
26 minute read
Robotland fait bouger votre monde
<< ROBOTLAND FAIT << ROBOTLAND FAIT BOUGER VOTRE BOUGER VOTRE MONDE ! >> MONDE ! >>
L’ENTREPRENEUR LUC VAN THILLO INVESTIT PLUSIEURS MILLIONS DANS UN PARC TECHNOLOGIQUE POUR LES JEUNES
Advertisement
Automation Magazine a eu l’opportunité de visiteur en primeur le parc Robotland à Essen. Le rêve du créateur et propriétaire Luc Van Thillo est que les jeunes prennent goût à la technologie et s’orientent vers un métier technique. Suite à l’épidémie corona, les portes sont fermées mais nous vous présentons les lieux sur papier.

Luc Van Thillo est le créateur de ce parc de 1,5 hectare dédié à la technologie, une initiative unique au monde.
IMAGE: Wim Daneels Luc Van Thillo a bien gagné sa vie avec son entreprise d’automatisation AVT et il sait combien il est difficile de trouver du personnel qualifié et motivé. « Quand on parle de technique, les gens s’imaginent des mains sales. Ce n’est plus le cas depuis longtemps. Quand j’expliquais jadis aux sollicitants que notre technologie permettait de réaliser des pièces pour la fusée Ariane, l’intérêt était là. Le monde technique a du mal à recruter du personnel. Je veux aider l’enseignement à solutionner ce problème et je veux motiver les jeunes à se tourner vers les études techniques. »
Luc Van Thillo a transformé l’ancien hangar de la douane à côté de la gare d’Essen en un parc technologique qui abrite des bras robotisés, des grues, des jeux pneumatiques et hydrauliques. Tout est interactif parce que regarder est ennuyant. « Faire des expériences est tellement plus amusant. Ici, tout est centré sur la technologie, les robots et le mouvement. L’apprentissage doit être un moment de plaisir, les jeunes ont le sentiment d’apprendre quelque chose de concret. Nous avons en Belgique de nombreuses personnes créatives et flexibles qui savent tirer leur plan. Un travailleur en Chine attend ses instructions, nous, nous sommes plus dans la prise d’initiatives », poursuit Luc Van Thillo.
Une équipe de 15 instructeurs explique le fonctionnement des diverses configurations exposées. Il y a le fonctionnement des engrenages, la loi de Bernoulli, l’utilité d’une tarière à spirale, le principe des poulies pour déplacer des charges, l’utilisation de l’air comprimé et de l’hydraulique, le fonctionnement des capteurs, jusqu’à l’impact futur de l’IoT, … Les visiteurs découvrent les dernières innovations technologiques dans le domaine du transport et des robots.
Il est possible de monter dans le cockpit d’un simulateur d’avion, de faire du vélo dans le Grand Canyon en en réalité virtuelle, des tours d’acrobatie avec un drone, de piloter une chargeuse compacte, une mini-excavatrice, une grue à grappin ou d’actionner un bras robotisé pour assembler une voiture… Vous pouvez discuter et danser avec des robots humanoïdes, qui scannent votre visage et estiment votre âge.
A Robotland, l’interactivité et le plaisir sont centraux. Luc Van Thillo: « Ici par exemple, les visiteurs peuvent colorier un dessin avec des véhicules. Lorsqu’ils positionnent le dessin sous un projecteur, les véhicules colorés sont enregistrés dans un petit film qui est projeté sur un grand écran. » Un peu plus loin, il y a une cage avec un gardien de but et un ballon que vous pouvez lancer avec de l’air comprimé. Sur un grand écran, il y a une tour avec des boîtes numériques que vous pouvez faire tomber avec un véritable ballon de football. Tous ces exemples expliquent le fonctionnement des capteurs.
A l’extérieur, deux wagons attirent le regard. Luc Van Thillo les a achetés à la SNCB et les a décorés de graffiti. Un des wagons abrite un simulateur de train, l’autre sert de local de classe aux écoles d’Essen.
