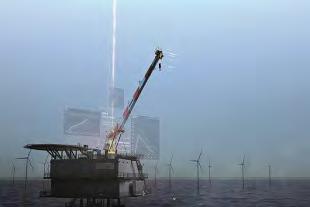
7 minute read
german equipment
from BTI Spring 2022
by Maritime-AMC
FUTURE-PROOF SOLUTIONS
German companies have revealed a number of initiatives to save time, reduce emissions and cut costs in port operations
Thyssenkrupp, Holcim and TU Berlin have begun a research product on CO2 reduction, which aims to reduce emissions at cement plants using carbon capture by means of a new amine scrubbing process.
The cement industry is working on reducing CO2 emissions in a number of ways. Even with the sole use of renewable energies, the raw materials used in cement production result in CO2 being released and emitted to the atmosphere. Thyssenkrupp Uhde, Holcim and the Technische Universität Berlin have therefore partnered up in a joint project to investigate the use of a novel amine scrubbing technology for carbon capture.
The goal is to significantly reduce CO2 emissions from existing cement plants and at the same time utilise the captured CO2 for other applications. In concrete terms, this includes the development of new mass transfer process equipment that is more efficient and resilient to contaminations. The project is being funded by the German Federal Ministry for Economic Affairs and Climate Action. Ralph Kleinschmidt, head of technology, innovation and sustainability at Thyssenkrupp Uhde, says: “Amine scrubbing is already commonly used to recover CO2 from process gases or exhaust gases. Now, we are developing the technology further and optimising it for the cement industry. Additional applications for capturing CO2 direct at source, such as in waste incineration plants, are also possible.
Arne Stecher, head of decarbonisation at Holcim Germany adds: “Carbon capture will be a must for cement plants in the near future. That is why we are testing different processes to find the best carbon capture technology. Carbon capture by means of amine scrubbing is a promising solution. I am pleased that, together with our partners, we can test the use of this innovative process in the cement industry.”
Jens-Uwe Repke, chairman of process dynamics and operations at TU Berlin, says: “Developing innovative carbon capture technology for gas treating and improving the efficiency, environmental compatibility, and sustainability of existing carbon capture processes, as well as putting them into practice, is an urgent and crucial task that makes a direct contribution to climate praotection. These goals can only be achieved if industry cooperates closely with research facilities such as universities.”
The performance and efficiency of this equipment is being tested using real exhaust gas at the cement plant located in Beckum, Germany. This is paving the way for commercial use. Various possibilities for using the captured CO2 are also being examined, for example methanol or sustainable fuels.
With this process, the partners are seeking to make a contribution to the reduction of greenhouse gases, especially in existing cement production plants. These can then be retrofitted with equipment for capturing CO2 from the process gas without further adapting the production process.
Changing maintenance
LiMain – Liebherr Intelligent Maintenance – is Liebherr’s answer to the market demand for next generation maintenance
According to the company, LiMain paves the way for an even higher crane availability at lower operational costs (OPEX) on offshore platforms.
The fully digital, semiautomatic, and remote maintenance system offers more independency of time, place and resources for platform owners, resulting in never-beforeseen savings.
A KEY ELEMENT OF LIMAIN IS ITS MODULAR SYSTEM ARCHITECTURE WITH FOUR DIFFERENT MODULES TO CHOOSE FROM
Accelerated by the global pandemic, there is a growing desire among platform operators for new approaches to regular maintenance.
Previously, maintenance processes for offshore platform equipment were time-consuming, costly and also required the use of many resources, further adding to the costs.
Additionally, platform owners face many obstacles that are difficult to manage, such as availability of personnel, weather conditions and need for professional expertise.
To solve the tension between increased crane availability at lower OPEX in combination with a higher degree of independence from these conditions, Liebherr has launched LiMain, which performs maintenance processes without having to operate the crane on site.
According to the company the achievable savings are outstanding: LiMain offers up to 75% less mobilisation on unmanned platforms and up to 50 fewer service days on manned platforms per year
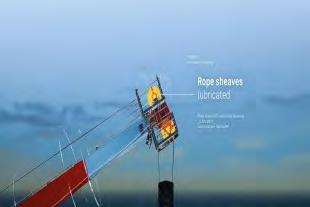
EVEN IN COMPLEXLY INSTALLED POSITIONS, CRITICAL COMPONENTS ARE CONTINUOUSLY CHECKED AND AUTOMATICALLY LUBRICATED
“We commit ourselves to shape the future of maintenance for our customers. LiMain will change the way they think about maintenance”, says global application manager Stefan Schneider. “The result of our commitment is an intelligent maintenance system, which solves challenges that platform operators have grappled with all around the world for years.”
