
3 minute read
A high strength low alloy steel alternative for tapered stress joints
Production tapered stress joint, 18m length.
Advertisement
For the construction and operation of oil production facilities, it is important to fnd the right balance between cost and safety. Weight and strength of the material used play a role in this. Recently, Schelde Exotech had a technological frst with the use of high strength low alloy steel for tapered stress joints.
ALL IMAGES COURTESY OF SCHELDE EXOTECH. WORDS BY ALFRED VAN AARTSEN, MATERIAL & WELDING ENGINEER (IWE) AT SCHELDE EXOTECH.
Tapered stress joints (TSJs) are used to connect the steel catenary risers (SCRs) to bottom-fxed or foating oil production facilities. Relatively a small part, when compared to the entire length of the pipelines, especially at the deepsea facilities in the Gulf of Mexico. Because of current, waves, and movements in case of foating facilities, the forces on the TSJs can be very demanding and may lead to fatigue of the material. The damage caused by this fatigue can be very severe for the facility as well as for nature.
A technological frst
Last year, Schelde Exotech (Vlissingen, the Netherlands) constructed high strength low alloy steel TSJs for one of their clients, Subseatec. A technological frst in the ofshore arena. In this project, Schelde Exotech made welding qualifcations, in several low alloy steel grades. After a full approval cycle, the actual production welding followed. The end-client of Subseatec will use the TSJs for connecting SCRs to a new to construct semi-submersible platform, which will be operating at a depth of approximately 2,400m in the Gulf of Mexico. Welding qualifcations started in Q1 of 2021 and involved the following low alloy steel materials: • Grade A508Gr.4 Cl.2, for forging with yield 100-120ksi (690- 827 MPa). • Grade A707Gr.3W, for forging with yield 80-100ksi (552- 690 MPa). • Grade API-5L-X65, for pipeline pup pieces, to be welded to the TSJ materials and to be connected ofshore to the SCR.
Competitive alternative
The A508Gr.4 Cl.2 low alloy steel, with its tensile and toughness properties, at the
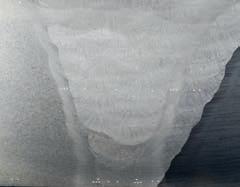
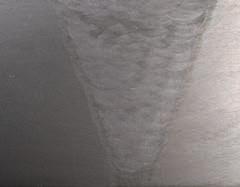
API-5L-X65 (left) welded to A508Gr.4 Cl.2 (right). A707Gr.3 welded to A707Gr.3
length and size supplied by Subseatec, provided a competitive alternative to the TSJ designs that are frequently used within the oil & gas industry. In case of sour-service demands, and approved by the end-user, the A508Gr.4 Cl.2 TSJ low alloy steel could be used, alloy 625 IDcladded. This was already done by Schelde Exotech for Subseatec and the same end-client with A182F22 low alloy steel in 2017, on six TSJs of 18m long.
The welding qualifcations made, were: • Clad welding of A508Gr.4 Cl.2 low alloy steel, intended for the ring grooves of the stress joint fange connection to the platform piping. The clad welding of the A707Gr.3W low alloy steel ring grooves were qualifed on earlier projects for this end-client. • Butt welding the SCR API-5L-X65 low alloy steel pup-pieces to a – A508Gr.4 low alloy steel forging; that was, more precisely, a post weld heat treatment butt weld and a ‘as-welded’ closure weld; – A707Gr.3 low alloy steel forging.
• Butt welding of A707Gr.3W to
A707Gr.3W, to construct the required length of the TSJ. The total length of the export joints is 26-30m.
Testing
All qualifcations were extensively tested, non-destructive and destructive with requirements based on a combination of the API-1104, DNVGL-ST-F101, and the design that was documented in the endclient’s specifcation. The destructive testing consisted of regular mechanical testing. For the butt welds, fracture toughness testing (crack tip opening displacement testing, CTOD) of the weld metal and the heat afected zones (HAZs) at -20°C and at 0°C was conducted. Of the total twenty sets of CTODs expected to do at time of ordering, Schelde Exotech had to execute only eleven sets as they could achieve the values required at 0°C through testing at the more stringent -20°C.
Quality statement
The fabrication took place in Q3 and Q4 of 2021. One of the challenges in this was to align and ft the parts of the export stress joints. After the welding and grinding of roots and caps of all the production welds, no adjustments or repairs were reported. Altogether, without a doubt, the qualifcation and production were a true achievement and a real quality statement for the fabrication and welding skills at Schelde Exotech.
i. exotech.nl
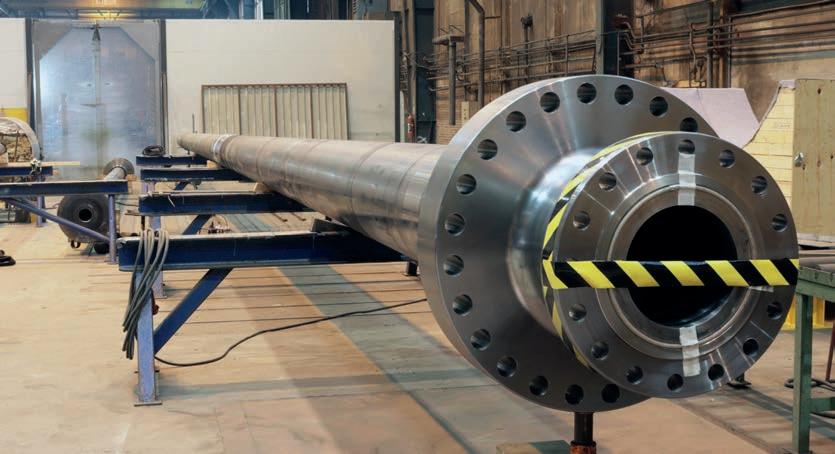