
4 minute read
Carbon Capture and Storage Projects
Source: Stephen Stokes, Global Head of CO2 transport and storage, John Wood Group plc
Stephen Stokes is a chemical engineer, and throughout his career he has had a continuing focus on the properties and flow of multiphase phase fluids. Before joining Wood, he had spent more than twenty years in oil & gas operations in the North Sea and in Western Australia, progressing from operations to carbon capture and storage (CCS). Wood is currently involved in more than half the CCS projects worldwide.
Most members of the audience were already familiar with vertically integrated CCS projects, in which producers of natural gas remove and re-inject CO2 to reduce greenhouse gas emissions. In this address, Stephen’s focus was on multi-emitter projects, involving several diverse and geographically widespread industries including thermal power stations, hydrogen, and ammonia production plants. Liquefied CO2 is transported through branch and trunk pipelines to a collection hub and then transported to, and injected into, depleted petroleum reservoirs. Stephen referred to several such projects, including the European ‘Northern Lights’ project in which CO2 is to be collected and shipped by tanker to an injection platform the North Sea. Another project in Korea involves repurposing existing assets for an endof-life hydrocarbon platform to transport and inject CO2 into the depleted (low pressure) reservoir; this is financially attractive as it reduces abandonment cost (ABEX). Locally, the ExxonMobil SE Australia CCS project will collect CO2 from across the region and re-inject it into depleted Bass Strait formations. In the United States, the Gulf Coast CCS project envisages 400 km of pipeline, collecting 12 Mtpa by 2030.
It has been estimated that this CCS market will grow to USD 4 trillion per year by 2050, together with increased
Materials Australia
diversity in the industrial sources of the CO2 captured. The development of shared transport infrastructure within CCS hubs offers attractive economies of scale for emitters. However, the development of large‐scale CCS hub projects is complex, with many stakeholders responsible for various aspect of the value‐chain.
All these projects rely on transportation of a CO2 -rich liquid. As Stephen stressed, this is not simply liquefied CO2; CCS hubs are in effect a garbage collection service. Transport can dominate the cost of these projects, in the cost of securing transport corridors, capital expenditure and operating costs. The transport network operation will have to deal with an impure CO2 ‐rich fluid and hence the requirements for asset integrity assurance will be onerous. The logistics involved in building hundreds of kilometres of 36 to 42-inch pipelines is a serious issue, particularly in the United States, where line pipe manufacturing capacity is currently limited.
Stephen then turned to the technical issues in transporting these impure liquids, first dealing with the major non-condensable impurities, present in mol percent levels, mainly hydrogen but also nitrogen and ammonia. He explained the impact of the additional gases by referring to the CO2 pressuretemperature phase diagram, showing how impurities produce a two-phase region, with the result that higher pressures are needed to maintain the liquid state essential for economic transport. With 4 percent hydrogen, the pressure in the pipeline must be above 40 bar, and the density of the liquid is reduced by 20 percent. Together, these result in a loss of around 10 percent line capacity compared to transport of pure CO2
Another consequence of the expanded two-phase region, and need for high operating pressure, is that a leak in the pipe, with isentropic expansion of the escaping fluid, a high pressure differential is maintained across the pipe wall. This means that high toughness is required in the pipeline material to arrest crack growth, with the issues exacerbated by the low temperature produced by the fluid expansion, and the potential for hydrogen embrittlement. Minor impurities, at the parts per million level, arising from hydrocarbon processing include water vapour, amine, and glycols (MEG and TEG). Their impact is exerted mainly through their effect on water solubility, and hence pipeline corrosion. Traces of combustion products, such as SOx, NOx, and also hydrogen sulphide and oxygen, must also be dealt with. The general aim is for less than 50 ppm water vapour, zero glycols, and less than 10 ppm hydrogen sulphide.
The approach taken to handling the potential for variable inputs is to develop a Network Code, specifying fluid composition limits, as well as metering protocols and responses to and recovery from excursions from normal operating conditions. Each emitter must condition the fluids to be sent to the system, and the operator will only accept the fluids if they meet the code. However, a balance has to be struck; if the code is overly restrictive, emitters won’t use the system, but if it is too lax, the integrity of the system will be compromised.
A major joint industry project (JIP) is currently being undertaken to set CO2 specifications.
Stephen then referred to Wood’s ‘Electronic Corrosion Engineer’ (ECE) model for accurately calculating phase behaviour, including dew point. This allows ‘what-if’ modelling of off- specification scenarios at any point a transportation system, and hence planning of operating responses. However, there are currently no methods to reliably predict the properties of dense-phase CO2 when water is present. The solution might need to be mandatory dehydration of input streams.
This raised the point that CCS hubs are integrated projects. A systems approach is essential and ‘the right people have to be in the room at the same time’. There are balances to be decided between CAPEX, OPEX, and asset integrity, not only for the operator, but for every emitter who plans to use the system.
In his concluding remarks, Stephen emphasised that CCS is happening now, driven by carbon pricing in Europe, and by government incentives in the US. Transportation of a CO2 -rich liquid is big issue, and it must be accepted that dealing with this will involve a steep learning curve.
Stephen’s presentation drew an audience of more than ninety members and guests, making this breakfast meeting a very successful celebration of Sir Frank Ledger and his role in founding what developed into the Western Australia branch.
