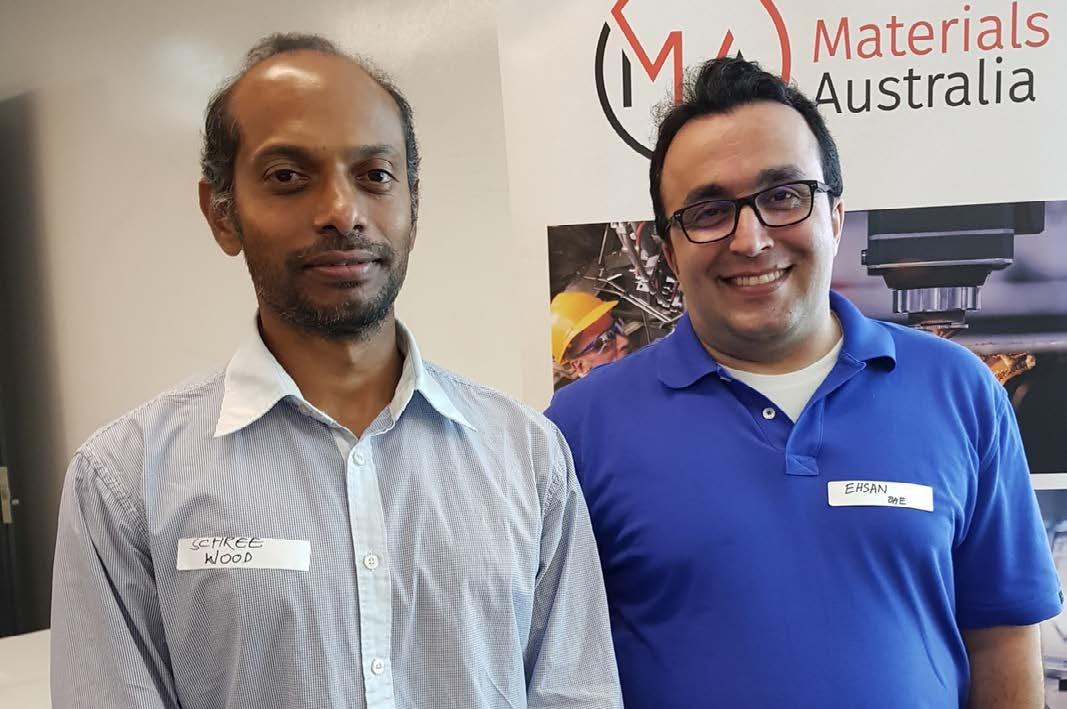
3 minute read
What Can Go Wrong?
WA Branch Technical Meeting
Source: Ehsan Karaji, Senior Welding Engineer – Maritime Sustainment, BAE
Ehsan Karaji (Senior Welding Engineer, BAE) presented in March to the Western Australia branch on the topic: Heat Treatment of 6000 Series Aluminium Alloys: What Can Go Wrong? Karaji started his career as materials engineer in oil and gas projects in southern Iran focusing on selection of materials for oil storage tanks, and later shifted his focus to welding aspects of materials engineering. Karaji's case study was about the challenges of developing a heat treatment schedule for producing T6 temper properties in complex shape machined from a 6082 aluminium alloy billet that was only available in the T5 condition. To put the challenge in context, Karaji gave an overview of aluminium alloys and their classification. Pure aluminium is soft and ductile and has high electrical and thermal conductivity, but these properties can be altered greatly through alloying. In particular, strength and ductility can be controlled through alloying to produce intermetallic precipitates followed by heat treatment to control their sizes and distribution. The challenge Ehsan confronted was of changing the distribution of Mg2Si precipitates. In the classification of aluminium alloys, the first distinction is between the three-digit (XXX) cast alloys and the four-digit (XXXX) wrought alloys series. With wrought alloys, the first digit (e.g. the ‘6’ in 6XXX) specifies the major alloying element. Thus: 1XXX refers to controlled unalloyed (‘pure’) aluminium, 2XXX alloys have copper as the main alloying element, 3XXX have manganese (giving good deep drawing properties, as used in aluminium cans), 4XXX have silicon (which reduces the melting point and is used in welding wires), 5XXX with magnesium have good corrosion properties (used in marine applications), 6XXX with magnesium and silicon have high strength (e.g. bicycle frames), 7XXX with zinc and several minor elements are used in aircraft applications, 8XXX alloys have tin, and some have lithium, while the 9XXX classification is reserved for future use. Heat treating of aluminium alloys, as for steel, is dependent on both temperature and time. The main feature is that it is a precision process undertaken in controlled furnaces. Reproducibility and uniformity are critical and generally, details have to be established for each type of product, not just for each alloy. The main heat treatment processes used with aluminium alloys are: Annealing: 300-420°C for stress relief and recrystallisation. • Homogenisation: 500-550°C to redistribute precipitates. • Solution heat treatment at 440-550°C, followed by quenching, to dissolve precipitates and produce a metastable single-phase condition. • Natural ageing at ambient temperature, for uncontrolled precipitation of intermetallic. • Artificial ageing (also called precipitation hardening) for controlled precipitation. Karaji was dealing with a complex component with 30 mm thick webs machined from a solid 500 mm diameter billet of alloy 6082 (1.1%Si, 0.75% Mg) supplied in T5 temper, with the following properties: 270 MPa UTS, 230 MPa proof stress, 8% elongation and 6% reduction in area (RoA). The typical corresponding properties in T6 temper are 310 MPa UTS, 260 MPa proof, 10% elongation and 8% RoA. An extensive program of testing of 30mm thick test pieces in a commercial heat-treating facility revealed a schedule of solution treatment, quenching and recitation hardening that could produce all the T6 properties except for RoA, which was found to be quite variable between test pieces taken from different heats (batches of alloy). However, 6% RoA was achievable, and the designers confirmed that this would be acceptable. The final schedule was solution heating for 12 hours at 550°C, with immediate quenching into water, and then precipitation hardening at 165°C for five hours. The conditions are quite critical. In giving examples of what can go wrong, Karaji explained that testing with temperature variations of 10°C in solution treatment and 5°C in hardening produced inferior outcomes. Metallographic examination showed that critical effect of process variation was in the form of the precipitates. A fine distribution without clustering is essential to developing the required properties. During questions about the test programme, a member of the audience recognised that the complex machined component was part of the new radar mast for the ANZAC Class Frigates. As to why it was this shape, which further complicated the heat treatment process, even if Ehsan had known the answer, he would not have been able to disclose it!