
12 minute read
Global Sulphur Cap 2020 (Part 1
from Wavelength #68
Technical
Global Sulphur Cap 2020 (Part 1)
Advertisement
A. Introduction
As agreed at the IMO’s Marine Environment Protection Committee (MEPC 70) meeting, held in October 2016, a 0.50 percent global sulphur cap on marine fuel oil will be implemented beginning January 2020. This will require all vessels operating outside Emission Control Areas (ECAs) to use fuel oil with a maximum sulphur content of 0.50%, while vessels operating within ECAs will be restricted to a maximum sulphur content of 0.10%.
Figure 1: Sulphur content requirements
In addition to IMO requirements, there are regional and local requirements addressing fuel sulphur content: - European Union: The European Union Sulphur Directive stipulates a maximum of 0.10% sulphur content for ships in EU ports. - State of California: California’s Air Resources Board (ARB) enforces a 0.10% sulphur limit within 24 nautical miles of the Californian coast. The regulation does not allow for any compliance options other than low sulphur marine gas or diesel oil (DMA or DMB). - China: Ships are required to use fuel with a maximum: •0.50% sulphur content while operating within ECAs defined by the Law beginning 01 January 2019. •0.10% sulphur content while operating in the inland water emission control areas from 01 January 2020 and around the island of Hainan beginning 01 January 2022. Figure 2: IMO & Local Emission Control Areas B. Compliance Options
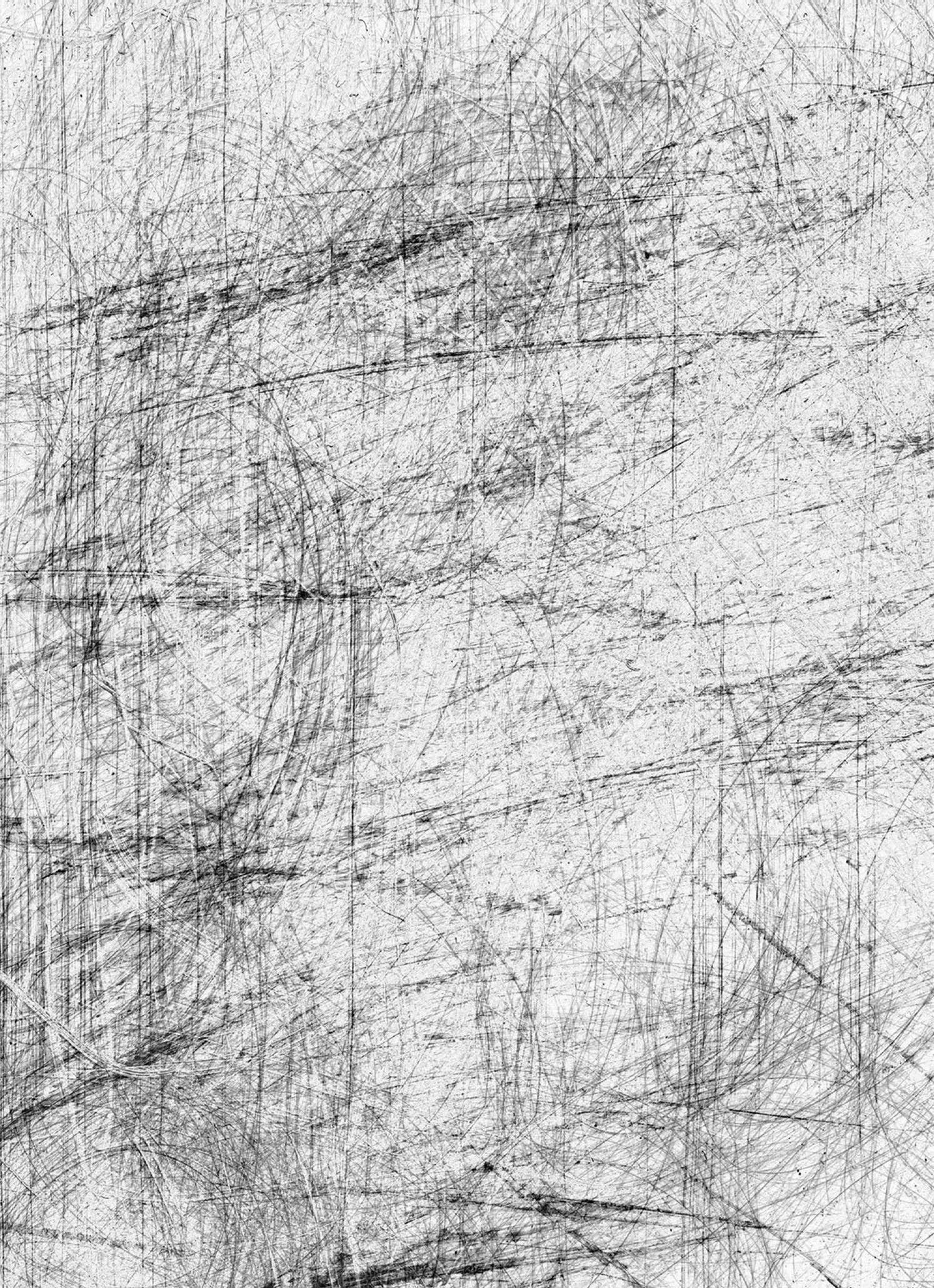
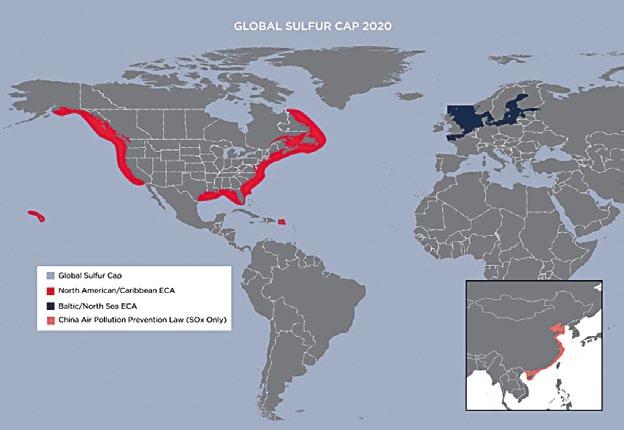
