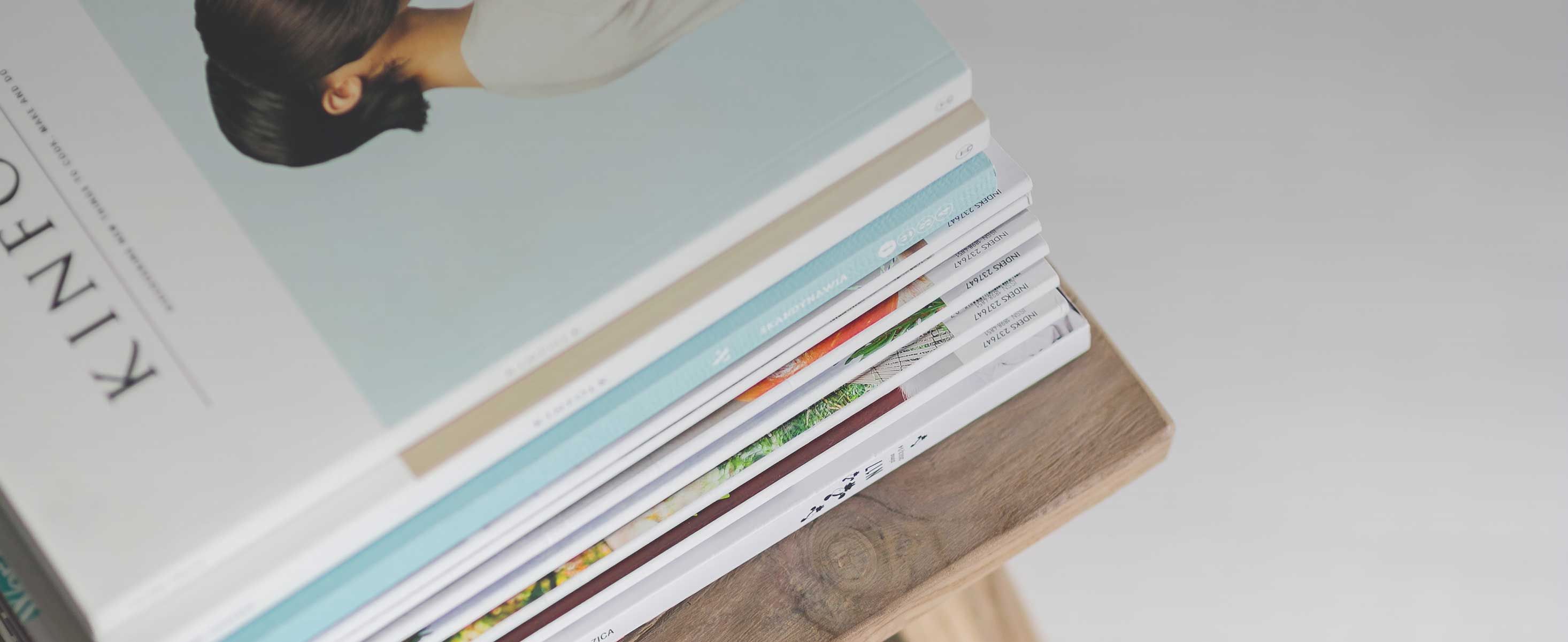
18 minute read
I. EXECUTIVE SUMMARY
This report covers the examination of the mold issue that has plagued the House of Justice as it relates to the air-conditioning system in place. A four-day survey was conducted from 29th of January to 1st of February 1, 2018. The survey covered a visual inspection to the facility, interviewing of building personnel in familiar with maintenance and operation of the air conditioning system in place, installing data loggers through the facility and equipment to record dry bulb temperature and relative humidity reading while the building was in use and when the building was unoccupied. Data was also collected on the air flow at the various zones, measuring the air flows of ceiling diffusers and registers for supply air, return air, and exhaust air. Data was used to analyze the dynamics of the air conditioning in place and how it affects the mold issues in the building.
