
16 minute read
Vessels & Marine Technologies of the Future
from Wavelength #78
Technical Vessels & Marine Technologies of the Future
By Yannis Vakkas
Advertisement
If you are a car-lover, you certainly know of the Geneva International Motor Show, where the latest automotive technologies and most innovative cars are presented. Being a ship-lover, I started writing these lines in the hope that it would be possible to present a summary of future technologies that will be applied in Shipping so that we can gain an insight into how what the “Vessel of the Future” will look like. However, after several hours in front of my laptop trying to write the article, I can admit that this was a futile effort. The conclusion was that due to the number of innovative technologies and the complexity of the Maritime sector, it would be necessary to have several Wavelength issues dedicated only to this subject in order to have a more informative view on forthcoming technologies. Although having a pure technical “Wavelength” edition dedicated to shipbuilding and “Green” technologies might look perfect and very interesting for the writer, it should be acknowledged that the Editor (and maybe others) might raise objections. Therefore, we request your contribution in order to address the items which the readers consider most interesting. In this respect, please review the infographic below that indicates some of the future technologies and visit the online questionnaire created in order for you to choose from each category which of the new technologies you would like to be analyzed in detail for the next issue of Wavelength.
The questionnaire is divided into five (5) parts, covering the following sections, with each section having various technologies for the reader’s selection. Below you may find a list of technologies with a short description for each one.
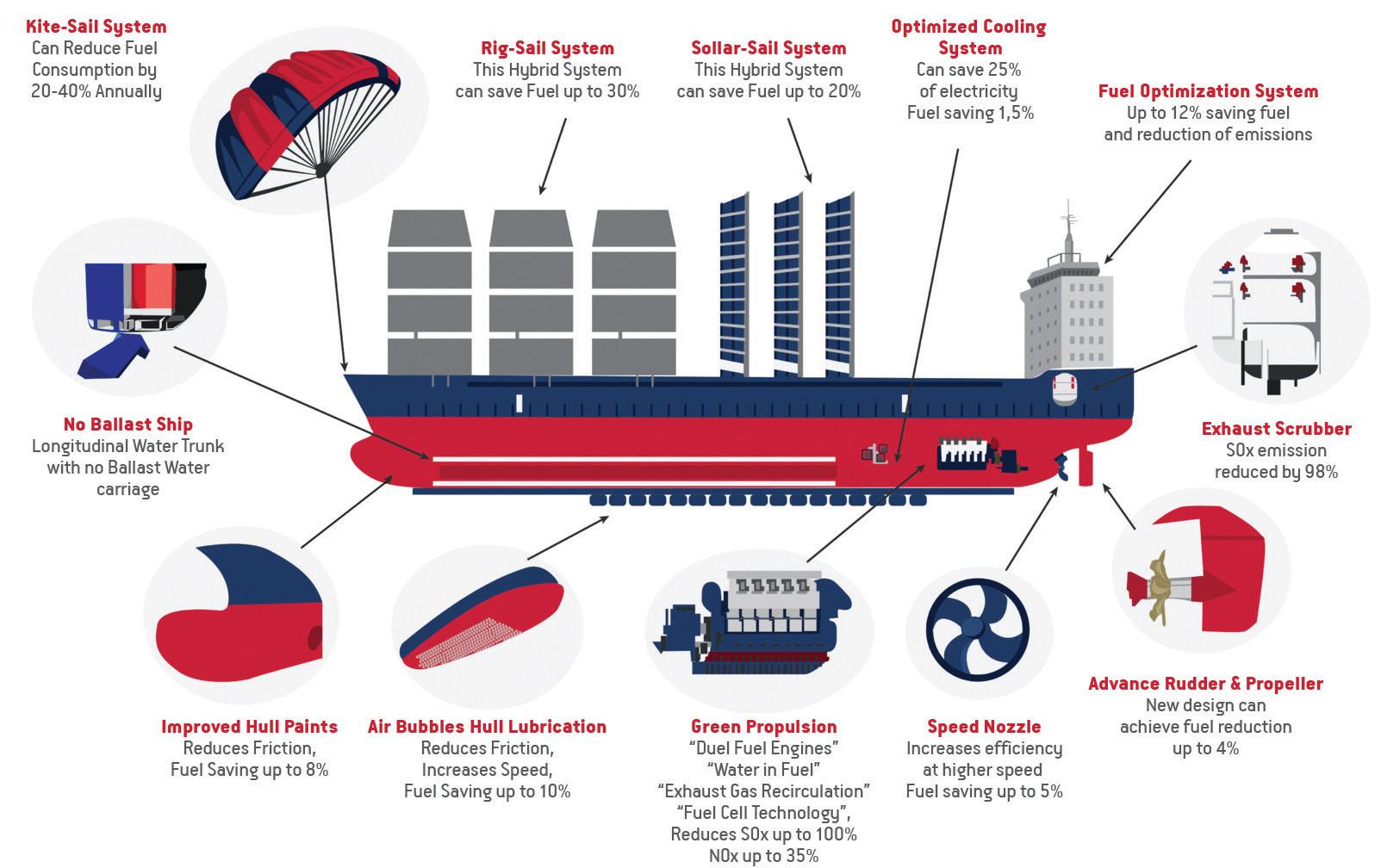
a. Engine derating and tuning This technology refers to the reduction of an engine's output and consequently, the reduction of the total fuel consumption by improving the match between the operational speed and optimization speed.
Machinery Technologies:
b. Speed control pumps and fans
Engine Room ventilation fans and Sea water pumps are being controlled with a Variable Frequency Drive (VFD) in order to meet the normal onboard operational condition, which is usually far below the extreme designed ones, thereby achieving increased energy savings.
c. Variable speed electric power generation
Variable speed power generation can provide significant fuel savings with diesel electric propulsion when the operational profile of the vessel has a lot of variation in speed and power demand. This concept enables optimization of the total fuel consumption of a vessel by adjusting the rotational speed of the main engines and the system’s frequency to vary within the specified range.
d. Hybrid shaft generator
The Hybrid Shaft Generator (HSG) uses Active Front End (AFE) technology, so fixed engine rpm is not required. The switchboard sees a constant voltage and frequency, and the correct phase angle to match the other generator sets running in parallel.
e. Waste Heat recovery
Waste heat recovery systems recover the thermal energy from the exhaust gas and convert it into electrical energy, while the residual heat can further be used for ship services (such as steam and hot water). The system can consist of an exhaust gas/oil fired boiler, a power turbine and/or a steam turbine with an alternator.
f. High efficiency Boilers and Purifiers
High efficiency Boilers come with the Energy Management System, which reduces fuel use by prioritizing heat distribution according to the needs of connected consumers. Furthermore, new hybrid boiler constructions are under development. New types of purifiers combine the low sludge output, high efficiency and low operating costs.
