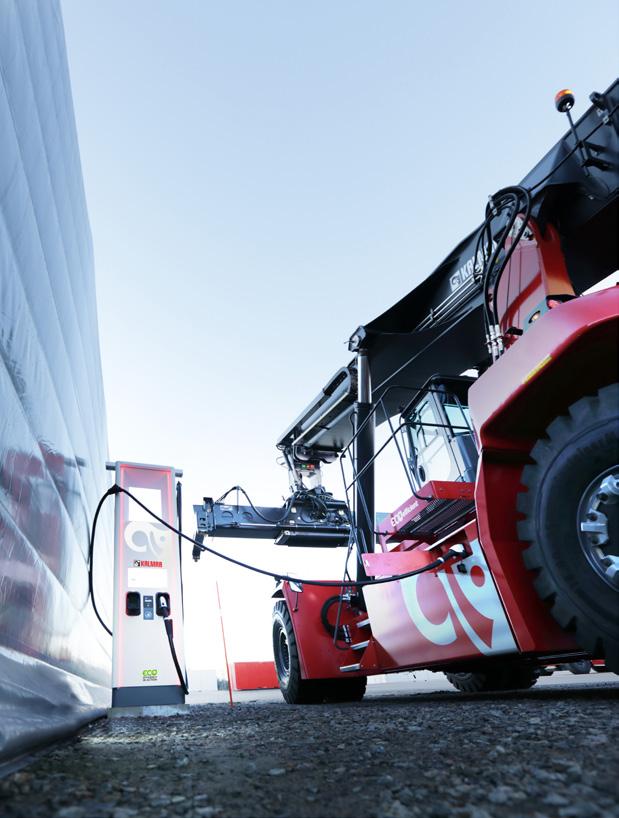
7 minute read
Electric Power Play
John Bensalhia tracks the advance of the electric reach stacker system including product R&D, trials, recharge issues and solutions, the order book and the cost equation
With terminal operators pursuing alternative energy and emission-free goals, electric and hybrid reachstackers are fast gaining in popularity with this position complemented by a broadening of the sources of supply.
One option in the latter respect is market newcomer and Sweden-based Camblift. Alongside other reachstacker models in its product range, the company reports it has introduced a completely electric machine employing a Li-ion battery for power. Precise specifications are not reported but Carl-Olof Eckerbom, CEO, Camblift says the design offers high performance in a sustainable way.
The product range incorporates reachstackers with a lift capacity of up to 46 tonnes and three different wheelbases. Annual output is forecast by Camblift to account for 40 to 50 machines.
Established manufacturers have also been busy evolving their clean energy reach stacker designs.
Jan Willem van den Brand, Director, Global Market Development, Hyster, explains that the first Hyster development project featured a 52-tonne capacity unit powered by a lithium-ion battery. However, he points out that lithium-ion batteries alone are not a suitable power source for every application. “This project has, therefore”, he elaborates, “been followed by developments utilising the power of hydrogen fuel cells. A Hyster hydrogen fuel cell powered laden container handler,” he points out, “is now in testing at Fenix Marine Services in the Port of Los Angeles. The truck is powered by two 45kw hydrogen fuel cells from Nuvera Fuel Cells. The hydrogen fuel cell works in tandem with an onboard lithium-ion battery to either power the equipment directly or charge the onboard battery.”
Hyster is also developing a zero-emission reachstacker featuring a hydrogen fuel cell for the Port of Valencia, as part of the European Horizon 2020 programme and H2Ports project. Additionally, Hyster recently announced a nonbinding Memorandum of Understanding to provide Hamburg terminal operator Hamburger Hafen und Logistik AG (HHLA) with two Hyster electric container handling vehicles, including the first-ever empty container handler powered by fuel cell technology in a real-world application.
Kalmar introduced its fully electric portfolio in December 2021. “We offer a choice of electrically powered reachstackers with a wide range of lifting applications, battery solutions and 42 to 45 tonne lifting capacities,” says Mette Kjems Baerentzen, Head of Sustainability, Kalmar. “We are not yet offering the empty container handling reachstackers (10-14 tonnes lift capacity) in an electric version but have an electric forklift for empty container handling offering a lift capacity of up to seven tons.”
Baerentzen says that Europe is the main growth market regarding zero emission reachstacker technology adoption with the Nordic countries taking the lead: similar to what can be seen with electric passenger vehicles. “Countries with “green” incentives and high fuel prices in combination with reasonable electricity costs are the front runners. However,” she says, “there are customers globally that have local incentives or requirements from the local municipalities that request the electric option.”
Kalmar’s order book includes the delivery of Sweden’s first electric reachstacker to the Port of Helsingborg. The port plans to build a new container terminal by 2028 (to cope with growing demand for container volumes and logistics services in Southern Sweden) and the facility will be developed with sustainability a key goal. This will include automation and electrification, with the 587kWh battery pack-powered reachstacker an important addition.
The current order book includes an electric reachstacker and combined charging system for Norwegian terminal operator, Westport. The unit is scheduled for delivery in the fourth quarter of 2022. Like Helsingborg, Westport’s new acquisition will help to achieve its target of zero emissions by 2030.
8 Under charge
a Kalmar electric reachstacker – average charging times are expected to come down as development proceeds
THE CHALLENGES
Baerentzen explains that although there is big interest in the electric reachstacker, as it requires on-site adaptation of the infrastructure, it entails what is effectively a new buying process for customers. It takes more time to prepare for the adoption of the system and especially in places with grid capacity challenges.
