest transformable structure of the time. By attaching the rigid covers to the parts of his structure with angles, the covers did not get in the way of the motion of this structure. Hoberman’s use of rigid covers provided safety and shelter from weather conditions & avoided many of the problems that membrane covers had for other designers in the past.
CASE STUDY 2: WINTER OLYMPICS HOBERMAN ARCH
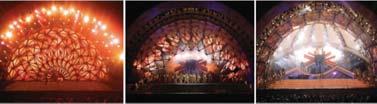
The Hoberman Arch at the Winter Olympics (Yenal, 2010).
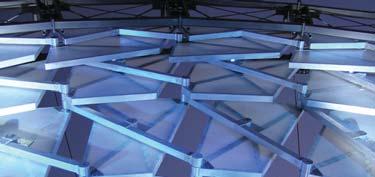
Hoberman Arch’s Motorized Structure with Rigid Covers (Hoberman Arch, n.d).
CASE STUDY 3: Transformable Dome, Iran, Maziar Asefi & Soheila Aram, 2017 (Asefi, Aram, 2018). This design is a transformable dome that uses rigid covering panels to cover the space when expanded. The rigid covers are attached to the interior of this surface, giving the benefit of extra warmth in cold places. It is smart to use detached rigid covers for it allows the installation to act as unitized modules. That way if one of the cover panels needs repair, they can do it without having to dissemble the whole thing. They designed this model through the computer model of Rhino, then manually assembled the pieces. Overall, they created a great precedent from which others can 76 learn stability, weather protection, & more.
CASE STUDY 3: TRANFORMABLE DOME WITH KINETIC ELEMENTS

Rhino Model of Transformable Dome Using Kinetic Elements (Asefi, Aram, 2018).
HYPOTHESIS If I learn possibilities of transformable/deployable structures, model 1 out of K’nex pieces, & finally, 3D print scissor hinges, than I will have a comprehensive understanding of how these structures work in regard to the AEC industry PROCESS I am exploring how transformable/deployable structures are assembled & how they expand & contract in different forms. I completed my project in 3 parts: PART 1: WOLFRAM SOFTWARE SIMULATIONS I logged into the Wolfram software & visited “Scissor Hinge Simulation” (Berczi, 2007) , “Expanding Fence Simulation” (Kabai, 2007), “Expanding Tower Simulation”(Kabai, 2008), & “Deployable Shelter Simulation”(Kabai, 2020). I experimented by changing the control variables that go into making the components of such structures. PART 3: 3D PRINTING SCISSOR JOINTS I wanted to learn how to 3D print, so I am 3D printing a 3D & 2D scissor hinge. The first step was finding a computer model of a Hoberman Sphere so that I could extract the 2 forms of scissor hinges to 3D print. I found a model that was already made on Thingiverse (Badro, 2014)- a website of shared, 3D models that the public can use to 3D print.
WOLFRAM SIMULATIONS Scissor Expandable Fence Expandable Tower Deployable Shelter ORIGINAL MODEL 3D PARTS I AM PRINTING MY ASSEMBLY GOAL
3D Model from which I extracted the parts (Badro, 2014). 3D Connector One Pin Arm Two Pin Arm Cap 2D Scissor Hinge 3D Scissor Hinge
I downloaded my files to Cura (Cura, 2017), where I rotated & arranged each piece on the bed & set the 3D printing settings. s se ettings sg . CURA 3D PRINTING SOFTWARE
3D printer settings prep (Cura, 2017). How I arranged & rotated my parts on the 3D printing bed (Cura, 2017).
I saved the Cura file to a USB, plugged it into the 3D printer, added the PLA blue filament & selected “print”. I printed each different piece as a separate print. In total, the actual time it took to 3D print was only 3 hours. t to oo ok k to o 3D D p 3 ho ou urs sr .t t wa aw s s on o ly ly 3D PRINTING PARTS PRINTED- NOT ASSEMBLED
Exploration of how the number of scissors determines the expansion & contraction of the computer model (Berczi, 2007).