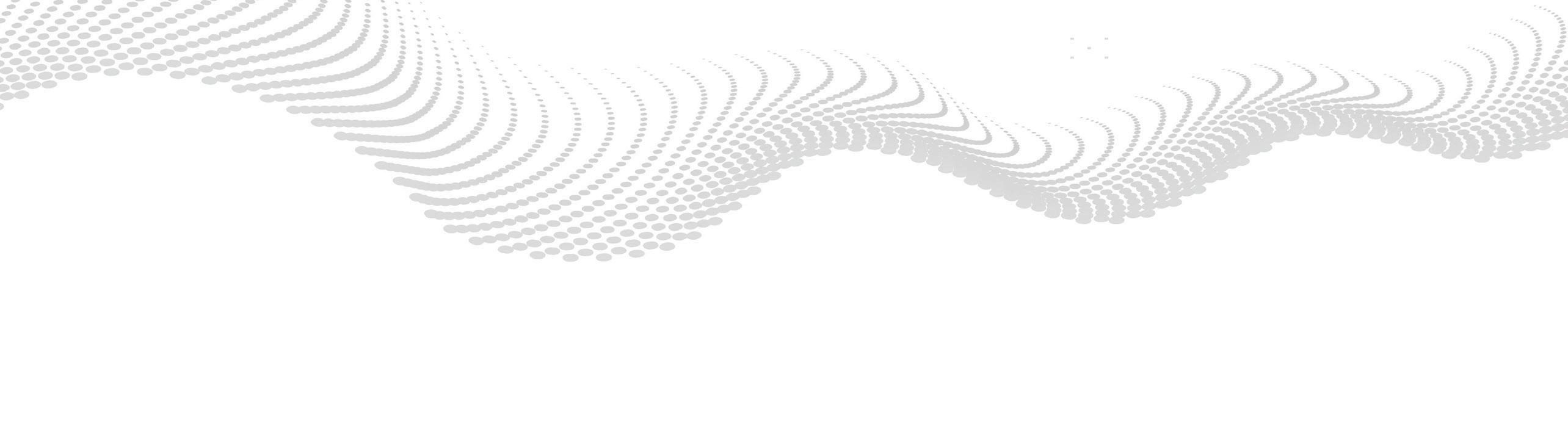
a. NOx treatment (Selective Catalytic Reduction & Exhaust Gas Recirculation)
The following technologies are available to meet the IMO Tier III NOx limits: • Selective Catalytic Reduction (SCR) by installing an SCR reactor. In the reactor, NOx is reduced catalytically by ammonia (as urea) to nitrogen and water. According to the reactor’s position, there are two types of
SCR systems: a. High Pressure/HP, with the reactor installed before the turbocharger and b. Low Pressure/LP, with the reactor installed after the turbocharger. • Exhaust Gas Recirculation is applied by recirculating a proportion of the exhaust gas from the Main Engine exhaust receiver to the scavenge air via a dedicated closed loop scrubber, which removes contaminants (PM, sulphur oxides etc.)
b. SOx Scrubbers
SOx scrubbers are installed in order to clean exhaust gases and reduce SOx emissions. Three (3) types are commonly available: open loop, closed loop and hybrid type. The principle is the same for all types. When exhaust gas enters the system, it is sprayed with water. The SOx reacts with water to form sulphuric acid.
c. Dual fuel engines
Dual-fuel engines are the diesel 2- or 4-stroke engines that can run on both gaseous and liquid fuels, including cleaner fuels like natural gas, LNG, methanol, LPG and ammonia, plus a wide range of biofuels.
d. New turbocharging technologies
Engine Various turbocharging technologies
Efficiency & have been developed over the last decades. Emissions after New type T/Cs are of the compact type with high turbocharging effi-
Treatment ciency resulting in reduced exhaust emissions and lower fuel consumption for the M/E. Also on the market there are hybrid turbochargers, which are optimized for waste energy recovery and fuel saving. Exhaust gas energy is recovered to turn the compressor, which supplies scavenge air to the Main Engine and also generates electricity through an alternator incorporated in the turbocharger.

Alternative Energy Sources and Fuels
a. Solar power: Solar panels are devices that convert light from the sun into electricity. Recent advances in solar cell and photovoltaic (PV) module technologies have led to solar power becoming a cost effective fuel reduction option for smaller vessels such as pleasure boats, ferries, etc. However, on large ships the amount of fuel saved through the use of solar power alone is relatively small. So, the idea of a commercially viable solar ship seems impractical at the moment. b. Wind power: Rotor sails are the evolution of rigid sails installed back in the 80s due to the oil crisis in the 70s. Rotor sails are comprised of vertical cylinders which, when driven to rotate, harness the renewable power of the wind to propel ships. The principle of operation for these highly efficient mechanical sails is based on the aerodynamic phenomenon known as the Magnus Effect, which provides additional thrust to vessels and delivers significant fuel and emission savings. c. Batteries: Fully electric ships represent a leap forward in power system design, but at present they are only feasible in limited applications such as short-sea shipping. However, the introduction of batteries enables a selection of smaller engine sizes that can operate for a longer time under optimal loads due to the additional power provided from the batteries when required (peak loads). Furthermore, for vessels with electric cranes and other electrical cargo equipment, batteries can present significant advantages. Alternatively, in operating conditions requiring low loads, the vessel may be able to operate on battery power alone, thereby reducing engine running hours, fuel and maintenance costs. d. Fuel cells: Fuel cells offer high electrical efficiency, as well as lower noise and vibration than conventional engines. The primary parts of a fuel cell power system are the fuel cells themselves, which convert the chemical energy stored in the fuel directly into electrical and thermal energy by electrochemical oxidation. There are various fuel cell technologies under development. The three (3) most promising fuel cell technologies for maritime use are the high-temperature proton exchange membrane fuel cell (HT-PEMFC), low-temperature proton exchange membrane fuel cell (LT-PEMFC), and solid oxide fuel cell (SOFC). e. Biofuels: Biofuels are produced from biomass (primary or residues) that are converted into liquid or gaseous fuels. A wide variety of procedures exist for the production of conventional (first-generation) and advanced (second and thirdgeneration) biofuels.The most promising biofuels for ships are LBG (liquid biogas, which primarily consists of methane) and biodiesel (e.g. HVO – hydrotreated vegetable oil, BTL – biomass-to-liquids, FAME – fatty acid methyl ester). SVO (straight vegetable oil) is the most appropriate replacement for HSFO, while Biodiesel may replace MDO/MGO and LBG may replace fossil LNG.
f. LNG / Ethanol / Methanol / Ammonia:
Liquefied natural gas (LNG) has as a main component methane (CH4) and it is considered as an “intermediate/transitional” fuel in view of IMO’s decarbonization strategy. Ethane, Methanol and LPG have already been implemented widely in new engines, and these fuels will be sufficient to reach IMO’s decarbonization goals for 2030 and 2050 in combination with efficiency improvements and vessel speed reductions. A very promising zero-carbon hydrogen based fuel for the future market is Ammonia and major engine builders plan to develop engines by 2024 based on this fuel. Hydrogen is also considered an alternative fuel. However, just recently the major engine builder MAN-ES announced that they do not plan to develop an engine operating on Hydrogen and will concentrate on developing engines operating on ammonia.
g. Water in oil:
When applying Fuel-Water-Emulsion (FWE), freshwater is mixed with the fuel on board the vessel before the mixture is injected into the engine’s combustion chamber. The water evaporation in direct proximity to the injected fuel causes local cooling of the combustion in the cylinder, thus lowering NOx formation. Research results have shown that each percentage point of water that is mixed with the fuel reduces NOx emissions at approximately the same rate. On the other hand, the stability of the emulsion is still under investigation.
