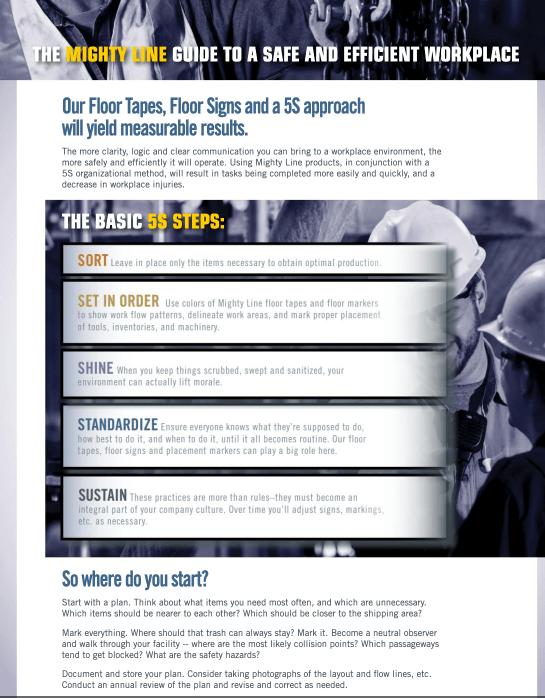
2 minute read
EXPLORING THE 5S SYSTEM AND ITS COMPONENTS
The 5S system is a cornerstone of workplace organization, particularly in industrial and warehouse settings. It consists of five key phases: Sort, Set in Order, Shine, Standardize, and Sustain. Each phase plays a pivotal role in minimizing clutter, reducing waste, and increasing operational efficiency.
SORT (SEIRI)
The first step, Sort, involves distinguishing necessary items from unnecessary ones and removing the latter. This process is facilitated by using red tag floor signs and tape to mark areas for disposing of unused items, ensuring a clutter-free workspace that enhances focus and safety.
SET IN ORDER (SEITON)
Once sorting is complete, the Set in Order phase organizes the remaining items. This stage utilizes tools like warehouse signs, LED sign projectors, stop signs, and floor and aisle markers to ensure everything has a designated place. This organization aids in reducing time spent searching for tools or equipment and enhances workflow efficiency.
SHINE (SEISO)
The Shine phase involves cleaning and inspecting the work area and equipment, which not only maintains the quality and functionality of the workspace but also prevents the buildup of dirt and debris that could cause errors or accidents.
STANDARDIZE (SEIKETSU)
In the Standardize phase, the best practices identified in the earlier stages are documented and implemented consistently across the organization. This includes the strategic use of custom signage and heavy-duty tape to resist traffic and prevent wear and tear in high-traffic areas, ensuring that the standardization is both effective and durable.
SUSTAIN (SHITSUKE)
The final phase, Sustain, focuses on maintaining and reviewing the standards set in the previous phases. It involves routine checks and continuous employee engagement to practice the established procedures, ensuring long-term adherence and continuous improvement.
Through these phases, Mighty Line floor tape and signs play an essential role in effectively implementing the 5S methodology, enhancing the visual management of spaces, and supporting the principles of Kaizen by reducing the eight wastes. This systematic approach not only improves operational efficiency but also fosters a safer, more organized, and productive work environment.
The Role Of Floor Marking In Supporting Kaizen And 5s Practices
Floor marking plays an integral role in enhancing the efficiency and safety of workplaces implementing Kaizen and 5S methodologies. Utilizing products like Mighty Line floor tape and signs, organizations can significantly streamline their operational processes and reduce the eight wastes identified in Lean manufacturing. These wastes include defects, overproduction, waiting, non-utilized talent, transportation, inventory, motion, and extra-processing. By strategically placing floor markings, companies can create a visual layout that directs behavior, optimizes workflow, and maintains safety standards.
Key Benefits Of Floor Marking
1. Visual Communication and Safety: Floor markings serve as critical visual cues that guide the behavior of employees and visitors, ensuring everyone understands the workflow and safety protocols. For instance, different colors and symbols can indicate specific actions, warn against hazards, or highlight emergency exits and first aid stations. This clarity is crucial in preventing accidents and ensuring a smooth operational flow.
2. Efficiency and Waste Reduction: Properly implemented floor markings can significantly enhance operational efficiency by clearly defining work areas, storage locations, and pathways. This organization helps in reducing motion waste and waiting times, as employees spend less time searching for tools or materials. Moreover, by delineating specific areas for certain activities, floor markings can help prevent overproduction and excess inventory, directly contributing to waste reduction.
3. Regulatory Compliance and Continuous Improvement: Floor markings also help organizations comply with safety regulations and standards, such as those set by OSHA. They are part of an ongoing improvement process, as they can be easily updated and reconfigured to adapt to new workflows or layouts, supporting the dynamic nature of continuous improvement practices in Kaizen.
Through these strategies, floor markings not only support the foundational goals of Kaizen and 5S by enhancing organization and safety but also play a pivotal role in sustaining long-term operational efficiency and compliance. By integrating these visual tools, businesses can foster an environment where continuous improvement and waste reduction are naturally embedded in the workplace culture.