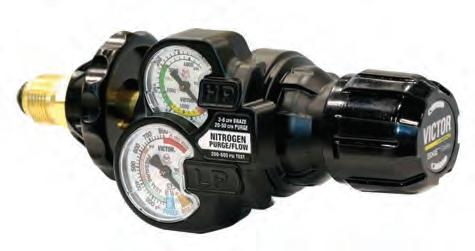
4 minute read
KEY SAFETY PROTOCOLS – PART I
Never isolate liquid sections of a system without provisions for a safety relief
With all refrigerants, attention must be given to the possibility of isolating liquid in one or more sections of the system without some form of relief device. For example, if a section of pipe is filled with a high fraction of liquid, there will be little room for expansion. If the pipe is 100 per cent filled with liquid, then there will be no room for expansion. If the pipe is exposed to heat, the liquid will start to expand. The pressure inside the pipe will expand rapidly, resulting in a hydrostatic condition. This rapid rise of pressure can quickly exceed the burst pressure of the piping, resulting in pipe rupture. Note that with R744 (CO2), the rate of pressure increase is higher than with other commonly-used refrigerants. For example, let’s consider the saturation pressures of R507, R717 and R744 at -40°F and +40°F. For R507, these pressures are 20.1 and 83.8 psia respectively. For R717, these pressures are 10.4 and 73.3 psia. For R744, these pressures are 145.7 and 567.6 psia. Between a range of -40°F and +40°F, the pressure of R507 increases 83.8 psi. For R717, the pressure increase is 62.9 psi. However, the rate of R744 is 421.9 psi.1 Referring to the gas laws, the pressure of a given amount of gas held at constant volume is directly proportional to the Kelvin temperature.
Ensure correct application and installation of pressure relief valves
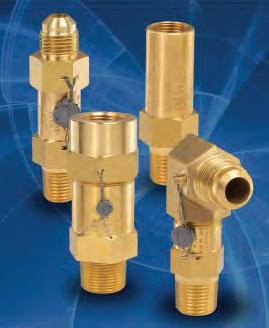
correctly sizing the relief valve for the correct flow rate and pressure, relief devices must never be isolated, not even temporarily. The inlet connection must never be reduced as it will restrict flow. Additionally, relief devices must never be stacked as this will lead to a very dangerous situation in the event of component over-pressure.
Replace damaged or corroded pressurevessels and components
The integrity of vessels and components must always be ensured. It is essential that corrective action is taken whenever a vessel shows signs of considerable corrosion and/or damage, even though there is pressure relief protection. A compromised pressure vessel may fail at a pressure that is lower than the relief device.
must never be isolated, not even temporarily.
On the topic of high-pressures, one must ensure that relief devices are installed in accordance with the various codes and standards. The ASHRAE 15 Safety Standard for Refrigeration Systems, outlines various requirements for relief devices and their associated discharge piping. In addition to
Avoid inhalation of brazing/welding fumes
Fumes from welding and brazing are generally toxic.These toxic fumes can also irritate the eyes, nose and throat and can even result in damage to the lungs. When brazing with systems that have previously contained refrigerant, the decomposed refrigerant along with other byproducts can be very harmful. With TIG welding, ozone is created along with off-gassing of molten metal.2 Welding of any type should only be done in a well-ventilated area.
It is also very important to wear the correct PPE. Longsleeved, fire-retardant clothing and safety glasses should be worn. For TIG welding, a full helmet, approved for the application, must be worn along with approved gloves and footwear. Note that many welders use a fire-retardant cotton bandana or skull cap to protect against airborne particles of very hot metal. Some welders use a balaclava sock hood that is made with fire-retardant materials.3 group, meaning that it is not toxic in the classic sense, and not considered to be flammable. However, R744 has a density that is approximately 150 per cent greater than air and displaces atmospheric oxygen. This means that R744 leaks will result in the workspace gradually filling from the ground up, similar to filling a container with water. In this case, R744 leak detectors must be installed in mechanical rooms at a low level, in accordance with national codes such as CSA B52, ASHRAE Standard 15, along with all relevant local codes that pertain to mechanical room ventilation and leak detection requirements. Wearing a personal refrigerant sensor badge or oxygendeprivation sensor on the body is an additional way to alert the technician that they are in a potentially dangerous situation.
Charging R744 into systems
R744 must initially be charged into the system as a vapour. The internal pressure of the system must reach a safe level above the triple point of the refrigerant before any liquid is charged into the system. This ensures that the R744 does not become dry ice in the charging hose and system. If liquid is accidentally charged into a system and dry ice has formed, never use a positive heat source in an attempt to melt the dry ice. System components can become brittle in the presence of dry ice and heating can cause rapid expansion and subsequent rupture of components.
Once the pressure of the system is at a level that is safely above the triple point, liquid can then be charged into the system. The liquid should never be charged into the suction, but into the high-side of the system, preferably into the receiver. Note that with R744 booster systems, the receiver or flash tank will be at a pressure that is above the suction, but below the gas cooler pressure of the high-stage circuit.
Never
pressure-test with oxygen
Ensure that an approved regulator is used when pressure testing.
Be aware of potential refrigerant dangers
Refrigerants exhibit different properties and are classified in terms of their relative toxicity and flammability to a predefined threshold as indicated in ASHRAE Standard 34. Using R744 as an example, it is listed in the A1 safety
Pressure-testing with oxygen is extremely dangerous. As the pressure of the oxygen increases in the system that contains oil, it may cause auto-ignition and result in a serious rupture in the system components. Use dry nitrogen for pressure testing and ensure that an approved regulator is used in order to prevent dangerous over-pressurization of the system. Never use a damaged pressure-regulator. Look for Part II of this article in the March/ April 2023 issue of Mechanical Business, where bypassing compressor safeties, starting compressors safely, and electrical test instruments will be discussed.
References:
1. Refrigerant pressures used for graph and discussion extracted from REFPROP ver. 9.1
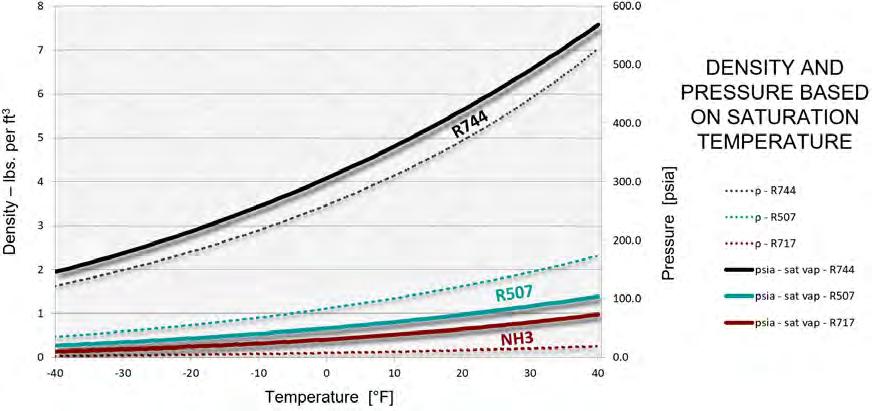
2. Gaslab.com, “Is TIG Welding Stainless Steel Dangerous?”
3. ESAB.com, “What to Know About Welding PPE & Protecting Yourself”
By Kerry Turner