Operations/Maintenance
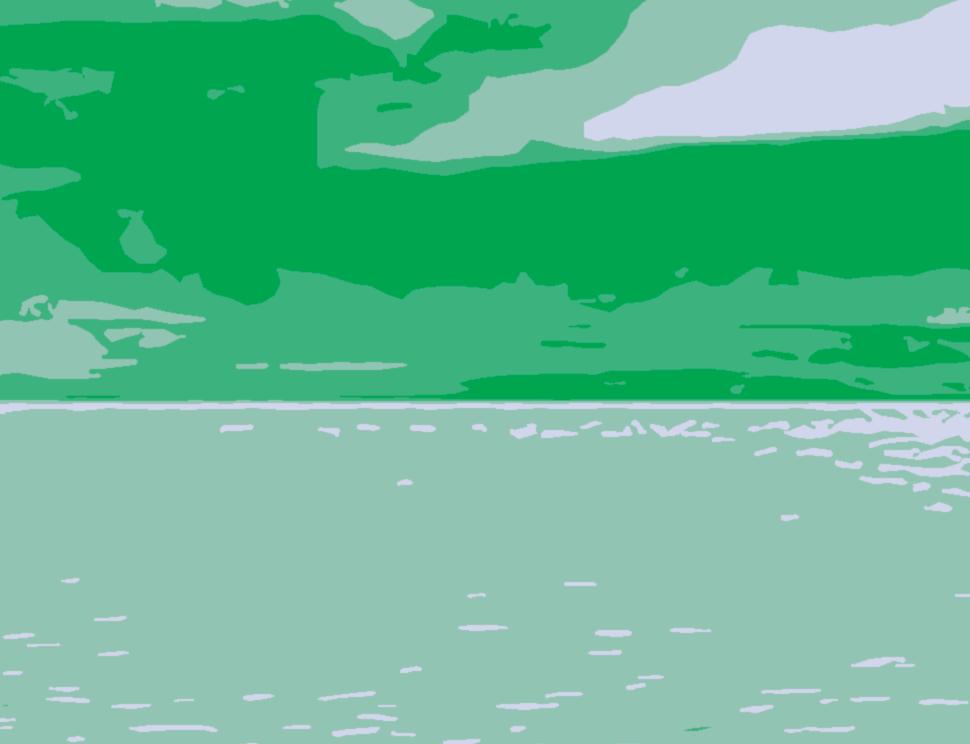
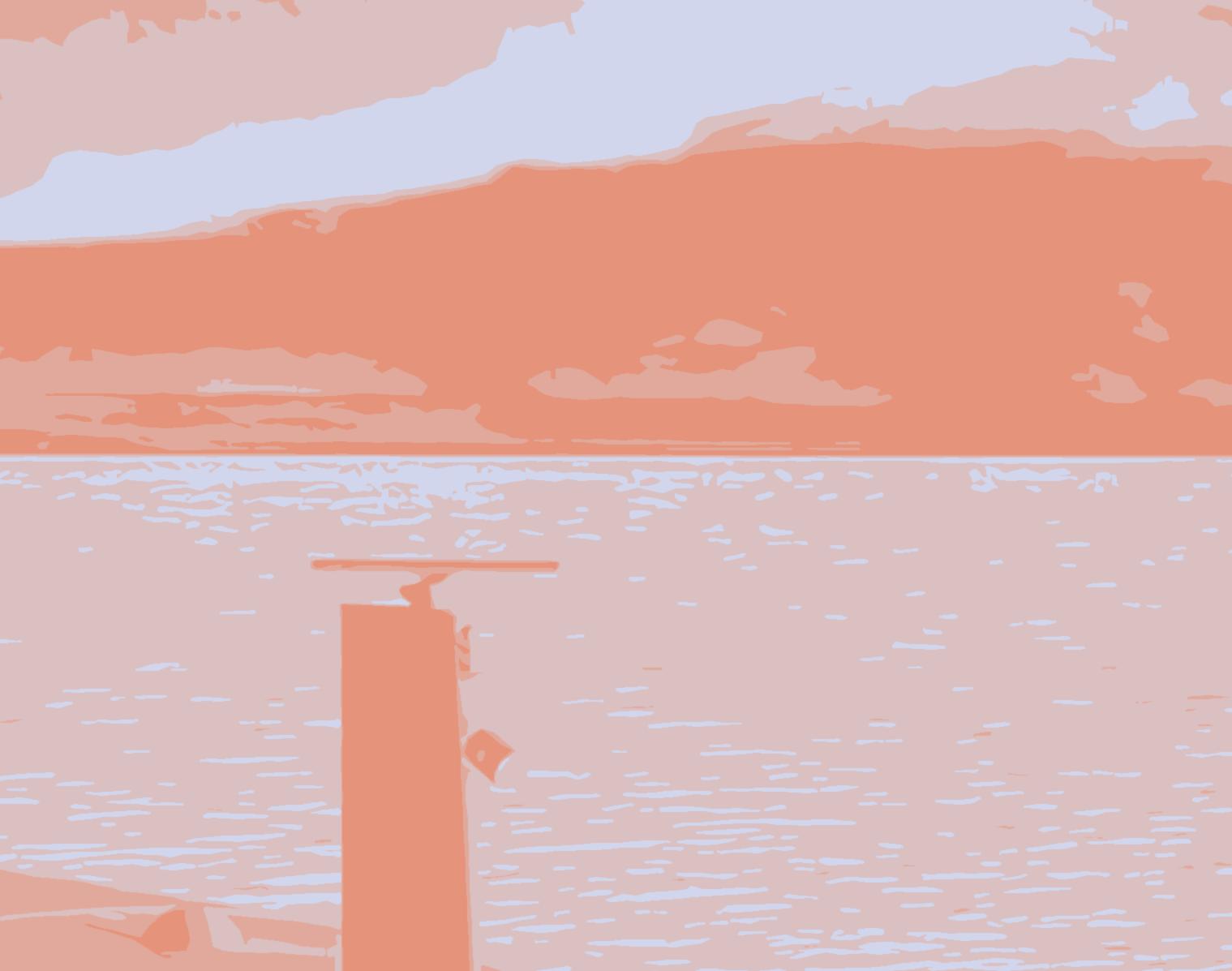
a. Autonomous / Remotely operated Ships
This field is a wide one, with many different automation applications and concepts that could benefit the maritime industry. These range from completely unmanned ships, to vessels that are remotecontrolled from land-based virtual Bridges, to support systems and sensors that warn the crew before a collision or help to optimize navigation and operations. Despite the fact that this is an exciting technology, various voices of concern are being heard in connection with regulatory, cybersecurity and safety issues.
b. Smart Ship
SmartShip, a project funded by the European Union with various partners, intends to offer a multi-layer optimization in the fields of energy efficiency, emissions control management and fuel consumption with full respect to the implementation of the requirements of the maritime sector. SmartShip will take advantage of available technologies and will deliver a holistic cloud-based maritime performance and monitoring system, for the entire ship’s lifecycle, aimed at optimizing emissions reduction, energy efficiency and fuel consumption for an environmental friendly shipping operation in full compliance with maritime standards and regulations.
