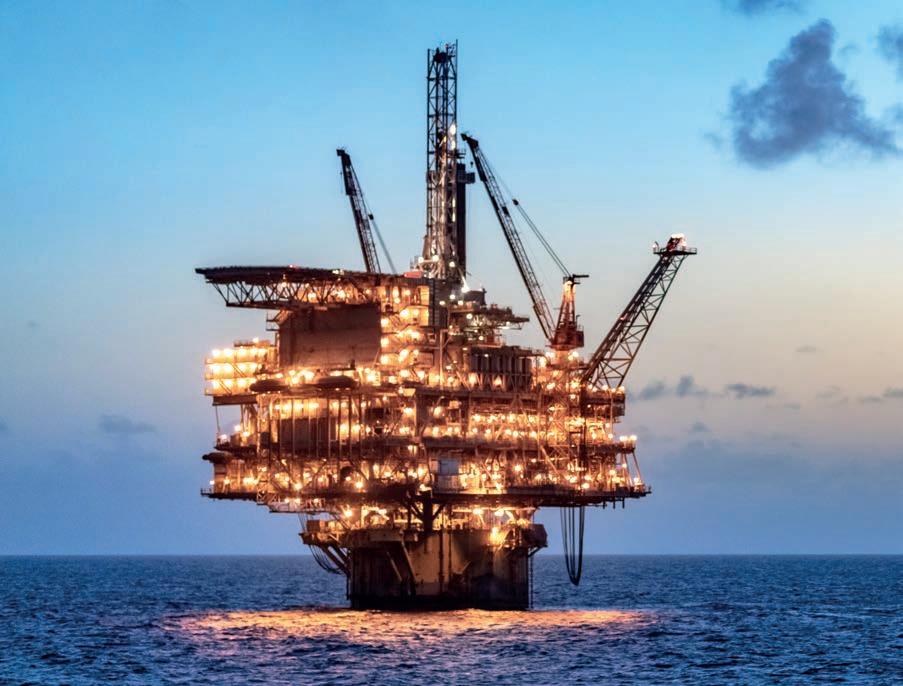
6 minute read
A balancing act
IT IS SIMPLY A GIVEN FACT. AT SEA, THE STRENGTH AND LIFETIME OF STEEL STRUCTURES ARE CONTINUOUSLY AFFECTED BY FORCES OF NATURE LIKE WIND, WAVES, WATER, SOIL, TEMPERATURE, AND SALT. THIS OFTEN RESULTS IN A COMBINATION OF CORROSION AND FATIGUE.
ALL IMAGES COURTESY OF TNO, UNLESS STATED OTHERWISE. Corrosion, even the smallest spot, can negatvely afect the fatgue strength of steel structures. Although corrosion in itself is not immediately threatening, in combinaton with the changing load and tension on steel structures caused by the circumstances at sea, it can accelerate the process of weakening steel as it acts as a potental fatgue crack initator. Research organisaton TNO (Delf, the Netherlands) has ample structural knowledge in the feld of ofshore oil & gas, ofshore renewables,
Advertisement
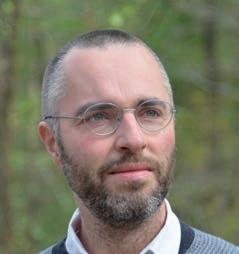
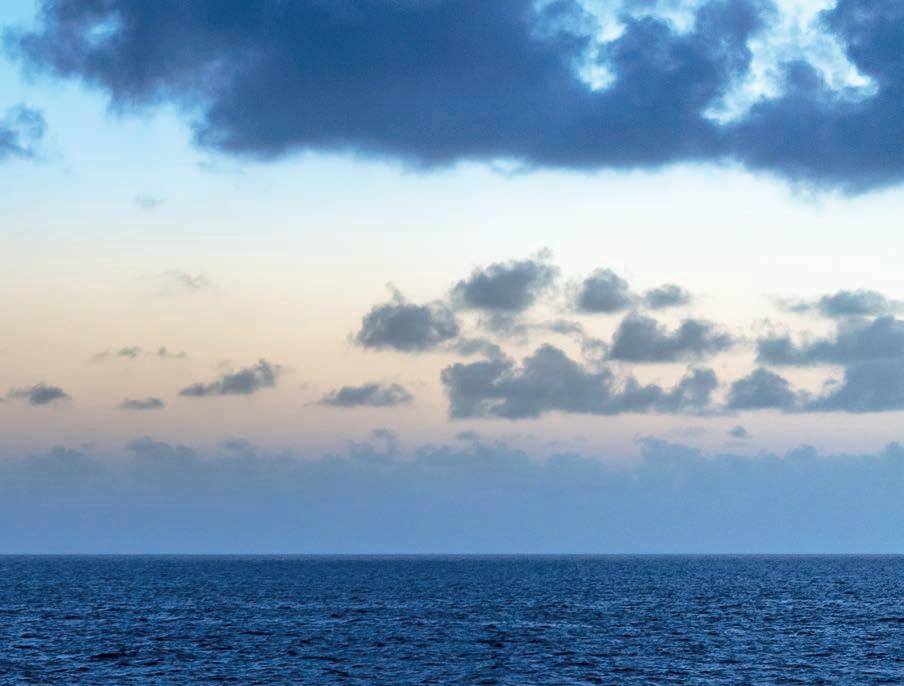
Richard Pijpers, Senior Scientist at TNO.
Photo courtesy of Photographic Services, Shell International.
and the maritme industry, and is one of the research organisatons that investgates the correlaton between corrosion and fatgue in steel structures.
Better safe than sorry
Both the oil & gas and ofshore wind industry make use of steel for their structures, as this is one of the most suitable building materials for ofshore use. However, according to Richard Pijpers, Senior Scientst at TNO, both industries in general terms have a diferent approach to using steel. “Corrosion protecton in many forms such as (paint) coatngs