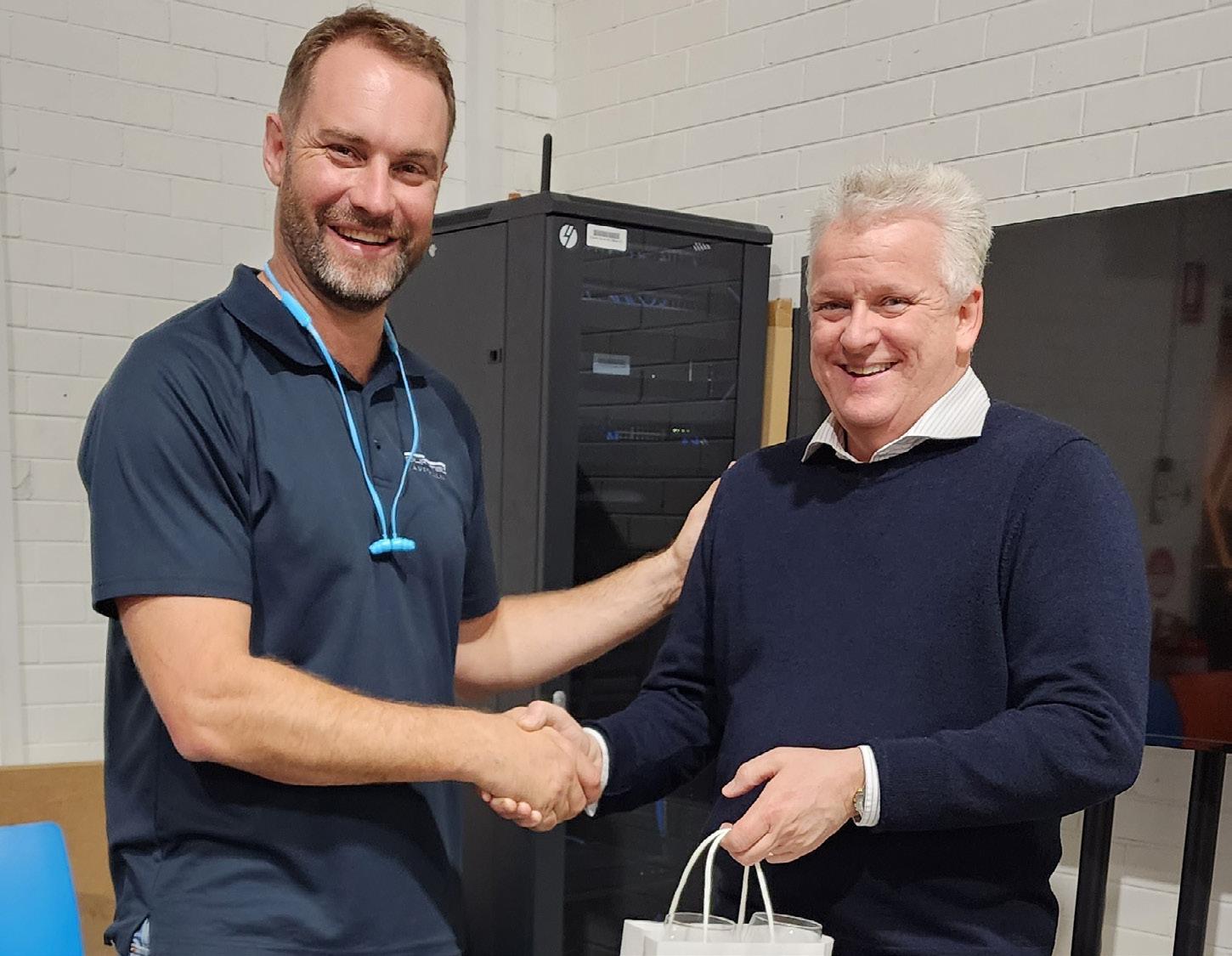
2 minute read
WA Branch Meeting Report - 10 October 2022
WA Branch Meeting Report - 10 October 2022 Site Visit to Duratec, Technical Laboratory, North Perth
The Western Australia branch recently hosted a site visit to Duractec’s technical laboratory. Duratec Australia specialises in the protection, remediation and life extension of steel and concrete structures. The technical laboratory conducts investigations designed to establish causes of failures, quantify deterioration and to aid in planning and execution of its on-site interventions.
Liam Holloway (National Technical Manager, Duratec Australia) developed the laboratory as a commercial application of the research on nondestructive testing of concrete, which he conducted at Monash University in gaining his PhD. The facilities demonstrated included: • Concrete petrography laboratory • 3D reality model capture, delivery and online defect management • Virtual reality spray painting training system • Electrochemical and rebound testing of concrete and masonry structures Concrete petrography, which uses geological microscopy techniques, is used to identify the constituents of the cement paste, classify the aggregate or sand type, map crack and microcrack patterns, identify secondary deposits and much more. This is used to determine which deterioration mechanisms, such as alkali-silica reaction, delayed Ettringite formation, sulphate, acid or soft water attack. One particularly interesting application is in heritage building conservation, for matching historic mortars and renders. From the petrographic and wet chemistry data, the percentage of portland cement, hydrated lime and sand in the existing mortar is calculated aiding in the mix design for remedial mortars and renders to obtain the best match.
Liam followed the demonstration of petrography with a demonstration of 3D reality model capture, using two examples: the old Fremantle power station and the Dampier Salt loading jetty. In the case of Fremantle power station, the model is based on some 35,000 to 40-megapixel images captured by drones. These high-resolution images allow the recording of sub-millimetre features (closer to 0.1mm), and with some supplementary laser scanning, cover the entire external and internal surfaces of the building. It was impressive to ‘fly around the building approaching from a distance and zooming in to fine details of cracked lintels, and so on. This model was used to develop options for stabilising the property, which is rapidly approaching an unsafe state.
The model of the jetty was constructed from 70,000 images from drone boats and flying drones and includes the ability to tag features and defects to each image point. Broadly speaking, it provides the equivalent of ‘close visual inspection’ over the entire structure, including locations that would be difficult to for a human to reach. The model was used to prioritise defects and to specify and price a $50 million contract. At the time it was made, processing the images took three months, but this is dependent of processing power and is reducing rapidly. The next demonstration was virtual reality training for spray painters, using a commercial software package ‘Virtual Paint’. The software is also used for planning access intended work, as it can be interfaced with models of structures and scaffolding to confirm accessibility for going to site. The virtual reality headset and manipulators provided visitors with a great opportunity to explore a virtual world. It was so immersive that, for some, it took a bit of time to get reoriented with the actual world!
Other testing equipment on show included rebound hammers, resistivitybased rebar locators. Electrochemical testing for corrosion potentials was demonstrated in conjunction with recently developed hybrid anodes, which are now being introduced for protection of rebar.
L to R: Dr Liam Holloway, Paul Howard