
8 minute read
Engineering skills
MARINE CIVILS AT THEIR MOST IMPRESSIVE
A coastal protection masterpiece in marine civil engineering has been completed by Jan de Nul.
The 4,500 tonne concrete threshold of a storm surge barrier has been installed on the seabed of an access channel at the Belgian port of Nieuwpoort after being built 105 kilometres away then transported on a barge.
It took 12 hours and two tugboats to bring the threshold on the barge from Kallo, where it was built to avoid too much disruption at Nieuwpoort, to Ostend, where the water is deep enough to submerge it.
The immersion operation took 20 hours, which reduced the weight of the threshold to 1,200 tonnes and allowed water tightness to be tested.
From there, a heavy lift crane vessel transported the threshold under water to its final destination at Nieuwpoort.
“Each tidal cycle, we only had a limited time frame to reach our final location,” says Jan de Nul. ”From three hours before high tide until three hours after, the channel was deep enough for the threshold to enter the access channel.
“On top of that, we had to adhere to strict weather limitations, both on wind strength and wave height. A detailed tidal plan guaranteed the safety, efficiency and success of the operation.”
The final task was to actually install the threshold between two abutments to within a centimetre of accuracy.
As well as the crane vessel, a pair of cranes operated from the shore, with divers on standby.
“An important role was set out for the survey team, which guided us to the exact location, with the help of a set of horizontal and vertical beams,” says the firm. “After some finetuning with a set of hydraulic jacks, the water pressure pushed the threshold to shore, creating a firm connection between both abutments.”
Jan de Nul says the threshold has been designed to last for at least a century and the entire storm surge barrier will be ready
8 Jan de Nul’s storm barrier
threshold
from 2025, after a 1,300-tonne steel barrier is installed.
Fibre optic technology firm Com&Sens has been contracted by Jan de Nul to embed an FBG fiber optic sensor network in the threshold to enable long-term deformation monitoring.
The port suffers from heavy storms about once a decade, and this barrier will protect it from waves as high as eight metres, Jan de Nul says.
“In Flanders, the government works with private partners to protect the 67km long coastline and the hinterland,” says Jan de Nul. “This storm surge barrier in Nieuwpoort is one of the masterpieces.”
A Victorian copper bell has been unearthed during work to connect utilities in Portsmouth, UK.
The bell, unearthed by the Southsea Coastal Scheme, was found while digging a trench to connect electricity on Castle Field.
“We are committed to working closely with on-site archaeologists to ensure that any historic remains are identified and recorded appropriately, as well as allowing our construction programme to continue without significant delays,” said Guy Mason, project director, Southsea Coastal Scheme.
The bell was found at a depth of 600mm, just five metres away from a Victorian cobbled road
COASTAL CIVILS PROJECT REVEALS HIDDEN TREASURE

8 The bell was unearthed by the
Southsea Coastal Scheme during civils works
that was also discovered at the same depth during the works.
Archaeologists examining the finds believe that the road had a military purpose, leading to the possibility that the bell was attached to a wall on a military site.
Given that a military parade ground once existed on Castle Field, the bell could have been part of that development. An iron element to the bell appears to have been added to attach it to a wall.
Following gentle cleaning to remove corrosion from the bell’s fragile copper elements, archaeologists conducted x-rays to see if any identifying marks could be seen to pinpoint its exact date and purpose. No marks were discovered so, for now, the bell’s origins remain speculative.
SURF intallation delivered in partnership
A SURF installation has been completed off Angola thanks to a partnership between two marine engineering firms.
UK-based marine engineering firm Maritime Developments Ltd (MDL) and DOF Subsea completed the SURF work package off the coast of Angola, MDL reported on July 12.
MDL’s spread consisted of a Generation 2 Reel Drive System, 4-track 85Te pipelay tensioner and an overboarding chute, mobilised onboard the offshore construction vessel Skandi Seven.
“We are happy with the efficient execution for this lay campaign, which completed on time with no incidents or accidents,” said DOF Project Portfolio Manager Thomas Hamre.
“Our end client congratulated the entire crew for the good synergies and problemsolving mindset created onboard the vessel.”
This project comes after several SURF installation campaigns over the last 18 months, in which the same vessel and spread combination were used. ”These campaigns have been optimised through the deployment of familiar assets, where project engineering could tap into existing deck plans, sea-fastening designs and installation methodology, and where field service teams were well experienced with working with one another,” MDL’s VP Sales Michael BleaseShepley said. ”A partnership-like approach allows us to have open and honest conversations with our clients to identify how further we can optimise operations and maximise returns for their businesses as a result.”
