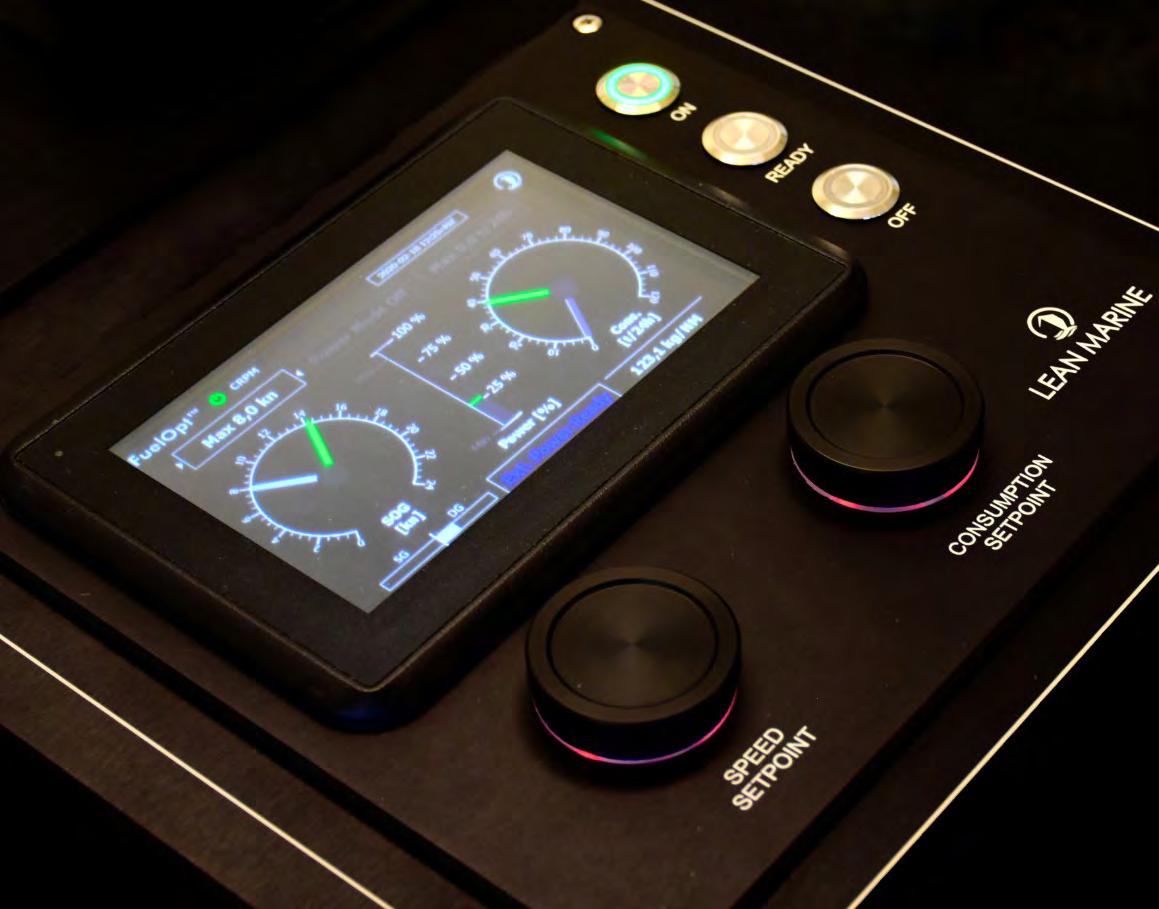
24 minute read
SCRUBBERS
from CSI Spring 2022
by Maritime-AMC
As companies consider the next stage in development past the use of scrubbing technology, Clean Shipping International talks to Stefan Petersson,
of Yara Marine
Technologies about the company’s plans
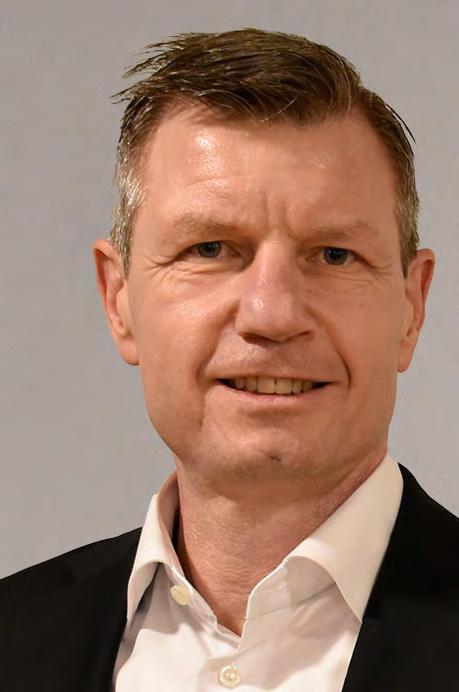
Stefan Petersson COO, Yara Marine Technologies
A FUTURE-PROOF
PORTFOLIO
Q As Yara Marine Technologies’ emphasis shifts from being a scrubber provider to becoming a green technologies enabler, could you tell us more about the evolution of the company and its offering?
A Since day one, Yara Marine Technologies (YMT) has had a green focus and desire to help shipping be more sustainable. Our initial focus was to help operators comply with the IMO 2020 sulphur cap through the use of scrubbers, enabling them to comply with emission restrictions without needing to switch to expensive distillates. Over the past few years, the maritime sector and regulatory bodies have increased the focus on decarbonisation.
However, following the covid-19 pandemic and dovetailed with a weakening oil price, the appetite for scrubbers has weakened. Consequently, this has presented us with the opportunity to re-evaluate our portfolio to meet shifting customer demands.
Our commitment to helping fight climate change made the new path clear: to provide and scale up clean technologies that benefit the shipping industry on its decarbonisation journey. Thus, our mission moved beyond scrubbers to “providing technologies to enable a greener maritime industry”. We are glad to see that maritime sensibilities have matured and stakeholders agree on the need to decarbonise, allowing us to concentrate on getting the best solutions to our customers.
For decarbonisation to be sustainable, we believe that we must keep an open mind to all available options. We have taken this approach with our portfolio, which consists of a mixture of both existing and emerging solutions. Over the past year, we have embraced a wide range of clean technologies, including solutions to automatically reduce consumption of any fuel on a vessel (FuelOpt), collect and analyse fleet-wide data (Fleet Analytics) and eliminate emissions at berth using shore power solutions.
