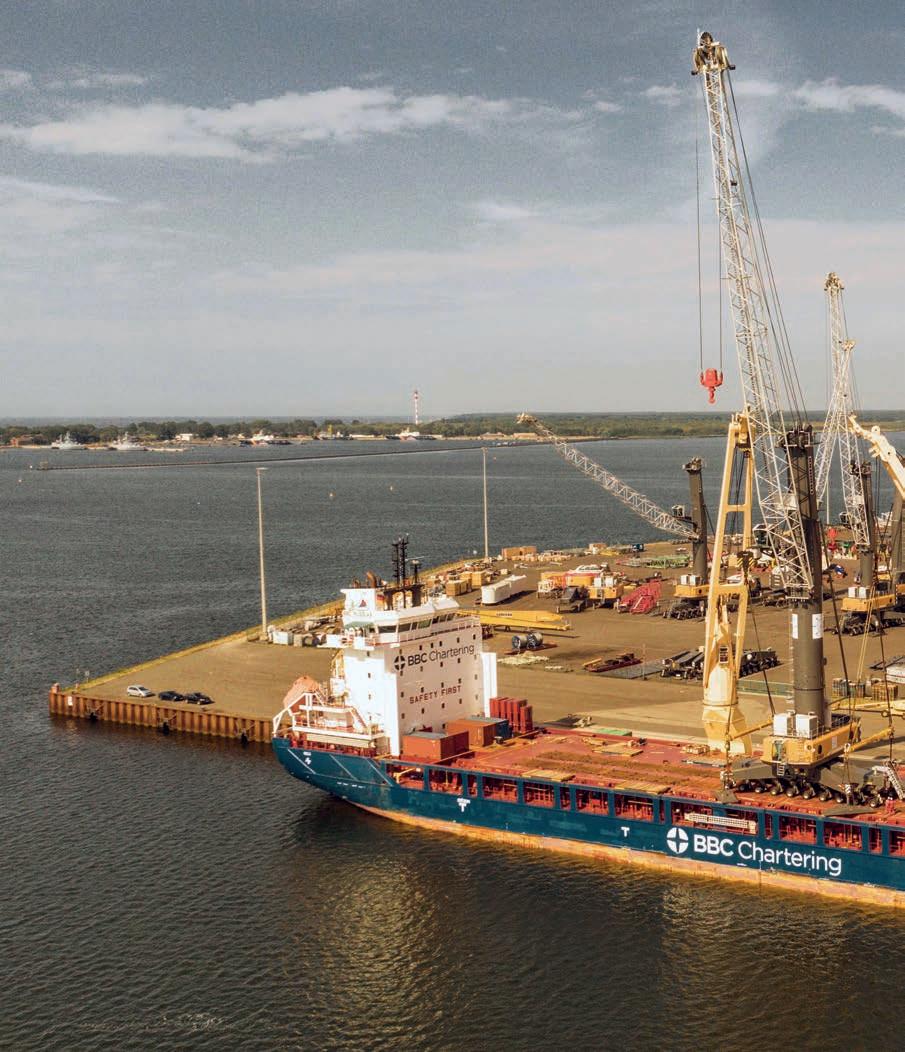
5 minute read
Going the distance
SINCE THE START OF PRODUCTION IN 2005, LIEBHERR-MCCTEC ROSTOCK HAS MANUFACTURED AND DELIVERED WELL OVER 1,000 MARITIME CRANES. TODAY, THE NUMEROUS MOBILE HARBOUR, SHIP AND OFFSHORE CRANES ARE IN USE IN OVER 100 COUNTRIES ON ALL CONTINENTS. THE 1,300TH CRANE HAS JUST LEFT THE ROSTOCK PREMISES TO ITS DESTINATION IN GHANA. >>
ALL PHOTOS COURTESY OF LIEBHERR.