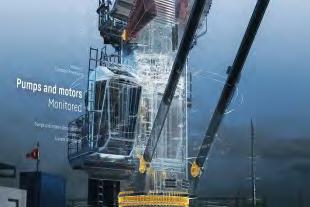
STATE-OF-THE-ART SENSOR TECHNOLOGY RECORDS DETAILED DATA ABOUT RELEVANT COMPONENTS AND CRANE SYSTEMS, INCLUDING POTENTIAL ENVIRONMENTAL MONITORING
A key element of LiMain is its modular system architecture, which consists of four different modules: automatic greasing, condition monitoring, predictive maintenance and remote maintenance cycle.
Automatic greasing means that core components of the crane are continuously checked and automatically lubricated, while the other modules set a new standard on different levels of maintenance.
With modern sensor technology as a part of the condition monitoring module, detailed data about the crane and its components are monitored in real time, which delivers an unprecedented level of transparency.
With predictive maintenance, Liebherr puts ad-hoc data into context, building on decades of experience from the construction of more than 1,000 offshore cranes and sharing this knowledge with the customers.
The remote maintenance cycle represents the all-inclusive-approach, which combines all LiMain modules and enables semiautomatic maintenance as well as self-diagnosis of the crane.
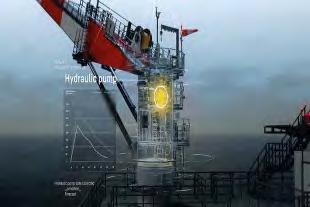
ADVANCED SENSOR TECHNOLOGY AND MANY YEARS OF EXPERIENCE ARE BUNDLED TO ADVANCE MAINTENANCE IN THE MOST EFFICIENT WAY POSSIBLE
According to Gregor Levold, sales director offshore for ship and port cranes: “Due to the modular architecture, our customers have the freedom to choose how automated their processes should be, meeting the specific needs of each client. In the near future, LiMain will also be available for further products in our Liebherr maritime crane portfolio.”

THE COMBINATION OF ALL LIMAIN MODULES ENABLES SEMIAUTOMATIC MAINTENANCE OF THE CRANE
Besides the usual maintenance processes, LiMain also has a positive effect on general logistics. The ability to pinpoint the optimal time to exchange spare parts eliminates unnecessary service intervals and results in more storage space for other equipment – keeping costs down and availability high.
Cranes head to lagos
Tincan Island Container Terminal Limited (TICT) has ordered two eco-efficient Konecranes Gottwald ESP.8 Mobile Harbor Cranes for their operations in Lagos, Nigeria. Booked at the end of 2021, for delivery in June this year it is the first order of a Generation 6 crane for Africa.
The cranes will be operated by TICT in the Port of Lagos, where they will handle containers alongside a large fleet of Model 4, Model 6 and Model 7 Konecranes Gottwald mobile harbour cranes already on site.
TICT is a consortium made up of Bolloré Ports and a Chinese partnership formed by China Merchants Holding International and China Africa Development Fund.
“The cranes will provide improved handling capacity to meet the demands of the steadily growing business. We look forward to the additional features the Generation 6 will bring, such as the possibility of electric operation in the future”, says Etienne Rocher, managing director of TICT.
The cranes on order are Konecranes Gottwald ESP.8 Mobile Harbor Cranes, with a working radius of 54 m and a capacity of 150 t. The natural successor to the Generation 5 cranes already on-site, they feature strong lifting capacity curves for improved performance and a higher classification, which effectively doubles their service life in container handling operations.
The cranes have a customised propping base adapted to local conditions, as well as a tower extension to reach higher container stacks and a better view of the vessel for improved precision and safety.
Built-in readiness for an external power supply will make conversion to electric operation easy when resources allow.
“This order shows the strength of our long-term partnership with TICT. With a total of 12 Konecranes Gottwald Mobile Harbor Cranes in its fleet, as well as RTGs and reach stackers from Konecranes, TICT will have the terminal capacity and flexibility to handle containers from almost any kind of vessel,” says Andreas Czwalinna, regional sales manager for Konecranes Port Solutions.