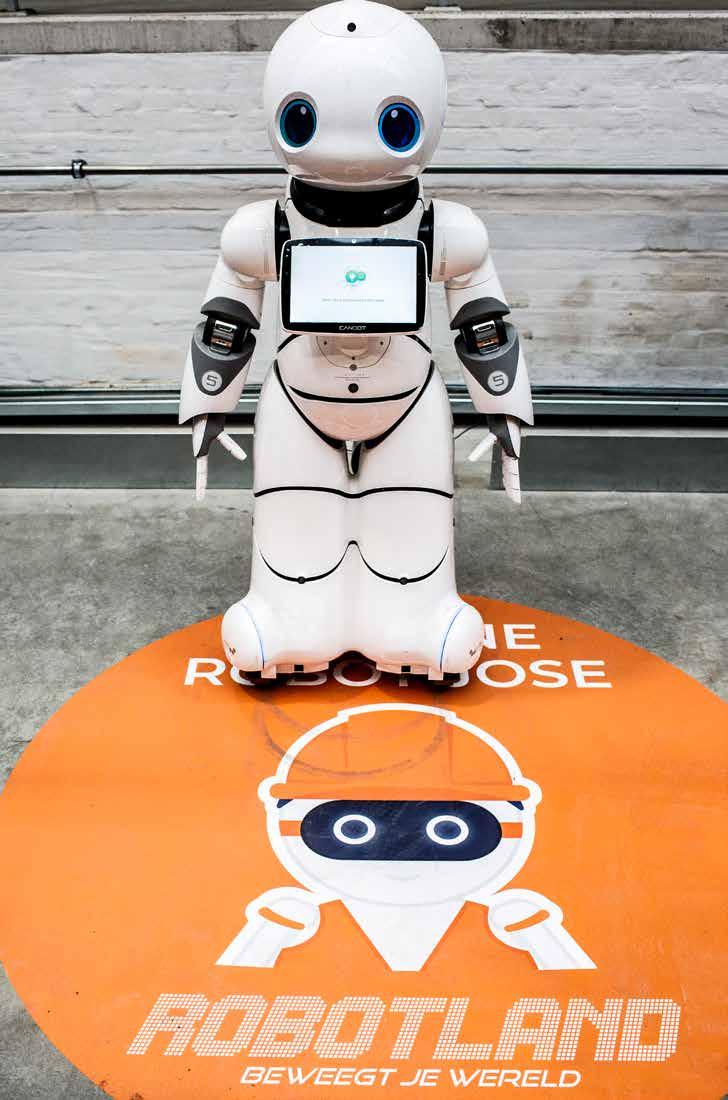
À partir du 28 décembre Robotland ouvrira ses portes.
Les robots humanoïdes scannent votre visage, contrôlent votre bracelet, déterminent votre âge, préparent vos boissons et vous les apportent.
La différence avec Technopolis est que le parc de Malines est axé sur les sciences tandis que Robotland s’intéresse aux techniques de transport, explique Luc Van Thillo. « Nos configurations montrent comme les choses se passent dans le monde de l’entreprise. Nous avons divisé le site en cinq secteurs : le transport sur l’eau, le rail, dans les airs et le transport intérieur. »
Certains éléments exigent le respect de règles de sécurité comme le port d’un casque ou de chaussures de sécurité. « Tout comme c’est le cas dans une entreprise chimique, les jeunes prennent cette habitude. Au début de la visite, un film sur la sécurité est diffusé. Après avoir répondu correctement aux questions, les visiteurs peuvent accéder au parc avec leur bracelet. »
D’après Luc Van Thillo, le site s’adresse aux jeunes âgés entre 10 à 11 ans jusqu’à 14 ans. « Via notre programme, nous proposons de l’émerveillement, de l’engouement, de l’expérience et beaucoup de plaisir, de 4 à 99 ans, à vivre en famille ou dans le cadre d’une sortie scolaire. Robotland n’est pas un musée mais un véritable parc interactif. Une visite à Robotland s’intègre parfaitement dans un programme de cours. Les élèves peuvent apprendre tellement de choses sur les techniques de transport en s’amusant. »
Robotland veut aussi collaborer avec les universités et les hautes écoles. « L’objectif est que les étudiants d’un master viennent ici effectuer des recherches pour leur thèse et tester de nouvelles idées. Vous voyez ce Zeppelin suspendu? Sera-t-il plus tard une manière durable de délivrer les achats commandés en ligne? J’espère qu’une des techniques développées ici percera un jour. » L’entrepreneur est toujours immergé dans la technique et de nombreuses configurations exposées dans le hangar sont le fruit de sa créativité, comme cet exemple ludique pour apprendre à pomper des liquides dans et hors d’un bateau et la machine qui envoie des avions en papier sur une cible. Luc Van Thillo ne manque pas d’inspiration.