There are following options to ensure compliance with Global Sulphur Cap: 1. Low sulphur distillate fuels 2. Low sulphur heavy fuel oil 3. HSFO with an SOx scrubber 4. LNG as fuel IACS United Interpretation UI SC 123 defines the "type of fuel" as the exact grade of fuel. The "grade" is grouped according to its sulphur content and viscosity as follows: - Residual Marine Fuel (RMF) refers to fuel oils with a sulphur content above 0.10%, but not exceeding 0.50%, which require some form of heating to achieve the required injection viscosity for combustion. - Distillate Marine Fuel (DMF) refers to fuel oils with a sulphur content above 0.10%, but not exceeding 0.50%, which do not require heating to achieve the injection viscosity. - Low Sulphur Residual Marine Fuel (LSRMF) refers to fuel oils with a sulphur content not exceeding 0.10% which require some form of heating to achieve the required injection viscosity for combustion. - Low Sulphur Distillate Marine Fuel (LSDMF) refers to fuel oils with a sulphur content not exceeding 0.10% and a minimum kinematic viscosity of 14 cSt at 40°C. B.1. Low sulphur distillate fuels (DMF)
Switching to low sulphur distillate fuels will result in a significant increase in fuel costs and may also require upgrading to a fuel treatment plant due to the significantly lower viscosity of the fuel. These types of fuels can lead to increased leak rates on fuel pumps. One particular concern is the reduction in the lubricity of the fuel which affects pumps and other components in the fuel system. HFO circulating and supply pumps may need to be replaced due to reduced fuel oil viscosity and lubricity. Additionally, a cooler or chiller should be installed in the fuel system to control temperature and maintain the viscosity of the fuel at the Engine inlet as per the Engine Maker’s recommendation.
