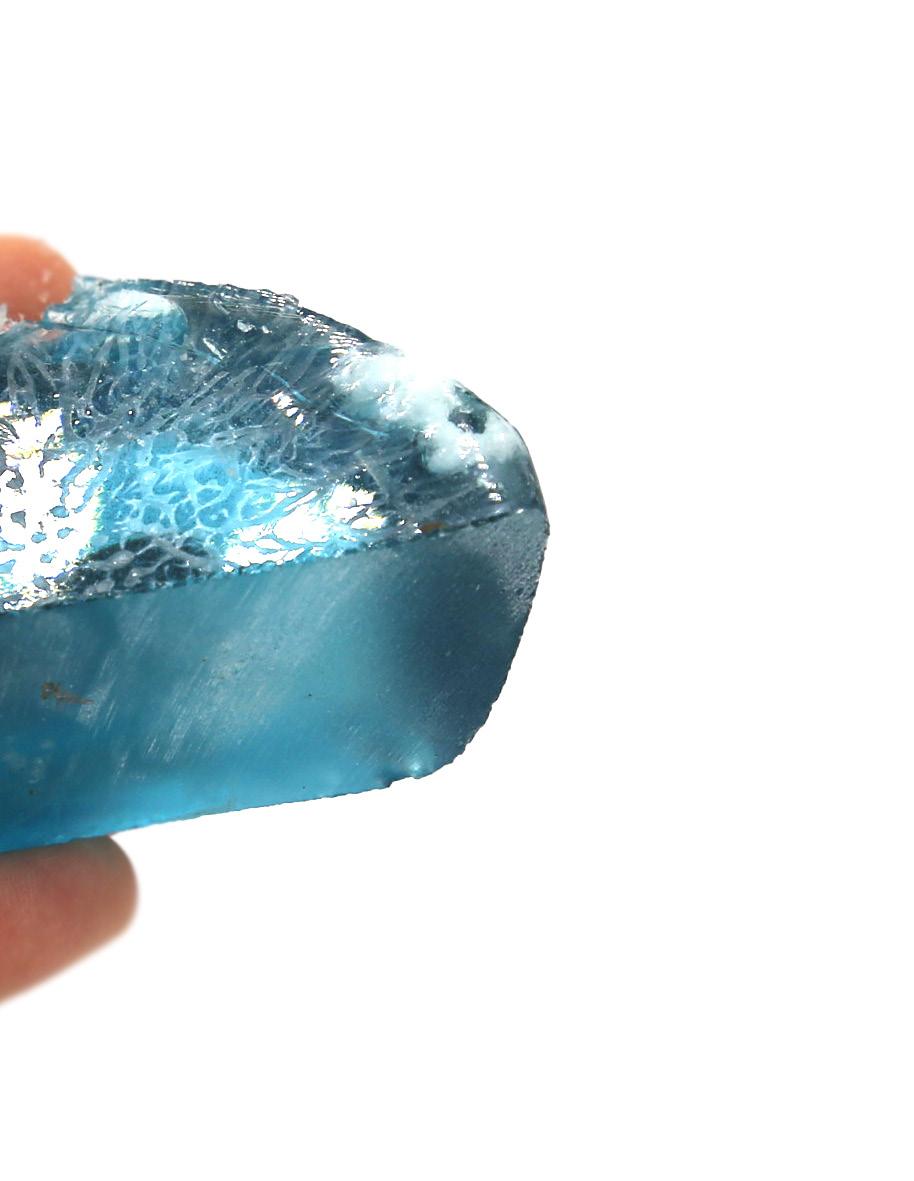
5 minute read
Glass
from Zebra Glass
Local Glass Production
The Great Lakes region has a very long history of glass making, through nearby large- and small-scale glass production and manufacturing.
Advertisement
“Michigan ranks third in the US in industrial sand production” a significant proportion of it supplying the glass industry. Libbey Glass has been operating in the region since 1888 when it moved to begin production of Edison light bulbs [22].