Dans ce splendide hangar de la douane, où un Zeppelin est suspendu, il est possible de faire voler un drone (dans une cage). Assemblez votre voiture avec le bras robotisé de KUKA.

Le système de levage sous vide déplace des blocs lourds. Pourquoi ne peut-on pas lever un bloc de béton avec une corde et une poulie, et bien avec cinq poulies ?
Vous rêviez de ranger des conteneurs dans un cargo avec une grue? A Robotland, vous pouvez charger tout un bateau de containers. En remplissant les cuves d’eau – ou en les vidant – vous apprenez à répartir la charge dans le bateau.
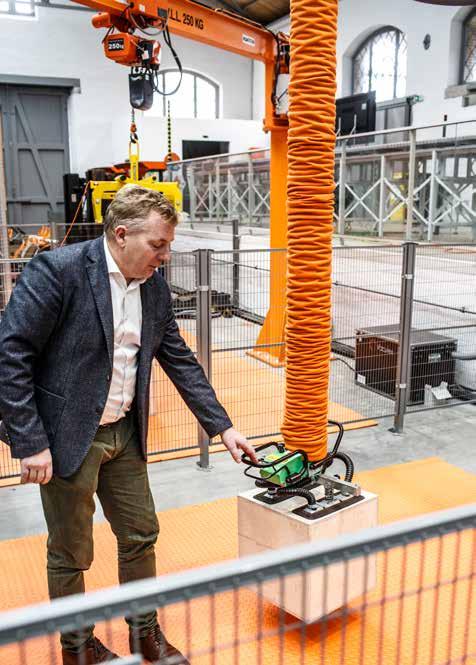
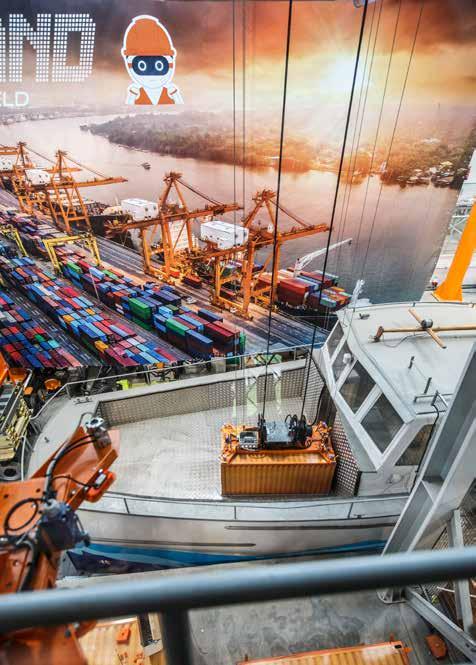
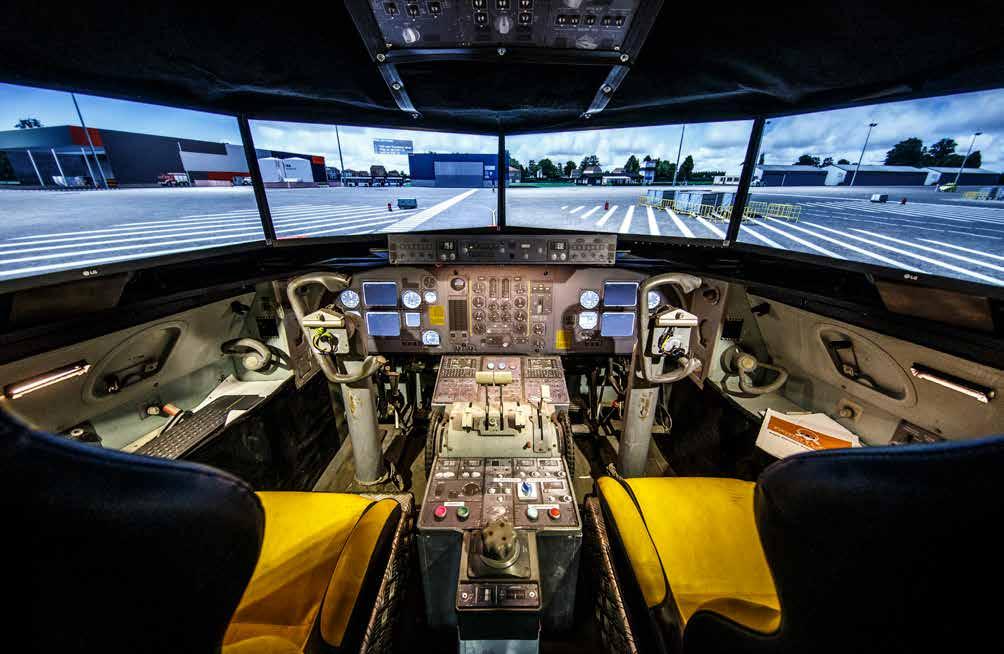
Vous pouvez atterrir à l’Essen International Airport avec votre Fokker 50 via le simulateur d’avion de Robotland.
Améliorez votre technique de frappe et marquez des points comme un Diable rouge. Les capteurs et l’air comprimé de SMC veillent au tir parfait du ballon. A l’extérieur du parc, les visiteurs peuvent piloter des chargeuses compactes et articulées, une mini-excavatrice et des segways, un drone grandeur nature, tester le simulateur dans le train, … un petit circuit est prévu et les enfants peuvent s’essayer à la conduite d’un aéroglisseur. Enfin, le parcours pour les chariots élévateurs est parfait pour l’organisation de formations.

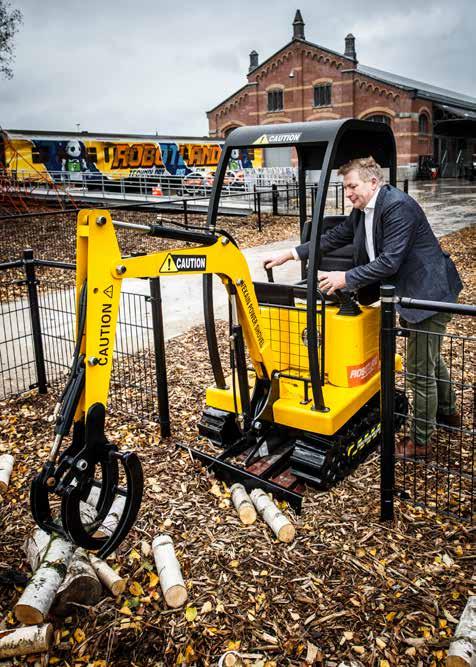
LUC VAN THILLO: ÉLEVEUR DE LAPINS ET PROPRIÉTAIRE DU CLUB DE FOOTBALL SK LIERSE