Figure 3: New M/E MGO Circulating pump
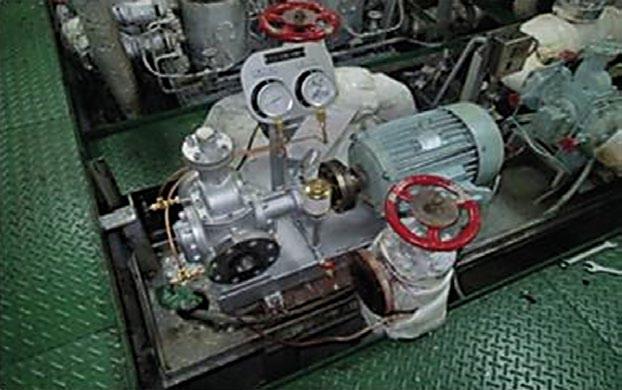
Figure 4: MGO cooler
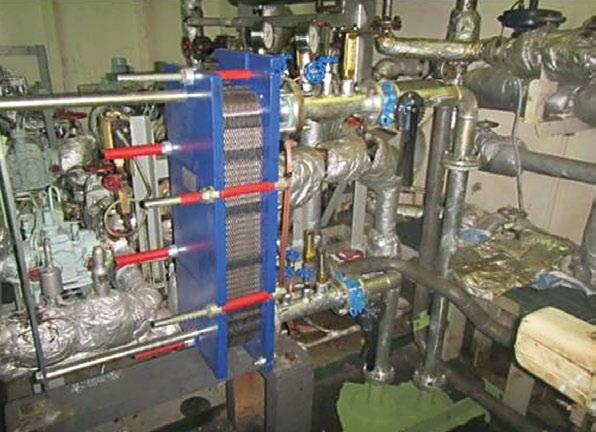
B.2. Low sulphur heavy fuel oil (RMF)
Various marine fuel suppliers have developed low sulphur fuel oils which contain low sulphur, like MGO, but have a higher flash point and higher viscosity similar to HFO, and require preheating. These fuels are blended products that incorporate various heavy and light refinery product streams, including residual fuel oils and middle distillates. When compliant low sulphur heavy fuel oil is selected, the following items should be examined: - Fuel Quality - Fuel Oil Procurement - Vessel Design / Modification - Documentation and Reporting - Operational Considerations - Crew Training
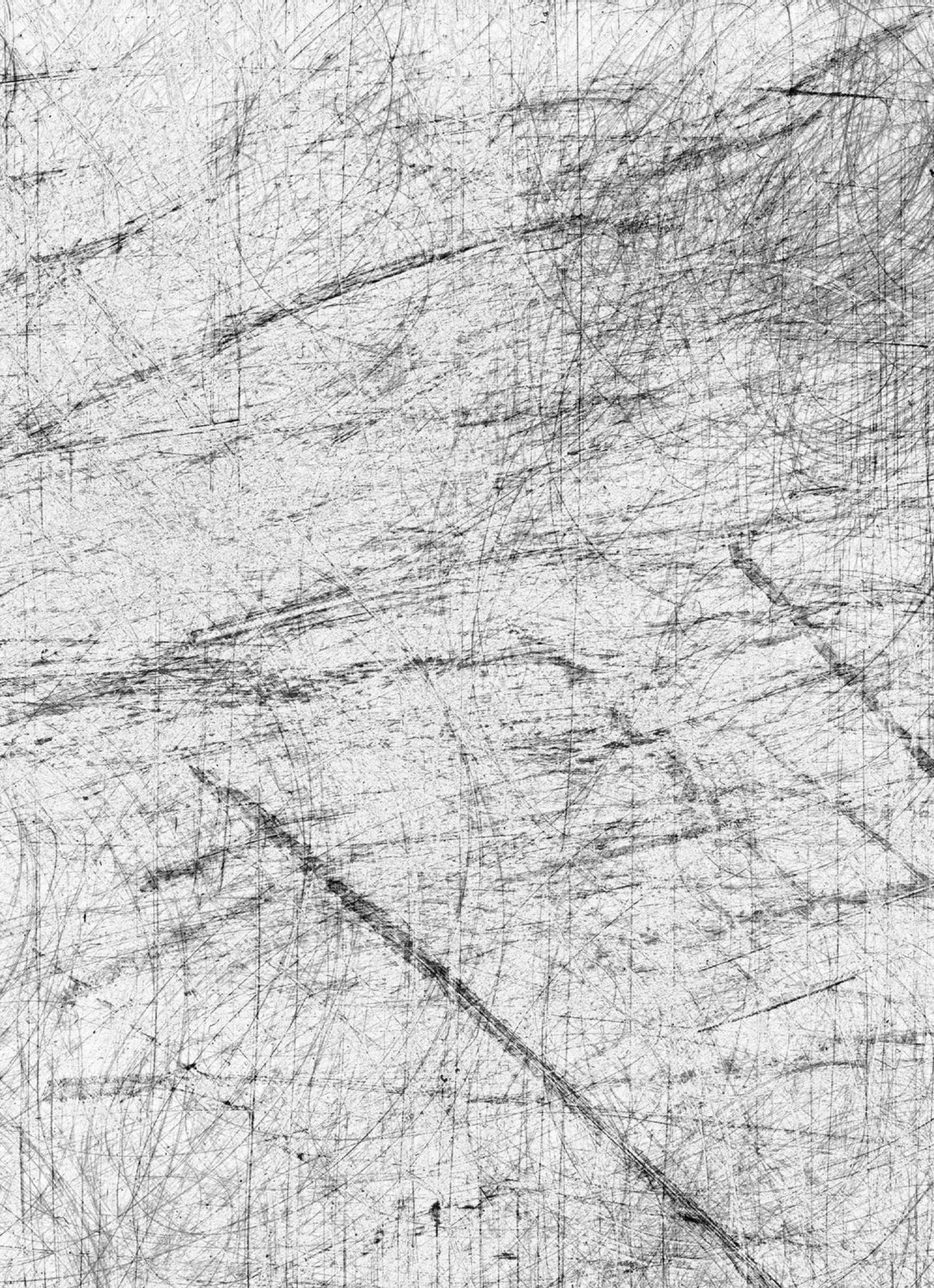
B.2.1 Fuel Quality The existing fuel standard, ISO 8217, does not cover all safety aspects related to the new fuel blends. The corresponding ISO Working Group is working on identifying methodologies for testing long-term stability and compatibility between different fuel batches. In response to the IMO request to provide consistency between the relevant ISO standards on marine fuels and the implementation of the 0.50% sulphur limit, the working group is planning to publish a Publicly Available Specification (PAS) in 2019. Key quality concerns associated with these fuels include: - Compatibility - Viscosity - Pour point - Stability - Flash point - Unusual - Catalytic fines - Ignition and components - Density combustion - Lubricant characteristics compatibility
• Compatibility The consequences of mixing different blends of fuel are the formation of asphaltenes and heavy sludge in the fuel oil system, resulting in a potential blockage and loss of fuel supply to the engine. In order to address fuel incompatibility, the following measures should