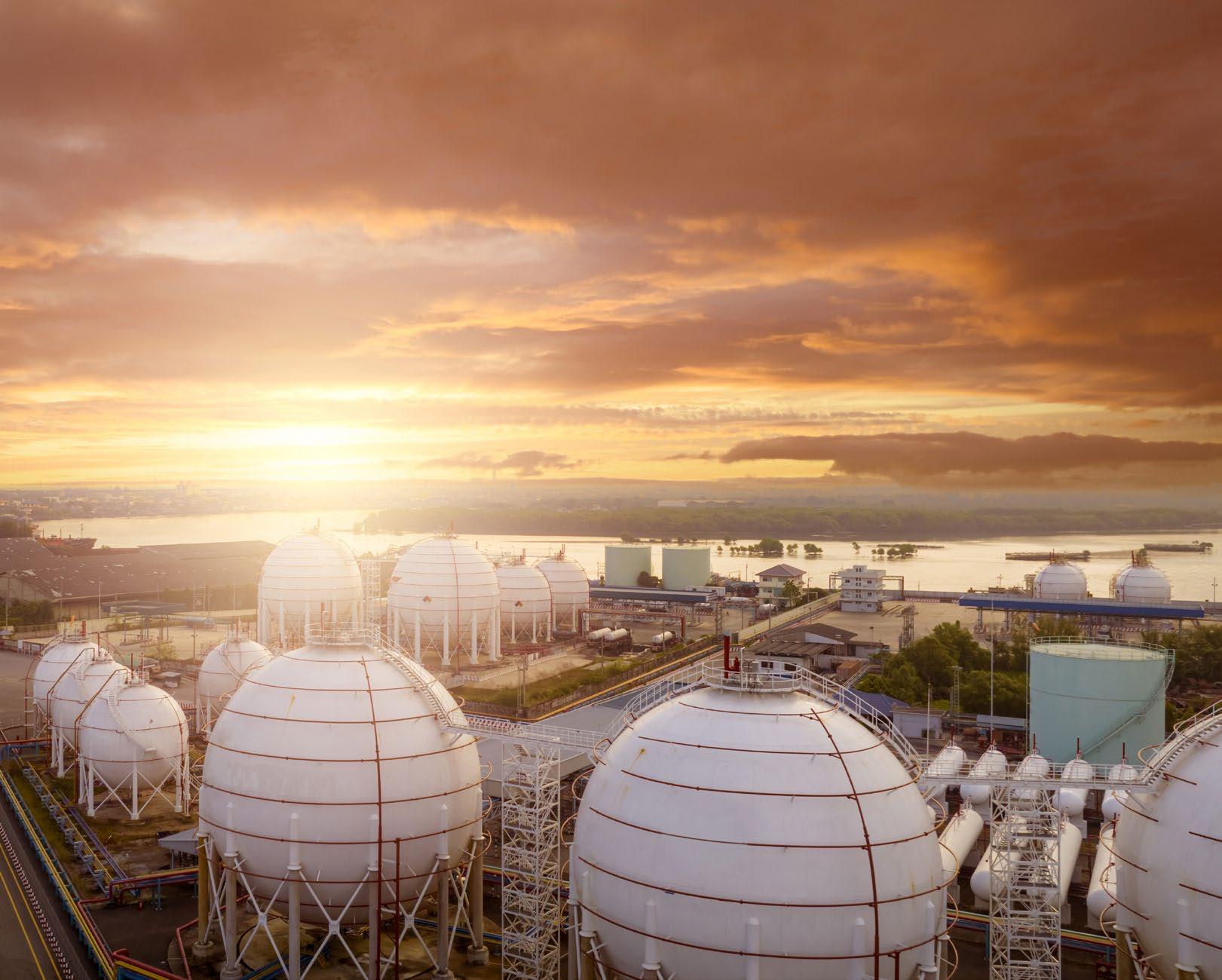
9 minute read
ALTERNATIVE FUELS
from CSI Winter 2022
by Maritime-AMC
A JOINED-UP APPROACH
A number of new partnerships, studies and trials are providing insights into the use of alternative marine fuels in the industry’s race to become more energy efficient and eco-friendly
A consortium led by classification society ABS and including CE Delft and Arcsilea, has published two of up to six reports studying alternative fuels and decarbonisation technologies for the European Maritime Safety Agency (EMSA).
ABS has offered a 360° view of biofuels and ammonia. Each fuel was analysed using various criteria such as greenhouse gas (GHG) impact, sustainability, fuel availability, fuel scalability and human needs.