Luc Van Thillo (51) est né à Essen et est père de trois enfants. Il s’est fait connaître via son entreprise Automatiseringen Van Thillo (AVT), et peut se targuer d’une très belle carrière.
Luc Van Thillo a étudié l’électromécanique et fut programmeur chez Siemens. « Je suis issu d’une famille ouvrière, je suis né et j’ai grandi à Essen. Pour pouvoir vivre des terres agricoles, j’ai élevé des lapins. Lorsqu’en 1993, les agriculteurs sont face au ‘Mestactieplan’, j’ai construit une machine de traitement du fumier à l’échelle d’une ferme. Plus tard, j’ai vendu le brevet à un investisseur. J’ai joué à l’inventeur dès mon plus jeune âge. J’ai démonté les appareils photos de mon père pour voir comment ils fonctionnaient. Hélas, je n’arrivais pas toujours à les remonter correctement. » (rires)
En 2001, Luc Van Thillo fonde son entreprise AVT. « Pour les PME, nous construisions des tableaux électriques, installions des convoyeurs à bandes, des bras robotisés, bref tout ce qui pouvait automatiser la production. Nous nous sommes développés comme cela, commande après commande. Plus tard, j’ai repris la division européenne d’Aerogo. Nous construisions alors des machines pour déplacer des pièces lourdes, comme des avions et des trains. Tout ce qui était lourd et encombrant était déplacé avec nos coussins d’air. Nous étions même actifs en Chine. » L’entrepreneur inventif a vendu son entreprise à VINCI.