What was found in the data and information gathered data shows that the building indoor condition promotes the growth of mold spores and colonize in surfaces. The mold and mildew within the building are evident by the musty smell throughout the facility It was most likely caused by water leaks from a various incident that happens in the building over the years During the inspection, there were only a few visible signs of mold on books, furniture, judge’s robe, and ceiling tiles, but none within the air handling units (AHU’s) and within the ductwork. The musty smell appears to be generated by materials that remained after the water leak events and not properly remediated to prevent the potential of mold growth such as carpet, furniture, ceiling tiles, gypsum board walls, furniture, books, papers, etc.
Advertisement
The air conditioning system does play a part in the continued problem of the musty smell by its inability to properly control the relative humidity within the various zones. Because of the changes in the uses of spaces throughout the building, the cooling load requirements have changed significantly, and the existing units are overcooled causing the room temperature requirements to be met quickly and not allowing enough time for the dehumidification process to occur thus causing wet-cold air. Additionally, there is very poor indoor air quality within the building. Most of the outdoor air dampers at the AHU’s were shut and inoperable. Also, almost all the exhaust fans were not working. This leaves the musty smelly air to re-circulate within the building with little means of escape.
Except for an ARRA funded chiller replacement in 2008 which installed new chiller, remote condenser and pump, most of the air conditioning system is old and antiquated with most equipment being what was originally installed when the building was open in 1997. Two of the existing chillers are still utilizing the R-22 refrigerant scheduled to be phased out in 2020. It is recommended to remove and replace older equipment and upgrade the system more appropriate to the current use of the building while improving the indoor air quality of the building.
II. GENERAL
WM Engineering Services, LLC (WMES) was tasked to provide mechanical consultation services to assess mold and high humidity throughout Guma’ Hustisia, Iimwal Aweewe, House of Justice Building located in the village of Susupe, Saipan, Commonwealth of the Northern Mariana Islands (CNMI) that may be caused by the existing air-conditioning system in place. The assessment shall focus on the air-conditioning system components including all associated equipment, piping, and controls. The intent of this project is to assess the current condition of the air-conditioning system that may be contributing to the high humidity conditions and mold, develop a concept design for the scope of work for the corrective repairs to the air-conditioning and ventilation system. The existing building is a concrete structure constructed in 1997 consisting of a basement, ground floor, and second floor, and houses the Supreme Court, 5 Superior Courtrooms, Justice and Judges Chambers, as well as supporting offices, library, and utility areas totaling to 32,637 square feet. Based on the construction documents provided, the airconditioning system in place is an air-cooled chilled water system which distributes chilled water at a constant volume to various air handling units and fan coil units. The air handling units and fan coil units are constant volume ducted systems which deliver cool air to the various cooling zones within the building. The controls for the air conditioning system are all local to the equipment and are stand alone. There is no central building automation system that controls or monitors the chiller plant, pumps, air handling units, fan coil units and exhaust fans.
WM Engineering Services conducted kick-off meeting on January 29, 2018, at 09:00 with the stakeholders involved with the maintenance and operation of the existing system to discuss the project concerns, challenges, goals, and expectations. WM Engineering Services then proceeded with a field survey immediately after the meeting. The survey was conducted from January 29 to February 1, 2018, on the existing air-conditioning system in place at the Judiciary Building. The survey included the verification of as-built conditions of the air conditioning systems in place by:
• taking photos to document of the facility
• record existing air flow at the registers throughout the building
• record temperatures, and relative humidity of various spaces
• confirm the operation and performance of air conditioning and ventilation equipment
• visually identify areas of suspicious mold growth and high humidity.
It should be noted that this investigation will not involve any breaking of walls, floors, and ceilings and will be limited to areas readily accessible and visible including access panels available. It should be noted that mold remediation and humidity solutions may extend beyond just the air-conditioning and ventilation system and may also include other disciplines such as architectural, industrial hygienist, and electrical engineering disciplines which are not part of this contract Our proposal excludes such architectural, industrial hygienist, mold spore evaluation, and engineering services.