An allied challenge is managing peak power demand, as battery-powered electric vehicles rely on the electrical grid. Van den Brand explains that the same grid brings electricity to homes and businesses daily, with the average household using 28.9 kWh and the average business using 70 kWh per day. “Charging a single container handler,” he says “with, for instance, a 260-kWh battery pack, uses significantly more. If a fleet has 100 vehicles and they each get charged once a day, that’s over 20,000 kWh: enough demand that could overload grid capacity.”
Against this scenario, Van den Brand, further notes that hydrogen fuel cell filling station usage can be easily planned. “For large equipment with big hydrogen tanks, it is expected to take up to 15 minutes to fill an empty tank which may be enough for eight to 10 hours of continuous run time. This means that hydrogen-powered units do not need to refuel as frequently as their battery electric counterparts need to recharge, nor do they spend nearly as much time parked at refuelling stations.”
With respect to the cost difference between electric and conventional diesel models, Baerentzen says that the answer is higher CAPEX, but lower OPEX. “Depending on the cost difference between diesel and electricity, most total cost of ownership calculations show that the electric reachstacker is the best alternative after four to five years.”
However, the best choice of power option completely depends on the specific application. “A “battery-only” approach will suit applications with a low to medium-duty cycle where there is suitable energy infrastructure and a strict charge management regime for opportunity charging. Whereas an alternative such as a hydrogen fuel cell powered machine may better suit larger fleets, due to the high demand on the electricity grid, or where multiple trucks would need to be charged at the same time,” says van den Brand.
THE RECHARGE EQUATION
In terms of a typical operational period for electric models before recharging is required, van den Brand says that the run time always depends on the specific truck and application. But he notes that: “If the right equipment is selected, it should deliver across shift.” And interestingly, he further states that, “Testing has shown that the electric and hybrid machines in development offer comparable, or potentially even better, performance to the equivalent IC models and provide excellent energy efficiency.”
If suitable charging power is available, Hyster expects that it may be possible to implement technology to charge container handler batteries of a certain size in as little as one hour. “This will be particularly important for efficiency, as battery capacity will not be sufficient for one day of operation so charging must be planned during the container handler’s normal daily operation. However, with the level of charging power more typically available, charging could take up to five hours, and deliver usage of four to eight hours.”
Sany’s electric reachstacker is capable of working continuously for five hours after one fully charged session. In
Jan Willem van den Brand, Director, Global Market Development, Hyster cases when the reachstacker cannot be charged, an alternative is the range extender. For example, in challenging working conditions (poor weather), the range extender can allow the reachstacker 20 hours of operation.
The Sany electric reachstacker includes a dual gun charging port that can realise high-power fast charging. It also meets the national standard GBT 20234.1-2015 electric vehicle conductive charging connection device requirements.
The typical operational period for electric models before recharging is required depends on both the battery size and the duty, as high productivity requires more energy. “An average example would be an operational cycle of 250 metres/move, 15 tons/move and a productivity of 16 moves/ hour,” outlines Baerentzen. “For this, the driving time before requiring charging would be from 3,5 to 8 hours, depending on the battery size.”
Alternative power for reachstackers is a relatively new market segment and many manufacturers are still in the research, development and testing phase. Van den Brand says that some parties are keen to explore electrification, whereas others are interested in hybrid solutions, and those featuring hydrogen fuel cells. “Regardless though, “he underlines, “of how the machine is powered, there are some enduring trends affecting the design of container handlers - for example, operator ergonomics, visibility, and productivity are as important as they are when selecting an ICE truck.”
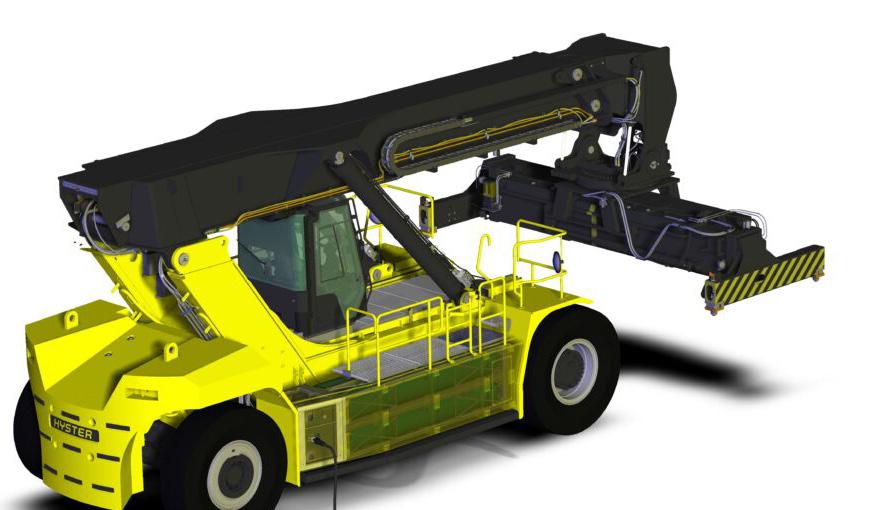
8 Hyster is
developing a zero-emission reachstacker featuring a hydrogen fuel cell for use in the Port of Valencia, as part of the European Horizon 2020 programme and H2Ports project
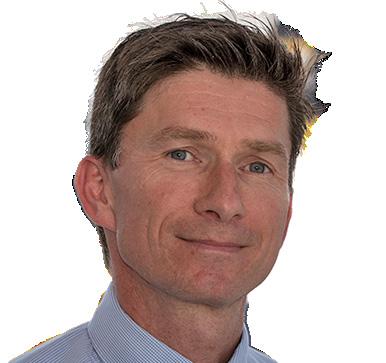