Luc Van Thillo est aussi le président et propriétaire du club de football SK Lierse. Il investit dans les entreprises notamment actives dans la construction métallique. Robotland est un projet privé ambitieux, qu’il finance entièrement. Le hangar de la douane à Hemelrijk, sous bail emphytéotique, est aménagé avec du matériel sponsorisé provenant d’acteurs technologiques majeurs comme KUKA, SMC et Schunk, le spécialiste des préhenseurs. « Robotland est unique au monde. Pour la partie extérieure, nous avons dû aller chercher les chargeuses articulées, les mini-excavatrices et autres, mais nous avons conçu la plupart des configurations nous-mêmes » souligne Luc Van Thillo.
La ‘Loi de Bernoulli’ décrit le comportement d’écoulement des liquides et des gaz. A Robotland, l’aérodynamique et l’hydrodynamique sont étudiés, notamment avec cette balle qui flotte sur un flux d’air.

MOBILAB CARE, INTERFACE ENTRE LES SOINS ET LA TECHNOLOGIE

L’INGÉNIEURE CIVILE EVELINE DE RAEVE ÉTUDIE COMMENT L’HOMME SE DÉPLACE
Ces dernières années, les robots, les imprimantes 3D, l’électronique et les capteurs ont noirci les pages d’Automation Magazine. Pratiquement toujours dans un contexte industriel. Nous vous proposons aujourd’hui de découvrir ces techniques qui fournissent d’aussi bons services dans un tout autre domaine. A la Haute-Ecole Thomas More à Geel, le centre de recherches Mobilab Care applique la technologie avec succès pour développer des soins plus intelligents. Un entretien avec la chercheuse ir. Eveline De Raeve à propos des études et des résultats.
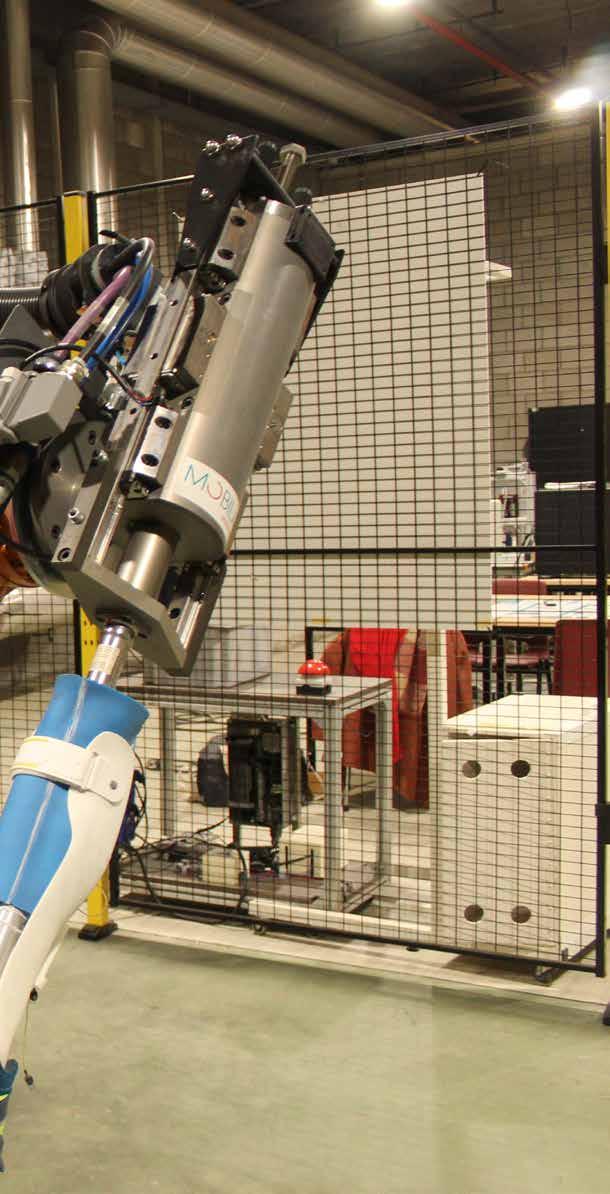
Eveline De Raeve et le robot de Mobilab Care: « Grâce à la technologie, nous créons des soins plus intelligents. » Peu de passants savent que le sous-sol du campus Thomas More à Geel abrite un robot Kuka KR 210 ayant une charge utile de plus de 200 kilogrammes et une portée de plus de 3 mètres. Au bras du robot, pas de préhenseur typique ni de torche de soudage ou d’outil de montage mais un système à ressort avec un pied artificiel et une chaussure de sport. Avant de vous présenter en détail cette application marquante, revenons au Mobilab Care, un centre d’expertise multidisciplinaire qui emploie 34 collaborateurs dans la recherche scientifique appliquée sur les soins et le bien-être, et met l’accent sur la technologie.
Automation Magazine a demandé à Eveline De Raeve quels types de projets elle menait et comment elle travaillait : « Un exemple de recherche que nous avons réalisée est le projet Efforth. Nous voulions étudier comment le secteur orthopédagogique pouvait utiliser au mieux des techniques comme l’impression 3D, le scannage 3D et le fraisage dans la fabrication de prothèses. Parfois, une autre structure est exigée selon le degré de flexion. Nous étudions le principe de fonctionnement et les matériaux les plus adaptés de l’impression 3D pour obtenir les caractéristiques souhaitées. »
