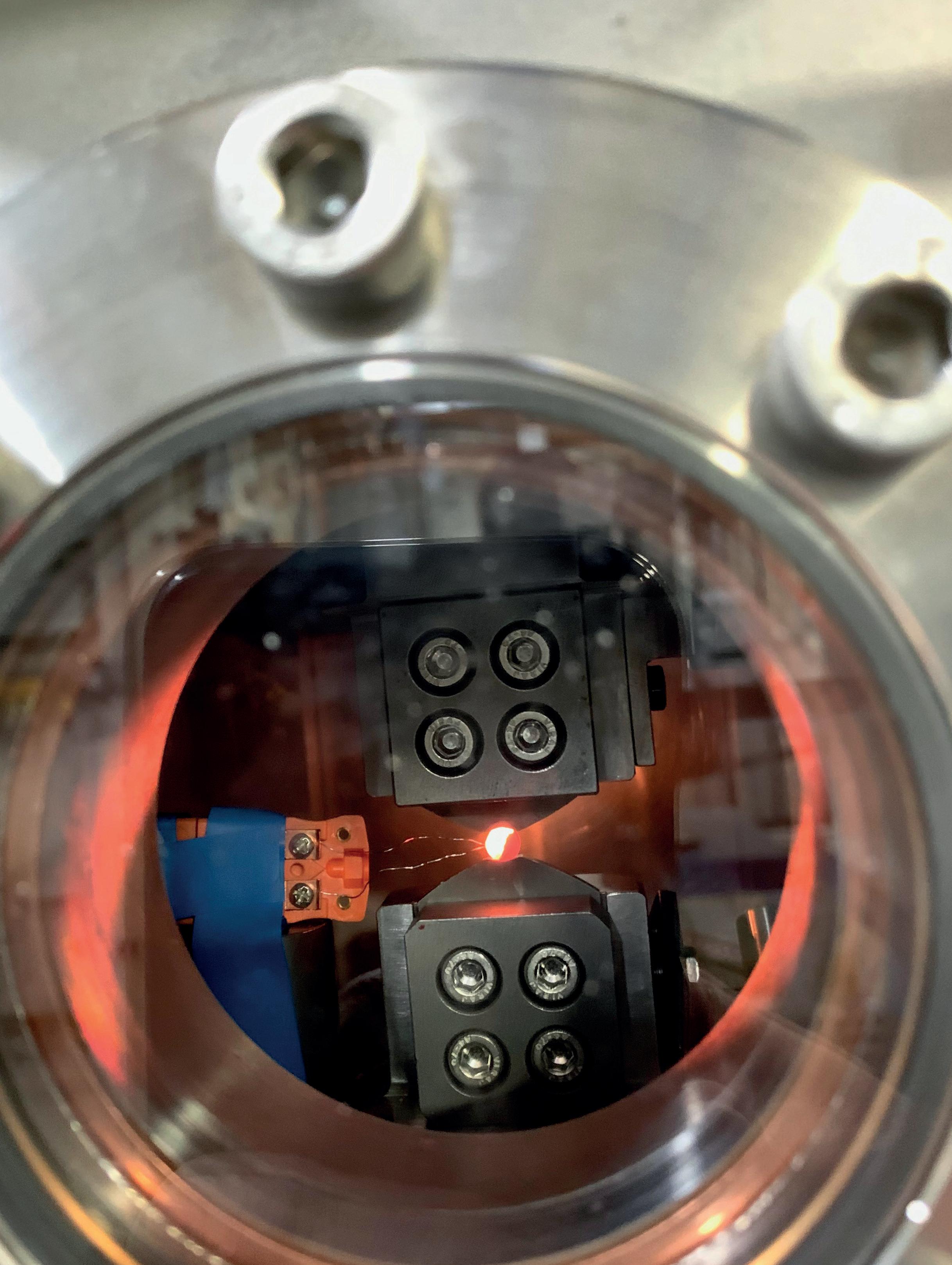
4 minute read
‘There is a crack, a crack in everything…’
Leonard Cohen ‘Anthem’
Almost every material is cracked to some degree, and we need to live with these cracks. The challenge, for an engineer, is to determine the conditions that can cause a crack to grow or propagate. Professor James Marrow (Professorial Fellow in Materials Science at Mansfield; James Martin Chair in Energy Materials at Oxford) elaborates on his current research.
The concept of how to live with cracks in materials underlies the field of ‘structural integrity’, also called ‘fracture mechanics’. Determining how cracks propagate is of vital importance, since this information can be used to predict a structure’s strength and the loads it can sustain over its lifetime. Cracks can grow by many different mechanisms, of which brittle fracture, fatigue, stress corrosion, thermal shock and corrosion fatigue are just a few. Understanding how cracks develop within a material’s microstructure also allows the design of damage-tolerant materials or optimisation of the material’s manufacture.