Advertisement
Liebherr Rostock has manufactured and delivered 1,300 maritime cranes since 2005
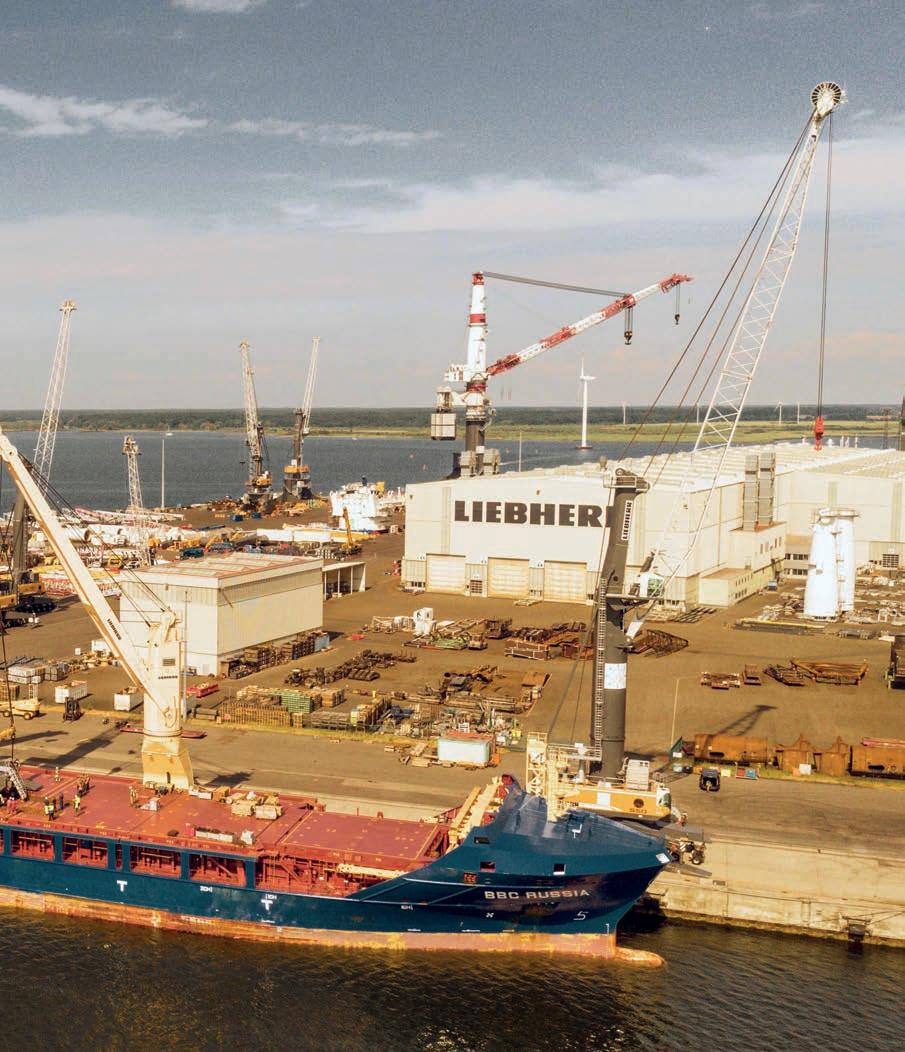
In additon to the worldwide customer service network, it is the contnuous technical development of the cranes and assistance systems that gives Liebherr’s customers the decisive edge. In the future, the mobile harbour crane series is set to run on the fossil-free HVO 100 diesel. The diesel reduces emissions by up to 90% and is derived from renewable raw materials. Liebherr is innovatng in a fast pace, and developing new solutons according to current and future circumstances.
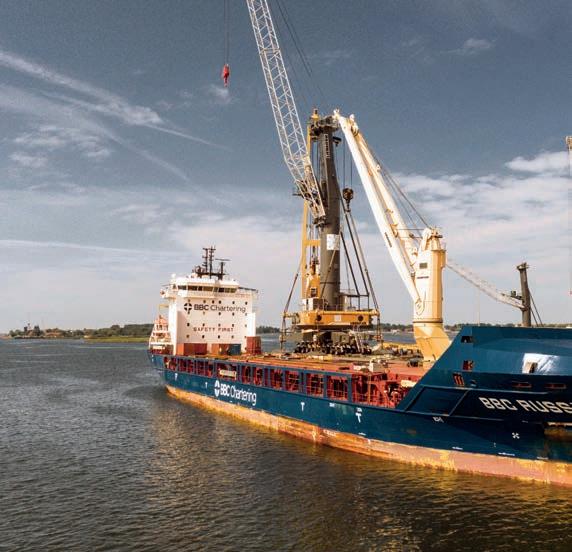
Building digital bridges
Distance doesn’t seem to be an issue for Liebherr either. Remote products are the topic of the hour and have been in greater demand than ever due to the COVID-19 pandemic. All the beter that the Liebherr Group has been working on such innovatve solutons for a long tme and is able to ofer its customers appropriate products for various applicatons, for remote maintenance as well as for collaboraton with local technicians.
Last year’s pandemic has given the digital transformaton an extraordinary impetus, demonstratng that there most certainly are solutons for performing work without being present on site. Such remote applicatons have many benefts and are currently experiencing a veritable boom. Liebherr has been working on various remote products for many years, now allowing the company to make use of these and to further expand its innovatve technologies.
At the push of a button
Liebherr has developed a remote service tool for crawler cranes, deep foundaton equipment, and maritme cranes. The app allows operators to share visual informaton, resultng in faster and easier troubleshootng. As part of a test, all customers had free access to the new app untl the end of 2020. The app allows for audio and video calls and comes with features like a chat functon, screen sharing, image and document exchange, and whiteboarding functons. These enable realtme, fast and efectve customer support from Liebherr experts worldwide.