« La recherche a lieu en collaboration avec les entreprises. Ici, le groupe était constitué de fabricants de scanners 3D, de logiciels et d’imprimantes 3D. Nous avons utilisé un robot. Via le programme que nous avons nous-même écrit, nous simulons tous les modèles de marche humaine possibles. Le pied artificiel marche sur une plateforme de force et des capteurs enregistrent le point d’application et la force dans trois directions. L’installation est là depuis quelques années et elle a été utilisée dans d’autres projets. Au début, nous testions les chaussures de sport, plus tard des prothèses pour lesquelles nous réalisons des mesures comme la pression entre la coquille et le moignon et l’influence de la pression sur les différents schémas de marche. Dans un projet plus récent, le robot a été utilisé pour tester les orthèses et prothèses dynamiquement et statistiquement. De nouvelles idées jaillissent en permanence. »
« Pour les fabricants, notre approche est souvent totalement différente de ce à quoi ils sont habitués dans les applications industrielles. En ce qui concerne le robot, il devait par exemple être capable de déterminer précisément les points de position pendant le mouvement. Les questions que nous posons sont différentes de celles qu’ils entendent habituellement. Le pied doit créer un contact avec la plateforme sous-jacente, alors que dans les applications industrielles, ce type de contact n’est pas recherché. »
Exosquelette et capteur sur le lieu de travail
« Une autre recherche concerne le projet Sense to Action qui démarrera bientôt. Nous étudierons comment introduire des capteurs et des exosquelettes sur un lieu de travail dans plusieurs secteurs : construction, logistique, chirurgie. Ici aussi, des fabricants de capteurs et des distributeurs d’exosquelettes sont impliqués dans le projet. Nous avons également participé
au projet ‘Exoskeletons for Logistics’ du Vlaams Instituut voor de Logistiek, où plusieurs types d’exosquelettes ont été testés dans des tâches logistiques. Nous avons réalisé des mesures à partir de domaines d’action spécifiques et étudié quand les personnes étaient limitées dans leurs mouvements. Nous avos conclu que le choix d’un type approprié est difficile et nécessite de l’expérience. Il y a aussi les mouvements que l’opérateur réalise à côté de la tâche impliquant l’exosquelette. S’il est limité dans ses mouvements, alors l’utilité est réduite. »
Orthèse actionnée