Brittle fracture is an example of ‘applied thermodynamics’. When a force is applied to a cracked body, it deforms and elastic strain energy is stored – rather like in a coiled spring. The crack tip concentrates force (or stress) in a local region with very high amount of strain. Thermodynamically, the crack tip can only propagate into this region if that would cause an elastic relaxation of sufficient energy to increase the crack’s surface area. Other crack propagation mechanisms, such as ductile fracture, fatigue and stress corrosion are not so simply described by thermodynamics. Nonetheless, the crack tip conditions necessary to crack propagation are still determined by the surrounding elastic strain field, so calculation and measurement of the ‘singularity’ of the crack strain field underpins virtually all of fracture mechanics.
My research group generally studies cracks and their singularities in materials used in energy generation and storage. These are as diverse as metals and alloys used in nuclear fusion, the graphite in nuclear fission reactors and ceramic composites for their potential replacements, and novel ceramic electrolytes for future lithium batteries. We are driven by the need for designers, operators, and regulators to have high confidence in the safe performance of the material, and so avoid over-conservatisms that can have adverse economic consequences on lifetime and operating costs. This is important if these energy systems are to have potential to contribute to net-zero carbon global goals. One challenge is that the properties of materials can change over their lifetime, with effects difficult to predict. Some of our most exciting results have come from experiments at the Diamond Light Source (the UK’s national synchrotron X-ray science facility) and the ISIS Neutron and Muon Source (at the STFC Rutherford Appleton Laboratory), both located near Oxford at Harwell.
Graphite – critical for the UK’s Advanced Gas-cooled Reactors (AGR) – is one example. It is inevitable that elements of the AGR graphite core will crack as the reactor ages, with potential effects on safe shutdown in the event of an earthquake: a possibility that must be anticipated, even in the UK. Addressing this problem involves monitoring the reactors, supported by predictive modelling of the evolution of crack populations and careful assessments of their consequences. Our work on the fracture mechanics of graphite is just one small part. We have used X-rays and neutrons to study graphite microstructure and observe in situ their deformation and fracture when mechanically loaded. Diffraction and 3D tomographic imaging have allowed us to quantify the stress and strain fields with high spatial resolution. This has helped us understand how nonlinear deformation contributes to the high toughness of graphite by relaxing the magnitude of the stress singularity. We are now designing novel test methods to qualify the new graphites required for next-generation nuclear fission advanced reactors.
We have also used X-ray tomography and diffraction to address a significant challenge in solid-state lithium-ion batteries. Cracking of the ceramic electrolyte creates pathways for short-circuits that limit the maximum energy storage capacity and lifetime. In situ studies have revealed how cracks can nucleate, and the complex interactions between the movement of lithium within the electrolyte structure and the propagation of cracks. These insights now guide strategies for the design of damage-tolerant electrolytes.
X-rays and neutrons are not the only tools available to study cracks. Interactions between electrons and the crystal structure of materials allow stresses to be mapped at high resolution. We are now applying analyses of backscattered electrons (HR-EBSD) to cracks to quantify their singularities at very small length scales. Ultimately, we will study the fracture properties of interfaces within materials microstructures, and how they are affected by environmental factors such as irradiation, oxidation and temperature. Our aim is to support predictive modelling of their lifetime behaviour, allowing us to live with these cracks confidently and safely.
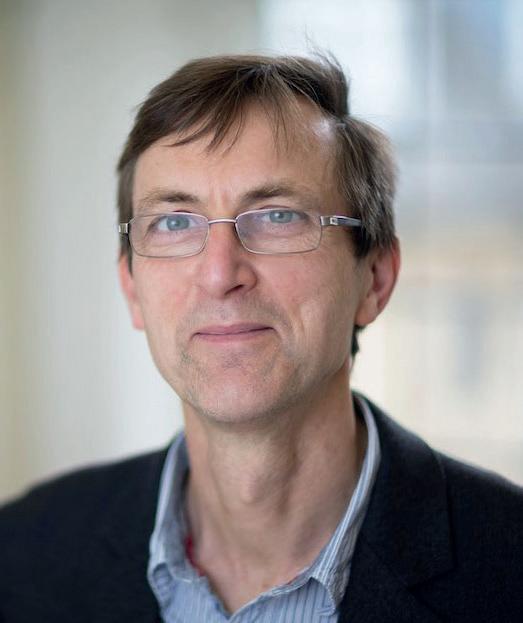