and cathodic protecton have been used for decades to limit negatve efects and to guarantee the assets’ technical lifetme at sea”, Mr Pijpers explains. “However, ‘beter safe than sorry’ is an important saying in the oil & gas industry. Operators and contractors not only look at the use of protectve measures and thorough inspectons and maintenance, they also use a conservatve approach when looking at building oil & gas platorms. They do not want to take even the slightest risk of a platorm failing due to a faw in the design. People work at many platorms, and there is also the risk of environmental disasters caused by oil spills. Therefore, they prefer to use broad margins for steel structures, which means they design structural components that are thicker than strictly needed. This improves the structure’s ability to withstand the natural forces at sea. The thicker the steel, the longer it will last.” He contnues, “A signifcant diference
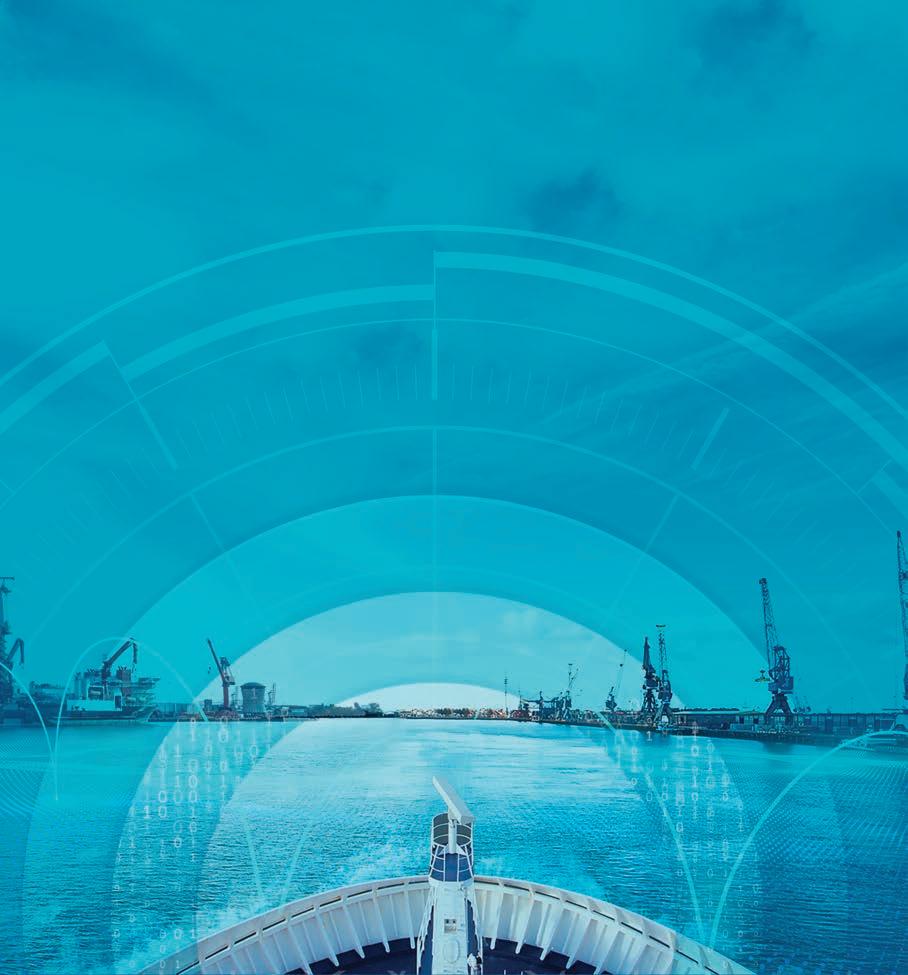
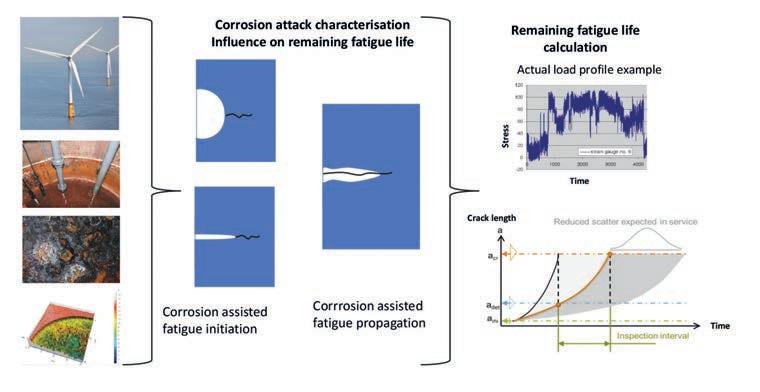
Corrosion – Fatigue approach from environmental conditions to assessment of pit growth rate to critical fatigue crack length.

Experimental setup for corrosion fatigue testing.
between oil & gas and the ofshore wind industry is the fact that oil & gas assets are ofen one-ofs, whereas ofshore wind farms consist of multple equal turbines with similar tower and support structures. This requires a cost-efcient constructon, especially in today’s highly compettve market. Furthermore, when compared with oil & gas assets, the consequence of a wind turbine failure is less severe than that of an oil & gas structure failing. Simply said: when an ofshore turbine collapses, the risk of people getng injured or the environment being damaged is small. Due to this lower risk, together with the cost efciency, ofshore wind operators look for a steel structure that is as thin as possible, whilst safeguarding structural integrity for a decent technical lifetme.”
Fatigue
It is obvious that the selected steel thickness for the structures will infuence their capability to withstand the environmental and operatonal conditons at sea. The safety of a steel structure is governed by the resistance of critcal connectons such as bolts and welds to the structural loading. “At sea, steel structures may be afected by material fatgue because of the impact of wind and waves”, Mr Pijpers elaborates. He contnues, “This fatgue, which can appear in the form of small cracks, is negatvely afected by corrosion. There will always be some level of corrosion at sea, even when coatngs or other types of corrosion protecton are used, as the mitgaton measures could be inefectve due to wear, damage, or unavailability. For asset owners, it is good to know when this corrosion will lead to an undesirable situaton based on acceptable structural reliability. When unnotced, small crack initatons can propagate untl ‘through thickness cracks’ result in severe problems. The challenge is fnding out the exact right tme to act. The challenge is to reduce material and mitgaton costs, while keeping the structures safe in operaton during their service life.”