« Dans le projet Motion, nous utilisons aussi la technologie. Il s’agit d’un projet européen Interreg pour lequel nous développons un prototype d’orthèse cheville/pied pour aider les enfants souffrant de paralysie cérébrale, une maladie qui les empêche de marcher correctement. Aujourd’hui, les orthèses qui offrent une aide au processus de marche sont peu adaptées au mouvement du moment. Nous voulons développer une orthèse qui génère un soutien adapté selon la phase de marche. Nous utilisons un moteur spécial sans balais de Hebi Robotics et un actionneur spécialement développé pour nos applications de recherche. Via des capteurs qui mesurent en permanence la position, la vitesse, le couple et l’inertie sur 3 axes, nous détectons le mouvement du haut de la jambe. Via un algorithme, nous définissons ensuite la phase exacte du déplacement. Sur base de cette information, nous programmons la rigidité dans le ressort de torsion de l’orthèse via le contrôle d’impédance. Nous pouvons donc donner une force supplémentaire au lancement, ou la contrer si nécessaire. Cela permet d’obtenir un support plus ciblé. »
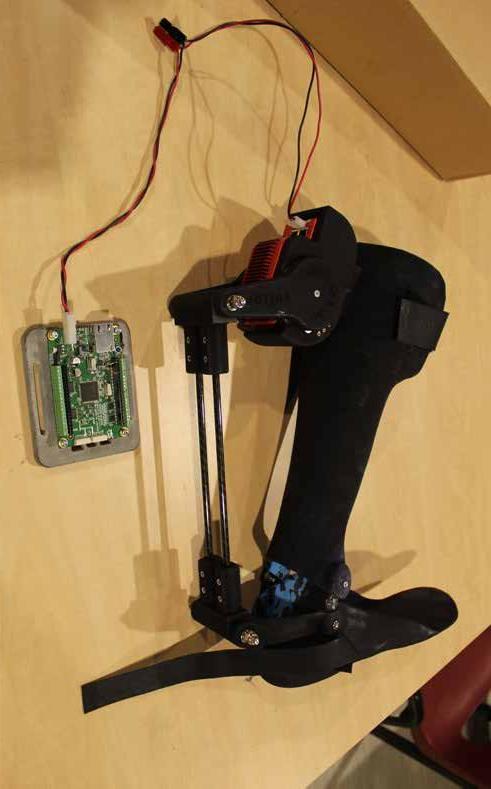
Tant des profils médicaux que techniques
« Chaque personne de l’équipe a sa spécialité et l’apport de chaque équipe dépend du contenu du projet. Il est logique qu’une personne ayant un bagage médical ne sache pas programmer un robot. Mais un regard neuf sur un tout autre domaine d’application est souvent très précieux pour les personnes plus impliquées dans la technique. Et cela va dans les deux sens. On peut parler à juste titre d’une équipe multidisciplinaire. Il y a des kinésithérapeutes, des orthopédistes, des infirmières, des psychologues et des sociologues mais aussi des ingénieurs civils et industriels actifs dans l’électronique, les logiciels et la mécanique. Moi-même, j’ai commencé à travailler à l’Université de Gand après avoir terminé ma formation d’ingénieur civil. Je suis diplômée en génie mécanique électrotechnique, option génie énergétique mécanique, et j’ai suivi plusieurs cours supplémentaires en génie biomédical parce que je m’intéressais à la manière dont l’homme se déplace. Une formation adaptée à ce centre de recherche.»
« Je connais Mobilab Care parce que j’ai habité à proximité. Lorsqu’un poste a été ouvert en 2010, je n’ai pas hésité un seul instant. Aujourd’hui j’enseigne aussi des matières comme la mécanique appliquée, l’électricité et la robotique et je travaille sur des projets dans le cadre de la formation de bachelier en électromécanique. »
www.mobilab.be
Cette orthèse (un appareillage qui compense une fonction absente) pour les enfants s’adapte à la phase de marche du moment via une rétroaction vers le moteur.