be taken: - Segregate fuel tanks and piping. - Avoid mixing different fuel batches. Empty tanks as much as possible before bunkering a new fuel batch. - If mixing cannot be avoided: •Reduce the amount of fuel in the tank as much as possible before bunkering new fuel. •Bear in mind fuels with similar viscosity, density and pour point often show acceptable compatibility, as they are likely to be of a similar fuel type. -Check the compatibility of the fuel in the tank and the new fuel (on-board, laboratory).
Figure 5: Compatibility Test
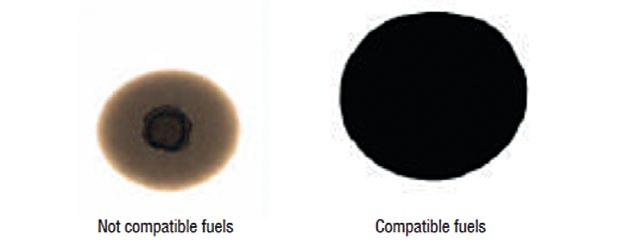
• Stability The stability of a residual fuel is defined by its resistance to breaking down and precipitating asphaltenic sludge even if it is subjected to forces such as heating and a long storage time. It is, therefore, important to perform regular sampling when the fuels are being stored for an extended period of time. • Catalytic fines (Cat fines) Cat fines are small, very hard particles originating from the refining process. They mainly consist of aluminium (Al) and silicon (Si) oxides. In limited quantities they can cause gradual engine wear. If present in larger amounts, they can cause significant damage to engine components such as fuel pumps, fuel injection valves, cylinder liners and piston rings. They may get trapped between sliding surfaces such as the piston ring and cylinder liner or the piston ring and ring groove. The trapped particles either roll freely between the surfaces, or become partially embedded in one of the surfaces, see Fig.6. Trapped hard particles will wear the sliding surfaces in a wear process known as 3-body abrasion. The more and bigger the particles are, the greater the wear will be. An example of such particle trapping can be seen in Fig.7, where cat fines are embedded in the soft graphite lamellas in the cylinder liner surface.
