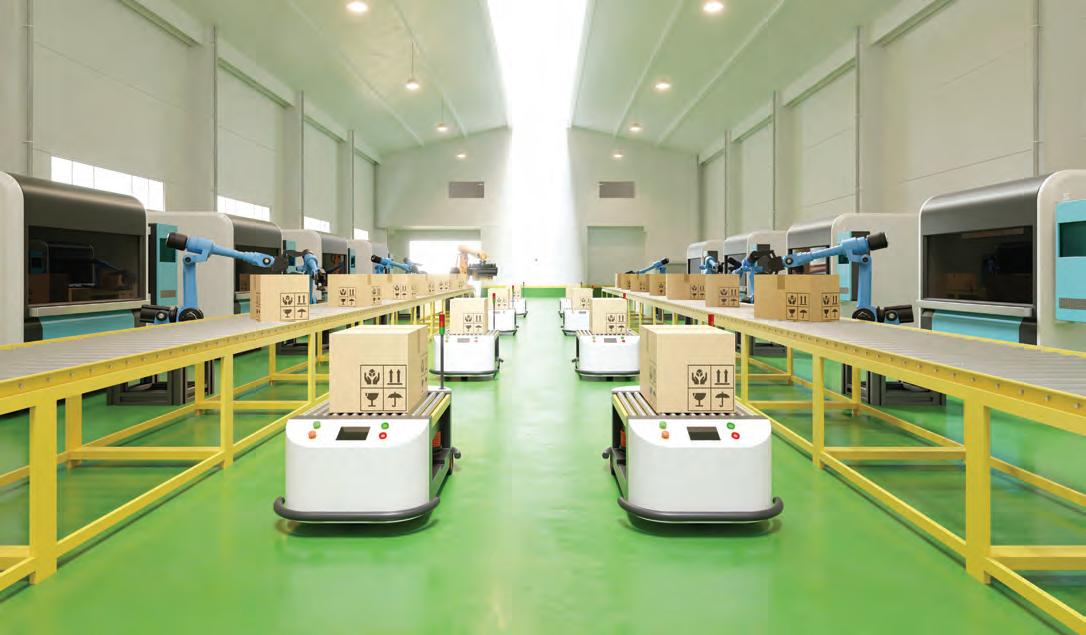
5 minute read
MOVE OVER: AMRs COMING TO A FACTORY NEAR YOU
MOVE OVER
AMRs coming to a factory near you
Advertisement
Every few minutes, an autonomous mobile robot (AMR) removes a full cart of partially finished goods and replaces it with an empty cart.
This, of course, is without the need for humans.
Nowadays, Michigan companies are saving time and money by investing in automation to streamline certain processes inside factories. It can be as simple as picking up trash in a plant or as complex as a pharmaceutical company moving product between its plasticinjection molding machines and assembly line.
According to Dennis LeMaire, a sales engineer for Zeeland-based Industrial Control, all industries — from retail to healthcare — are analyzing processes to gain efficiencies, avoid production bottlenecks, and stay competitive. By purchasing robots, companies can free up human workers for other tasks and eliminate project downtime.
“Where I see automated guided vehicles (AGVs) and AMRs really coming into play are companies continuing to refine their processes,” LeMaire said. “It just makes sense to pull that labor out and have a consistent way of being able to deliver products from point A to B.”
Unlike AGVs which navigate with magnetics strips embedded in the floor, AMRs are guided via stored floor maps and are directed from a Fleet Server or the company’s ERP system, whic communicates to the robots using a wireless network. Lidar, ultrasonic sensors, and 3-D cameras allow the robots to adapt to changing environments and production requirements, all with modifications to their software.
“So if you’ve got a robot that needs charging, or if there’s downtime, you can program in opportunity charging,” said LeMaire, noting AMRs are a form of automated guided vehicles. “The goal is to be able to have enough robots and capacity to move the product where you need to, including built-in charging time, so that you’re actually never down at the factory.”
LeMaire said an AMR can cost as much as a hi-lo, but “you also get additional savings from the labor needed to operate that equipment.”
“A lot of companies deal with moving parts — from the raw goods stage to finished goods — which may be just a few boxes of product leaving,” he said. “Electrical components, metal machine parts, household goods, and consumer goods are all great opportunities to be able to move with AGVs.”
Those opportunities are why AMR demand continues to rise, LeMaire said. According to a market intel report, the segment is expected to reach $22.15 billion by 2030, up from $1.61 billion in 2021.
“When companies adopt their first robot, a lot of times they go from one (or) two to five to 10 robots,” LeMaire said. “That number rises exponentially because they’re able to see what that benefit is on their floor.”
Ben Greve, senior sales engineer for Industrial Control, said there’s a ubiquitous need for this technology.
“Anybody who’s moving stuff is going to need this technology,” Greve said. “With the labor shortage, if (employers) can spend $40,000 to $60,000 on an AMR and repurpose one or two associates for higher-value tasks, that’s a no-brainer right now.”
A customer of Greve’s recently purchased 45 robots to address some of those concerns. This customer built up his or her
fleet of robots over the past three years.
“I have one customer that uses these for a ‘milk run,’ where they’re taking parts that are ready to be put into assemblies, and instead of a person pushing a cart around and unloading the parts, the AMR makes the run,” Greve said. “The person is freed up to do something else.”