“I am very excited about this project and the work that ABS is delivering for EMSA and the shipping industry,” says Georgios Plevrakis, ABS vice president of global sustainability. “These two reports are the result of one year of intense activity with our collaborators, EMSA and industry leaders to gather data and conduct three hazard identifications (HAZIDS) for each study. Our analysis is very unique and, in my opinion, what is needed to empower and inform future studies, conversations and decisions.”
“Biofuels are one of the main available renewable fuels at the moment and the shipping sector needs to move to e-fuels to decarbonise,” says Jasper Faber, director of shipping at CE Delft. “These two reports provide the most recent information on the availability, sustainability and cost implications of using these fuels
“The ro-ro passenger ship HAZID was a particularly notable example of industry collaboration, where a variety of ropax and cruise operators volunteered valuable time to contribute to the HAZID together, and this will help build much needed technical competence and confidence in alternative fuels,” says Edwin Pang, founder of Arcsilea.
The four-year project began in 2021 with the objective of studying key aspects of the decarbonisation of shipping, including alternatives such as biofuels, ammonia, hydrogen, wind-assisted propulsion, and complementary measures such as air lubrication and other promising technologies. The initiative is part of EMSA’s mission to provide technical assistance to the European Commission in the promotion of sustainable shipping.
KEEPING TABS
GoodFuels, a biofuels provider for the global transport industry, recently announced the results of a new partnership with global certification organisation Control Union and France’s IDS Group to test the effectiveness of a unique isotopic tracer for biofuels.
A successful pilot, conducted during a recent delivery of 500 tonnes of biofuel to the Norden-owned tanker Nord Gardenia, has proved the effectiveness of the tracer technology in real-life applications.
The partnership, which commenced in early 2022, has seen the companies collaborate to create the new tracer, which can be added to marine fuels as a unique “fingerprint” and verification tool.
The isotopic tracer stays within the fuel throughout the entire downstream of fuel delivery. It then can be tracked and traced by inspectors to verify that a fuel product has not been diluted or tampered at any stage in the supply chain. The trial has demonstrated that the tracer does not adversely impact the physical properties, quality and stability of the biofuel, and that tracing and testing activities could be performed without any impact on bunker operations.
The pilot also showed that the isotopic tracer can successfully measure for fuel dilution, when biofuels are used in a blend, for example.
The tracer can be applied at any stage in the supply chain and is based on natural elements so as not to compromise the sustainability of the biofuel product. It has been specifically designed to trace fuels at different granularity levels, making it suitable to be used within fuel products whether they are 100% biofuel or part of a blend with conventional marine fuels.
It can also be used to support carbon calculations and provide evidence for carbon pricing and tax reductions, giving shipowners and operators assurance on the amount and quality of biofuel they are deploying in their pursuit of sustainable shipping.
Commenting on the partnership, Dirk Kronemeijer, chief executive of GoodFuels, says: “Being able to undisputedly trace that our fuels are sustainable and uniquely assignable to one of our clients is intrinsic to what we do at GoodFuels. Following the world’s first bunker delivery using blockchain technology in 2018, we continue to introduce cutting-edge solutions, together with our partners, to increase traceability in the shipping industry. Using a physical marker that combines with software is the likely next step in this trend. We are focused on driving even greater trust and transparency in the marine fuels supply chain.”
Johan Maris, chief executive of the Royal Peterson and Control Union Group, comments: “Through this trial we have now proved this tracer technology and that proof brings endless potential. The tracer technology can, for example, ensure that fuel doesn’t originate from banned countries but can also be used for many other purposes, in other liquids like oil or even champagne, and in almost any type of solid materials like meat, plants, and metal.”
Patrice Fauvet, chief executive and R&D director of IDS Group, adds: “We are pleased to demonstrate and prove our ability to physically mark, track and trace (bio)fuel products, setting the new bar for traceability alongside the frontrunners in sustainability. We are also exploring expanding our patented marking technologies to any other hydrocarbons product.”
According to Henrik Røjel, head of fuel efficiency & decarbonisation at Norden: “Biofuel is a key transition fuel on Norden’s journey to zero-carbon shipping, as it can be used onboard our current vessels to make an immediate reduction on carbon emissions. We continue to bunker biofuel on a regular basis and support efforts of adding more transparency on the green fuels we bunker.”
The tracer project is just the start of a wider partnership between GoodFuels, Control Union and IDS Group. All three companies share an ambition to increase transparency in the fuel supply chain and the tracer will help to advance a shared vision of a standard label for biofuels that would be recognised worldwide as a sign of quality by the fuel market. CHECKLIST CONTRIBUTION
The IAPH Clean Marine Fuels (CMF) Working Group has published a total of six new checklists, which cater for both ship-to-ship and truck-to-ship bunkering operations of liquefied gases as a marine fuel at ports.