Figure 6: Wear in combustion chamber parts Figure 7: Replica print showing cat fines (red arrows)
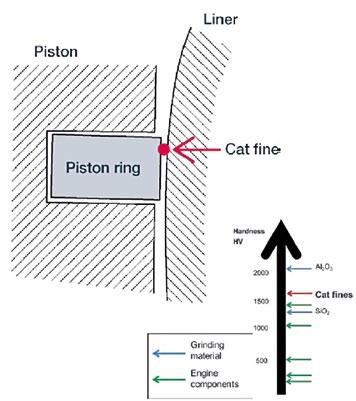
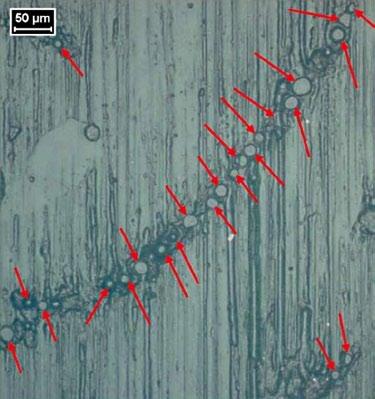
Technical
The latest marine fuel standard specifies a maximum of up to 60 ppm Al+Si in the fuel (ISO 8217). A maximum level of 15 ppm at the engine inlet is acceptable for a short period of time, but the normal level must be kept lower. Figure 8: Recommended maximum content of cat fines in fuel entering the engine
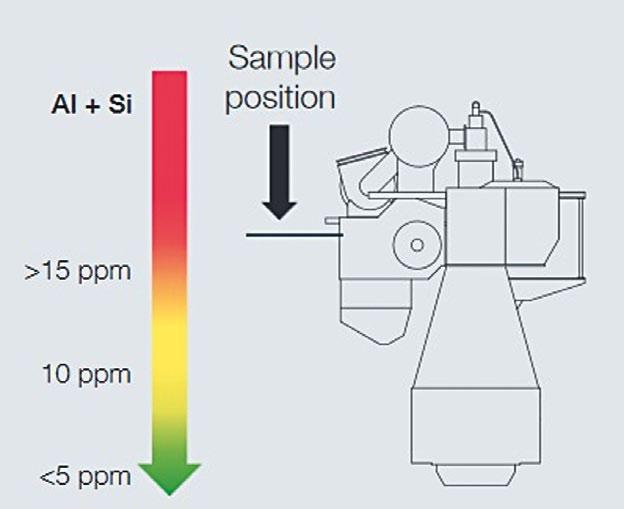
In order to reduce the cat fines, the following measures should be taken: - Maintain the optimum operating condition of the purifiers and filters. - Install a fine filter of 10μm before the engine. - Clean/drain service and settling tanks on a regular basis. - Check the fuel regularly for cat fines content, use drain oil analysis and inspect the engine for wear on the piston rings, pistons and cylinder liners. • Density It is anticipated that the 0.50% sulphur limit compliant fuel will have broad ranging density characteristics due to different production processes. While density variation may not have an immediate safety impact on machinery, it could affect the operation of the purifier and the reading of the tank gauging system. It is, therefore, important to take following corrective measures: - Adjust the purifier setting for a different fuel density. - Calibrate the tank gauging system according to fuel density for accurate readings. • Viscosity It is anticipated that the 0.50% sulphur fuel will have broad ranging viscosity characteristics. It is, therefore, important to ensure the proper function of the automatic control system for viscosity and temperature. • Flash Point SOLAS Regulation II-1/4.2.1.1 requires that the flash point of any fuel oil used in machinery spaces must not be