Screenshots of my exploration of different heights of the scissors & how they can be formed into a closed circle (Kabai, 2007). Screenshots of my exploration of how the scissors bending angles can be manipulated to form a closed structure (Kabai, 2008). Screenshots of my exploration of how the scissors can form a shelter (Kabai, 2020).
PART 2: MODELING A HOBERMAN SPHERE OUT OF K’NEX TOY PIECES To model a Hoberman Sphere, I followed a tutorial (Mosely, 2017). To begin, I collected the K’nex pieces I needed to build the model. K’NEX INVENTORY 48- short green rods 96- grey 2 prong connectors 96- grey 1 prong connectors 96- red 3 prong connectors 96- blue spacers 192- yellow long rods 12- white 8 prong connectors
DOCUMENTATION AND INSTRUCTIONS
My infographic 3D printer in King Library’s Makerspace. Caps Printed 3D Connectors
One Pin Arms Caps
Two Pin Arms
I assembled the 2 scissor hinge types. I had some difficulties fitting some of the pieces together, so I took an Xacto knife & cut out excess material that resulted from the 3D printing process. I also printed cap pieces, but it turned out that I did not need them. Overall, the process was educational & I accomplished my goal of showing the 2D & 3D scissor hinges. ASSEMBLED 2D SCISSOR HINGE ASSEMBLED 3D SCISSOR HINGE
Expanded How 2D arms connect to the 3D hinge Contracted
DISCUSSION REFERANCES Arneill, P. (2017). My Shot. Retrieved April 6, 2021, from https:// www.nationalgeographic.orgencyclopedia/ yurt/ Asefi, M., & Aram, S. (2018). Flexibility in Architecture: An Innovative Design-Covering of Transformable Dome Using Kinetic Elements,41-52. Retrieved April 6, 2021, from http://soij.qiau.ac.ir/ article_545 286_9b62172367beefe52344cca1d9bcfcea.pdf Badro, A. (2014). STL. Thingiverse MakerBot Industries, LLC. Bérczi, S. (2007). “Nuremberg Scissor” http:// demonstrations. wolfram.com/NurembergScissors/ WolframDem onstrations Cura LulzBot: Quick Start Guide. (2017, November 22). I achieved my hypothesis by successfully learning about different forms of transformable/deployable structures Retrieved April 06, 2021, from https://www. lulzbo t.com/cura-lulzbot-edition-quick-start-guidethrough the demonstrated simulations, physically modeling my own Hoberman Sphere, & by 3D printing Delivering Differently: Emerging Technologies. Retrieved March16, 2021, from https://www.my own scissor hinges. Through my demonstrated newcivilengin simulations, I learned that by using a scissor hinge type, eer.com/archive/delivering-differently-emerging I can create numerous forms of transformable structures. technologies-18-01-2016/ This visualization gave me clarity to how a scissor hinge De Temmerman, N., Roovers, K., Mira, L. A.,Vergauwen, A., actually works & that using the least amount of sides/ bars, gives me a more lightweight & compressed Koumar, A., Brancart, S., Mollaert,M(2014). Lightweight Transformable Structures IV. doi:10.2495/mar140011 structure that will be easier to store & transport. Through my K’nex Hoberman Sphere, I gained knowledge in how scissor hinges can join together in order for Folding Gate Installation. (n.d.). Retrieved April 6, 2021, from https://www.acfoldinggates.com/maxguard them to expand & contract in 2D & 3D. I learned Hoberman Arch.(2020). Retrieved April 06, 2021, from that there are much more pieces involved in creating https://en.wikipedia.org/wiki/Hoberman_ Archa deployable structure than I thought. However, these pieces could be mass fabricated, for there are only Hoberman Arch. (n.d.). Retrieved March 10, 2021, from http a couple different type of parts needed. Lastly, through s://www.hoberman.com/portfolio/olympicarch/my 3D printing of scissor hinges,I learned how to bring the 3D model into Cura & how to control the actual 3D printer. In the end, I got a glimpse of how Kabai, S. (2007). “Extendable Frame” http://demonstrations. wolfram.com/Extendable Frame/ WolframDem- onstrations easy it would be to large-scale manufacture parts of deployable/transformable structures. I can design Kabai , S. ( 2008) “Extendable Tower” http://demonstrations. wolfram.com ExtendableTower/ Wolfram Demo-my own transformable/deployable structures in my nstrations future. Because I want to specialize in humanitarian architecture & social infrastructure, I could use my Kabai , S. (2020) .