We are also very proud of our partnership with BAR Technologies to develop, produce, and commercialise WindWings – a windassisted propulsion solution.
Q There is still a lot of interest in scrubber solutions in the short term. will Yara Marine continue offering scrubbers going forward? How do you think the scrubber business will evolve in the mid/long term?
A We believe in offering customers the right solution for their needs – and this includes emission abatement technologies such as scrubbers. In fact, we are constantly working on developing and improving both our inline scrubbers (I-type and L-type) and packed bed scrubbers (U-type), with both open- and closed-loop options.
Our new scrubber installations include Yara Marine’s ratio control system that prevents the YMT scrubber system from over-scrubbing and reduces operational costs by up to 60%. This efficiency gain is also possible for previously installed YMT scrubbers through a software upgrade.
While the industry will transition to alternative fuels in the long term, it is unsustainable to replace the existing fleet immediately, and retrofitting vessels to new fuels may not be technically or commercially feasible. This means that there will continue to be a market for vessels using conventional fuels, but these vessels need to comply with emission regulations. For these vessels that continue operating with heavy fuel oil (HFO) or a hybrid of very low sulphur fuel oil (VLSFO) and HFO, SOx scrubbers are a suitable measure to improve their green profile.
Future fuels may also be suitable for scrubbing, so we are exploring all technological paths.
Q As the industry is closely following the fuel price increase, many ship operators are concerned about its financial impact and some are bringing back scrubbers into the discussion. What are your observations on this?
A The price of VLSFO (containing 0.5% sulphur) which is used by a majority of cargo ships is spiking, with news reports of a 55% year-on-year increase at the majority of bunkering ports. This has a huge impact on operating costs, especially in cases where fuel prices are fixed in charter parties and may prompt operators – particularly those who have been affected by the pandemic – to explore using less expensive fuel with higher sulphur content.
However, international regulations on emission levels are clear and noncompliance can have serious financial, operational, and reputational impacts. Scrubbers offer operators using HFO and hybrid fuels the flexibility to use whichever fuel matches their budget without risking vessel detention or onerous fines – and, most importantly, without compromising their commitment to protecting the planet.
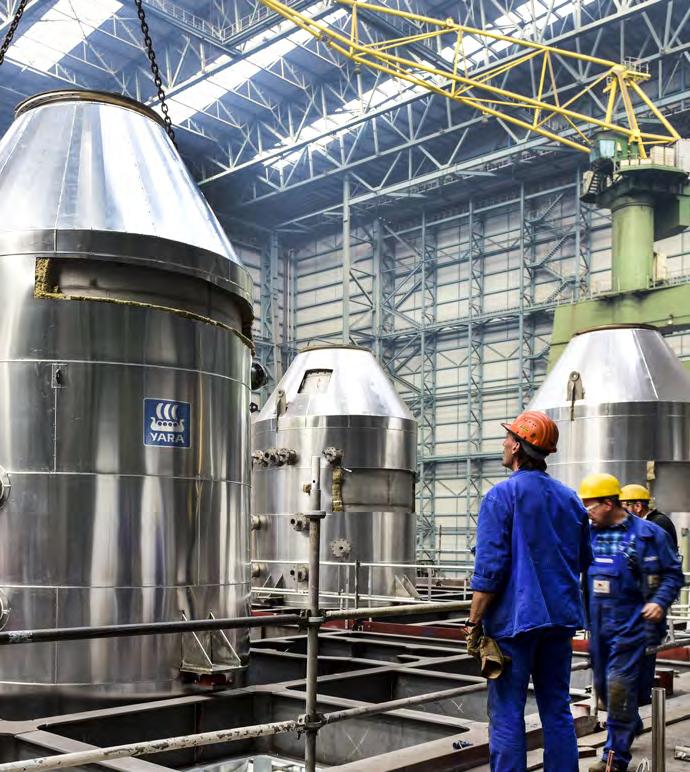
Q Alternative fuel discussions are high up on the shipping’s agenda. Which one do you think has the best chance of gaining the approval of the industry? What are the key challenges?
A Although some fuels, such as liquefied natural gas (LNG), methanol, hydrogen and ammonia, are seeing intensive research and heavy investment by vessel operators, there is no guarantee that the entire industry will settle on a single fuel. There are many factors that will affect the fuel used, such as bunkering infrastructure, funding to retrofit older ships or equip new technologies, government incentives and, of course, increasingly stringent – and ambitious - regulations.
I believe that shipping will use a mix of fuels in the mid- and long-term, with a fuel of choice in certain regions/across major routes. The eventual fuel landscape is dependent on a tipping point in favour of a chosen few fuels – or even one.
Q Considering that the large-scale use of alternative fuels will take time, what would your advice be to shipping companies for the short/mid-term emissions reduction?
A Our most important advice is for operators to act now. There are multiple emission reduction solutions available on the market and every minute and every drop of fuel counts. While some may worry about investing in technology that will become obsolete, we must remember that there is no single magic bullet to make shipping green forever.
Rather, progressively making vessels greener is the ideal way to save the planet and also meet regulatory requirements such as EEXI (Energy Efficiency Existing Ship Index) and CII (Carbon Intensity Indicator), which lay the foundations for continuous improvement of the global fleet.
The business case for going greener is also very apparent for vessel optimisation solutions, as reduced fuel consumption (irrespective of fuel type) limits both emissions and operating expenses. YMT customers using our vessel optimisation solutions – FuelOpt, Fleet Analytics, and Route Pilot AI – have confirmed the financial and operating benefits of closing the loop between the voyage planning, execution and post-voyage analysis stages.
Q Remembering the cold ironing debate for cruise ships and the issue of plugging into shore-side energy supplies, the challenge was that shore-based energy needed to be greener than energy from the ship’s auxiliary engines, which very often was not the case. How is the situation in the industry today? What about the ship-toshore power technologies? Are the other issues such as incompatible systems solved?
A Decarbonisation and sustainability conversations are happening around the globe in various industries. Not only are energy producers increasingly investing in renewables infrastructure, but there is also a greater degree of transparency about how green an energy source really is.