less than 60°C. The same is specified in ISO 8217. However, even if the fuels bunkered with flash points not less than the minimum required value are stored at a temperature below the determined flash point, flammable vapors may still develop in the tank headspace, especially if fuel heating is provided. It is, therefore, important to ensure the following: - The heater or heat tracing is to be bypassed if necessary. - Heating is to be automatically shut down upon detection of a higher temperature than the designated limited (typically 10°C below flash point). - No uncertified electrical equipment is to be positioned in the vicinity of the fuel tank vent outlet. • Ignition and Combustion Characteristics The Calculated Carbon Aromaticity Index (CCAI) of the sulphur limit compliant fuel should be verified in line with the ISO 8217 specification. The CCAI is the ignition characteristic of residual fuel. Several engine tests have revealed that these fuels ignite and burn as other fuels do. • Pour Point The pour point indicates the minimum temperature at which the fuel should be stored and pumped. The cloud point is the temperature at which a cloud of wax crystals first appears in the fuel. The temperature in the tanks and pipes should be higher than the pour point of the fuel. If the temperature falls below the cloud point, waxy precipitates might form which could block filters and other equipment. If the temperature falls below the pour point, then the fuel cannot flow. A severe case of waxy precipitates may be seen in the photo in Fig. 9. Figure 9: Waxy precipitates in a fuel sample
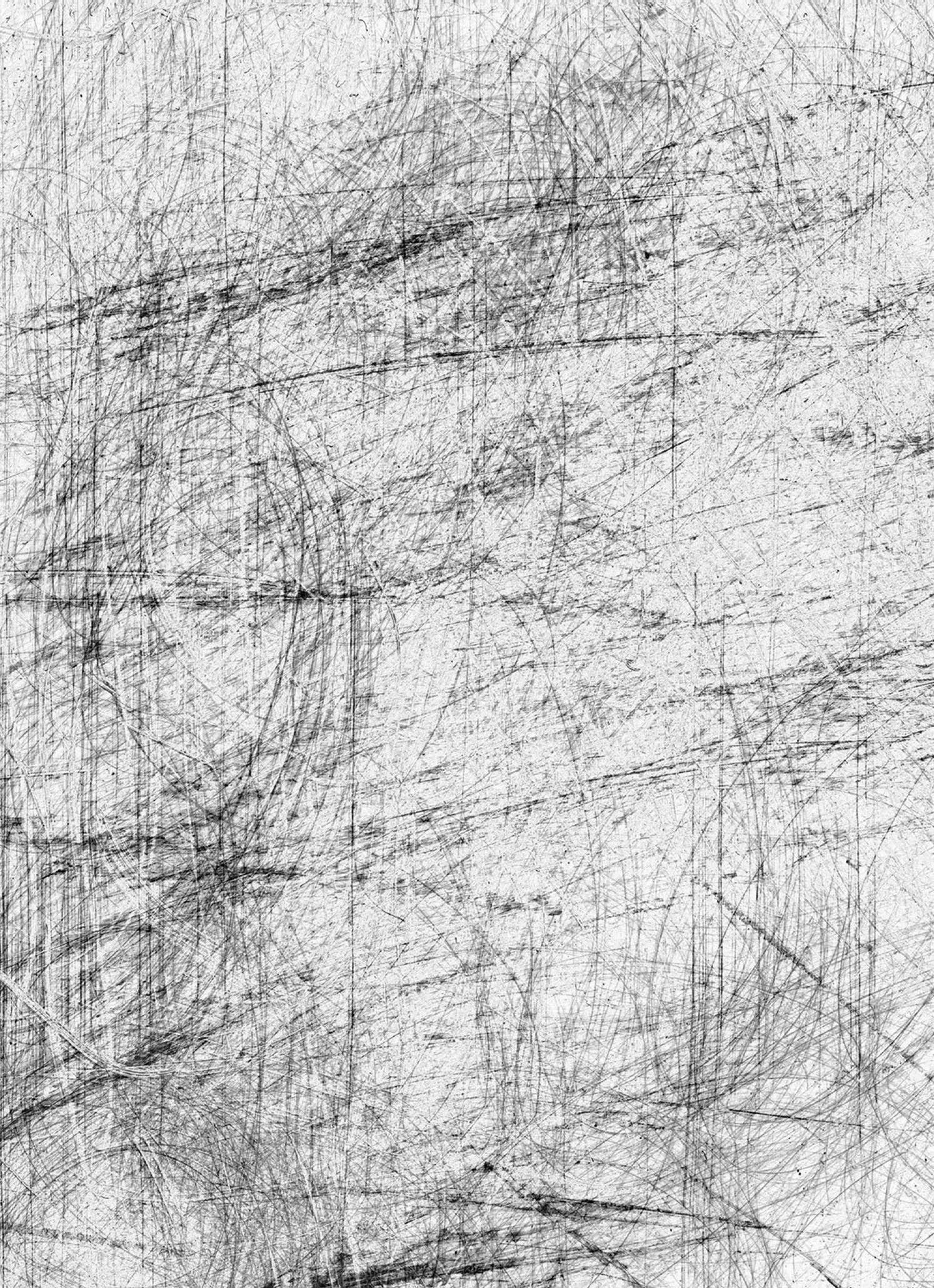
The following corrective measures should be taken: - Confirm that the cold flow characteristics are suitable for the ship’s design and intended voyage. - Provide heating arrangements for the fuel.