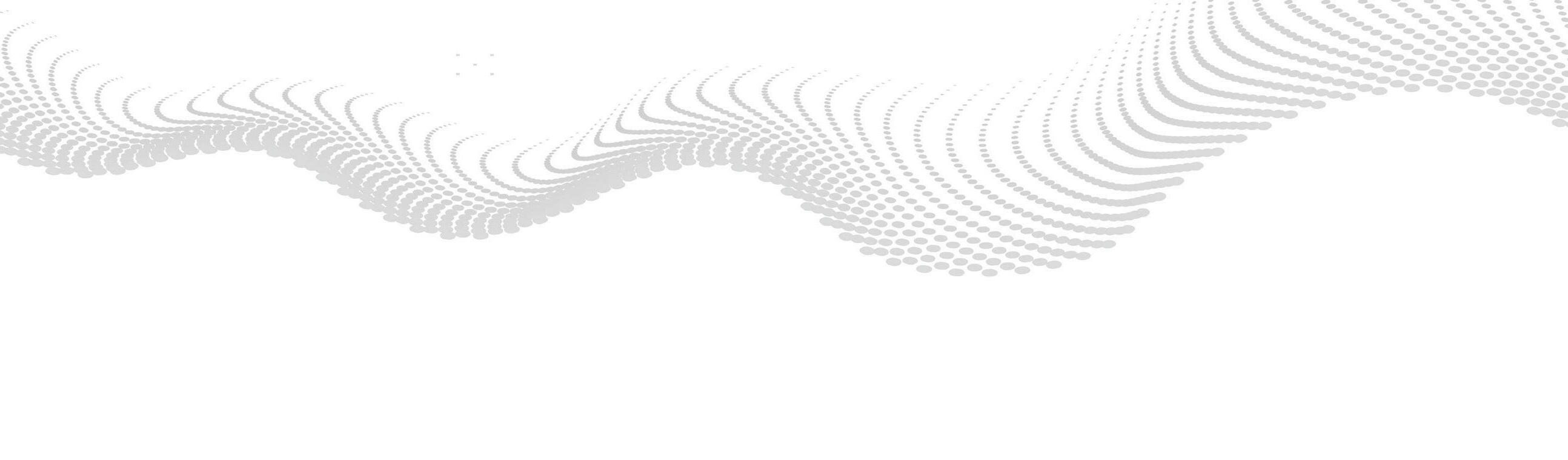
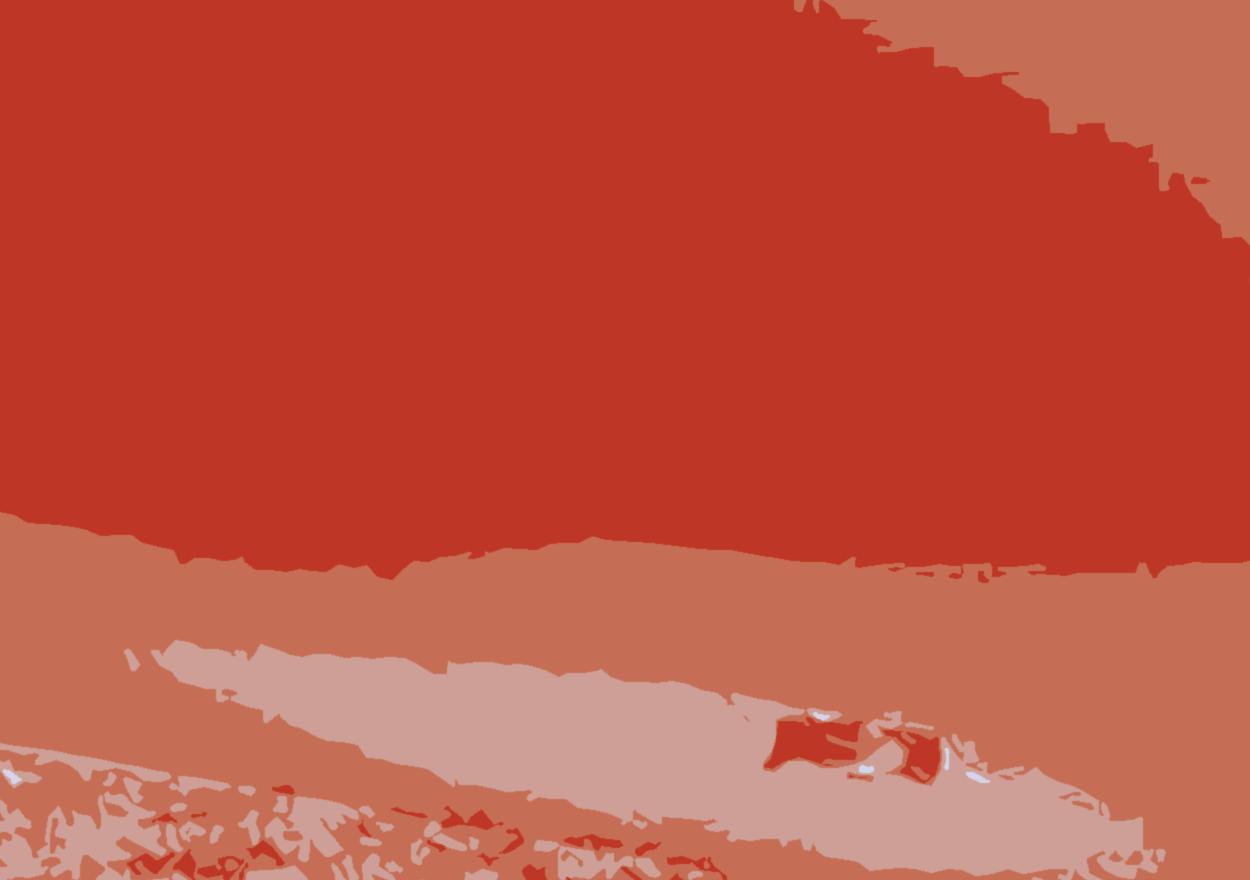
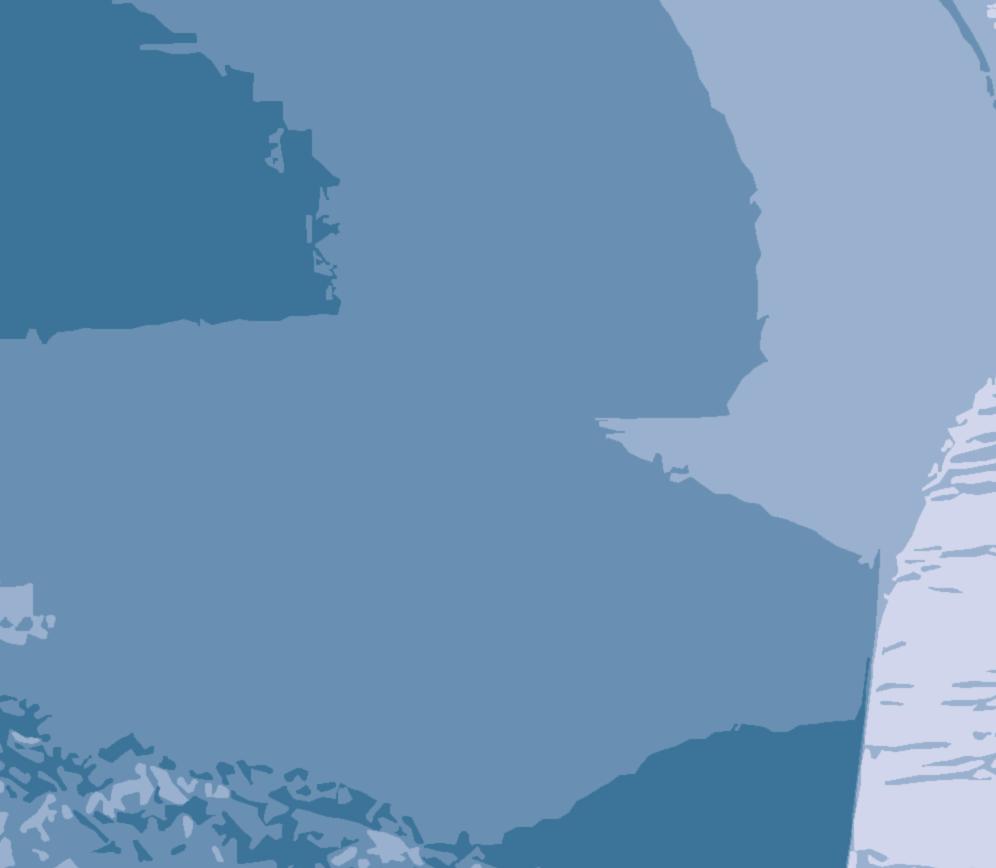

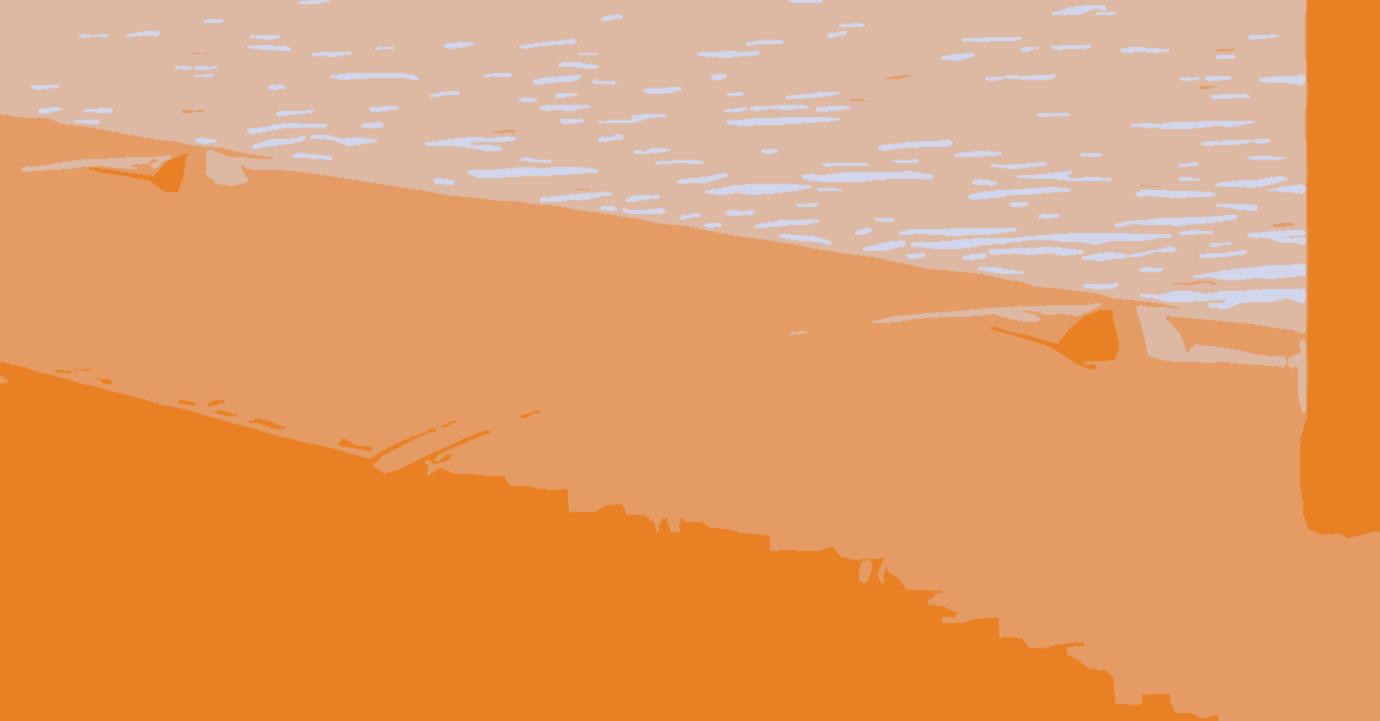
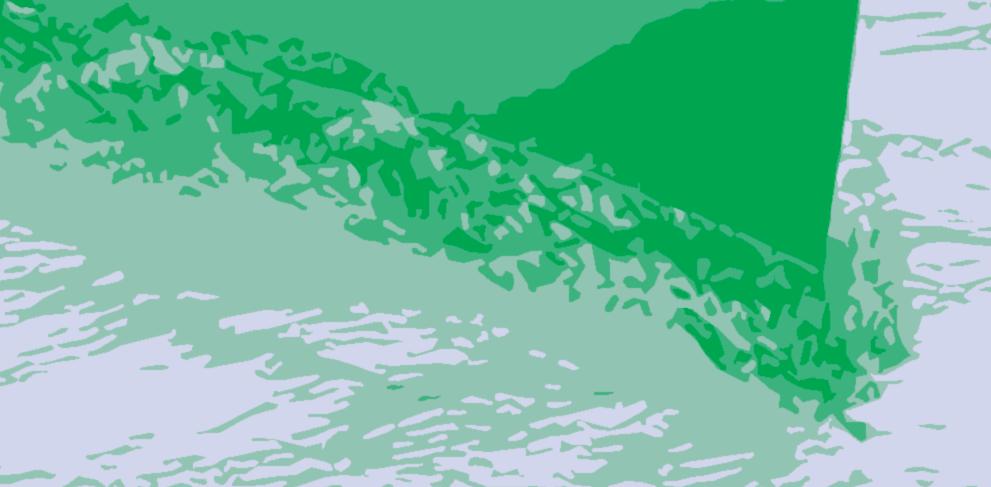
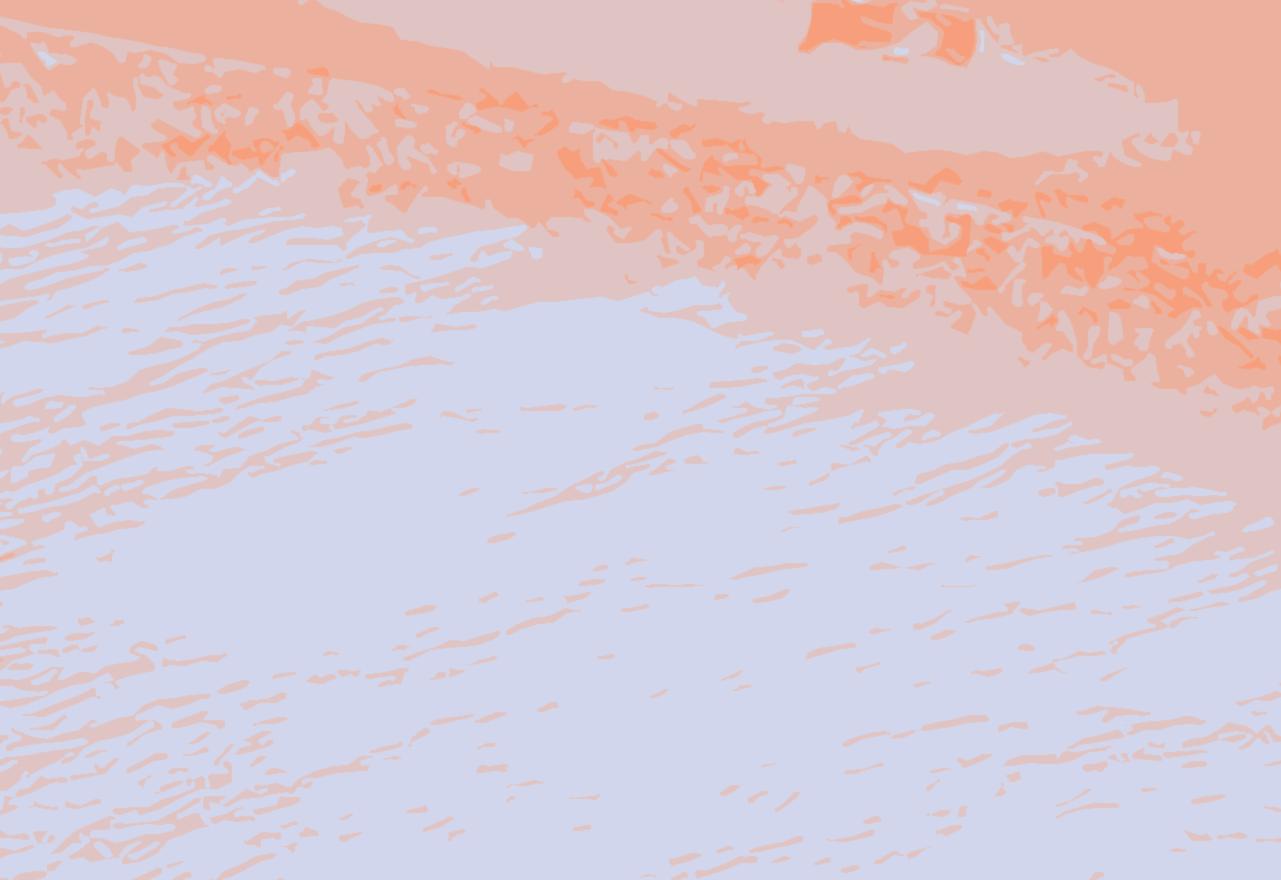
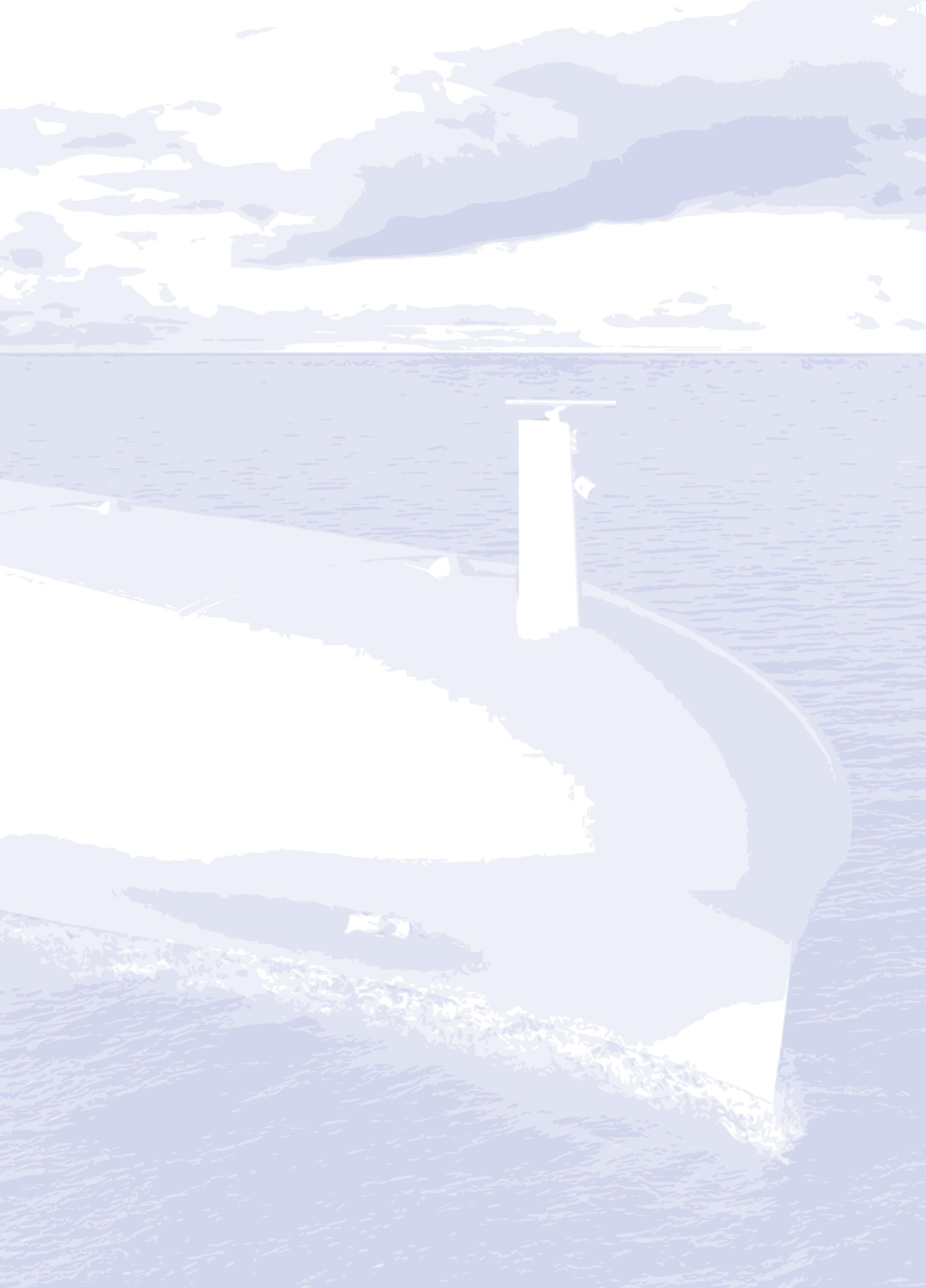
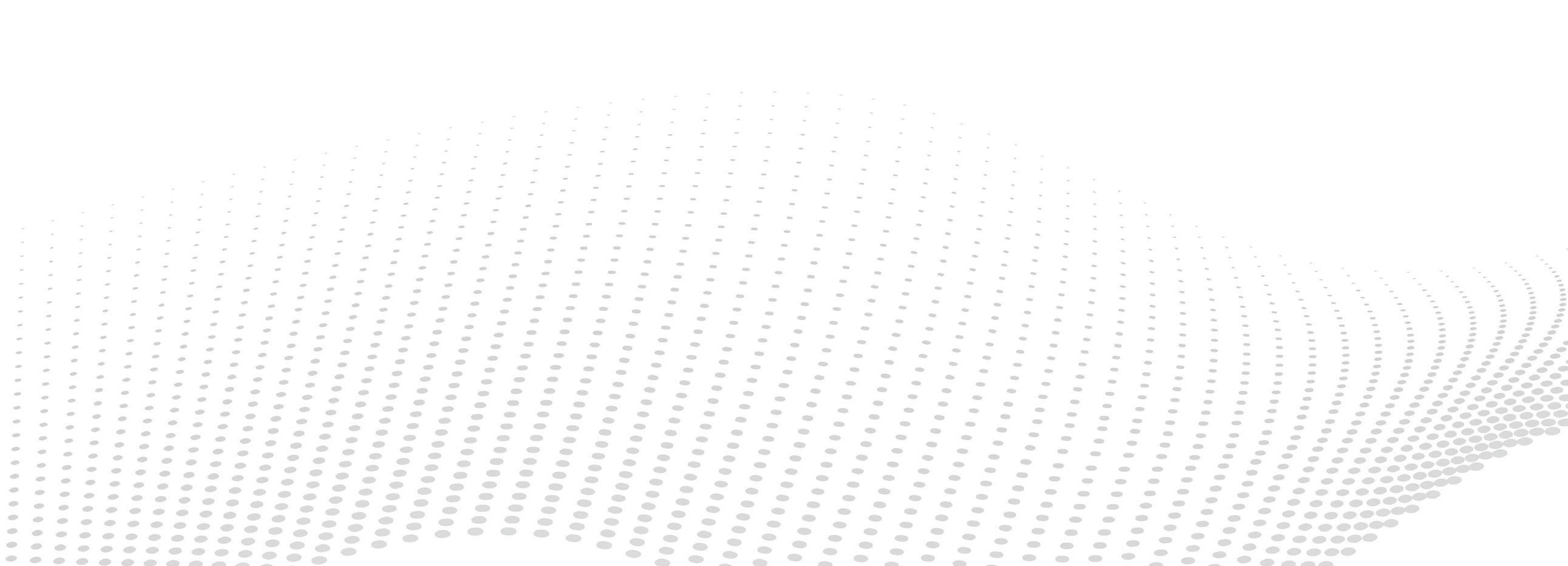
c. Just in time arrival In cases where the schedules for berthing and cargo handling at ports are notified in advance, the vessel must control/reduce its voyage speed at sea to save waiting time in ports and thus save fuel and emissions. In this respect, waiting time in ports, turnaround time and Greenhouse Gas Emissions could be reduced.
e. Trim optimization Most ships are designed to carry a designated amount of cargo at a certain speed for a specific fuel consumption. This implies the specification of set trim conditions. Loaded or unloaded, trim has a significant influence on the resistance of the ship through the water and optimizing trim can deliver significant fuel savings. For any given draft, there is a trim condition that gives minimum resistance. Software tools which combine hull, propeller pitch and main engine power output/ settings in order to advise on optimal trim settings to reduce fuel consumption are readily available on the market.