Shipping is one of many industries competing for access to cleaner energy, but I’m glad to say that we are already seeing ports, terminal operators, and shipowners factor energy sources into their decarbonisation equations
Furthermore, national, regional, and local regulatory bodies have already begun planning and implementing strict requirements for shore power, increasing the likelihood of this containing a higher percentage of clean energy in the mix.
Compatibility of systems across various ship types and ports is definitely an issue that must be considered carefully. In many cases, incompatibility is the result of operators combining various thirdparty systems that may not integrate well with each other.
At YMT, we address this by offering turnkey solutions that remove this risk in project-to-installation. Our solutions are particularly cost- and time-efficient for large fleets, where compatibility in systems and equipment is critical to reduce the project management and administrative burden.
Furthermore, our worldwide after-sales and service is also able to manage customer needs (such as spare parts) for the lifetime of the product.
Q Does Yara Marine plan to expand its offering with other clean technologies?
A We believe that an open mind and collaborative approach are the ideal ways to build a greener future for maritime, which is why we are committed to adopting promising new technologies as they emerge. We feel strongly that our industry must be given all the tools it needs to transition to a decarbonised future.
Moreover, we wish to encourage and support the creation of new technologies, which is why we launched our three-month tailored startup accelerator program, Yara Marine X.
The second edition Yara Marine X was launched in December 2021 and is targeted at start-ups focused on clean technologies for the maritime sector. We believe that our program gives newcomers a unique opportunity to gain direct access to our network and resources.
We are also keen to adopt and support existing technologies, which is why we welcome partnership opportunities. After all, working together will benefit everyone, not just from a business viewpoint, but also by helping to secure a greener tomorrow.
GRIMALDI APPROACH
Technology group Wärtsilä, together with the shipping company Grimaldi Group, have unveiled a new system that uses exhaust gas scrubber washwater to tackle the amount of microplastics in the world’s oceans; a critical and growing global environmental challenge.
According to the association Plastic Europe, 368m tonnes of plastic were produced in 2019 worldwide and around 3%, or 11.4m tonnes, of this plastic ultimately ends up in the ocean. To tackle the growing amount of microplastics in the world’s seas, Grimaldi has developed and patented a system that filters out microplastics from open loop scrubber washwater.
Wärtsilä, in partnership with the Neapolitan group, will take the microplastics filtration system – which traps plastic particles before the washwater is returned to the ocean – to market. The capability to filter microplastics will be an integrated feature of Wärtsilä’s future washwater treatment system.
The new system requires very little changes to onboard procedure and uses the natural capabilities of an open loop scrubber to contribute to cleaning the oceans during each voyage. Currently, a 10-megawatt engine will require scrubbers to process approximately 450m3 of water per hour, potentially resulting in a large amount of microplastics being captured from seawater. According to early test results, the microplastics filtration system is efficient in capturing particles smaller than 10µm and the captured concentration by volume equals around 76 particles/m3 .
Adding an abatement solution for microplastics to Wärtsilä’s portfolio further strengthens its commitment to use exhaust gas cleaning systems as a part of a modular platform that can enable further environmental technology innovations.
“Reducing microplastic pollution in our world’s oceans is an important challenge and we are pleased to provide a solution for the shipping industry,” comments Emanuele Grimaldi, managing director of the Grimaldi Group. “The idea for this innovative technology originated from recognising that open loop exhaust gas cleaning systems can draw seawater for exhaust scrubbing and simultaneously collect microplastic present in the oceans as part of their normal operation.
“We have already completed pilot testing of this system onboard one of our vessels deployed between Civitavecchia and Barcelona. The results are promising, with 64,680 microplastic particles collected on a single voyage between these two ports. We are glad that Wärtsilä also recognises the potential of this system, and we look forward to further collaboration to tackle microplastics in our oceans.”
Tamara de Gruyter, president marine systems at Wärtsilä, says: “Microplastics are a pressing environmental challenge and we’re proud to work together with Grimaldi to tackle cleaning up the oceans. Even more importantly, the ability to capture microplastics shows how scrubbers are a platform for solving a wide range of sustainability challenges – and now even ones that are beyond the stack.”
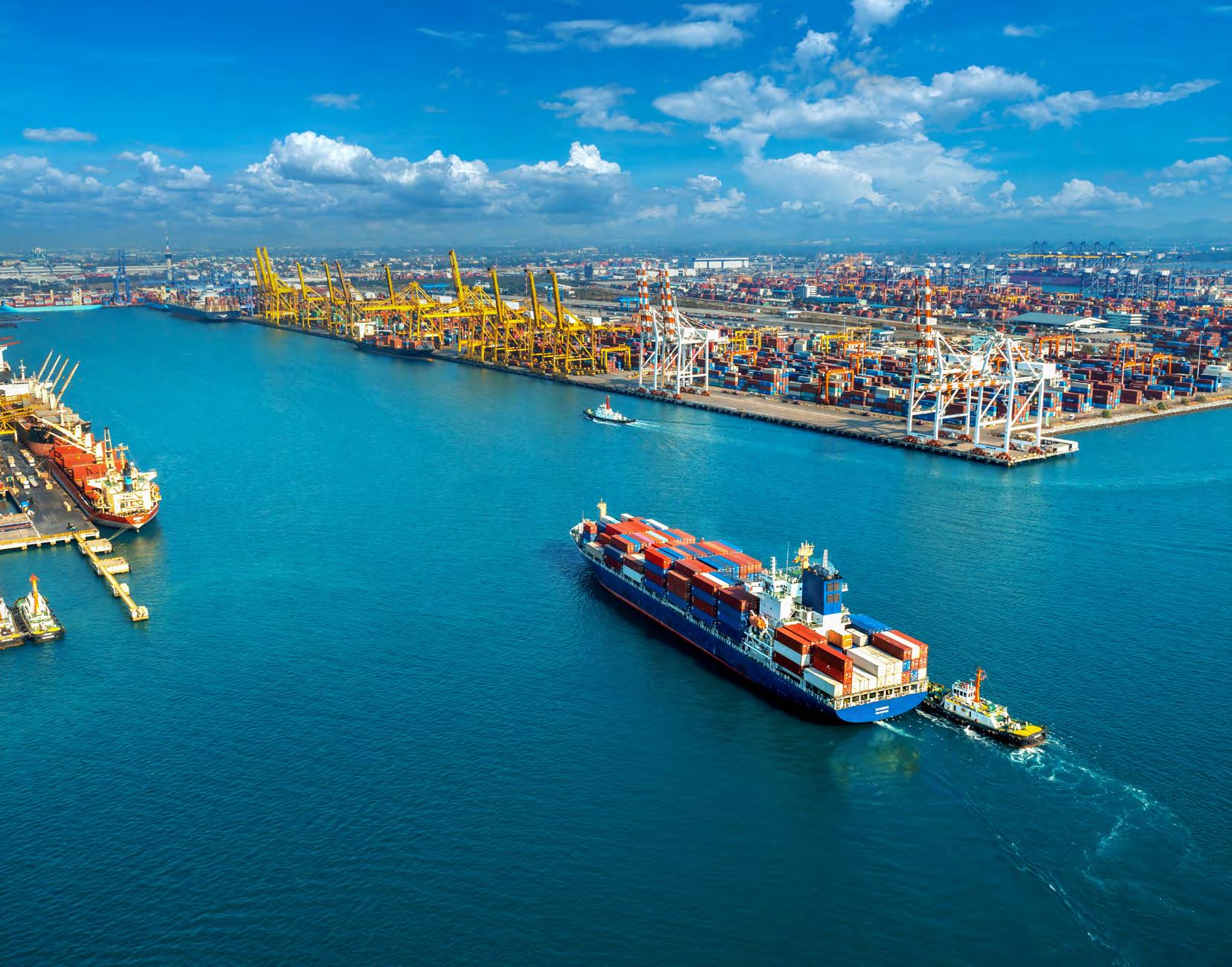
North P&I Club has produced a useful guide to global ports’ approaches to scrubber use, while co-operation between companies is also pushing the environmental agenda
MEETING PORT PROTOCOLS