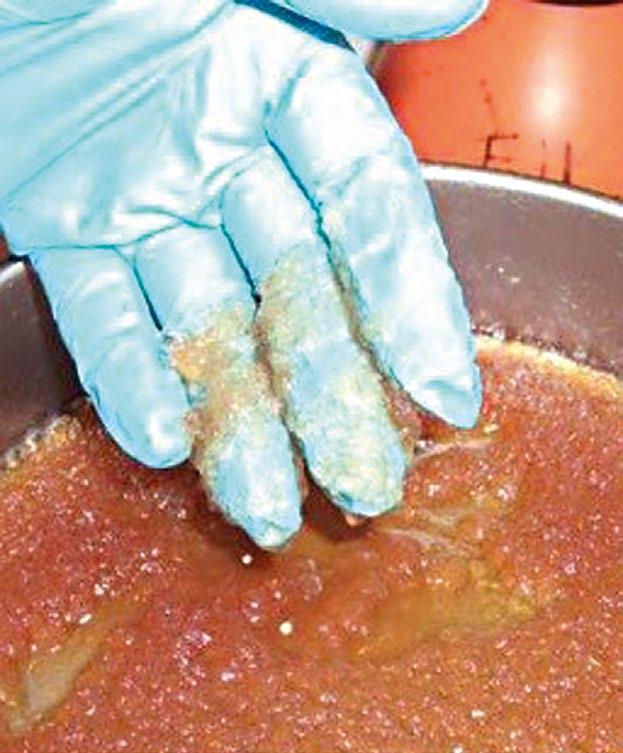
• Unusual Components Although the fuel may comply with ISO 8217, there may be components not specified in the standard that contaminate the fuel and cause various problems such as seizing and damage to fuel pumps, excessive sludging and filter blocking. Some of the unusual components identified include fatty acids (carboxylic acids), phenols and nitrogen containing compounds. In order to identify the unusual components, additional testing such as Gas Chromatography – Mass Spectrometry (GCMS) testing should be conducted. • Lubricant Compatibility When low sulphur fuel is used, a reduced amount of sulphuric acid forms in the combustion chamber, and fewer additives in the lubricant will be used. High-BN cylinder oils will lead to overadditivation in the process of controlling the corrosion and an increased build-up of piston crown deposits. This may disturb the lubricant film and could lead to micro-seizures on the piston rings and liner, thereby cause scuffing. Engine Makers recommend switching to low-BN cylinder oil when operating on low-sulphur fuel oil.
Figure 10: Recommended BN levels for M/E cylinder oils
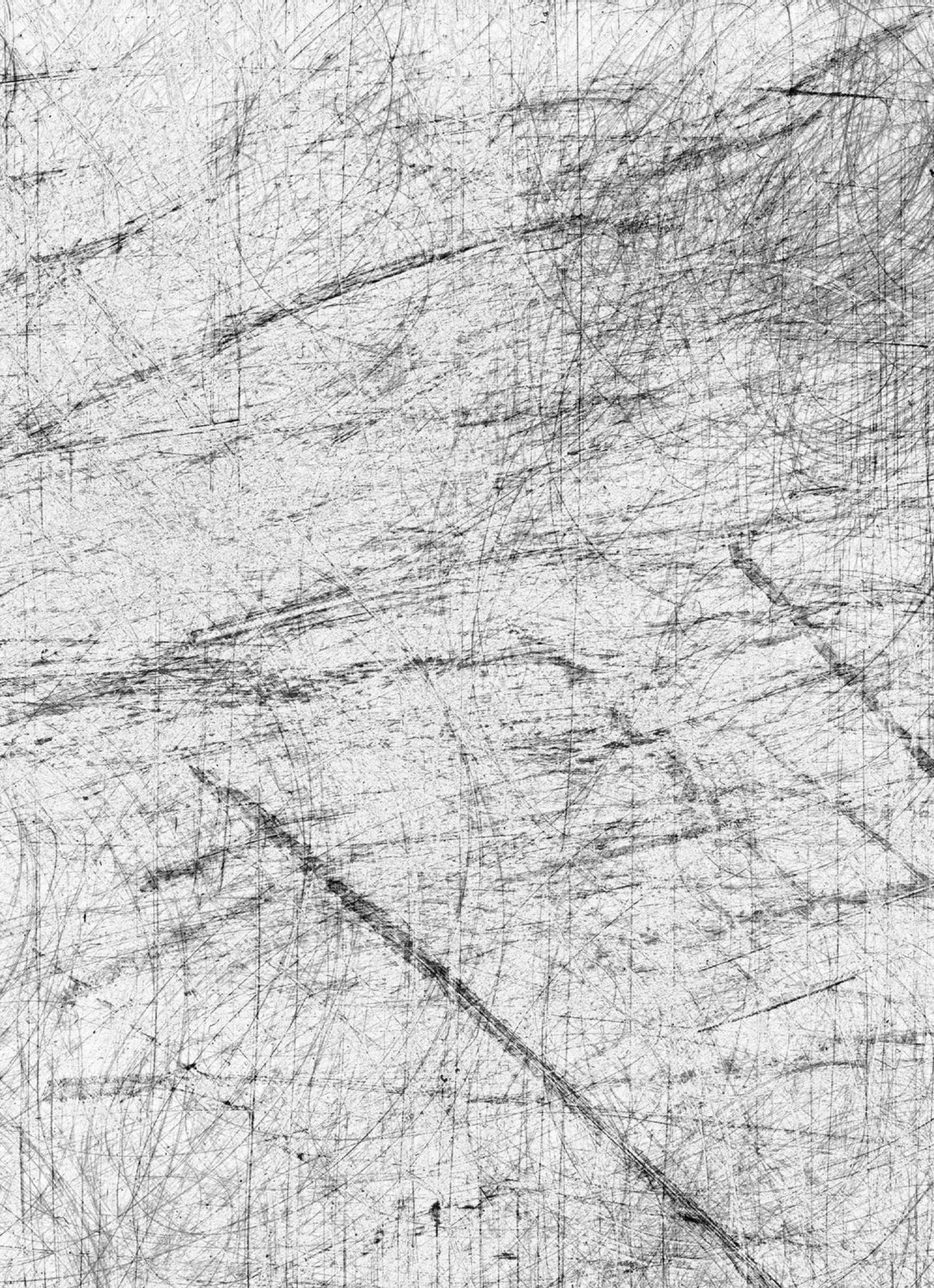
B.2.2. Fuel Oil Tank Design and Modification - Storage Tanks For vessels that use both RMF and LSDF, at least one storage tank is required for each type of fuel. In practical design, multiple storage tanks are typically provided. One of the measures for mitigating incompatibility hazards due to the use of different RMFs is to provide two (or two group) storage tanks for RMFs. - Settling Tanks The “two settling tank” concept is the most common arrangement. As an example, one settling tank is used for 0.10% maximum sulphur distillate fuel (LSDMF) and the other for 0.50% maximum sulphur fuel (RMF). - Service Tanks As per SOLAS Regulation II-I/26.11 “two fuel oil service tanks for each type of fuel used on board necessary for propulsion and vital systems shall be provided on each ship, with a capacity of at least 8 hours at maximum continuous rating of the propulsion plant and normal operating load at sea of the generator plant”. B.2.3. Operational Considerations - Fuel System Cleaning To avoid compatibility and stability issues while switching from Heavy Fuel Oil (HFO) to 0.50% residual marine fuel (RMF), cleaning of the fuel system (tanks & piping) is required. The cleaning methods are as follows: - Manual tank cleaning - The use of MGO to dissolve and flush away the sludge in the