III. FINDINGS
Since the facility was first built and occupied in 1997, there has been no significant changes recorded to the air conditioning system except for the “addition” of an ARRA funded 200 TON Smardt Chiller in 2008-2009 that included a new air-cooled condenser and chilled water pump. According to the building staff the building has been experiencing elevated relative humidity and mold issue over the past 10 years. Over the years there have been several changes of Building Superintendents supervising the facility. With the change of personnel, there appears to be a poor turnover of record keeping of the building’s maintenance records. Presently there are no available maintenance records or OperatingMaintenance manuals for the existing equipment. The current Building Superintendent stated there is no current preventative maintenance program in place for the air conditioning and ventilation system due to funding issues and the repairs and maintenance are on an on-call basis as required. On the kick-off meeting, it has been discussed the event of major water damage from a pipe bursting where the lower floor was flooded with kneedeep water in early 2000, but the remediation and repairs to the building appear undocumented. There has also been water infiltration damage from the Soudelor Typhoon. There is a contract in place to re-seal the windows which are continuing to leak wind-driven rain into the building. There is also an on-going contract to replace all carpet in the facility with laminate vinyl floor tiles.
It was found that there were several undocumented changes in room partitioning and changes in room use which differs from the construction document plans on record. A lot of designated offices have become the storage room for files, and other miscellaneous office supplies and furniture. Another major change to the building was the enclosure of the public lobby of the House of Justice building and the addition of a large package air conditioning unit, although the unit is not currently in operation. This area was originally designed as an open-air area with natural ventilation. Another significant change in use is the Library which currently used for offices, assembly, and file storage.
The water side of the HVAC system consists of two (2) 100-TON air cooled chillers, one (1) 200-TON Smardt chiller and three remote air-cooled condensers. The current system operates with the Smart DT chiller operating as the primary chiller in operation with the two TRANE chillers as back-up. The Smart DT chiller utilizes R134a refrigerant and the TRANE chillers both are R-22 type refrigerant. During the survey, the Smart DT Chiller was down for repairs and the two TRANE chillers were operating but only at 50% each due to compressor or refrigerant circuit issues on each chiller. The existing remote aircooled condensers were on the roof but were not accessed. The current leaving chilled water temperature conditions at 52 degrees F and returning at 56 degrees F, See appendix photo 1.0
Based on existing plans the chilled water pump is end-suction pumps rate at 240 gallons per minute (GPM), 120 feet total dynamic head pressure, and 25 horsepower. Currently, the newly installed chilled water pump number three (3) is down for repairs. Pump gages are not calibrated or broken so pump pressures could not be confirmed. The remaining 2 older pumps appear to be in fair condition, and the pump base and foundation are in fair condition. Originally the chilled water pumps were interlocked to operate with its associated chiller but appear to be manually operated. The indoor chilled water piping and insulation remained intact. Chilled water components are in fair conditions, but the surface of piping showed signs of corrosion, see photo 1.1.
Due to Scope of work, there was no testing of the valve and inspecting inside section of each component. More so, the underground chilled water pipe is not assessed. There is a suspected water leak in the chilled water piping system which requires the make-up water tank to be filled every 3 days according to maintenance sub-contractor JWS.
The air side of HVAC system consists of chilled water type Air Handling unit and Fan Coil units which distributes air into the various rooms within its respective zone via an insulated steel duct system. There are 16 large AHU ranging in capacity of 10 TON to 25 TONS of cooling. The smaller FCU consist of 8 units and range from 1 TON to 2.5 TONS of cooling. The AHU’s are single zoned, constant volume unit and have a mixing-filter box with washable filter. There was originally motorize dampers on the outside air and return duct, but they are not operational. The original automated controls have been disabled and the AHU’s are being controlled locally by a temperature sensor in the main return duct within the mechanical room and a thermostat controller on the mechanical room wall. There is also a timer installed within the mechanical room but was disabled for the most part. There is also a large TRANE package type unit, independent of the chilled water system, located on the supreme court roof and intended to cool the main entry but the capacity could not be confirmed because it is missing the nameplate data. This unit is currently not operational, and it is not known if it is still functional. The Building Superintendent stated it was not in use to reduce electric cost. There is a standalone direct expansion unit located in the ADR/Conference room area. A separate split type unit in the IT room that supplements the existing air supply near the former storage/workroom. There are three (3) 120-pint Honeywell dehumidifier was added and installed in the return duct of AHU 8, 14, and 15 that are in constant operation, but there are no plans or other design documents recording what was installed or how it was installed. The installing contractor JWS did mention that the dehumidifiers are always in operation, but it was not clear how it’s operation coincides with the operation of the AHU’s.