The use of exhaust gas cleaning systems (EGCSs), or scrubbers, is an accepted equivalent measure in complying with the International Maritime Organization (IMO) 2020 global sulphur cap. However, their use has split the shipping industry, with some preferring to opt for low-sulphur fuel solutions as others go down the scrubber route – at least for the moment.
In the same way, ports have looked at the impact of scrubbers used in their waters and some have indicated that since the new sulphur cap rules were applied they would not accept the use of scrubbers in their waters, most notably the discharge of washwater from scrubbers.
North P&I Club has put together a useful roundup of different ports’ approaches to the issue of scrubbers, outlining some of the ports where the use of scrubbers is banned, or certain conditions need to be applied to use them.
The club has produced a table outlining the different approaches followed by ports as far as the use of scrubbers is concerned. This list includes whether open-loop ECGS discharge is allowed, what regulations have been introduced to control their use and also whether such regulations have been suspended at any point.
In Australia, for example, the club advises that the Australian Maritime Safety Authority (AMSA) is “currently investigating the potential impacts of EGCS washwater discharges on Australian port environments and has commissioned a study to assess the potential cumulative impacts of washwater discharges from open-loop EGCS over time”.
Here, the system must be approved by the ship’s flag state administration or a recognised organisation appointed by the flag state, as well as being operated in accordance with IMO requirements.
The master, owner or operator of a ship using a scrubber system has to notify AMSA before the first arrival of the ship in an Australian port after the system has been installed and approved. Washwater testing needs to be undertaken when the system
is installed and every 12 months thereafter for a minimum of two years.
The club advice also outlines specific approaches taken by individual ports and includes advice by the Clean Shipping Alliance on individual ports and waterways. Use of open loop scrubbers is banned, for example, in the Suez Canal. To view the table, visit nepia.com
SOLSTAD SIGNS UP
As offshore fleets seek to reduce their carbon footprint, Solstad Offshore has signed an agreement with technology group Wärtsilä to collaborate on achieving a 50% reduction in CO2 emissions by 2030.
The agreement aims to identify, evaluate and implement solutions that will increase fuel efficiency and significantly reduce greenhouse gas emissions from Solstad’s offshore vessels. Each vessel will be assessed for appropriate solutions, possible operational improvements and life extension considerations. The company hopes to reach full carbon neutrality by 2050.
“Co-operation is essential if we are to implement the solutions needed to succeed with the green shift that is underway,” says Tor Inge Dale, head of sustainability at Solstad Offshore. “For this reason, we at Solstad are partnering with forward-looking companies such as Wärtsilä that have the expertise, experience and innovative technologies required.”
Solstad has been working on reducing emissions for a number of years and, consequently, average fuel consumption per vessel has been reduced by more than 20%. The further reduction to 50% is expected to be reached by optimising energy efficiencies and by retrofitting the vessels to operate with alternative fuels such as hydrogen, ammonia, and methanol.
Additionally, new ship designs must be capable of offering low or zero emissions from the outset.
Wartsila has also secured a new agreement for its exhaust gas cleaning systems to be installed on two newbuild 218m roll-on/roll-off passenger vessels at Guangzhou Shipyard International in China.
The contract, which was signed in February 2022, will see Wärtsilä fit and commission two 25-megawatt V-SOx hybrid scrubber systems, which can run in both open-and-closed loop configurations, on each vessel.
The order comes as a result of Wärtsilä’s long-term commitment to the Asia-Pacific region, where the organisation has regional resources to enable it to provide sales, support and lifecycle services.
By choosing to install Wärtsilä’s exhaust gas abatement technology, the RoPax vessels will immediately comply with the 0.5% Global Sulphur Cap and will also be futureproofed against impending regulatory change. This is because Wärtsilä’s modular, lifecycle technologies can be upgraded to tackle other pollutants, including Nitrogen Oxide, Particulate Matter and Carbon Dioxide.
Wang Bin, area sales manager at Wärtsilä Exhaust Treatment in China, said: “We are very excited to start 2022 with this order of SOx scrubbers onboard two RoPax vessels being built by our partners at GSI. This agreement not only proves our longterm partnership with GSI, but also demonstrates the commercial and technical viability of scrubbers in shipping’s complex decarbonisation landscape.”
“Our technology completely fulfils technical requirements for newbuilds, ensures compliance with current regulation, and is also the first building block for future sustainability innovation. We look forward to working with GSI on this collaboration and others in our future together.”
Jiang Lei, purchasing manager at GSI, said: “It is a real pleasure for us to be working with Wärtsilä to fulfil this latest order on two RoPax vessels. We recognise the long-term potential of scrubbers for solving many crucial challenges in the shipping industry, and we are proud to carry out installations at our development-oriented shipyard.”
