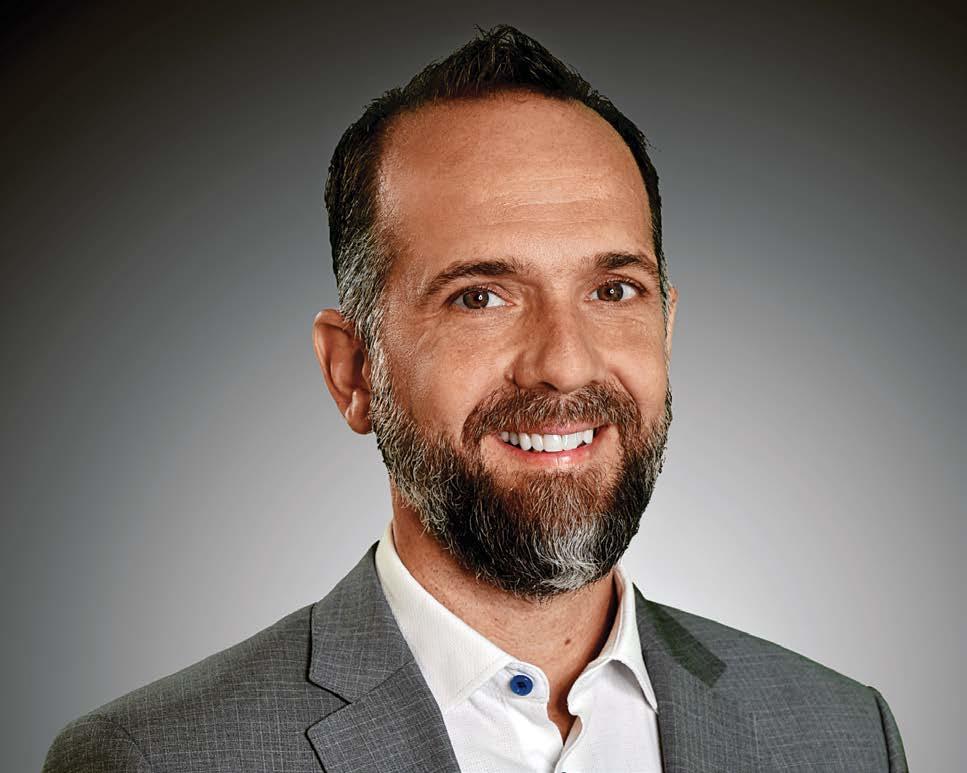
8 minute read
The End of the Jumbo Jet Era
In January 2023, Boeing delivered the last Boeing 747, marking the end of the jumbo jet era that revolutionized air travel five decades ago. Changing market dynamics, the COVID-19 pandemic and advances in aviation technology increasingly have rendered the jumbo jets less relevant, ultimately leading to their discontinuation.
The Boeing 747, affectionately known as the “Queen of the Skies,” first took flight in 1969. It was designed to meet the growing demand for air travel forecasted for the 1970s. With its distinctive hump and four engines, the 747 quickly became a symbol of luxury and prestige and was used by many airlines for long-haul routes. However, the rising cost of fuel and the advent of smaller, more fuel-efficient aircraft, such as the Boeing 777 and Airbus A350, have made the 747 less economically viable. The 747 was the first airplane known as a “jumbo jet” due to its wide-body design, as reported by MBN.
The 747 democratized global air travel in the 1970s, making it possible for the middle class to travel outside the EU or the US at an affordable price. However, the jumbo jet fell behind twin-engine passenger jets, which are today’s standard. While the retirement of these iconic aircraft marks the end of an era, it also reflects the changing nature of the aviation industry. The rise of low-cost carriers and the increasing popularity of point-to-point routes have led airlines to increasingly favor smaller, more fuel-efficient aircraft that offer greater flexibility and lower operating costs. Furthermore, advances in technology, such as the development of more efficient engines and the use of composite materials, have made it possible for smaller aircraft to achieve similar levels of range and capacity as their larger counterparts.
Retiring the 747
Over the past five decades, the Boeing 747 was used by many top airlines worldwide, with Japan Airlines being its largest operator, using 108 aircraft. British Airways was the second-largest client with 94 aircraft and Lufthansa was the second-largest operator in the EU with 81. In Mexico, several Boeing 747s have operated throughout the years, mainly to Mexico City, Guadalajara and Cancun. The first carrier to operate a 747 in Mexico was KLM, followed by British Airways, Lufthansa, Pan Am, Iberia, Japan Airlines and Air France. The 747 was also flown to Mexico through freighters, such as Atlas, Cargolux and Cathay Pacific.