Following the work of the members of the working group, these checklists, which are applicable to LNG and liquefied biogas, but also to liquid hydrogen, will contribute in a very concrete way towards shipping’s energy transition.
The harmonised bunker checklists reflect the extra requirements of ports about safe bunkering operations of alternative marine fuels in or near their port environment. By using such bunker checklists, a high level of quality and responsibility of the bunkering operators can be obtained. They will also be of great benefit to vessels and their crews bunkering in other ports because it will reduce the potential confusion caused by having to comply with different rules and regulations in different ports.
The checklists can be obtained by registering, accepting terms and conditions and then downloading the checklists from the IAPH Clean Marine Fuels Working Group portal.
BIO-LNG BOOST
Attero, Nordsol and Titan have joined forces to achieve a decentralised production of bio-LNG designated for use in the maritime industry. The plant will be located at Attero’s facility in the Netherlands.
The FirstBio2Shipping project is set to deliver the first bio-LNG in early 2024. The plant will produce around 2,400 tons/year of bio-LNG (or liquefied biomethane). Attero will process domestic biowaste into six million Nm3 of biogas per year. Nordsol and Attero will jointly produce 2,400 tons/ year of high-purity bio-LNG and 5,000 tons/year of liquid bio-CO2 from this biogas using Nordsol’s patented iLNG technology.
Clean fuel supplier Titan will supply the bio-LNG to the maritime industry, where it will cost-effectively substitute fossil fuels.
The produced bio-LNG will reduce greenhouse gas (GHG) emissions
by 92% compared with conventional maritime fuel, representing more than 87,500 tCO2e net absolute emissions avoided during the first 10 years of operation.
More ambitious sustainability goals and the need for energy independence have increased the demand for biomethane in both gaseous and liquid forms, the partners say. With the decision to invest and collaborate in the FirstBio2Shipping project, the three partners make it clear that bio-LNG production with integrated biogenic CO2 liquefaction offers maximum green value and economic value for biogas, even if the production plant is smallscale and is decentralised.
Léon van Bossum, commercial director, Nordsol comments: “Nordsol is committed to making bio-LNG mainstream, together with various partners. In 2021, we built the first Dutch bio-LNG installation to make road transport more sustainable. As a frontrunner, we are proud to also contribute to the decarbonisation of the maritime sector, together with Titan and Attero. The FirstBio2Shipping project is intended to start a snowball effect, resulting in more and larger installations that help make shipping more sustainable.”
Ronald van Selm, CTO, Titan says: “At Titan, we are dedicated to delivering all fuels that decarbonise shipping and industry in a substantial way. We recognise bio-LNG as a strong clean fuel and we have therefore acted to progress its production and supply to the maritime industry. We are excited to reach the build stage of the project with the Attero and Nordsol teams.”
“Producing bio-LNG out of biogas from biowaste for decarbonising the maritime sector is a unique innovation,” adds Jan-Willem Steyvers, business developer, Attero. “We are delighted with the cooperation with partners Nordsol and Titan in bringing biogas to a high-end quality product – yet another step in our mission of continuously increasing sustainability and creating raw materials and energy out of waste.”
Last year, The European Union awarded the project €4.3m in funding, a recognition of the vital role that bioLNG will play in decarbonising longhaul maritime transport.