h. Slow steaming / speed optimization
Speed optimization can produce significant savings and a reduction in greenhouse gas emissions. However, optimum speed means the speed at which the fuel used per tonne mile is at the minimum level for that voyage. It does not mean minimum speed; in fact sailing at under the optimum speed will consume more fuel rather than less. Reference should be made to the engine manufacturer's power/ consumption curve and the ship's propeller curve. Possible adverse consequences of slow speed operation may include increased vibration and soot.
d. Auto-pilot adjustments
Large improvements in automated heading and steering control systems technologies have been applied in the recent past . Whilst originally developed to make the bridge team more effective, modern autopilots can achieve much more. An integrated Navigation and
Command System can achieve significant fuel savings by simply reducing the distance sailed "off track". The principle is simple; better course control through less frequent and smaller corrections will minimize losses due to rudder resistance.
f. Weather routing
Weather routing is the use of meteorological data to assist in voyage planning to minimize fuel consumption, possible cargo damage, hull stress and to maximize crew safety. It is particularly useful during periods of bad weather such as winter in the northern hemisphere and the monsoon season in the
Indian Ocean. It can also be considered during transoceanic crossings where greater options for alternative routings exist. The main objective of optimized route planning is to avoid high storm or wave frequencies and maximize a calm sea state.
h. Hull and Propeller maintenance Routine in-water polishing of the propeller can lead to an improvement in efficiency. The surface of a propeller will become less smooth due to strain and cavitation damage, while fouling will reduce efficiency over time. This can be avoided by regular polishing or coating of the propeller.
Ship-Design technology & Hydrodynamics
a. Air lubrication
A vessel’s resistance when moving through the water is made up of multiple components, of which frictional resistance is the most dominant. Injection of air into the turbulent boundary layer (between the stationary and moving water) can reduce the frictional resistance of the hull. Air lubrication is achieved by pumping air beneath the hull, reducing the area of the hull in direct contact with the water flow, or in the case of discrete bubbles, by modification of momentum transport and average density in the boundary layer. There are three major categories of air lubrication technology being studied now: Air Layer Drag Reduction (ALDR), Bubble Drag Reduction (BDR),and Partial Cavity Drag Reduction (PCDR). Air lubrication systems are recognized by IMO as a Category B-1 “Innovative Energy Efficiency Technology” as described in MEPC.1/Circ.815.
b. Energy saving devices (Mewis duct, contra-rotating propeller, etc)
The main goal of energy / propulsion improving devices is to create an optimal inflow for the propeller by guiding one side of the stern flow in the opposite direction to the propeller rotation, generating pre-swirl. The solution consists of multiple curved fins and/or a ring attached to the ship’s aft part of the hull in order to prevent the power losses that typically occur in a propeller’s slipstream. The curved fins enhance the propeller’s efficiency while keeping resistance at acceptable levels. The ring reduces the tip vortex and also levels out the peak stresses that occur in severe loading conditions such as slamming. As a result, less power is needed to propel the ship, leading to fuel savings.