Greve said customers also ask him if the robots can be used to pick up trash or scrap.
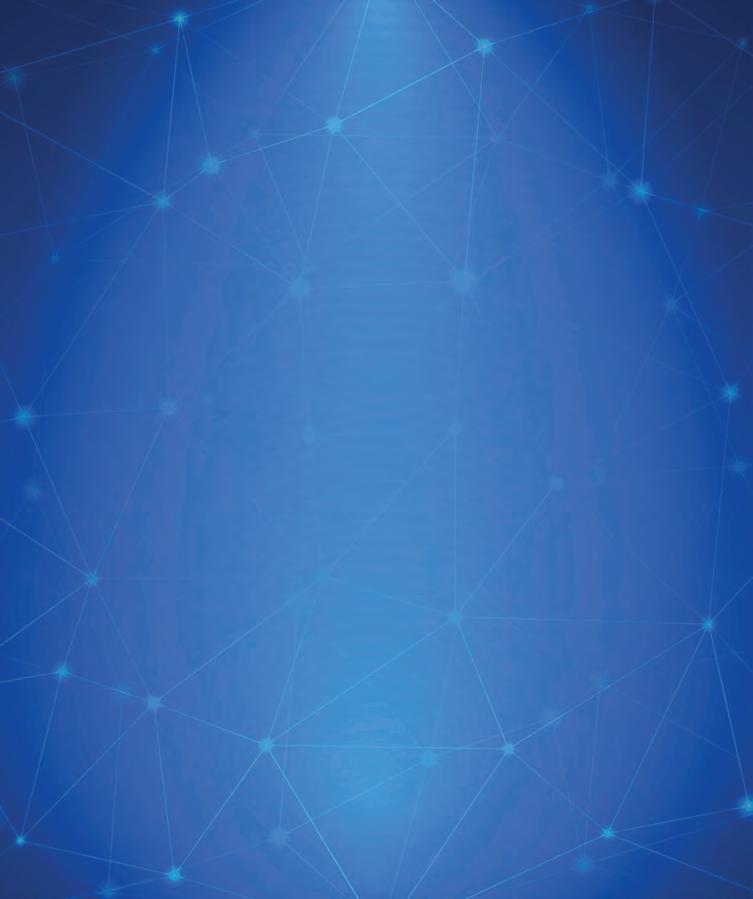
“It’s bringing materials to lines or taking materials from lines,” he said.
“That’s helped alleviate staffing shortages. Now you have a robot that’s doing the job of a person and frees them up to do something higher value add.”
“Where I see (automated guided vehicles) and AMRs really coming into play are companies continuing to refine their processes. It just makes sense to pull that labor out and have a consistent way of being able to deliver products from point A to B.” —Dennis LeMaire, sales engineer for Industrial Control
LABOR, LABOR, LABOR
AMRs can independently move around obstacles to fulfill tasks, ensuring material flow stays on schedule. LeMaire remembers a robot demo when roughly 30 people moved through halls, putting their feet in front of the robots to mess up their routes.
But “the robots had blinders on,” he said.
“This was an application where at any point, a portion of that labor force was bringing small orders from one end of the building to the other. The robots did it seamlessly.” It’s the new normal, say industry insiders, who note menial warehouse and inventory tasks can now be handled by the AMRs.
“As the environment changes where skids come into play, and the product is moved around, the robots will read off of those situations and revise its route so that it can optimize how it gets through the plan,” LeMaire said. “It has the ability to look out in front of itself … 50 feet. It can recalculate as things are coming toward it.”
Companies use this to their advantage by taking the human factor out of driving hi-los.
According to LeMaire, the traceability of where and how the product is moved is all tied to the management system, which can be accessed via a Wi-Fi connection.
“And this technology has all happened in the last four or five years,” LeMaire said. “I’m looking forward to seeing the advancements in this technology. Highbay storage is a situation that’s going to be out there in the market.”
While contemplating the future of warehouse technology, LeMaire sees AMR possibilities outside the four factory walls.
“I mean, can you really see someone driving around on a golf cart moving goods?” LeMaire asked. “Probably not.” n
Smart Maintenance
Increase reliability with OEE and predictive maintenance
Smart Service
Leverage secure remote access for troubleshooting
Smart Safety/ Compliance
Avoid risk with early awareness
Smart Information
Awareness of key performance indicators
Smart Sustainability
Save energy and reduce waste
Smart Operation
Increase production and ROI
TM
We know that qualified talent and a healthy talent pipeline are the keys to success.
Discover Manufacturing is a network of hundreds of manufacturers who are leveraging training dollars, connecting to youth, shaping curriculum, and growing awareness of the industry in West Michigan.
Sign up for our newsletter to stay up to date on Going PRO Talent Fund announcements, apprenticeship programs, student initiatives, professional development opportunities and more!
discover-manufacturing.com
Wire EDM Cutting 6 Axis Fast Hole EDM EDM Die Sinker Water Jet Cutting Laser Cutting CNC Machining & Milling Carbon Cutting Cryogenic Tempering CMM Vision Measurement System
EXPERIENCE AND KNOWLEDGE
Serving the Die, Mold, Gauge and Stamping Industries.
3180 Three Mile Rd. NW • Walker, MI 49534 | Phone: 616.453.4360 • Fax: 616.453.2549 • Email: data@pwedm.com