15.
16.
17.
PCU-1
Supreme Court
Sally Port/Basement
ADR/Conference Room (DX-split Unit)
Main Entry (Package Unit)
The AHU # 2 filter and filter rack were severely damaged due to corrosion, see photo 2.8. The AHU that serve the Superior Courts 202, 205, 217, 220 and 223 each has outside air damper that was shut closed and corrosion damage is present on each damper’s louver, see photo 2.9. The AHU # 3, 7, 9, 11 and 12 are installed with new outside air Manual volume damper and was also close The old actuator motor and its wiring are left inside the Mechanical Room, see photo 3.7. The AHU # 10 is installed above the ceiling of Evidence Room at Marshals Office. Unit’s Power and control wiring are pulled out of its connection. Smaller FCU was not visually surveyed because they were primarily recirculation of air within small spaces. Ductwork within the mechanical room appeared to be in fair condition except for the outside air ducts and some mixing boxes which were corroded and inoperable. Accumulation of dust and dirt are present at diffuser face and at intake louvers.
See photo 5.1.
The only air circulation comes from the people traffic which comes mostly in the main entry for the public and the employee traffic in the back entry. This allows untreated warm humid air to enter the building without being treated. There are several exhaust fans and ventilators throughout the facility and most are not operational. Many of the exhaust registers are cover with dust. The controls appear to be either manual controls or interlocked with the light switch.
IV. ANALYSIS
There was a strong musty smell within the air-conditioned areas which is a sign of an environment that promotes mold and mildew. Mold and mildew usually can be found in building components (duct insulation, gypsum board, ceiling tiles wood, etc.), furniture, papers, and carpet floor covering where water is absorbed readily. The usual cause would be water damage from water leaks from piping or water infiltration into the building from wind-driven rain such as a storm or typhoon or even structural cracks on the roof or improperly sealed pipe, or duct penetrations through the walls or roof. Once the mold and mildew have occurred within the building, the best way to remediate is to remove the affected areas and maintain a dry environment. Because there has been recorded major water damage from a pipe leak and continues to have water leaks around the window, the presence of the mold and mildew will persist until physically removed from the premises. Disinfecting and cleaning of affected areas can remove on the surface but will not remove mold and mildew deep inside the material. The planned removal of the carpet and the repairs to the leaky window are a good way of reducing the sources of moisture that promote the growth of mold and mildew in the building. It is strongly recommended to dispose of all clothing in one of Justice’s wardrobe closet, furniture, books, and papers where mold is visible, see photo 5.6. There were only a few areas where building components had visible mold and mildew. No visible mold on the surface of walls and partitions. Some were found on ceiling tiles such as in Jury Room C, but they appear to be water leaks from the structure Many ceiling tiles on the first floor and second were sagging and could be an indication of high water content in the material, thus ceiling tiles should be replaced, see photo 5.2. There was no evidence of mold and mildew within the cooling coils, air filters, fans, or inside the ducts. It is highly recommended that the air distribution ductwork, air handling units, fan coil units, and diffusers/registers be professionally cleaned. Also, install more efficient disposable MERV 13 filters in the AHU’s and FCU’s to reduce the dust in the building. The fungus is more likely to grow whenever the environment suited them. A spore (seed), a viable source of food, adequate moisture in the food source and acceptable temperature are the four (4) elements that molds needed to grow. Over the years, the building where exposed to several types of water damage. Without a proper water removal or drying, moisture remains entrapped in the surfaces. Introducing cool-dry fresh air into the space help help lower the humidity level in the space. With the lack of fresh air due to the closed fresh air intake dampers and the broken exhaust fans, the musty air is only circulating within the space through the air handling units The only air that may exfiltrate or leaves the building is from people moving into and out of the building through the main entry, back entry, delivery areas, and other less used exit doors.