In October, the European Parliament adopted the FuelEU Maritime Regulation, which aims at the decarbonisation of maritime transport, and recognised (liquefied) biomethane as a renewable fuel and its potential to blend with and replace fossil liquefied natural gas. The joint bio-LNG project, therefore, fits into European policies to achieve the climate and energy transition goals. REGASIFICATION APPROVAL
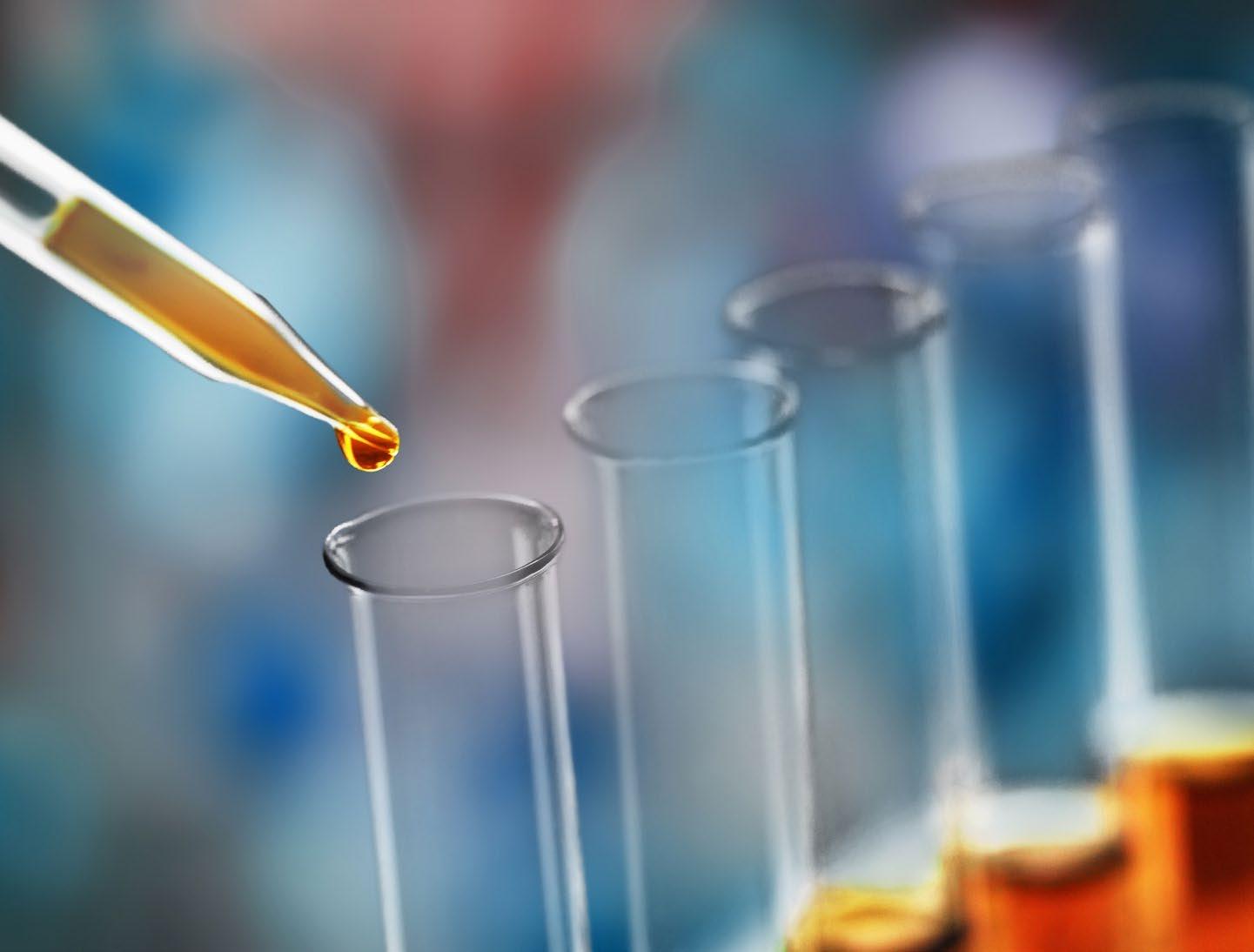
ABS has awarded approval in principle (AIP) for a next-generation, highly efficient concept of a regasification system (Hi-ReGAS+) for floating storage regasification units (FSRUs) and floating liquefied natural gas (LNG) terminals that uses natural circulation.
The technology was developed by Korea Shipbuilding and Offshore Engineering (KSOE), the intermediate holding company of Hyundai Heavy Industries Group, and Hyundai Heavy Industries (HHI) and is a follow-on model to the HiReGAS system from HHI Group.
The stand-out feature is a natural circulation system that utilises the density difference of the fluid in the intermediate heat transfer system that transfers heat from seawater to LNG, creating a highly energy-efficient circulation system and reducing energy consumption to improve reliability.
“FSRUs are in high demand right now and this new regasification system has the potential to reduce operational expenses while increasing the reliability of the unit – a win/win situation for all involved,” saysd Darren Leskoski, ABS vice president of business development.
“LNG will be used as a core energy source in the low-carbon era, and reducing the energy required to use LNG is a core issue for meeting carbon regulations after 2030,” says Sungjoon Kim, senior executive vice president & CTO of Korea Shipbuilding & Offshore Engineering. “Highly efficient systems, such as HiReGAS+, are new systems that meet this global trend.”
The Hyundai Heavy Industries Group built a demonstration facility on a scale of 1/100 of an actual regasification system to verify the performance of the highly energy-efficient regasification system. Based on the experience accumulated through long-term operation of the demonstration facility, improvements were identified and applied to the design. After an analysis by ABS, an AIP for this ship class was obtained.