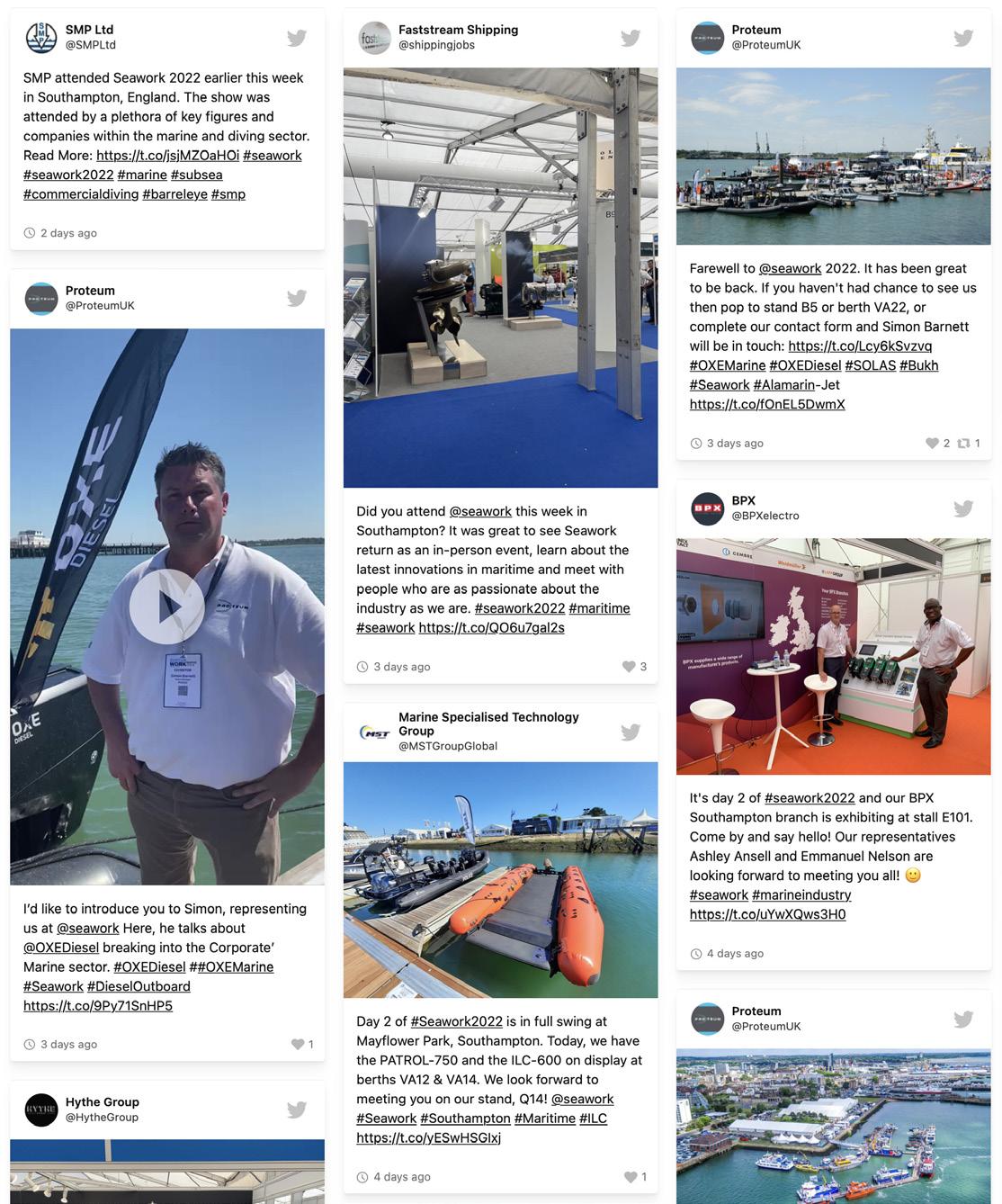
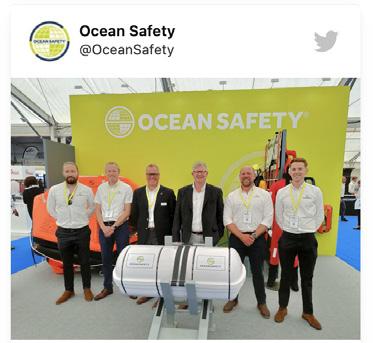
#seawork2022 ‘‘
It was great to see Seawork return as an in-person event, learn It was great to see Seawork return as an in-person event, learn about the latest innovations in maritime” about the latest innovations in maritime”
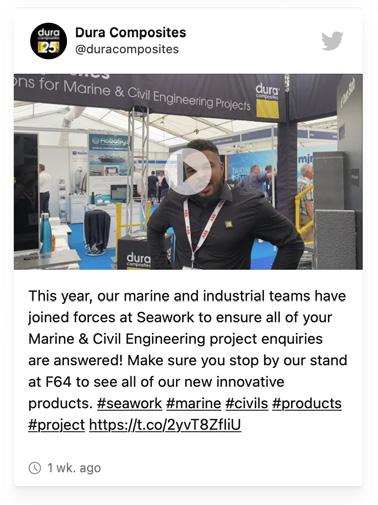
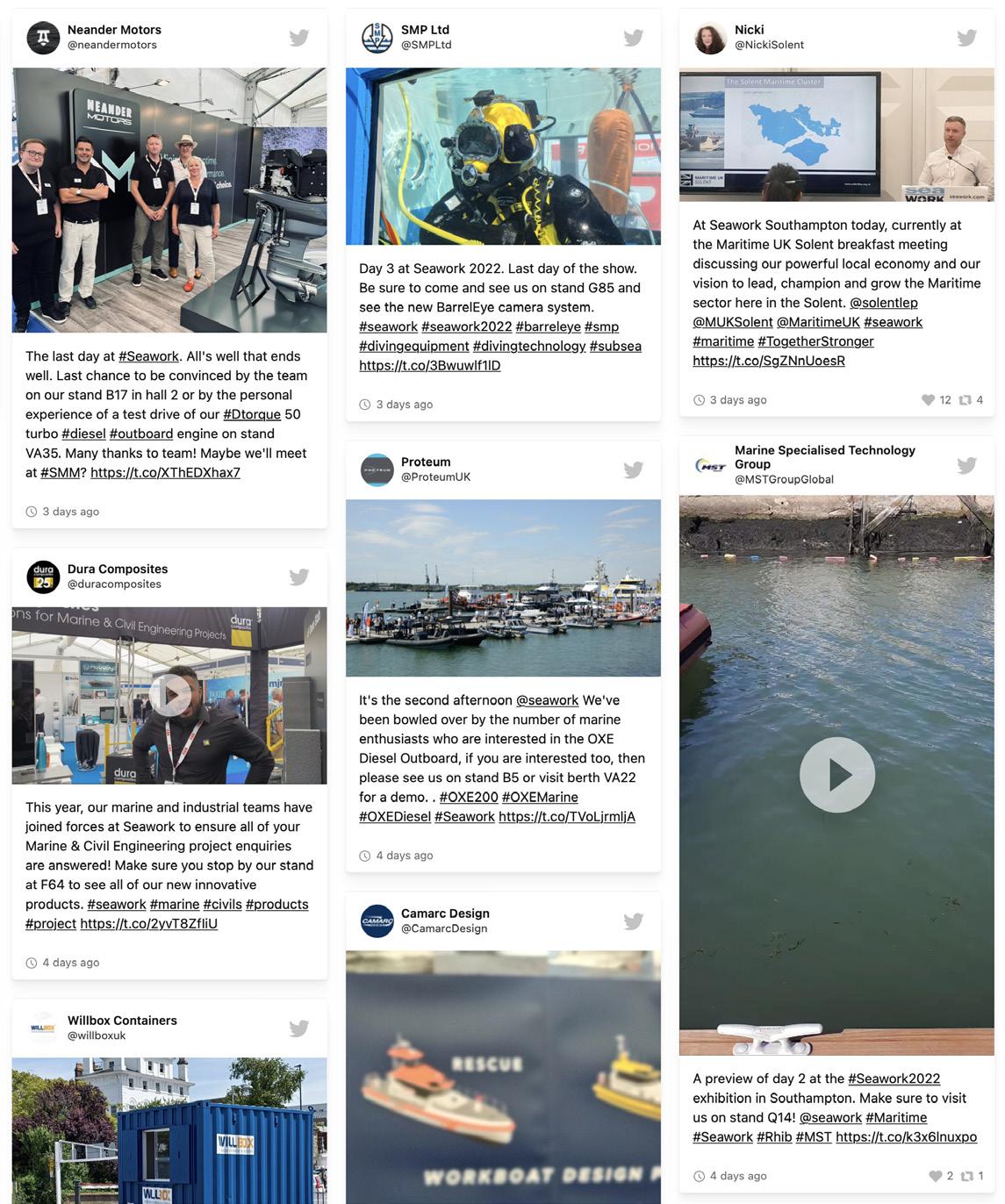
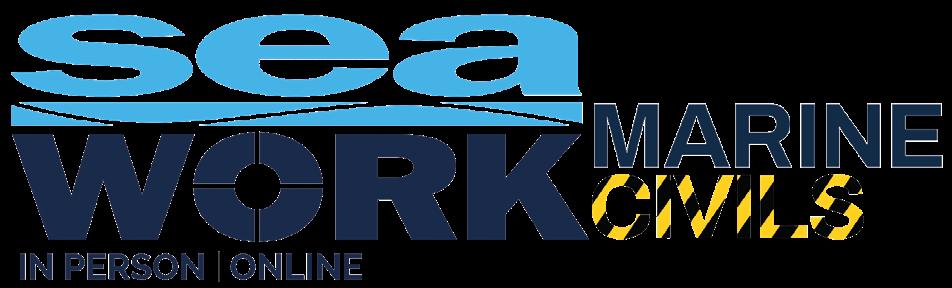

CONTROL UPGRADE FOR FLOATING DREDGE INSTALLATION
Alewijnse has successfully upgraded the control system of a unique floating sand processing installation
The upgrade of the complete control system on board the unique floating sand processing installation Kaliwaal 41 was part of a complete overhaul ordered by owner Van Nieuwpoort Groep.
