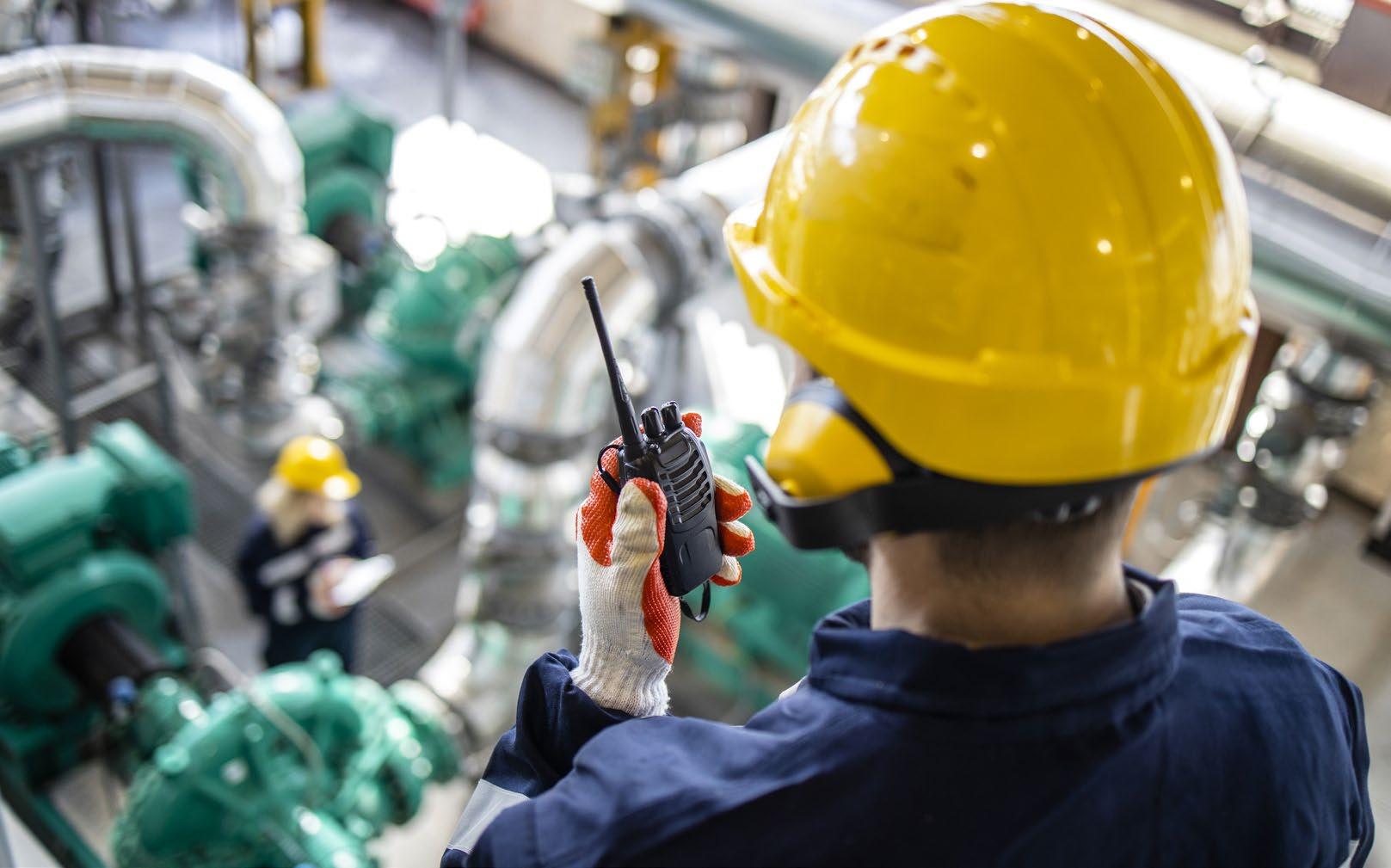
7 minute read
ALTERNATIVE FUELS LNG
from CSI Winter 2022
by Maritime-AMC
Liquefied natural gas is one of the alternative fuel options that is attracting much interest at the moment, with a number of recent developments promoting its use
THE FUEL OF THE FUTURE?
