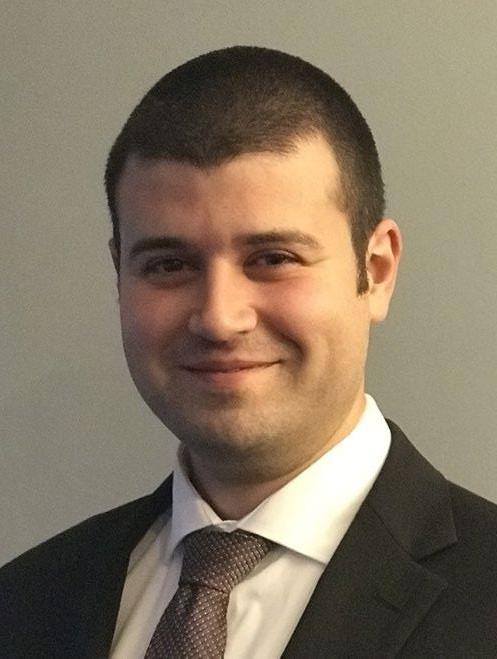
2 minute read
How did you get into your existing role?
Equipment Manager Tips - Anthony Lewis
Winter provides the opportunity to thoroughly inspect equipment, replace wear items, and provide a finished product that will run all season with very minimal issues. Parts lists are generated during October and early November, but it is common to find a deeper issue during service.
Advertisement
There is a sequence for when equipment is brought in for service that follows our monthly budget starting in October with the end goal date of March 1st. The Mid-Atlantic weather is unpredictable, and I’d rather know our fleet is ready to go.
A good example is spotting dust accumulation inside a rear wheel driven by a planetary gear system. This was an indicator that the seal was failing, which is a result of worn bearings. We were able to rebuild the case before it failed during the season and a rebuild kit versus a complete case is roughly a fifth the price. The winter period allows us ample time to be thorough - so take advantage of it.
Typically, our assistant, Walter, and I will brainstorm a sustainable approach for maintenance checks. Any new method will be explained to our management team so we can all monitor the change, and determine if it solved the issue. Our 9009A height adjusters had a habit of coming loose during the season. I no longer wanted to make inspecting the levers part of my morning routine. We decided to secure the levers with aviation wire because they will be unable to disengage themselves and the OEM design is still intact.
Depending how often we need to use trimmers, chainsaws, and backpack blowers - we will either drain the tanks, treat with Stihl Motomix or assign a scaled amount of equipment to be used and cycled through for winter refurbishment.
Reorganizing the equipment storage area to streamline morning mower setup along with indoor and outdoor lighting improvements. Assigning staff to pressure wash and wax equipment when time is available is also a big help. I believe this increases pride in the appearance of the equipment fleet and can be a team building experience.
Similar to my last position, my preference is to create Excel documents for each type of equipment. This way the typical filters and wear items are already on the sheet for next year, then additional parts for special projects on that type of equipment can be easily added. It is so much easier to pull in five consecutive fairway mowers, knowing everything you need is already on the shelf barring an unforeseen issue that is found during teardown.
Superintendents and assistant managers can assist in communicating daily and weekly plans for the golf course. Equipment Managers tend to focus on the winter maintenance. We could be spending the entire day blindly working on a sprayer, and not have the knowledge a PTO powered blower needs to be set up for the next day. These small instances creep up from time to time.
Anthony Lewis
Chevy Chase Club alewis@chevychaseclub.org