The AHU’s airflow has a noticeable drop in performance. Based on airflow taken at the registers and diffusers during the survey (see Appendix C-3), the air flow has been reduced from 19-43% of the original design parameters creating even more poor air circulation. The data collected from the survey showed that there was unusually high relative humidity over the entire building, except for the ADR/Conference room area and the server IT area which has its own air conditioning system and is independent of the chilled water system. ASHRAE standards for room dry bulb temperature and relative humidity for human comfort set the ranges at 75-78 degrees Fahrenheit (F) for summer conditions and relative humidity (RH) in a room from 40-60%. The existing rooms served by the chilled water system have room dry bulb temperatures of 68-72 degrees F and RH in the range of 6588% (see Appendix C-5). Currently, the thermostat is set at 68 degrees F and the almost time the timers have been disabled, thus allowing the unit to run continuously. This includes the AHU with dehumidifiers installed in the units. Also, interesting to note that despite the diminished capacity of the chilled water system and the air handling units, the space temperature remained colder than what is expected. It was usual to see some people have small floor mounted space heaters near their desk (see photo 5.8). An analysis was performed on the cooling load requirements based on the current use of the building (see Appendix D). Because of the many changes of room uses, such as converting an office to a storage area, or converting the library to an assembly room/storage/IT/office requires a much different cooling capacity. From the table below, it can be seen that the current load is up to 87% less than the original cooling requirement.
The design has a change of temperature of the entering and leaving temperature 10 degrees F with water entering at 45 degrees F. This should create a drop on air temperature across the cooling coils of 15-20 degrees F. Currently the existing temperature entering and leaving the coil is only 4 degrees F and the temperature drop across the cooling coils are only 1 to 3 degrees F. The elevated entering chilled water temperature at 52 degrees F reduces the AHU to reduce temperature and lower the relative humidity in the room. When the AHU’s capacity is oversized for space, the temperature can be met quickly and not allowing moisture in the air to condensate at the cooling coil. The psychometric process of air conditioning cycle is to cool and dehumidify the air as it reacts to meeting the thermostat setpoint.
The age of the equipment, the current repairs, and the refrigerant it uses, it is recommended to replace the older TRANE chillers, remote air-cooled condensers, and associated chilled water pumps. The older TRANE units are using R-22 refrigerant which had stop production in 2010 and is scheduled to be phaseout by 2020. Also, it is recommended to replace the existing AHU’s and FCU’s and its associated piping and controls because it is also at its end of useful life and it is oversized for the zones it serves. By replacing the existing AHU’s with more appropriate size units, the system will be able to control the temperature, as well as, the relative humidity better in the occupied spaces. As an option, ACCU thermo-fusers VAV diffusers (see appendix G) can better control air flow into the space based on the demand for cooling by varying the amount of airflow into the space. This can reduce the energy cost of operating the air conditioning unit by reducing the fan speed during the time of low occupancy. Typically, a building would introduce outdoor requirements of a building into the AHU’s to allow the air to be pretreated before entering the building. Other outdoor air may enter the building untreated through people traffic at entry doors and infiltrate through small gaps around fenestrations in the building construction. The lack of fresh air into the AHU’s creates poor indoor air quality. Outdoor and exhaust air is required per the International Mechanical Code and ASHRAE 62.1 standard. The normal building design would keep the building under slight positive pressure by providing at most 10% more make-up air than exhaust air. Since the exhaust fans are mostly not working and the outside air dampers in the AHU’s are closed there is currently no mechanical means from the system that generates the code required fresh air and exhaust air flow rates. There is a lot of infiltration and exfiltration from the people traffic in the Main Entry where the public enters and the Back Entry where the employees enter and exit. Because the Main Entry air-conditioner is not in operation and the back entry not having any air conditioning because AHU #10 is not operational, the building’s exit and entry points are under neutral building pressure allowing untreated warm, humid outside air to enter the building thus attributing to the high humidity conditions
It is recommended to re-introduce an air conditioning system at the Main Entry, using dedicated outdoor air units to provide the required make-up air plus 10% above the required exhaust air to pressurize the building and minimize the amount of infiltration of the untreated humid outside air into the building to reduce the buildings high relative humidity. Additional, a vestibule can be added to the main entrance where the most people traffic occurs to further reduce the amount of warm outdoor air infiltrating into the building It is also recommended to incorporate a ventilation demand system into the AHU’s where occupant load varies greatly over the day. A ventilation demand system will modulate the amount of outside air in the space by using carbon dioxide (CO2) sensors to detect occupant load based on the CO2 level in the room and modulate a motorized damper in the outside air ducts. This system will reduce energy cost by minimizing the amount of outside air when the zones have low occupancy. Further, it is recommended to incorporate an odor control GPS system (see appendix G) into all AHU’s and FCU’s to control the musty smell. There is no preventative maintenance plan in place for the upkeep of the air conditioning and ventilation system. It is highly recommended to incorporate a preventative maintenance plan to ensure the system is functioning optimally and to guard against major breakdowns in the system. A central building automation system is also a good tool to centrally monitor the equipment’s operation that is remotely located on the roof and is hard to access. The central monitoring station can be located in the Buildings Superintendent Office and/or maintenance service provider.