HFO tank and fuel oil piping - Cleaning with chemical additives - Fuel Switching Fuel switching may involve changing over from one RMF to another for fuel segregation and switching between RMF and LSDMF or vice versa when a ship enters and leaves an ECA. A fuel switching procedure has to be ship-specific based on the tank and piping arrangements and the ships’ operation pattern should be prepared.
B.2.4. Fuel Oil Procurement - A fuel purchasing procedure should be developed and an action plan prepared if the compliant fuel is not available. - The bunkered fuel should be in general compliance with ISO 8217. - The bunker fuel contract may include a clause for additional testing for the identification of unusual components.
B.2.5. Documentation and Reporting - Ship Implementation Plan (SIP) The Ship Implementation Plan will help to mitigate the risk associated with the transition from the current use of heavy fuel oil to 0.50% max sulphur fuel by addressing the following: - A risk assessment and mitigation plan - Fuel oil system modifications (if required) and tank cleaning - The fuel oil capacity and segregation capability - The procurement of compliant fuel - A fuel oil change-over procedure - Documentation and reporting - Fuel Oil Management Plan (FOMP) A ship-specific FOMP based on the fuel oil piping system, main and auxiliary engines and other related equipment should be prepared. - Fuel Oil Non-Availability Reporting (FONAR) The Master / Company should submit to the Port State Administration in the port of arrival and the Flag Administration the fuel oil non-availability report (FONAR) as soon as it is determined that compliant fuel oil cannot be procured and used. B.2.6. Crew Training Initial and periodic training will help the crew to increase awareness of the challenges associated with compliance with post-2020 operations using 0.50% maximum sulphur fuel and the respective mitigation measures.
