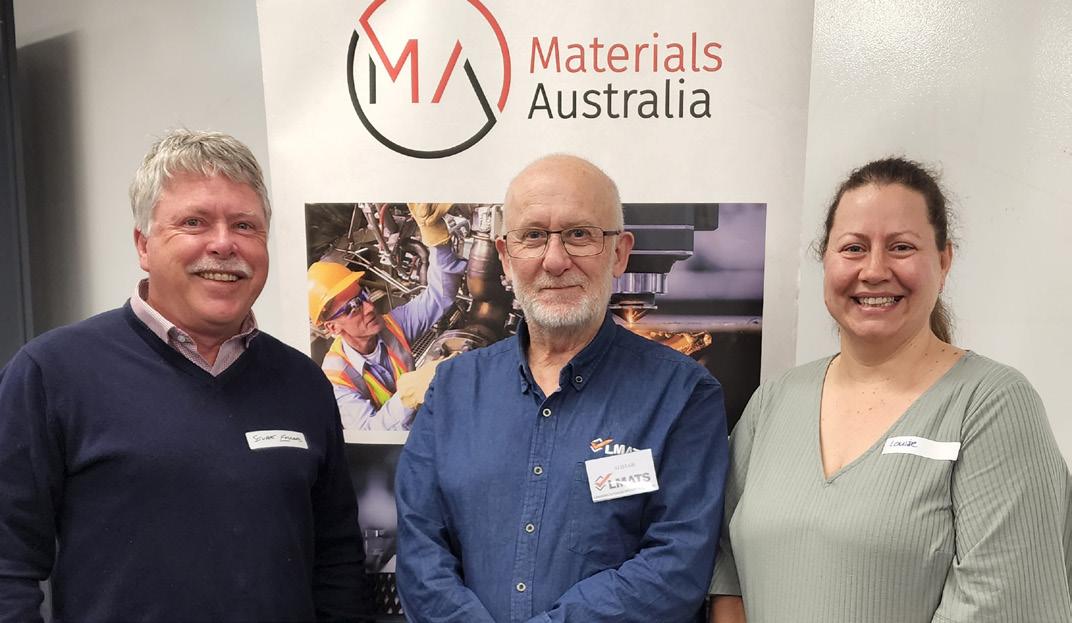
3 minute read
WA Branch Meeting Report - 12 September 2022
WA Branch Meeting Report - 12 September 2022 Ron Cecil Lecture: The ‘Dos and Don’ts’ of Stainless Steel: A Panel Discussion
Source: Alistair Tawns (LMATS), Stuart Folkard (Wood), Louise Petrick, Materials & Welding Solutions
Stainless steels are widely used in industry, both for structural and pressure containing applications. Whilst they have proven to be of significant benefit and have provided superior performance when compared to other materials, they can also be vulnerable to failure if their properties and performance are not subjected to careful consideration during the design, material selection, fabrication and installation phases. This year’s Ron Cecil Lecture featured a panel of experts whilst also welcoming contributions of experience, insights and questions from the audience. Many in the audience work regularly with the numerous grades of stainless steel, in design and engineering of equipment and processing systems, welding and installation or monitoring of their performance in asset reliability assessments. To form the expert panel, Alistair Tawns (LMATS) was joined by Louise Petrick (Materials and Welding Solutions), and Stuart Folkard (Wood), both of whom have presented at Western Australia Branch meetings earlier this year. Alistair’s 50 years' experience in materials started with his work as laboratory technician in the Royal Aircraft Establishment in Farnborough, focused on the then-new technology of carbon fibre composites. He then worked at DSIR in New Zealand on failure analysis. On returning to the UK, he continued his studies at the University of Leeds, where he gained his PhD on thermite welding of rails. After consulting work in the oil and gas industry in Aberdeen, he moved to Australia, taking on a role at Wood, and later at LMATS, where his expertise on thermite welding is still regularly called on. Alistair started the meeting by presenting a failure analysis case study concerning leaking at the mechanical joints on a super duplex 2507 grade stainless steel pipe. Extreme pitting corrosion had occurred in-service at room temperature with slightly alkaline seawater. Applying a G48 ferric chloride test confirmed susceptibility to severe crevice corrosion, while microstructural analysis revealed intermetallic precipitates. The combination of susceptibility to pitting and precipitates had led to autocatalytic corrosion. Alistair showed with time-temperature-transformation curves that the root cause was that the cooling rate during manufacture had been too slow – it had needed to be quenched within less that one minute. Ten years later, the result was failure in service.
Louise then spoke on welding of stainless steels and changes to AS 3992:2020 Pressure equipment welding and brazing. She highlighted issues of dissimilar metal welding in which chromium (ferrite stabilising) and nickel (austenite stabilising) equivalents are key factors, summarised in the Schaeffler diagram. Heat input and cooling rates are also critical. Local depletion of dissolved chromium, either by dilution adjacent to the weld, or by precipitation of carbides in the solidifying metal, is liable to lead to localised corrosion. Responding to the invitation to contribute from the floor, Bob Jensen passed around a failed swivel from a yacht anchor chain. This was stamped ‘316 stainless’, but it turned out that the bolt in the centre of the swivel, the part that had broken, was a lower chromium 200 (manganese) series steel. This led to discussion of the importance of material certification, and questions as to whether procurement departments understand this. Examples of ‘type’ certifications were given, in which purportedly official certificates had been supplied for each order of material, but were all exactly the same, even though it was clear form other information that they had come from different heats and could not have been identical.
The panel and audience then turned to pitting corrosion, emphasising the importance of passivating the stainless steel surface after pickling. The observation was made that 70% of the life of the component subject to pitting corrosion is in forming the pit. Hence, ‘if you provide a crevice, you’ve already lost 70% of the potential service life!’ Stuart wrapped up the meeting by answering questions about cryogenic applications – austenitic stainless steels do not have a ductile-brittle transition – and also on high temperature use. He provided an interesting example of corrosion of exhaust stacks, in which ‘steady state is your friend’, as condensation is an issue when the gas temperature falls below the dew point. All agreed that the meeting had succeeded in its stated objective of being an “interesting and stimulating opportunity for attendees to learn from the experts; bring and share knowledge and experiences; and to develop beneficial networks within their industry.”
L to R: Stuart Folkard, Dr Alistair Tawns, Louise Petrick