Wärtsilä and GSI will complete the delivery and installation of the four scrubber systems by the end of 2023 for both vessels.
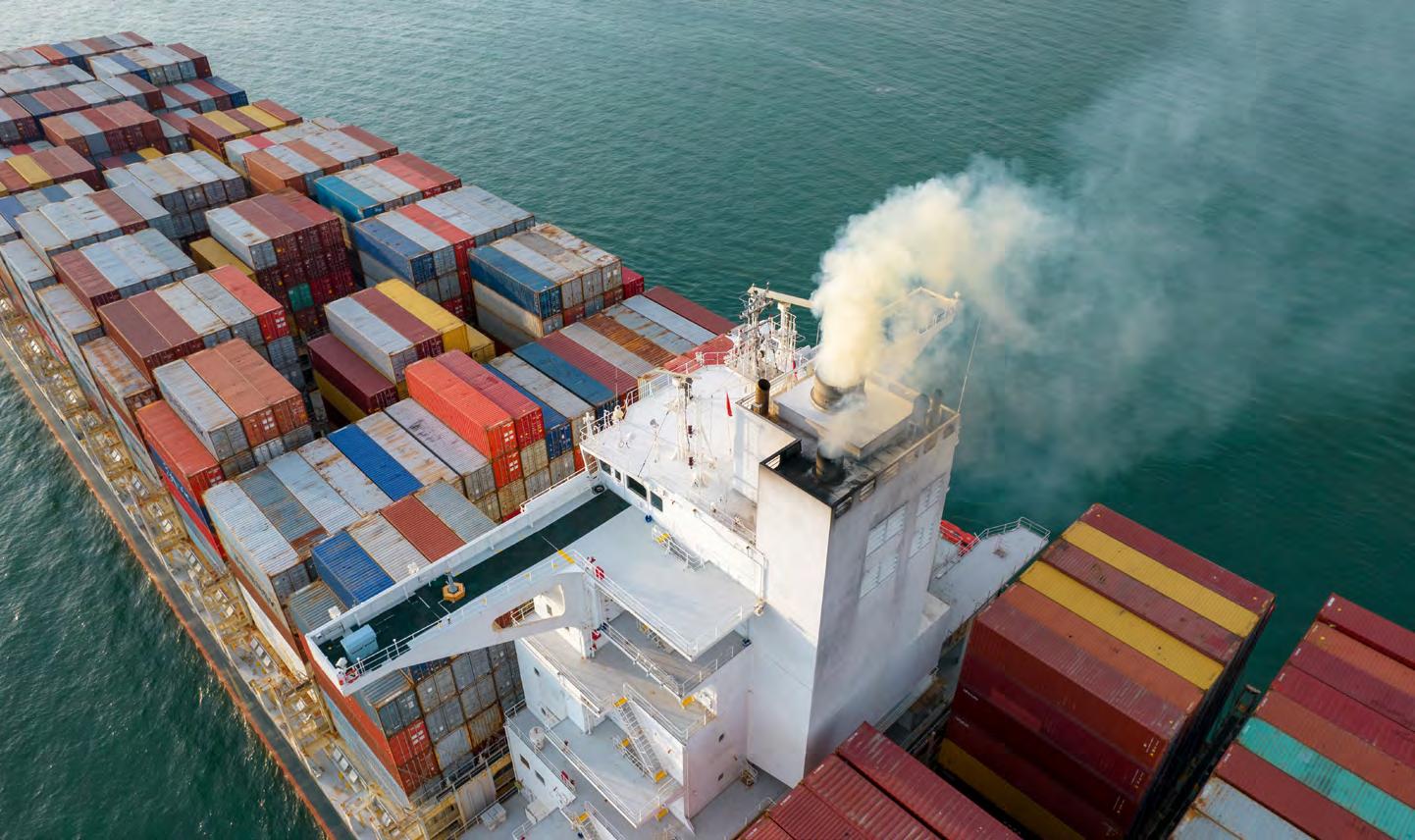
PROTEA: MEETING MONITORING CHALLENGES
This is a demonstration of collaboration between uses and manufacture, enabling state of the art developments to meet the requirements of a critical industrial sector to meet environmental goals.
Protea, among its extensive advanced analyser range manufacture a marine in-situ continuous emission analyser. The analyser, designated the P2000, is a variant of an analyser previously manufactured by Procal Kittiwake.
This unique approach to monitoring exhaust emissions is an ideal solution for the marine industry to enable compliance with International Maritime Organization (IMO) regulations. The P2000 in-situ analyser is fitted directly to the exhaust with the gas monitored within the exhaust duct.
Unlike extractive systems, the in-situ technique does not require sample preparation components. Extractive monitoring systems require the sample to be transported to an analyser cabinet employing pumps, filters, heated lines and other sample conditioning components, all of which necessitate inclusion in a maintenance regime.
The P2000 analyser is certified by several classification societies as an analyser system suitable to monitor sulphur dioxide (SO2) and carbon dioxide (CO2) and report the SO2:CO2 ratio.
The P2000 was developed from a successful land-based analyser and was first installed on early exhaust gas cleaning systems (EGCS) in 2010. Since then, several hundred P2000 have been installed on several classes of vessels, both on scrubbed and unscrubbed applications.
The installed base of in-situ analysers are photometers using the absorption of selected infrared wavelengths to determine the concentrations of both CO2 and SO2.
The analyser is zero based, therefore every 12 hours the system automatically switches in instrument air, which forces out the exhaust gas from the probe enabling the analyser to verify zero. In the same way, manually or automatically certified test gas can be introduced, allowing a span check (see image, below right).
Protea took over the manufacture of the Kittiwake Procal analyser range, including the successful P2000 used in both land-based and marine applications.
FINDING SOLUTIONS
In the process of evaluating the performance of the installed base, it was determined that the P2000 was an ideal solution for the majority of landbased applications.
However, for marine installations it was decided that the instrument would benefit from a series of product improvements. Working with existing users and marine industry specialists, three main areas were identified that would benefit from improvements.
