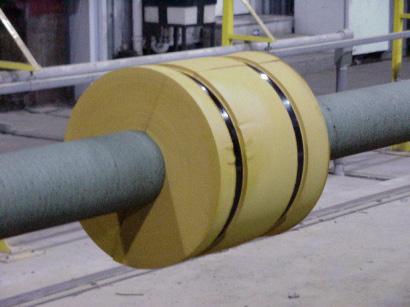
1 minute read
URETHANE PIPE SPACERS
Prevent A Slow Down In Operations With A Material That Can Stand The Test Of Time
Polyurethane is the ultimate workhorse.
Advertisement
Whether used as a spray, foam, a flexible, spongey elastomer, or a solid that is as hard and tough (almost) as any diamond, polyurethane’s versatility means it can be molded into components of any size, shape, and hardness.
The oil and gas industry demands a lot from its tools, including customization in the design-build phase and ongoing reliability in the field. Polyurethane parts stand up to any punishment thrown at them, and new ones can be quickly machined as needs change or evolve.
Urethane pipe spacers and casing spacers are placed around pipelines in underground and subsea applications. They make a perfect case study to illustrate what we’re talking about.
Put simply, these humble components keep pipes carrying oil and gas a specific distance apart. Outside of the oil and gas industry, they’re used to hold water, sewage, and electric pipelines in place. They also prevent damage to pipes and casing as they’re being stored in pipe yards or transported to the field. Pipelines protected by casing also use spacers to separate and isolate the carrier pipeline from the casing.
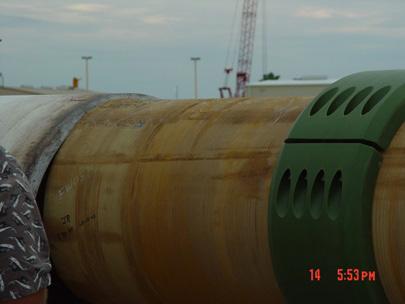
Pipes maybe made of steel, concrete, PVC, polyethylene, or plastic. Pipe spacers can be formed from various types of rubber and plastics, including polyurethane, polyethylene, PVC, carbon steel, and stainless steel. Along with the product the pipe carries and the environment surrounding the pipeline, the pipe’s material will determine what kind of spacers are appropriate.
Polyurethane, however, is our material of choice for the harsh environment of the oil and gas industry. When other materials often crack, break, tear, swell, abrade, and deteriorate, polyurethane can stand the test of time. Metallic and plastic spacers are vulnerable to problems that can slow down operations and, ultimately, lose revenue.
Polyurethane pipe spacers can be easily formed to your precise specifications because they are castable. Complicated design and engineering are usually required to adjust metallic pipe spacers, while urethane-based materials are easily formed into exact dimensions from simple silicone molds.