Class society RINA has confirmed that the CO2 reduction achieved by the new Molten Carbonate Fuel Cells (MCFC) technology for carbon capture in shipping, developed by Ecospray, matches expected targets announced by the company at the beginning of the project.
Ecospray chose to use bio-liquefied natural gas (LNG) as fuel for the MCFC technology. The MCFC can be fuelled with hydrogen, methanol, ammonia, fossil LNG, but the use of a CO2 neutral – or negative – fuel represents a plus in the application of this technology, the company believes.
The announcement follows an assessment carried out by RINA, following the signing of a memorandum of understanding (MoU) with Ecospray. The classification society assessed the CO2 life cycle, confirming that a 500kW MCFC, when fed with the carbon negative super bio-LNG (a bio-LNG for which the CO2 is captured during the production process) can cut the CO2 equivalent emissions of a 10MW engine by 20%, as calculated and stated by Ecospray.
The process combines the effect of using a bio-LNG, for which the CO2 has been captured, with the high-efficiency and carbon-negative power-generation capability of the system “
The MoU also includes the assessment of feasibility of the installation of MCFC technologies on ships. Technologies based on MCFC enable the capture of CO2 at the same time as energy production. As such, these technologies are considered strategic in the context of the energy transition, precisely due to their capacity to capture the carbon dioxide in exhaust gases and generate additional clean energy.
According to RINA, this is undoubtedly a technologically complex solution, but it is also the one whichthat guarantees the best results in terms of reductions in emissions, as well as keeping operating expenses low for companies. The ideal application for these technologies is not limited to a particular type of ship: they can be used on all types of engines and with all fuels .
Ecospray plans to start testing MCFC technologies at its laboratory, equipped with engine, DeSOx scrubber and wet electrostatic precipitator, with a launch on the market in expected in 2025.
The 500kW MC fuel cell is very small and compact, meaning its footprint is limited, and has little to no effect on the ship’s layout, the company says.
“Ecospray continues working on several shipping decarbonisation projects, focusing on two main aspects: CC technologies and bio-LNG production. In our view, the bioLNG is already playing an important role in road transportation, but will have an everincreasing role in shipping, beside the LNG,” says Filippo Lossani, marine business unit director of Ecospray.
Giosuè Vezzuto, executive vice president marine at RINA, comments: “The results achieved by Ecospray demonstrate that systems and technologies for achieving the CO2 reduction goals set by regulators are being developed and introduced to the market. The industry is asking for doable and sustainable solutions: we are delighted to confirm that the Ecospray MCFC system may well be a possible option, as it delivers what it promises in terms of emission reduction.”
POWER OF THREE
Classification society Bureau Veritas (BV) has delivered an approval in principle to GTT for a new liquefied natural gas (LNG) carrier based on a three cargo tanks arrangement.
The new LNG carrier design features a total cargo capacity of 174,000m3. In comparison to conventional LNG carriers, this new concept is based on a three cargo tanks arrangement instead of four.
The main ideas that have led to this innovative design are the reduction of boil-off gas (BOG) and the cost optimisations for the ship (both CAPEX and OPEX). The concept is designed to fit either with Mark III or NO96 technologies, developed by GTT. In fact, the effect of an increase in tank length has been specifically investigated by GTT in order to address the specific challenges of this new concept (tank length increased by up to 55%).
To support and better understand the sloshing pressures caused by the liquid motion inside the tank, BV has developed specific tools that can now be leveraged for other large tanks.
Ulrik Dan Frorup, chief commercial director at Bureau Veritas Marine and Offshore, comments: “Collaborating with GTT to develop this innovative design has been truly interesting as it has direct benefits for our clients. Class is here to address risks and opportunities.”