Automotive glass has been produced in factories throughout the upper and lower peninsulas of Michigan to supply the automobile industry. [23]
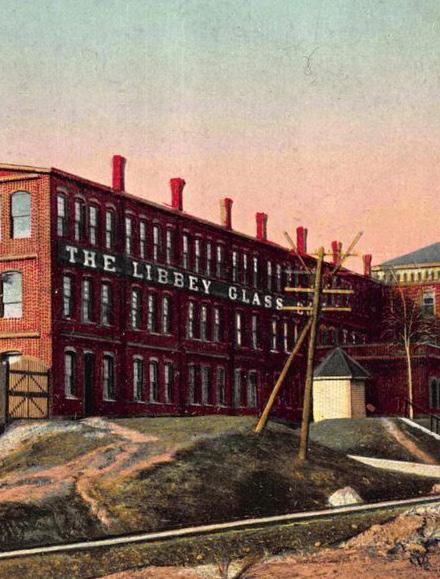
Material Chemistry

SiO2 (Silica)
A former (silica) from sand which constitutes 70- 75% of the mix by weight “According to Dr. Glenn K. Lockwood, a ceramic engineer, ‘At high temperatures, Silica liquefies into a very viscous melt that generally impedes crystallization kinetically when it goes below its melting temperature.’…”
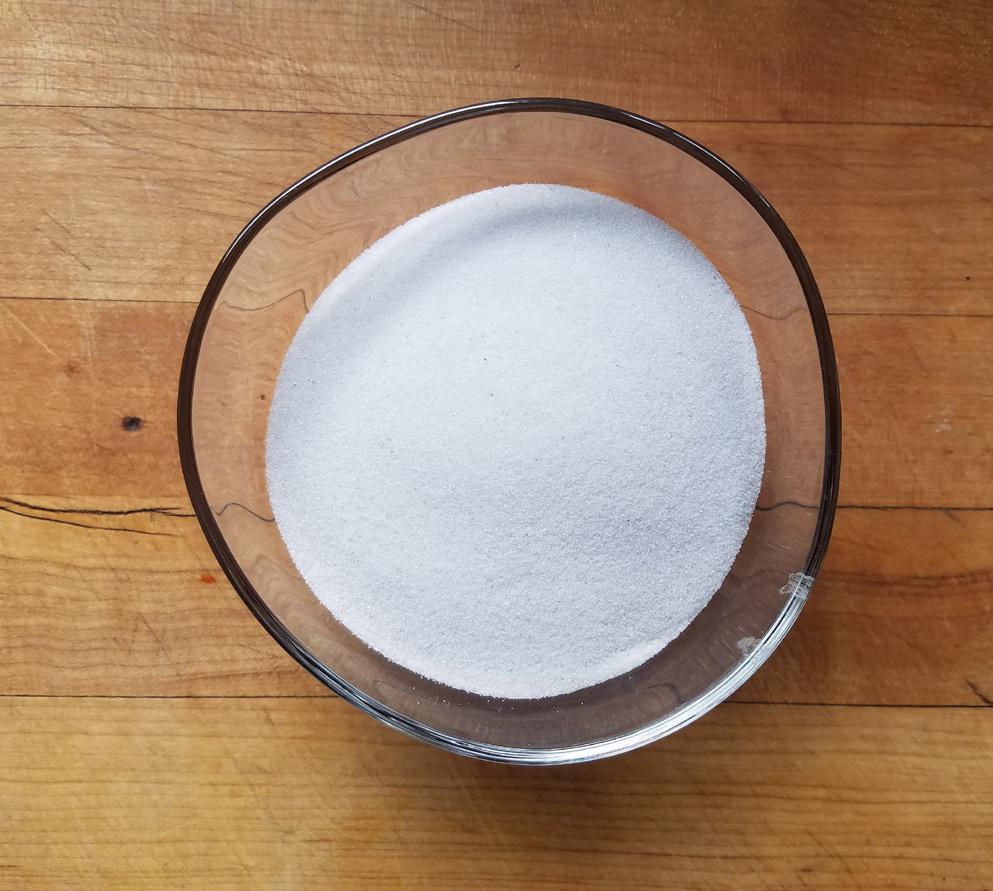
CaCO3 converts to CaO (Lime)
A stabilizer (lime) or calcium oxide makes up 10- 15% of the mix “…Although an excess of calcium oxide to a silica melt will cause devitrification, additions of small amounts of lime stabilize the glass melt with respect to water, fixing the problem of water solubility introduced with the soda component.” [24]

NaHCO3 converts to NaO (Soda)
A flux (soda) or sodium oxide makes up 12-16% of the mix. “…helps reduce the melting temperature of the silica. However, its addition also makes the resulting glass soluble in water.” which necessitates…. The final % is made up of balancing agents and
colorants.