c1. Hull re-designing
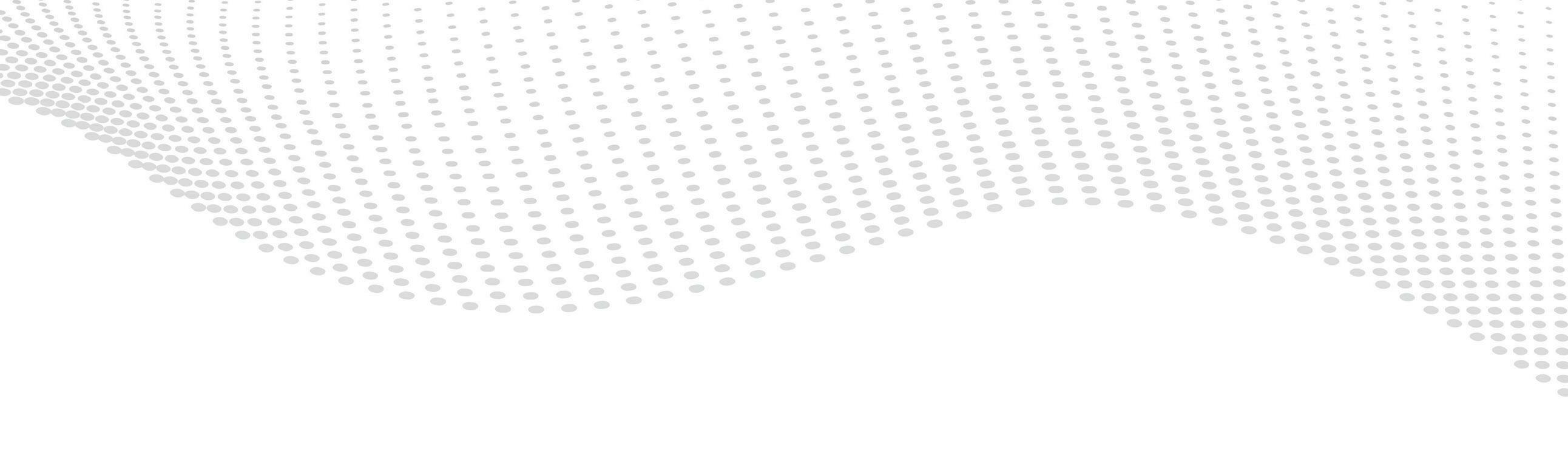
c2. Rudder re-designing c3. Bulbous bow
Newbuilding ship design offices are making a continuous effort to introduce new vessel designs by optimizing rudder, hull and bulbous bow design in order to gain benefits such as: improved energy efficiency and reduced fuel consumption, excellent manoeuvrability, lower vibration levels, greater comfort onboard and reduced emission levels.
d. Superstructure aerodynamics An increasing number of newbuilding shipyards are investigating the possibility of building vessels with the introduction of a streamlined and aerodynamic shape to a ship’s superstructure. Some designs also include a built-in citadel along with other piracy prevention measures. In most of the cases the accommodation block features energy efficient LED lighting and noise and vibration insulation for enhanced crew comfort, as well as a wheelhouse with a widened backward view for safer navigation. e1. Lightweight construction
e2. Sandwich plate system (SPS) The motivations for using conventional and more advanced types of lightweight materials and SPS structures are in connection with increasing payload, reaching higher speeds and lowering fuel consumption. In ship building, SPS allows for simplified, more robust structures with less welding, labour and material required. The reduction in fatigue and corrosion prone details increases service life and reduces maintenance costs.
f. Hull surface anti-fouling coating
a. e.
b. f.The use of an appropriate anti-fouling coating system is an additional means by which hull and propeller efficiency can be improved. While modern biocidefree systems may offer better performance and do not release harmful toxins into the marine environment, they also require additional monitoring for the build-up of slime. The main types of antifouling paints are: • Hydrophobic foul-release coatings:These low energy coatings enable an easy release of marine organisms; • Enzyme-based and biocide-free coatings: These coatings apply new components, which promise less hull fouling; • Copper-freeantifouling:Thesepaintsharmlesslyrepelmarineorganismsfrom the hull, rather than kill them; • Nanoantifouling:Thesecoatingscreateasurfacesoslipperythatnoorganism can stick. However, in most cases, speeds above 10 knots are required.
c. d.
g. No-Ballast system
Non-ballast or ballast free ships are currently prototypes that have emerged from the need of operators to control the risks associated with the recent Ballast Water Management Convention, since taking up and discharging ballast water can lead to ecological and economic consequences. Traditionally, ballast water systems increase the weight of a vessel in the light cargo condition, thereby improving stability, propulsion, manoeuvrability, and reducing stress on the hull during transit. A change of thinking in this concept has focused on the use of the ballast condition as a change of buoyancy, rather than an addition of weight in order to get the vessel to its safe ballast drafts. This led to the invention of the ballast free ship concept, where traditional ballast tanks are replaced by longitudinal, structural ballast trunks that extend beneath the cargo region of the ship below the ballast draft. Currently, some projects are in progress, including ones with hull forms that do not require ballast at all (V-shape). Results are expected in the near future.
In order to access the questionnaire, please scan from your smartphone the following QR code:
or visit the following web address: https://forms.gle/TwUeGJnxS2vFFfrc8 Having in mind that this is the first interactive article, for which your participation is required, please feel free to vote and encourage your fellow colleagues to do the same, in order to formulate the contents of the next article that will be published in the next Wavelength issue. This is your chance to become a columnist. Let’s do it….
g.
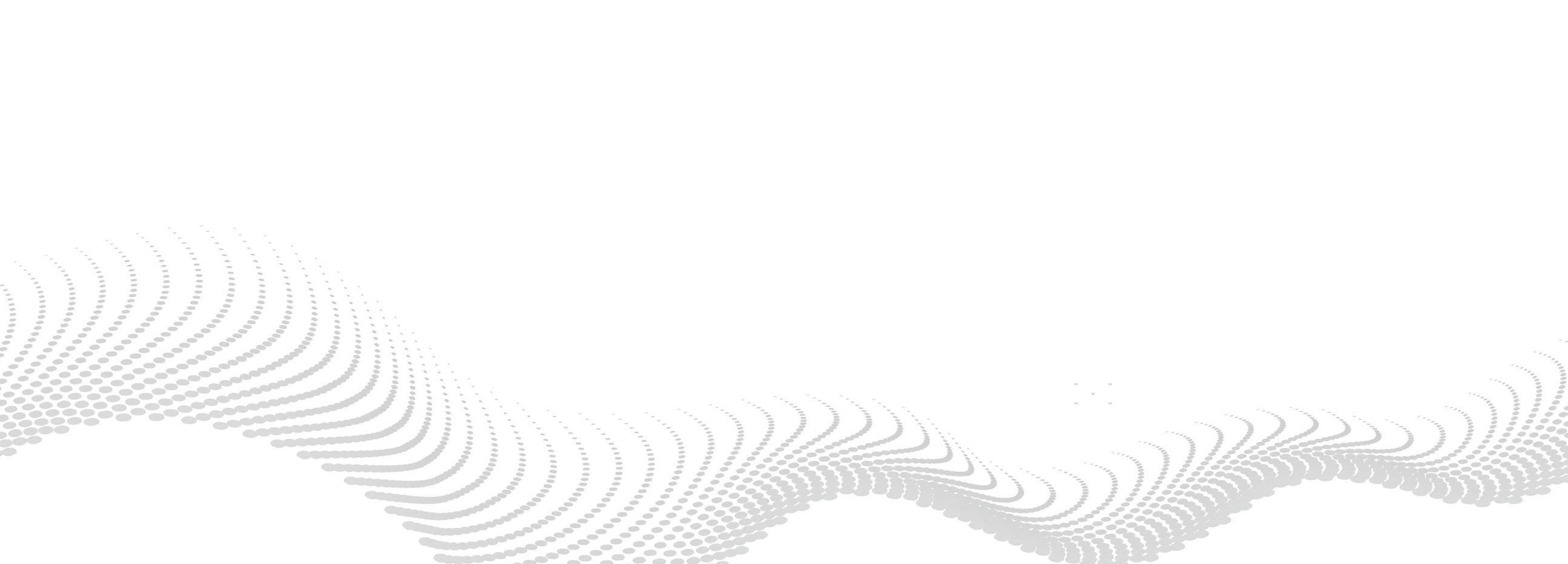