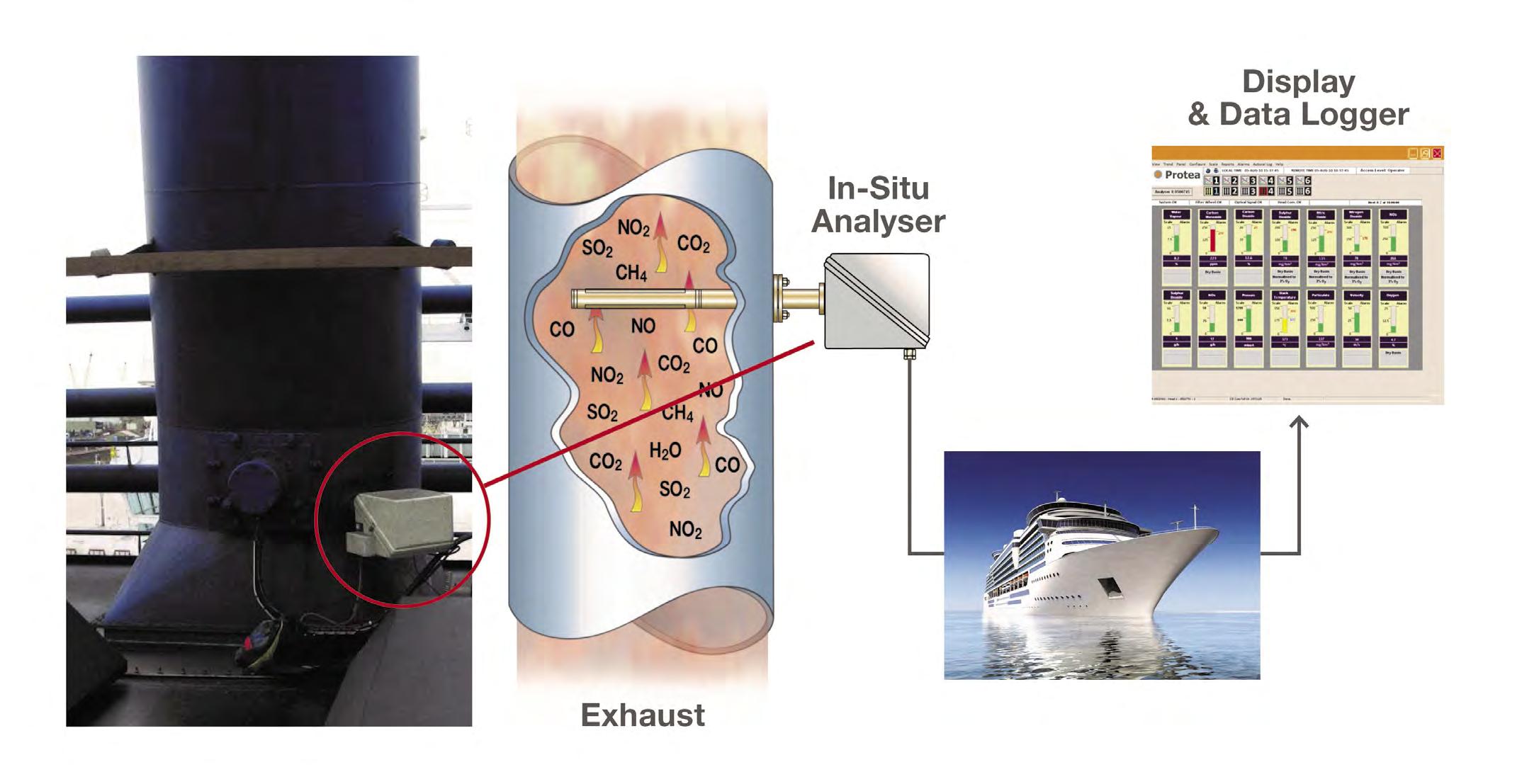
These were: 1. Capability of monitoring lower levels of SO2 in a background of relatively high water vapour. 2. Capability of monitoring postscrubber with liquid phase water vapour carry over. 3. Enhanced support to enable vessel engineers to identify and rectify performance issues.
Taking each point in turn, the solutions to the identified improvements were as follows: 1. The P2000 is an infra-red analyser, monitors SO2 in a region of infrared where there is interference from water vapour in many marine applications involving monitoring post-wet scrubber, and inevitably the water vapour is high and variable. CO2 is monitored in a part of the infra-red spectrum unaffected by water vapour.
As part of the maintenance procedure for the existing installed base of P2000, the visiting service engineer is required to verify that the analyser monitored concentration are unaffected by water vapour. To achieve this the engineer is required to use a sophisticated water vapour generator, which inevitably adds time and expense to a routine service visit.
Protea’s solution: develop a highbred UV/IR analyser to monitor the SO2 using ultra violet (UV), which is unaffected by water vapour. CO2 cannot be monitored in the UV and therefore is still monitored in the infra-red. 2. The analyser probe is mounted within the duct and therefore subject to the emission flow, which if mounted post-scrubber in certain designs of EGCS liquid water droplets were present. This caused the probe to be “chilled”, resulting in condensation forming and errors in the monitored concentrations.
Protea’s solution: design an enhanced analyser probe with a thermal barrier, which increases the probe temperature thus ensuring any liquid water is vaporised before coming in contact with the system insitu optics. 3. Protea’s solution: develop an integrated software application that automatically runs a routine that collects data under all the phases of operation these include zero (instrument air), certified test gas and process.
The data is collected in a file, which is then e-mailed to Protea support for analysis, findings including any remedial actions are then reported back to the vessels chief engineer. This approach has been invaluable during the current pandemic, which has enable Protea to support installed systems remotely.