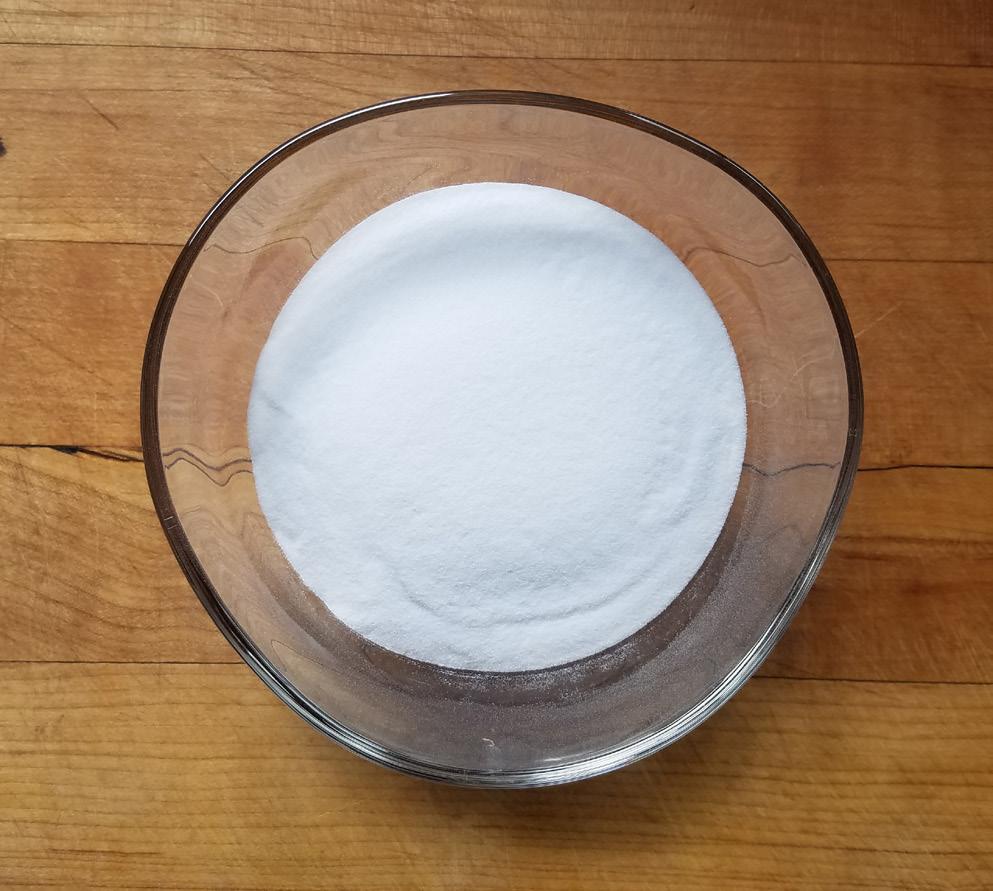
Processing

To process zebra glass we begin by collecting zebra and quagga mussel shells off of the beaches of Muskegon and Lake St. Clair, where the species was first introduced in 1989. Then the shells are boiled to remove excess organic matter. The shells are then ground into a fine texture with a mortar and pestle. Lastly, the newly ground shells are sifted to ensure a fine, uniform consistency.