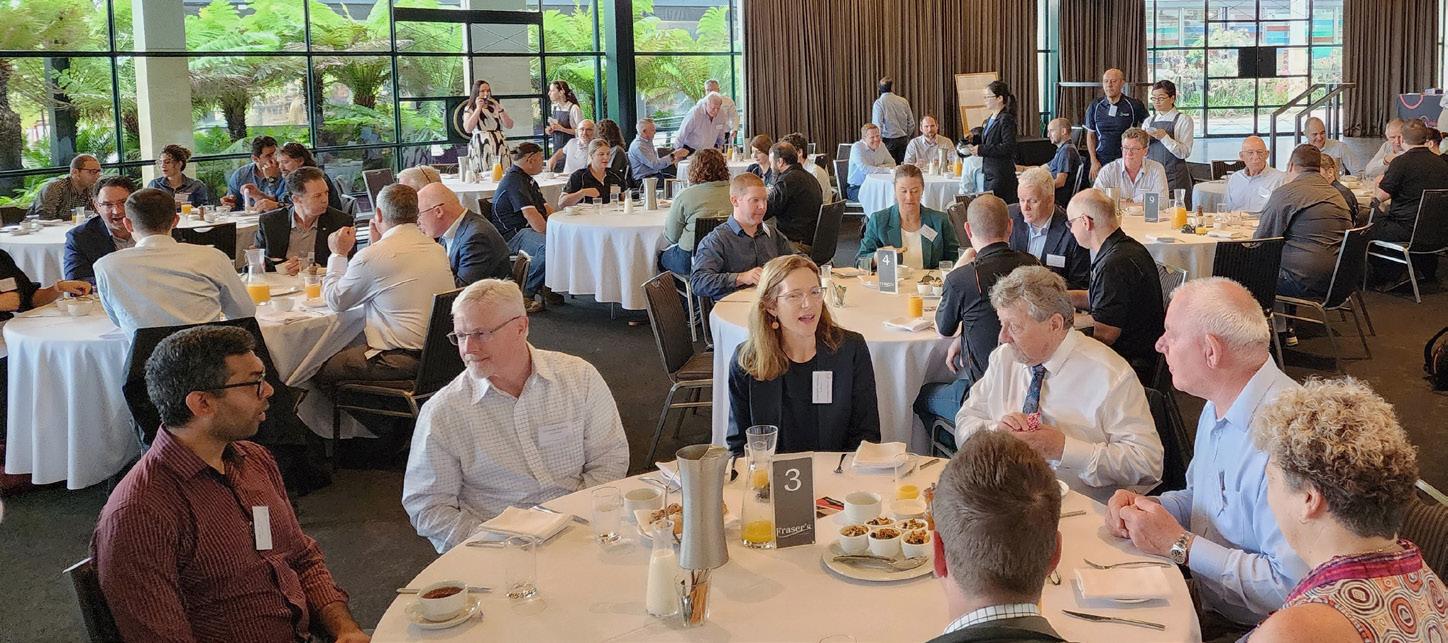
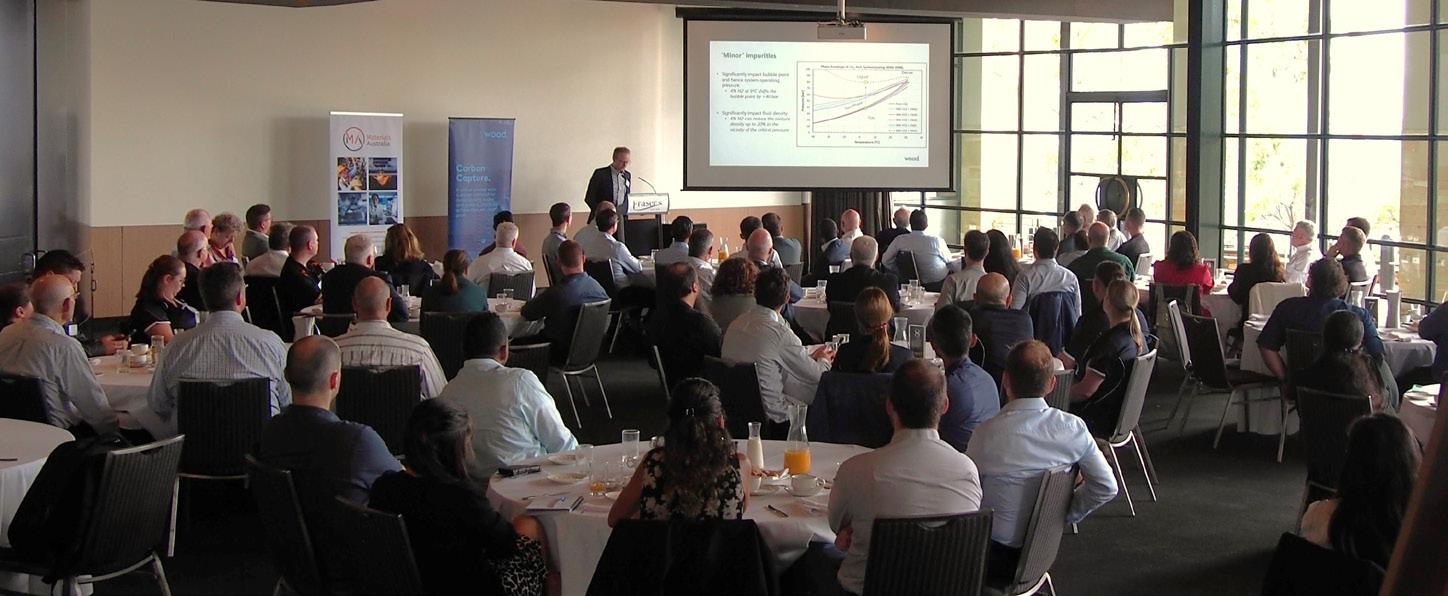