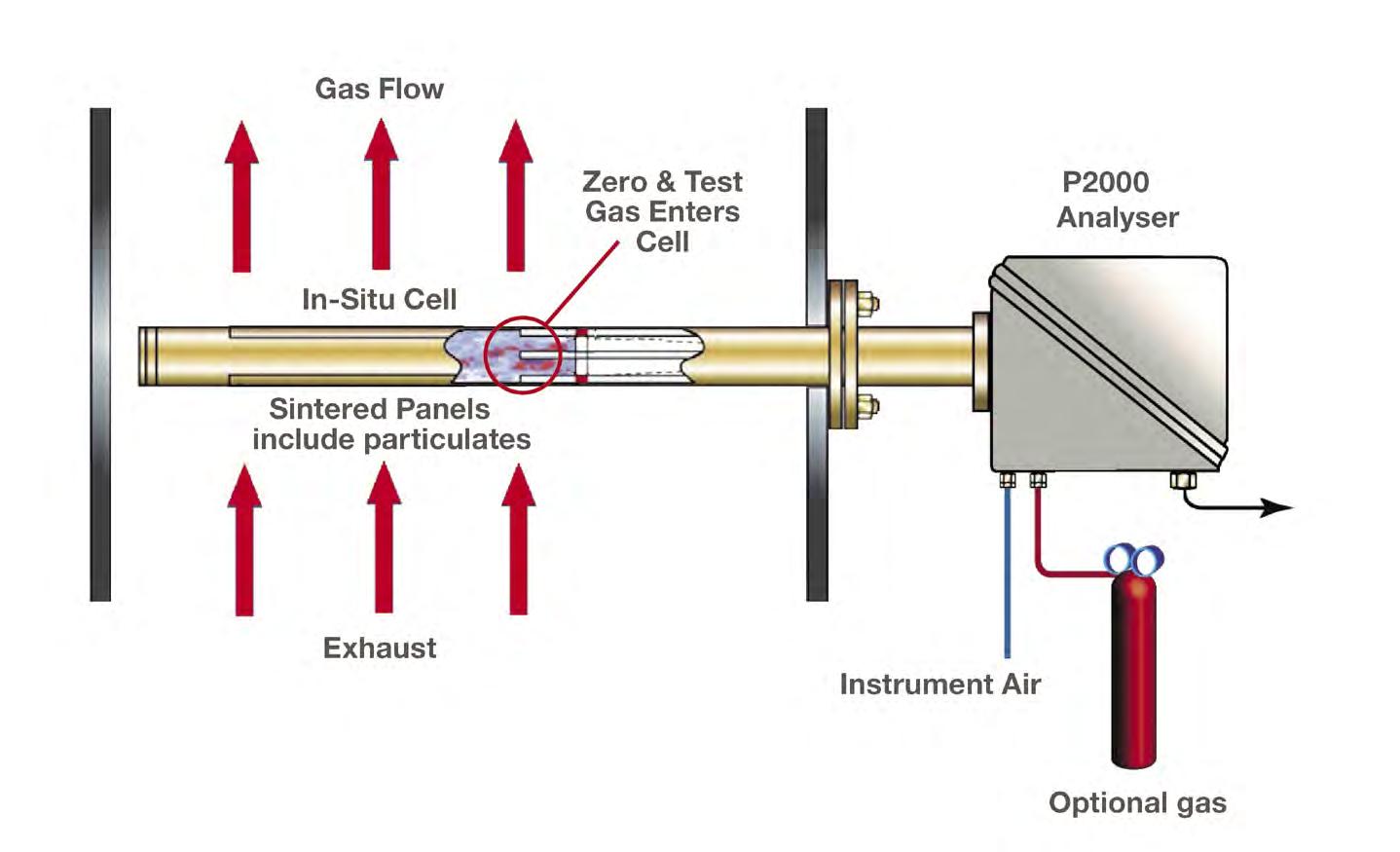
ENHANCED SUPPORT
In addition to acquiring the Procal Kittiwake products, Protea has also taken over the support of the installed base of marine installations. Protea is the only organisation able to support the Procal Kittiwake P2000 installed instruments with marine clarification society certified spares.
Protea has also entered into contracts to update existing installations to the latest standard with the current uses of the P2000 analysers. This includes system software upgrades, enabling the operator to take advantage of the remote diagnostic capability of Protea’s customer support team.
In addition, Protea operates an extensive worldwide network of factory trained sales and service partners strategically located to support the marine industry.
Protea would like to invite all users of the Parker Kittiwake Procal P2000 to contact us regarding ongoing support and the cost-effective upgrade of their current exhaust emission monitoring analysers.
Protea would also like to thank and recognise the input from our valued marine engineers for their undoubted expertise in improving our products for installation in challenging applications.

For more information, visit: protea.ltd.uk
CYGNUS: SUSTAINING A RENEWABLE WORLD
Even green technology falls victim to corrosion. As we strive to increase our use of renewable technologies, we are yet to free ourselves from the clutches of this issue, particularly at sea. Although the use of scrubber systems and wind turbines is booming, both are susceptible to corrosion.
BEST PROTECTION
Water ingress into a ship’s engine room is just one example of the type of catastrophic incident that can occur when corrosion has compromised a scrubber’s structural integrity. Aggravated by the high temperatures of exhaust gases, acidic, corrosive washwater causes extremely severe corrosion. As a result, classification societies such as DNV-GL require wall thickness measurements for the SOx scrubber overboard distance piece in annual class surveys.
Early, preventative maintenance provides the best protection against costly repairs, focusing on the overboard pipe and its surrounding area, including the external hull. For this, many companies worldwide choose Cygnus – a recognised brand for 40 years in the marine industry, renowned for its extremely reliable and easy-to-use ultrasonic testing equipment!
Cygnus 1 Intrinsically Safe gauge is the only one of its kind in the world certified to Class 1, Div 1 (“Zone 0”) for ATEX, IECEx and CSA-US, offering safe operations in hazardous, potentially explosive atmospheres. It is particularly crucial when working on vessels transporting flammable cargoes. This heavy-duty device is water-resistant to IP65 and uses the Cygnus-pioneered multipleecho technique.