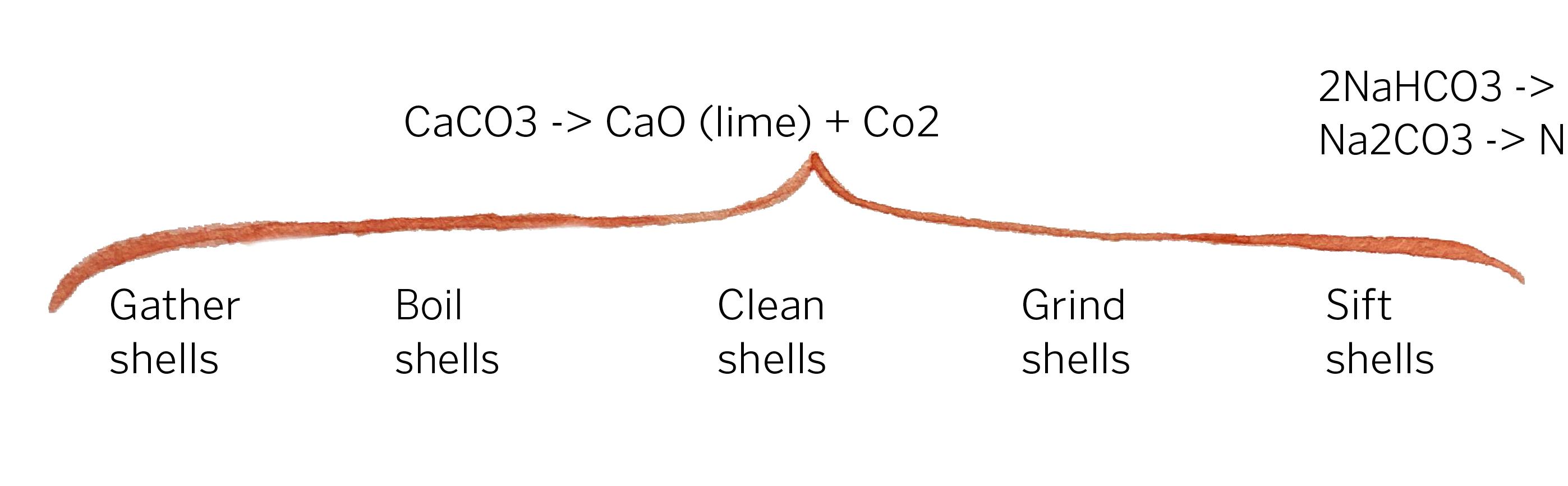
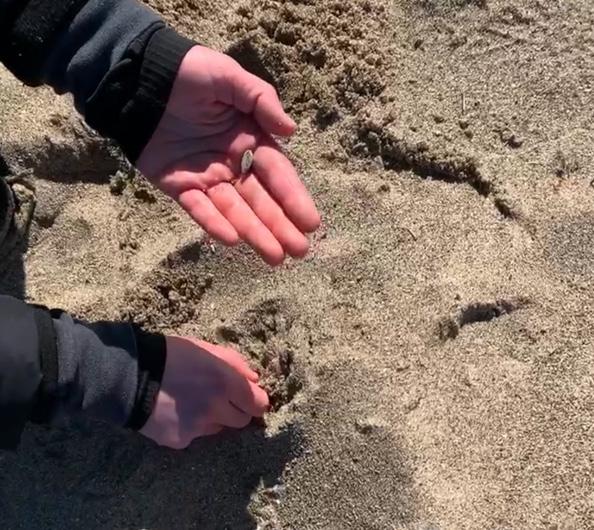
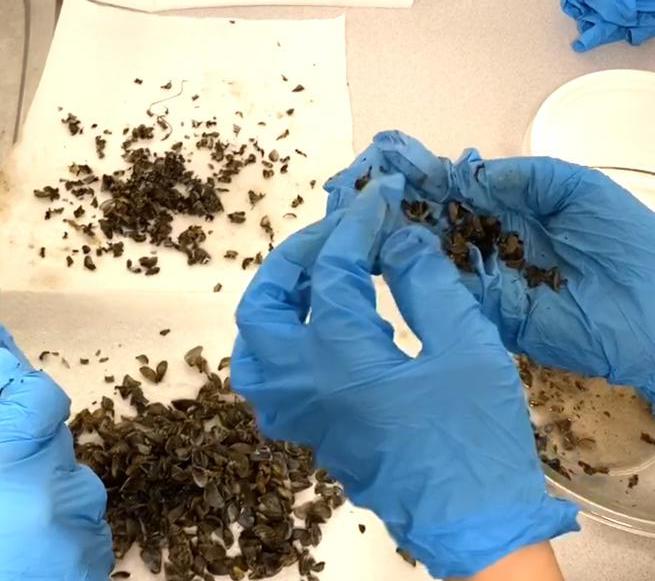



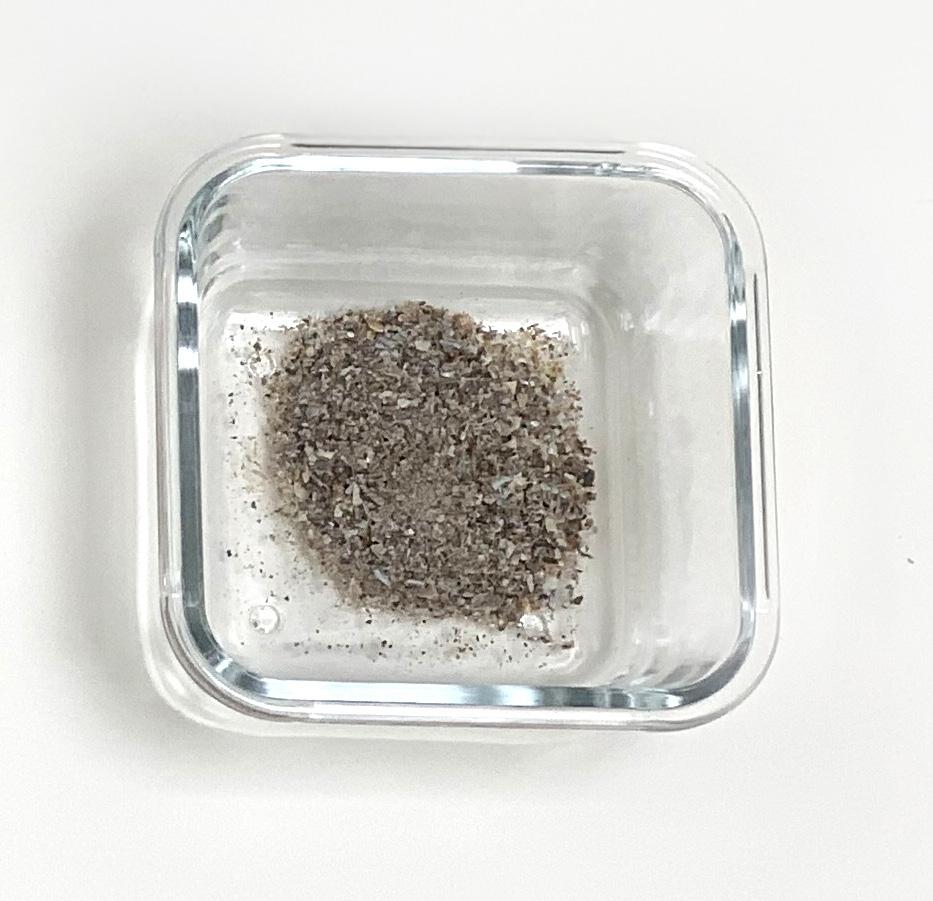
Batching

Two of our main ingredients Sodium Bicarbonate (NaHCO3) and Calcium Carbonate (CaCO3) go through several chemical reactions, losing a great deal of mass in CO2 and H2O as they transform into Soda (Na2O) and Lime (CaO). In order to have the correct proportions of final ingredients carried out batching calculations using molar masses.