Jean-Baptiste Boutillier, vicepresident of development, innovation, and technical strategy at GTT, says: “We highly appreciate the collaboration with BV to obtain this AiP for a three-tank LNG carrier. Over the years, GTT continues to improve the application of its technologies in order to provide its customers ever more efficient and optimal solutions. We hope to see this concept become the standard in the near future.” CLEAN TECHNOLOGY
Wärtsilä has entered into a joint development agreement with Hycamite TCD Technologies, a privately-owned Finnish company specialising in the development of a pioneering technology for producing clean hydrogen and solid carbon from methane.
The two companies will work together to enable cost-effective production of hydrogen from liquefied natural gas (LNG) onboard marine vessels. The concept design will be ready by mid 2023 and the prototype testing unit will be ready during the second half of 2024.
The concept will allow the existing LNG infrastructure to be utilised and enable production of hydrogen onboard in combination with Wärtsilä’s LNGPac Fuel Gas Supply System. By producing hydrogen onboard and blending it with LNG, the current range of fuel flexible Wärtsilä dual-fuel engines can reduce the vessel’s overall carbon dioxide and methane slip emissions. Alternatively, the hydrogen can also be used in fuel cells onboard.
The by-product from the process is solid carbon that, unlike conventional technologies that produce CO2 as a byproduct, can more easily be stored and managed onboard. The carbon produced consists of high-grade allotropes, like industrial graphite and carbon nanotubes, thereby offering a possible additional revenue stream.
“We are investing in the development of viable future marine fuel technologies and solutions that can accelerate the efforts to decarbonise shipping operations,” says Mathias Jansson, director, fuel gas supply systems at Wärtsilä. “This collaboration with Hycamite is an important step forward towards meeting our corporate targets. Our gas engines can already operate with mixtures of hydrogen and LNG.
“The ability to produce the H2 onboard opens up exciting new opportunities. This solution overcomes the lack of an existing hydrogen supply infrastructure. It also supports reducing the safety risks around storing and handling of liquid hydrogen and enables a gradual decrease of the vessels’ environmental impact.”
“We are delighted to be partnering with an established technology leader such as Wärtsilä. It brings a vast depth of knowledge and experience in marine fuel gas supply systems and, by working together, we can make the availability and onboard storage of hydrogen a realistic option for the marine industry,” says Laura Rahikka, chief executive of Hycamite.
The technology can in principle be applied for all vessels operating with LNG fuel. When using bio-LNG, this solution enables even power generation on board ships with a negative carbon footprint.
FIRST FOR GERMANY
Germany’s first bio-LNG compact plant in Darchau, Lower Saxony, producing CO2-neutral fuel for trucks, was officially opened in August 2022.
Liquid manure will be used to create CO2-neutral biofuel for heavyduty transport. Whereas biogas was previously mostly used to generate electricity, the plant produces liquid bioLNG which can be used to power trucks and buses.
Biofuel from agricultural residues represents a new business model for farmers. “We could do with a lot of small, decentralised bio-LNG plants in Germany right now,” says Kunibert Ruhe, shareholder of RUHE Biogas Service.
“Agricultural businesses can produce biogas self-sufficiently in the form of a circular economy using residual materials from their own farms and from businesses in their region and refine it into bio-LNG.”
Ruhe is one of the pioneers of the biogas plant industry in the country The compact unit in Darchau alone replaces about 1.3m litres of fossil diesel per year and saves up to 7,000 tons of CO2.
“In principle, any agricultural operation can become a bio-LNG production facility. The new liquefaction module can be retrofitted to operators of existing bio-gas plants who are looking for a follow-up concept to the EEG subsidy for the conversion of biogas into electricity,” explains Ruhe. Bio-LNG is therefore attractive to farmers because heavy goods traffic is desperately seeking a climate-friendly alternative. “Only about 30% of farm manure is currently used in conventional biogas plants. If we were to use 100% in the future and process it into bio-LNG, we could supply about 37% of the truck fleet.”