Cygnus’ multiple-echo technique, specified by class societies, reads through coatings, negating the need to remove the expensive protective coatings or epoxy that safeguard
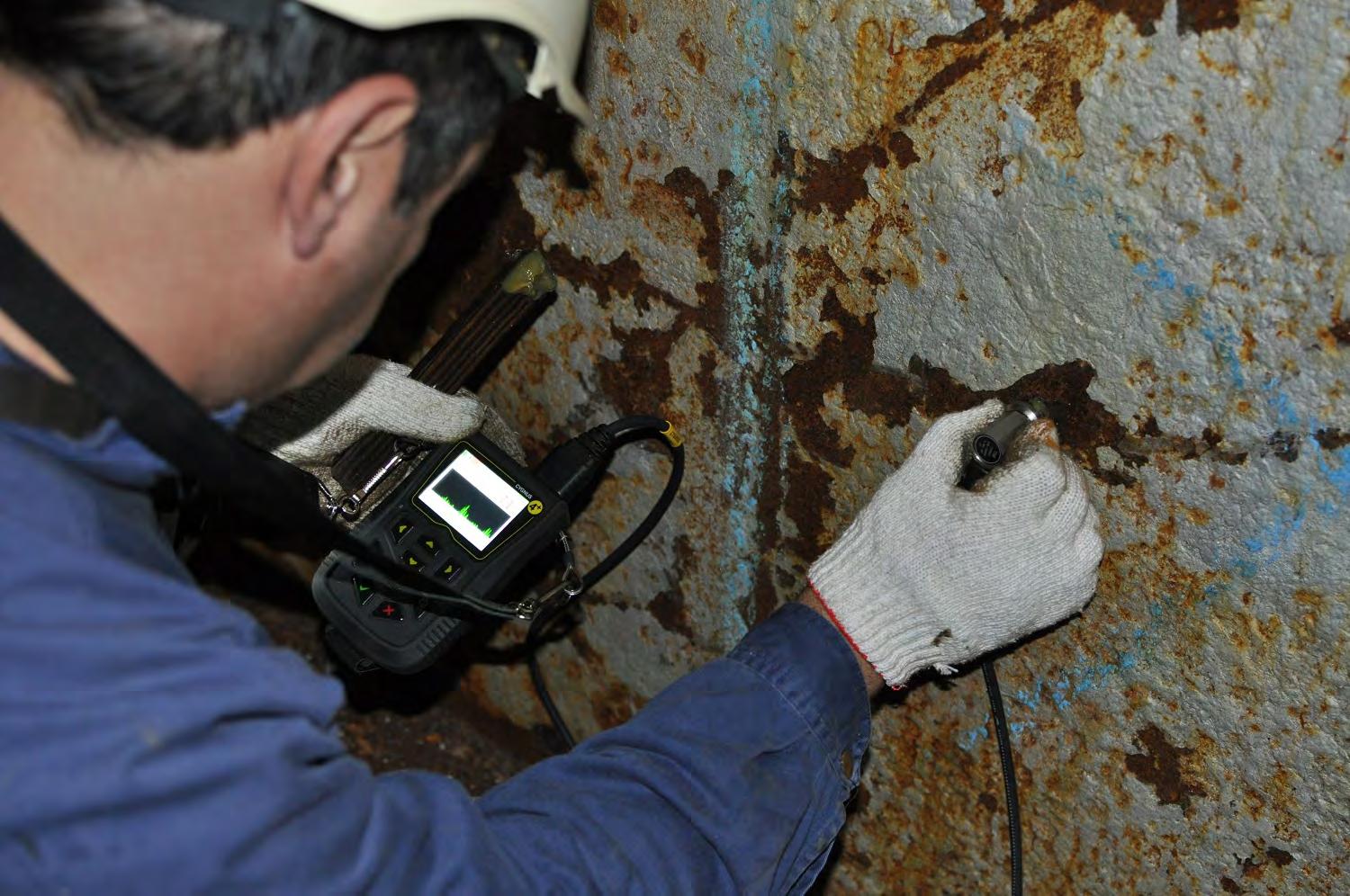
against external scrubber corrosion. For heavily corroded metals with thin or missing coating, Cygnus Plus gauges offer echo-echo and singleecho measuring modes, along with its Measurement Stability Indicator (MSI™) for quick, reliable readings.
Cygnus 4+ thickness gauge is a fantastic little all-rounder. Small but rugged, this wrist-wearable gauge features an A-scan display, datalogging and auto log for hassle-free recording, post-reporting and analysis, making wall-thinning and corrosion easy to monitor over time and helping to address issues early.
COASTAL CORROSION
Whether offshore or onshore, corrosion is known as one of the primary mechanisms degrading the structural integrity and shortening the lifespan of wind turbines. It reduces the thickness of the structure, sometimes at an alarming rate, encouraging cracks and buckling that can be irreparable.
Most turbines are situated in coastal areas, where harsh winds, rain, salty air and frost rust and erode the leading-edge blade tip, an imbalance that can undermine the shaft and gearbox.
Those offshore also battle against the sea, different sections of the turbine suffering different challenges.
While UV radiation and humidity above the surface and the growth of micro-organisms below are damaging, the most vulnerable of these sections is the “splash zone” (where the turbine meets the water’s surface). Constant abrasive wave action, intensified by the seawater’s temperature, chlorinity and salinity, is the perfect recipe for extreme corrosion.
So how significant is the impact on the wind power industry? Soaring demand has increased pressure to minimise turbine downtime, before considering the loss of revenue and productivity, and high emergency repair rates, which result in a severely costly ordeal. The by-products of corrosion are costly to the environment, too.
As always, prevention is key. Ultrasonic thickness gauging is a simple, inexpensive and reliable method for regular maintenance surveys. Cygnus gauges work quickly and efficiently with easy-to-use functionality – a critical solution to the vicious cycle of extensive checklists that are essential to the safety of wind turbines, time-constrained, highpressure schedules, and specialist engineers who are in short supply and high demand.
Working at great heights and in tight spaces comes with the territory of turbine maintenance. Cygnus MK5 surface range offers lightweight, compact and highly portable equipment that is shatter-proof and waterresistant (IP67) if dropped. The option of twin-crystal and right-angle probes allow more flexibility for tight, awkward spaces.
Cygnus’ multiple-echo technique and Measurement Stability Indicator (MSI™) confirm accurate measurements, eliminating hesitancy and precious time between measurements. Although coatings are widely used on turbines to ensure an adequate lifespan, inspection is still recommended considering potential coating failures and defects. Cygnus gauges can measure metal thickness without the need to remove anti-corrosive coatings, saving time and money.
Cygnus 4+ and 6+ Pro Ultrasonic Thickness Gauges are the most advanced models of Cygnus’ surface corrosion gauges, both ideal for this application.
The highly intuitive Cygnus 6+ boasts an array of excellent features, including three versatile measuring modes, live A-scan and B-scan displays, and the radial points function for further investigation on heavily corroded areas. The A-Scan display allows users to visually verify the back-wall echo signals and adjust the gain manually where necessary.
What’s more, the 6+ has a comprehensive data-logging feature that records your measurements for hassle-free reporting and post-analysis.

For more information, contact: Tel: +44 (0) 1305 265533 Email: sales@cygnus-instruments.com cygnus-instruments.com