After the COVID-19 pandemic, only a few airlines continue to operate the Boeing 747, including Air China, Korean Air and Lufthansa. The last 747 produced in history was delivered to Atlas Air on Jan. 31, 2023, as reported by MBN.
While the Boeing 747 and Airbus A380 will likely continue to fly for several years, they are past their prime and production has come to an end. As the aviation industry continues to innovate and evolve, planemakers and airlines are turning to newer, more efficient aircraft, such as the Boeing 777X and the Airbus A350. With the end of the jumbo jet era, the industry will be led by those players capable of using sustainable aviation fuels (SAF), hybrid or electric aircraft, which can significantly reduce emissions and operating costs. The end of this era represents a significant moment for commercial aviation, as it continues shifting toward new directions.
Turning Mexico Into One of Bombardier’s
Three Main Pillars
Q: What are Bombardier’s environmental, social, and governance (ESG) plans to adapt to current disruptions in the aerospace and aviation sectors?
AP: ESG plans are essential to us; we published our plan a few years ago and we update it every year. The current plan addresses 11 key areas and includes well-defined strategies, so everyone in Bombardier can follow every part of our services or processes. With ESG, we measure our success through results. For example, we are focusing on our environmental footprint, diversity and inclusion, compliance and customer satisfaction.
MD: Not only is sustainability important for Bombardier but it has become critical to the community surrounding the company. In Mexico, we see a great deal of participation from all employees, who appreciate that this is a priority for the corporation. In Mexico, prioritizing ESGs is part of the community’s values, which greatly helps advance these goals at a corporate level.
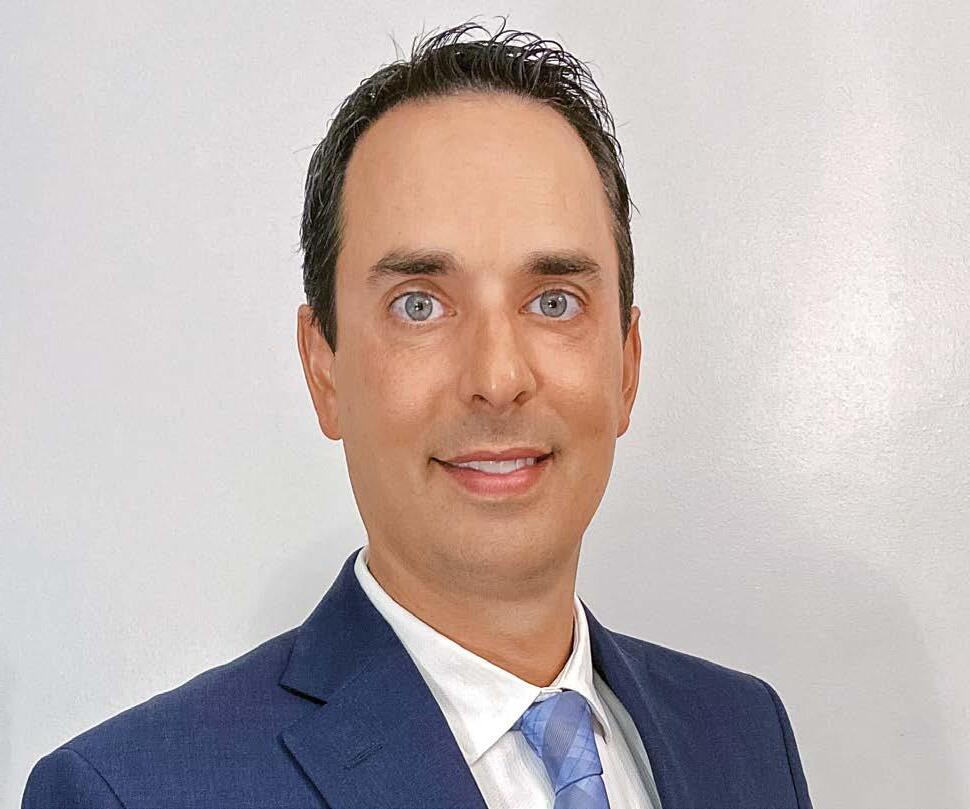
Q: How are projects like the company’s EcoJet research helping test the next generation of business aircraft?
AP: The EcoJet is a fantastic project and a platform for research. We are using it to focus on designing a new aircraft shape that will help us reduce aerodynamic drag. It has also been helpful in our research on Sustainable Aviation Fuels (SAF) and hybrid propulsion. We are increasingly seeking to use electrical systems on aircraft, including electrical propulsion. The existing technology capacity does not allow us to go fully electric yet, so we are working with our partners and testing the technology on the EcoJet to prepare the technology we want to use in our next aircraft programs.
MD: The advances are real. The aerospace sector, by nature, is very conservative, especially when it comes to metallic parts. However, we are seeing the evolution of Bombardier by introducing new technology and exploring new ways to do things.