“Frame for a Deployable Shelter” http:// demonstrations.wolfram.com/FrameForAnew gained knowledge to create flexible, portable, DeployableShelter/ Wolfram Demonstrations & easy-to-erect structures that are sustainable, leaving no permanent damage to their sites. Some practical Merchan, C. (1987). Deployable Structures (ii-83, Rep). Cambridge: MIT.implementations of what I could design from my new knowledge could be Covid-19 vaccination hubs, social Mira, L. A. (2014). Parametric Structural Assessment of Deployable Scissor Systems: Optimizing the distancing igloos, shelters in natural disasters, refugee USC. Brussels: Uitgeverij University Press. rooming, etc. More temporary spaces are needed in our built environment because in times of crisis, these Mosely, J. (2017, October 22). K’nex Expanding Sphere. Retrieved March 10, 2021, from https://www. structures can quickly serve an essential purpose. I feel instructables.com/Knex-Expanding-Sphere/ more prepared going into the architecture field because I learned the importance of testing simulations under Pamperin, N. (n.d.). Bronze Age Folding Chair Found in N. Germany & Now in Helms Museum different conditions, making physical models, learning [Photograph]. new AEC computer programs, & the characteristics Archäologisches, Helm’s Museum, Hamburg. of flexibility, adaptability, reuse, & transformability in a 78 sustainable context.
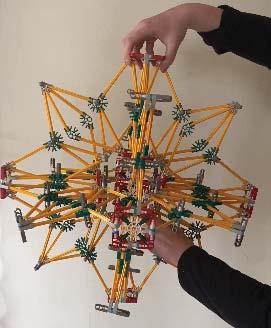

SHUAILANG YAN (JACKY)
1998
JUNIOR
ARCHITECTURE MAJOR
ABOUT ME
JACKY YAN
ARCHITECTURE IS ABOUT TRYING YO MAKE THE
WORLD A LITTLE BIT MORE LIKE OUR DREAM
BACKGROUND
After I started learning architecture, I came into contact with a lot of new things, started to touch some computer modeling software AutoCAD, Sketchup, and also learned that Photoshop, InDesign, Illustrator is not only used to make posters, but also to modify and type our drawings. What makes me feel most incredible is parametric modeling. By learning and consulting, we know that many things in life are inseparable from numbers, like big data, finance, design, and many of the most basic things in software are numbers. Digital has influenced the development and future of cities, like digital cities, digital modeling. Parametric modeling is one of the representatives of digital modeling, parametric modeling is free modeling through numbers, formulas, and software. Why free modeling is because you can build whatever arc you want, whatever shape you want. Model production in a purely digital space is simply a transformation of ideas for designers, allowing designers to greatly enhance their designs, diverge their thinking, and create different buildings. Rhino is the most representative software because it is a parametric modeling software that was molded earlier and contains very functional software Grasshopper. In the process of learning this software, I found that the biggest difficulty is that it has too many functions, there are many small functions in each big function, you need to spend a lot of time to practice in order to better master this software. But I really enjoy the process since Rhino is more like a game software than a model software, it lets you think of design as an interest, love a favorite thing to do, you don’t think it’s boring, because you can find more inspiration here.