Last year, the enterprise tested the tool in remote locatons and challenging situatons
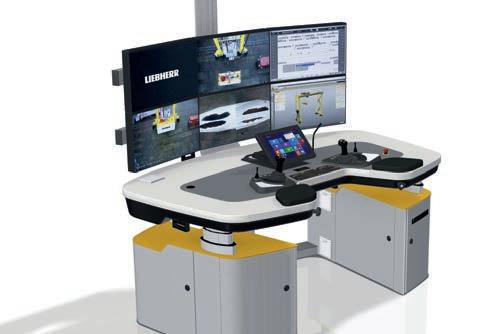
Crane number 1,300 was shipped from Rostock, Germany to Ghana in June
Remote Service App in use for remote assembly of a mobile harbour crane.
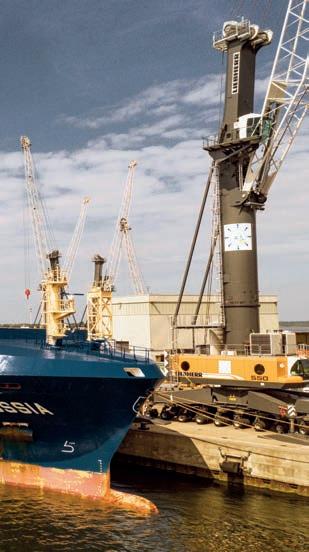
in order to meet and adapt to customer requirements. The app can be used around the world in real tme and can transmit visual informaton, allowing fast and efcient customer support when needed. Liebherr also ofers remote diagnostcs for its cranes of the latest generaton. If a problem occurs, a service engineer connects to the crane control via an encrypted mobile phone connecton to support the customer by troubleshootng the issue. The remote tools allow issues with the machine to be identfed more quickly, avoiding unnecessary journeys for maintenance – an especially important factor in tmes of any travel restrictons. Precise fault diagnosis allows the correct parts to be ordered so that the crawler crane, rope excavator, maritme crane, deep foundaton machine or mobile crane can quickly be put back into operaton.
Smart glasses
Smart glasses are a practcal tool for providing swif assistance to customers in faraway places without having to send a technician around straight away. The glasses allow pictures to be easily shared and discussed. So this remote tool not only avoids the need for travel, but also saves substantal costs and makes customer service more efcient. Liebherr is also testng this capability in its internal engineering and producton in the Aerospace division. Virtual and augmented reality allows fnal inspectons to be performed on a landing gear assembly using these glasses. In this case, the 3D model is superimposed on reality, enabling the inspector to examine the machine virtually ‘live’ and to improve the quality inspecton process. The company also uses smart glasses for earthmoving machines and material-handling technology, enabling digital remote support for service and maintenance cases. The customer wears the smart glasses and a live image is directly transmited to a Liebherr service technician. They subsequently carry out a fault diagnosis and ideally fnd a soluton to the problem.
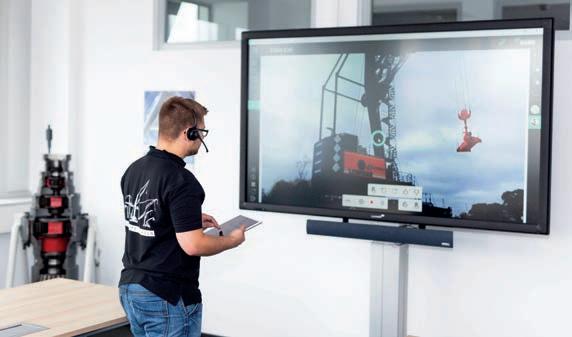
Instead of sitting in an operator cabin, the Remote Operator Station (ROS) offers an offce environment
Control from the offce
Another remote innovaton is Liebherr’s Remote Operator Staton (ROS), which has been developed for use with all Liebherr container crane products and ofers fexibility in operatons. The ROS is ergonomically designed and fted with multple displays, allowing the operator to perform all normal driving functons from a remote ofce environment. Furthermore, the move to automaton with remote control brings operatonal benefts, with a single ROS operator being able to operate several cranes simultaneously. Additonal benefts include faster and easier shif changes and a more atractve work environment for employees.
Digital troubleshooting
When asked if operatons like these, in which the Remote Service App played an important role, will become more common in the future, Customer Service Manager for Liebherr-MCCtec Rostock Christan Lübke responds, “Solutons like the Remote Service tool will certainly be part of our digitalised future. That being said, we will probably be less reliant on the app for supervising commissioning. Instead, it will probably be used more ofen for troubleshootng machines that are already operatonal. The Remote Service App can be used to identfy errors more quickly. Currently, if an assembly mechanic initally travels to a locaton and then realises a pump is damaged, he may need to make a second trip to replace that part. Digital troubleshootng allows the assembly mechanic to arrive on site and meet the client with the required part in hand, correctng the problem straight away. This not only allows us to start troubleshootng faster, it also lowers travel costs. In the end, this may also reduce the amount of tme that the crane is not operatonal.