“The installation dredges sand and gravel, which are separated at the beginning of the process. The next step is the transfer of the gravel to a vessel alongside,” said Richard Pols, commissioning engineer at Alewijnse. ”With the installation of two new conveyor belts, the gravel can be loaded to an additional vessel on the other side of the pontoon as soon as the hold of the first vessel is filled. ”The system [we installed] automatically switches between the conveyors without stopping the process.”
Project scope
Alewijnse was contracted for the upgrades to the automation applications and electrical installations at the same time as new conveyor belts, electric motors and a submersible dredge pump were being installed in order to increase the efficiency of sand production.
The systems integrator installed new hardware, adapted the wiring and updated the PLC program and SCADA to match the requirements of the new equipment.
Additional works included the expansion of the main switch board with an 800A power supply and the installation of a power cable for the new sand pump on the rear side of the production pontoon. The new pump dredges the finer sand fractions that are surplus to requirements and discharged through a conduit aft of the pontoon.
Kaliwaal 41 is a unique floating pontoon equipped with an industrial installation that is fed with material extracted from the riverbed, separates the sand from the gravel, and then uses vertical flow separation tanks to deliver up to 150 different grades of sand for use in concrete applications.
It is one of just a few floating separation installations in the Netherlands and is currently playing an important role in the Dutch Maaspark Well River widening project, which aims to create a safer living environment in the Maas valley between Well and Aijen.
Alewijnse and Van Nieuwpoort Group have been working together successfully for many years, ever since the original construction of the installation in 1998.
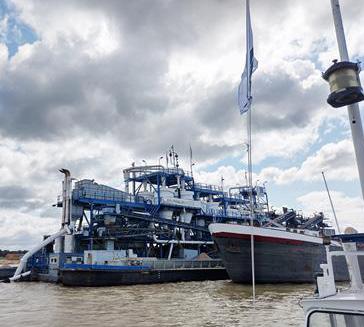
8 Alewijnse has
upgraded the complete control system on board the floating sand processing installation Kaliwaal 41
Islands to get submarine cable connection
90km of cable at depths of up to 1150m will be laid between Spanish islands and the north coast of Africa.
Cable systems supplier Prysmian Group will lay subsea cables between two Canary islands and another island and a coastal city in North Africa.
It will also lay about 11km of land cable.
The two contracts are worth approximately €250 million and have been awarded by Red Eléctrica de España, the Spanish power grid transmission system operator.
One cable will connect power between the islands of Tenerife and La Gomera and the second will connect the Spanish

Courtesy Prysmian Group
8 Giulio Verne at Napoli
mainland to Ceuta, a Spanish city on the north coast of Africa.
Prysmian’s cable-laying vessel Guilio Verne will be deployed to lay the cables in 2025.
The first is a 66kV HVAC (high voltage alternating current) double circuit, three-core submarine power cable with EPR insulation and synthetic wire armouring, which Prysmian says will be laid at a world record depth (1150m) for this kind of cable.
The second cable is a 132kV HVAC double circuit, three-core submarine power cable with XLPE insulation and synthetic wire armouring and will be laid at about 900km.
The submarine cables will be manufactured at Germany’s Norderham Plant and Finland’s Pikkala Plant, which are both owned by the Prysmian Group. The land cables will be produced in the local plant of Vilanova in Spain.