V. SUMMARY OF RECOMMENDATIONS
A. Remove all carpet, furniture, books, paper, clothing, and sagging ceiling tiles affected by mold. Seal building leaks in the structure and windows. Seal any duct or pipe penetration in the building envelope that may be leaking into the building.
B. Remove and replace existing air-conditioning system including TRANE chillers, chilled water pumps, remote air-cooled condensers, AHU and FCU. This would include the replacement of the two r-22 chillers with one 100 TON, R-134A chiller, removal of 2 remote air-cooled condenser and replace with on 100 TON package air-cooled chiller one roof, removal of 3 chilled water pump and replace with two variable frequency drive pumps rated at 240 GPM, 120 TDH, AHU and FCU to the appropriate size based on current use. All control will be local.
C. Add dedicated pre-cooled outside air unit at the Main Entry and Back Entry Add appropriate controls to incorporate OA dampers controlled by the CO2 sensor.
D. Add odor control system to AHU and FCU. (See brochure in appendix G)
E. Clean duct, and install higher efficiency filter (MERV-13) (See brochure in appendix G)
F. Perform Testing and Balance air distribution and chilled water to the new system.
G. Remove and replace all exhaust fans
H. Remove AHU-10 and connect ductwork to AHU-9.
I. Option, provide ACCUTHERM diffusers to allow for individual room control and retrofit VFD to the AHU (See brochure in appendix G)
J. Option to install a Building Automation System to provide central monitoring of HVAC operation at Building Superintendent office.
Vi Estimated Cost
Base Mechanical:
A. Removal of existing 2 ea 100-ton Trane Chiller including its remote condensers, chilled water pump, and associated accessories. Supply and installation of a complete system of 1ea 100-ton high efficient chiller with remote condenser and option of 1ea 100-ton H.E. package chiller, including 3 ea new variable frequency drive chilled water pump, support, and accessories.
Estimated Cost: USD 2,249,891.06
B. Supply and complete installation of Precooling Coil system including demand control ventilation DCV (CO sensor) support and other accessories.
Estimated Cost: USD 532,263.03
C. Supply and Complete Installation of Odor Control System.
Estimated Cost: USD 186,515.09
D. Supply and complete replacement of Roof ventilator and Inline Exhaust Fans.
Estimated Cost: USD 139,692.10
E. Source removal, Cleaning and Sanitize Air Duct System including Supply and installation of new high efficient pleated type filter.
Estimated Cost: USD 125,260.07
F. Complete Removal of AHU #10 and Install ductwork to AHU #9
Estimated Cost: USD 9,332.42
G. Test and Balance Air distribution system and Chilled water system
Estimated Cost: USD 315,751.35
Options:
A. Supply and Installation of ACCU Therm-fuser VAV Diffuser for offices, including basic TAB works.
Estimated Cost: USD 435,152.61
B. Supply and Installation of Building Monitoring System (BMS) including training and supply of Hardware and software devices.
Estimated Cost: USD 366847.11