We decided to try two recipes at the extremes of the (flux&stabilizer)/(silica) range for soda glass from our research. The stabilizer/flux ratio was held fairly constant for this experiment…
Recipe 1 high flux/stabilizer, low silica: (15% Lime, 15% Soda, 70% Silica) corresponding to (20% mussels, 30% baking soda, 51% sand)
Recipe 2 low flux/stabilizer, high silica: (12% Lime, 13% Soda, 73% Silica) corresponding to (16% mussels, 27% baking soda, 57% sand)
Recipe 1

Recipe 2
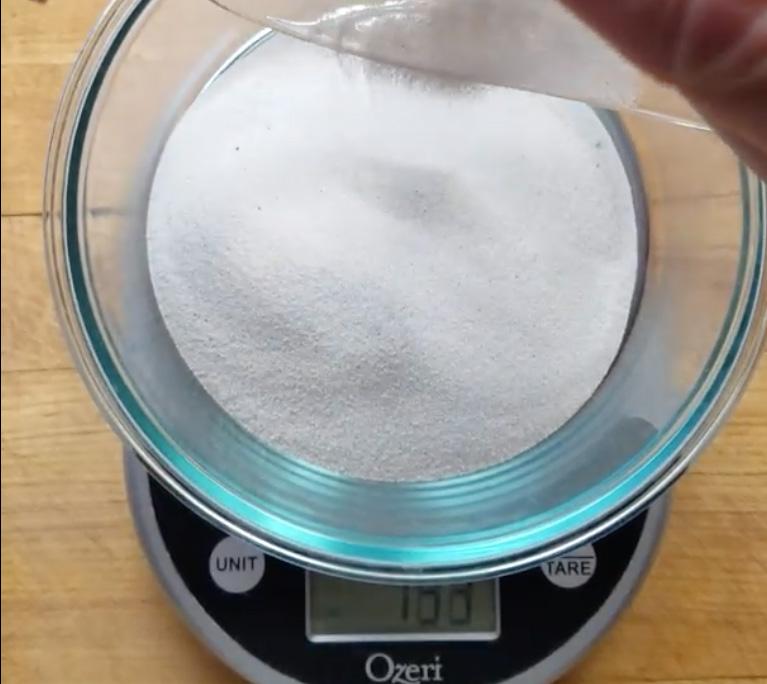
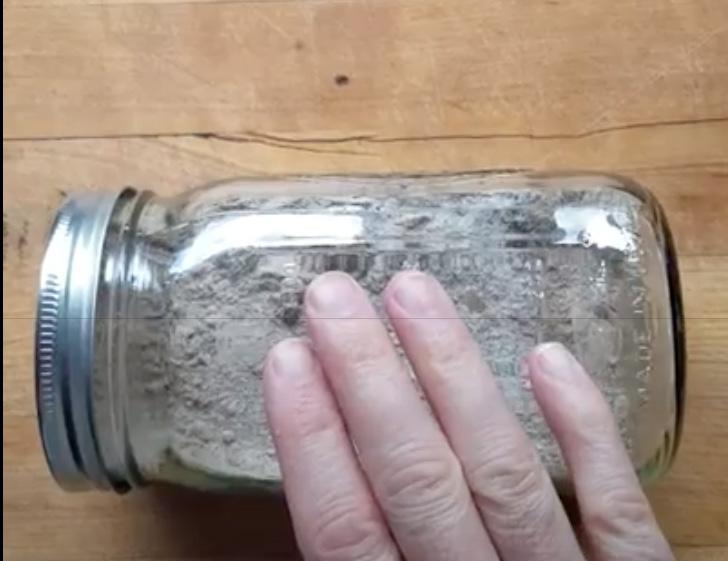
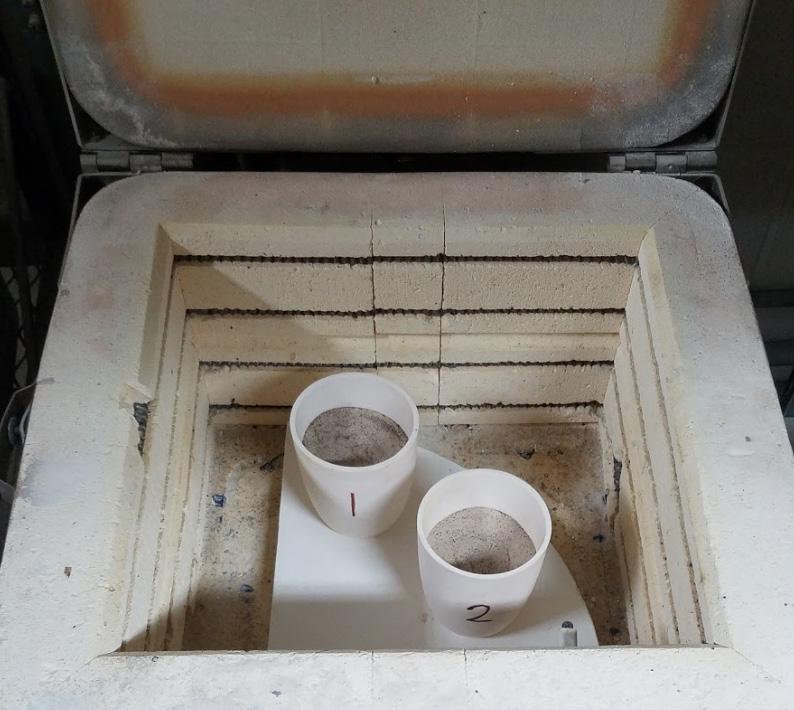

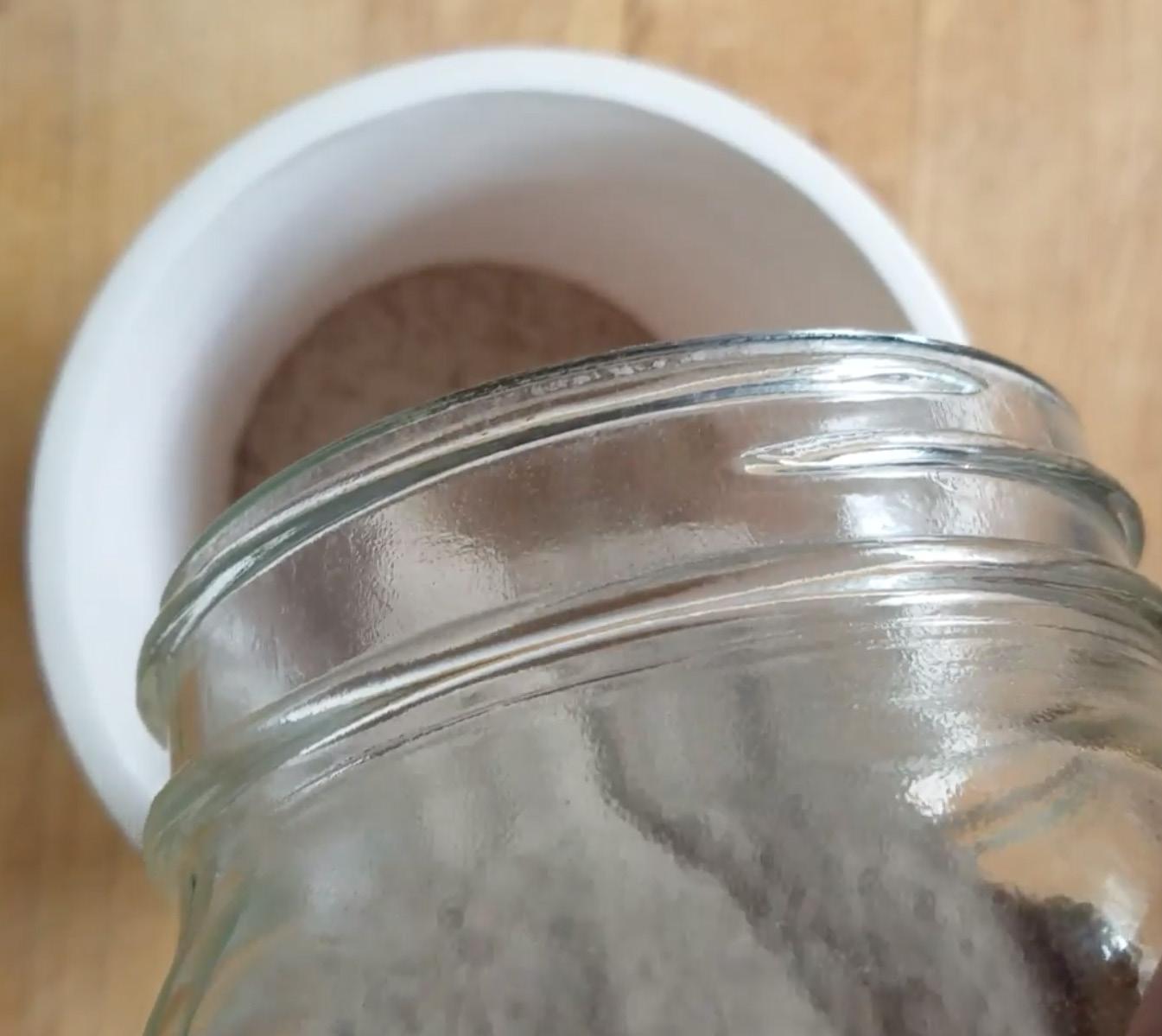
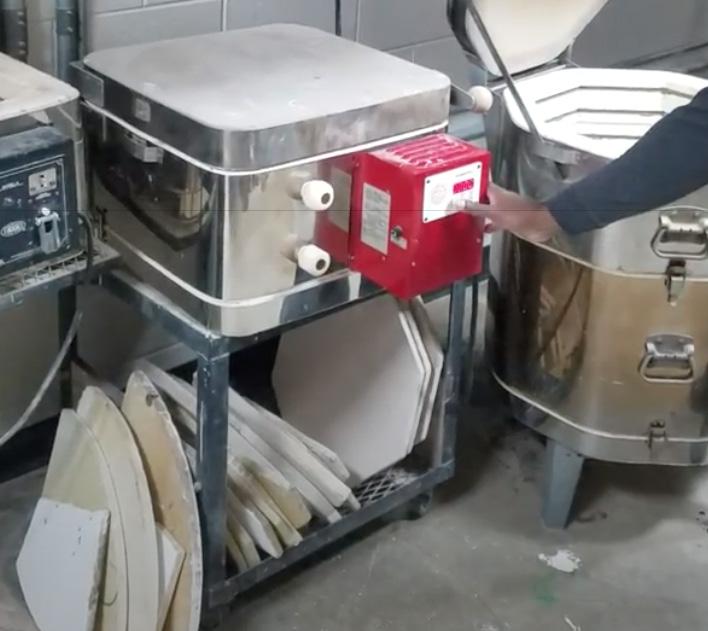
Firing
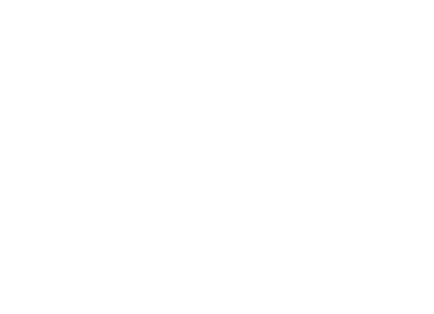
Firing temperatures and ramp rates are crucial to avoid boiling over of the melt which can affect batch mix proportions and potentially cause damage to the kiln. For our initial 2 recipes we ramped up at 3C/min pausing for an hour at each chemical reaction temperature to allow for the controlled venting of CO2 and H2O. We then held for 5 hours at our melting temp. After melting we ramped quickly down through the vitrification range at 10C/min to the anneal range holding at 480C for one hour and then ramping down at .5C/min until 370C at which we ramped to ambient at 3C/min.