Q: What has been the focus of Bombardier’s innovation efforts in recent years and how is this helping companies to reduce costs in a strained economic environment?
AP: For the past five years, most of our innovation has gone into improving passenger experience. The Global 7500 is a leader in the industry that includes seats, which revolutionized the seat market. For almost 50 years, the seats on the plane had remained the same and we developed a new mechanism that brings comfort to the passenger. A Global aircraft can travel for 10, 12 or 14 hours of flight, so when someone is traveling across the globe, they should be able to rest and arrive well-rested to their destination. Our competitor copied our aircraft lighting system, so we consider ourselves leaders in this as well.
We have also redesigned the cabin on the Global 7500, which will be called the Global 8000 and will be the longest business aircraft available, with three dedicated workspaces for corporate customers. We want to get our customers’ feedback and improve it. All of our innovation comes from listening to our customers and the constant need to innovate.
Aerospace original equipment manufacturers (OEMs) must strive to manufacture aircraft that can travel sustainably for longer distances and support net-zero goals. They must produce quality components with tight tolerances from difficult-to-machine materials like heat-resistant super alloys (HRSAs), while also keeping production cost-effective and errorfree — but how?
This is where digitalization and big data come into play. Combined digital and tooling solutions will be essential for errorfree production in tomorrow’s aircraft manufacturing industry. That includes Sandvik Coromant’s own CoroPlus Machining Insights, CoroPlus Tool Library and Silent Tools Plus process control solutions, which enable users to monitor their machining process and secure a successful output.
The aerospace industry faces unique manufacturing challenges. The complexity of the component shapes and structures, combined with the varying tolerances required for different components can make the production process demanding and costly. The nature of aerospace — and its strict quality assurance rules — also means that component production must be error-free. To optimize manufacturing, proper planning and preparation informed by accurate and reliable data is absolutely essential. To support aerospace OEMs, Sandvik Coromant offers several solutions to improve machining processes and to ensure quality and reliability of components.
An increasing number of industries are incorporating digital technologies into their manufacturing operations. Digital tools and the data that they can generate on key parameters can give a level of intuition and insight that traditional machining lacks. This is particularly key in heavily regulated industries, such as aerospace where accuracy and efficiency are crucial at every stage.
The Sandvik Coromant CoroPlus Tool Library is a web-based software that allows users to build and manage their tool library and tool assemblies from standard data on over 900,000 items from several cutting tool manufacturers. The library is cloudbased, allowing easy sharing of data and import into CAM and simulation software. Production and machine engineers and CAM programmers can easily create tool assemblies adapted for specific machining tasks or receive specialized recommendations for each application. The tooling data is verified by each supplier and is compatible with system environments meeting ISO 13399, the international standard for cutting tool data representation and exchange.
Using the CoroPlus Tool Library can save aerospace component manufacturers valuable time by removing the need to manually find and input tool data and reduce the margin for error involved in sourcing data from different systems. The centralized platform contains all essential standard data and minimizes risk, allowing manufacturers to get it right from the start.
Aerospace manufacturers can also improve their operations by using CoroPlus Connected with Silent Tools Plus. CoroPlus Connected enables process automation driven by data to increase efficiency and optimize output quality. This solution is particularly effective in complex processes, such as production of jet engine components and landing gear, where visualization is difficult and operators may struggle to accurately see inside components due to their complicated structures or challenging materials.