Optimising effectively
TNO is one of the partcipatng partners in the Corrosion Fatgue Life Optmisaton (C-FLO) project. This project aims at developing and calibratng corrosion fatgue models to optmise the design and maintenance of monopiles. “In ongoing research projects,” Mr Pijpers states, “we are developing advanced models for the service life predicton of monopile foundatons. The research work evaluates the existng knowledge on corrosion and fatgue of representatve ofshore wind monopiles, including the efects of environmental conditons and countermeasures. We will build a model to describe the interacton of corrosion, including microbiologically infuenced corrosion, for example caused by the soil type in which the monopile is mounted, and fatgue. By using the new models, combined with existng feld data retrieved from the industry, we can adequately quantfy the efect of environmental factors on corrosion and the efectveness of corrosion protecton on ofshore wind energy structures, thus extending their lifetme.”
Lifetime extension
“With the right models and simulaton, we can help to improve the availability of steel structures throughout their entre lifetme, and even beyond”, Mr Pijpers says. “In the oil & gas industry, it is already common practce to extend the lifetme of assets to avoid expensive decommissioning. And in >>

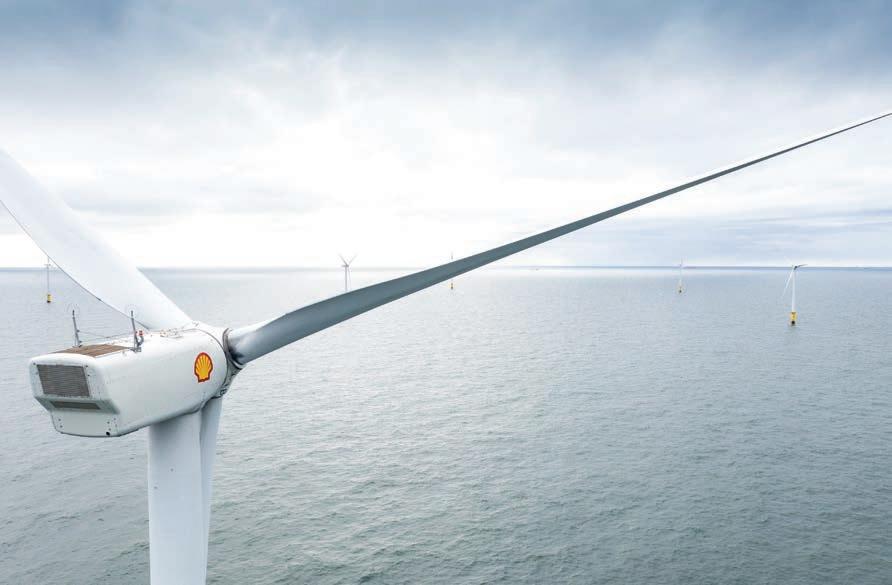
the ofshore wind industry today, research is being carried out on extending a wind farm’s lifetme. Turbines are growing both in size and output, and it would be nice to be able to install a new, bigger, and more efcient turbine on an existng foundaton. This obviously requires a well-constructed, conserved and maintained structure.” Although maintenance remains inevitable, much can be won in the design phase. “Each acton at sea costs money, tme, and can even be risky”, Mr Pijpers concludes. “Therefore, in designing ofshore steel structures, one should aim at reducing the amount of maintenance, without being too conservatve. However, one should also look at cost-efcient engineering, without losing sight on safety. It is in fact a balancing act between reliability and necessity, and we help to keep this balance in control.”
i. tno.nl
Offshore wind operators look for a steel structure that is as thin as possible, whilst safeguarding structural integrity for a decent technical lifetime.
TNO is one of the participating partners in the Corrosion Fatigue Life Optimisation (C-FLO) project, which aims at developing and calibrating corrosion fatigue models for optimising the design and maintenance of monopiles.
Photo courtesy of Photographic Services, Shell International.
Photo courtesy of SIF Group.