1000 C
Ramp to 100 C and hold 1 hour
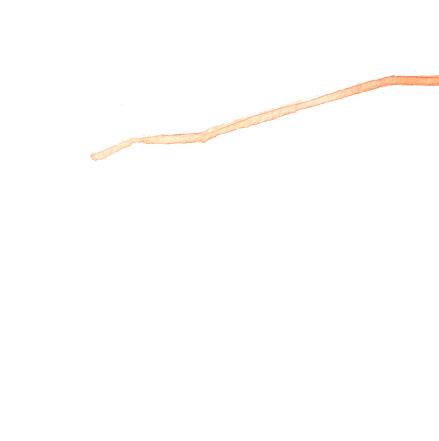
At 100 degrees C sodium bicarbonate is converted to sodium carbonate, H2O, and CO2. An hour hold prevents rapid steam formation and bubbling.
851 C 1000 C
Ramp to 851 C 3 C/min hold 1 hour
At 851 degrees C Sodium carbonate is converted to sodium Oxide (soda) and CO2. An hour hold prevents bubbling.

Ramp to 1000 C 3 C/min hold 1 hour
At 1000 degrees C Calcium carbonate is converted to calcium Oxide (lime) and CO2. An hour hold prevents bubbling

1300 C
480 C
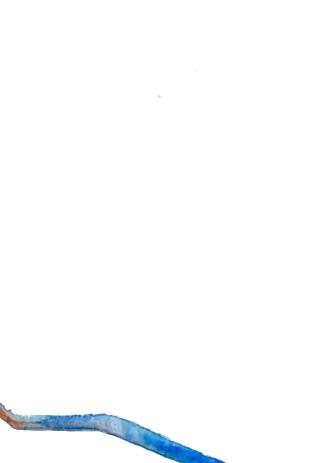
370 C
Ramp to 1300 C 3 C/min hold 5 hours

Full melt occurs at 1300 C. A 5 hour hold ensures full melt and homogeneity.
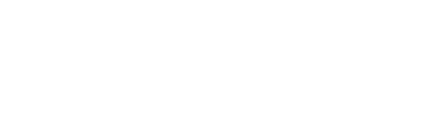
Ramp to 480 C 10 C/min hold 1 hour
Quickly transitioning through 480 C prevents vitrification and crystallization
Ramp to 370 C .5 C/min
Slowly transitioning from 480 C to 370 C anneals the glass preventing internal stresses that can lead to spontaneous explosion
Ramp to ambient 3 C/min 21 hour total cycle
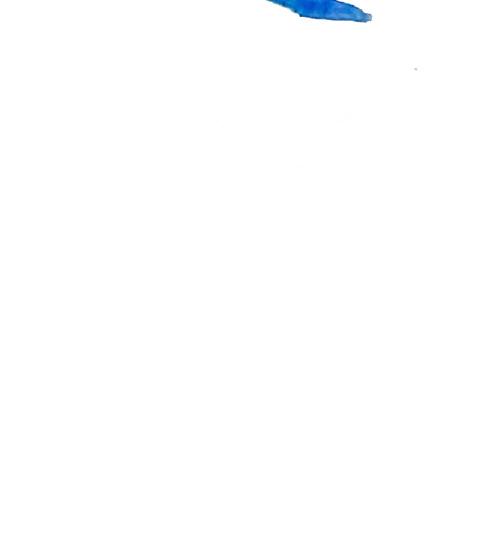
After reaching max temperature the kiln slowly ramps down. Total cycle time is approximately 21 hours
Bauccio, 1994 M.L. Bauccio (Ed.), Engineered Materials Reference Book (second ed.), ASM International, USA (1994)
H.G. Pfaender Schott Guide to Glass, Chapman & Hall, London (1996)