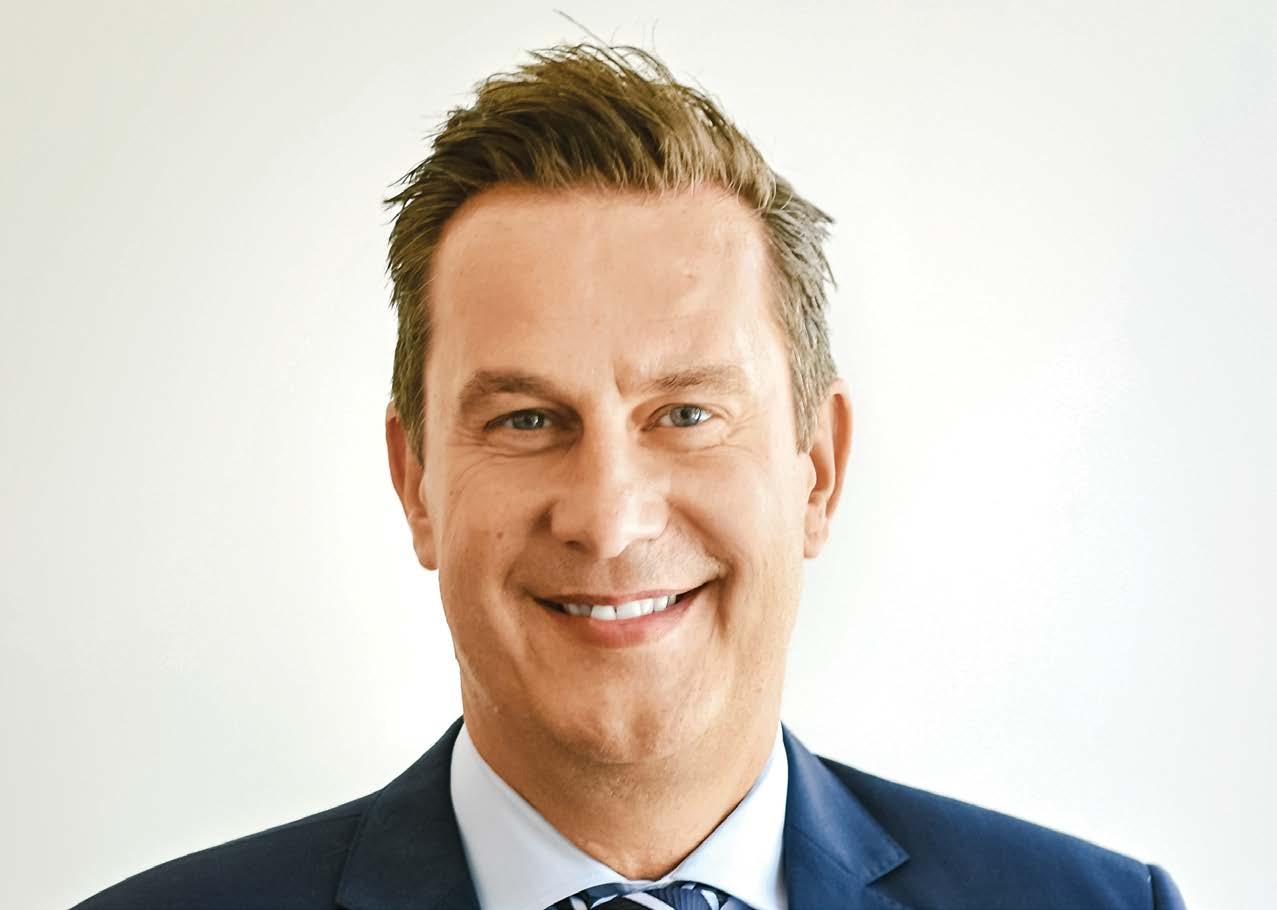
Silent Tools Plus adaptors are equipped with sensors that can measure important parameters, such as height, temperature and load, and transmit this data automatically to the machine, minimizing tooling set-up and improving operator control when the tool is in cut.
Ensuring that tools are correctly set up and working to appropriate loads and measurements can effectively minimize downtime and wastage of resources. This is particularly important in the aerospace industry, where accuracy is key in preventing the need to scrap partly machined components in exotic, costly materials. Silent Tools Plus also supports safety and component security and increased cycle times, leading to overall productivity gains and protection of assets and output.
To improve operational efficiency and overall equipment effectiveness in complex aerospace manufacturing processes, reliable collection and analysis of data is essential. CoroPlus Machining Insights offers engineers and operators a centralized oversight of machine data, allowing them to visualize the process from start to finish. While manual data collection is slow and prone to error that aerospace engineers must avoid, the cloud-based system collects and stores data from all machines and tools for total operational transparency. Real-time and historical reports let engineers see machine and tool use, errors and performance, giving insights into areas for improvement and process optimization. This can improve overall productivity and highlight risk areas in manufacturing.
CoroPlus Machining Insights is easy to integrate into a machine shop and can easily be scaled up and down as it is a softwarebased product. As well as giving the user a full view of the machine utilization and predictive maintenance needs, the user can also log in to visualize several locations off site. This gives engineers more control over production and can allow for predictive maintenance and straightforward diagnosis of issues that may negatively impact manufacturing.
Digitalization in the aerospace industry can certainly offer significant benefits in production quality, but sustainability is another important concern. Sandvik Coromant’s digital technologies can offer tool recommendations optimized for specific tasks which consume less power overall. Establishing connectivity between machines also contributes to an overall more efficient operation, with reduced machining times and faster cycles.
These digital solutions are just the beginning when it comes to combining automation with tooling for the aerospace industry. Artificial intelligence and machine learning are paving the way for new technologies to blend sophisticated software algorithms with decades of specialized machining knowledge. Sandvik Coromant’s technologies aim to drive automation and improve process productivity and sustainability. In processes that must be accurate, precise and error free, digitalization and data-driven decision-making can yield financial savings and productivity gains.