PENDANT LE CONFINEMENT, LE CHIFFRE D’AFFAIRES DE L’INDUSTRIE TECHNOLOGIQUE A CHUTÉ DE 13,5 % ET LES EXPORTATIONS DE 28 %
Au cours des six premiers mois de 2020, le chiffre d’affaires de l’industrie technologique en Belgique a baissé de
6,5 % par rapport au premier semestre de 2019. Au deuxième trimestre 2020, on a même observé une baisse de 13,5 %. Les reculs les plus importants ont été enregistrés dans le secteur automobile (-26,5 %) et dans celui de la construction mécanique (-13 %). En revanche, les services IT ont progressé de 5 %.
C’est surtout pendant le confinement que les chiffres ont chuté de manière drastique : le chiffre d’affaires a baissé de 13,5 %, tandis que les exportations ont diminué de 28 %.
Agoria s’attend pour cette année à un recul de chiffre d’affaires de l’industrie technologique de 7,5 %. Si en 2019, son chiffre d’affaires atteignait encore le montant record de 132 milliards d’euros, il devrait cette année baisser de 10 milliards d’euros pour avoisiner les 122 milliards d’euros, et ce alors que l’industrie technologique belge était en pleine croissance depuis cinq années consécutives. Les baisses les plus importantes concernent le secteur automobile (-18 %), la construction mécanique (-13 %) et l’électronique (-11,5 %). Seul le secteur des services informatiques connaitrait une progression limitée de 2 %.
Pour l’année prochaine, Agoria prévoit une nouvelle augmentation du chiffre d’affaires de 6,5 %, en particulier dans les secteurs qui ont connu des difficultés cette année : la construction mécanique, l’automobile et l’électronique.
L’exportation de produits technologiques enregistre une baisse de quinze pour cent. L’Allemagne, la France et les Pays-Bas sont les principaux pays vers lesquels la Belgique exporte ses produits technologiques. Au cours du premier semestre de 2020, ce sont surtout les exportations vers le Moyen-Orient (-25 %), l’Amérique du Sud (-23 %) et le reste de l’Europe (-17 %) qui ont diminué. Or, les exportations vers certains pays ont également progressé : le Canada (+ 65 %), Taïwan (+ 46 %) et la Chine (+41 %).
Une plus grande part de marché
Même si les exportations sont en baisse, la part de marché de l’industrie technologique belge ne cesse quant à elle d’augmenter. Depuis l’été 2015, nous notons pour la première fois en quinze ans un redressement (amélioration de 1,6 pour cent) de la part de marché de la Belgique au sein de l’Union européenne dans l’exportation de produits technologiques.
Plus de 310.000 personnes travaillent dans le secteur technologique. En 2019, le chiffre d’affaires du secteur s’est élevé à 132 milliards d’euros et les investissements à plus de 4 milliards d’euros.
www.agoria.be
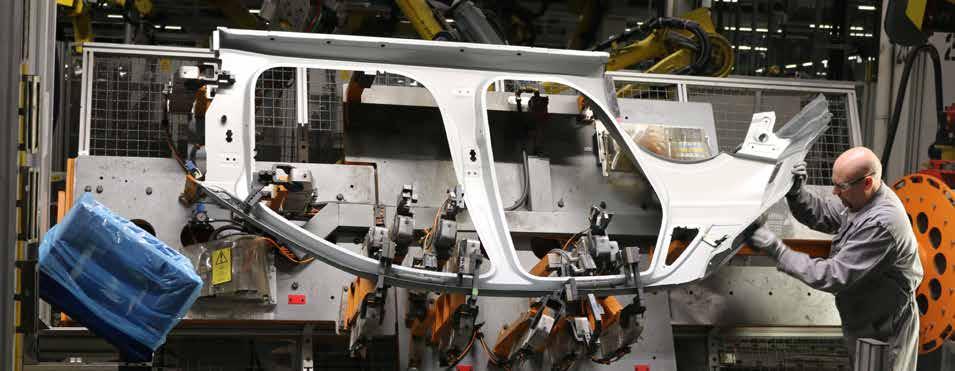
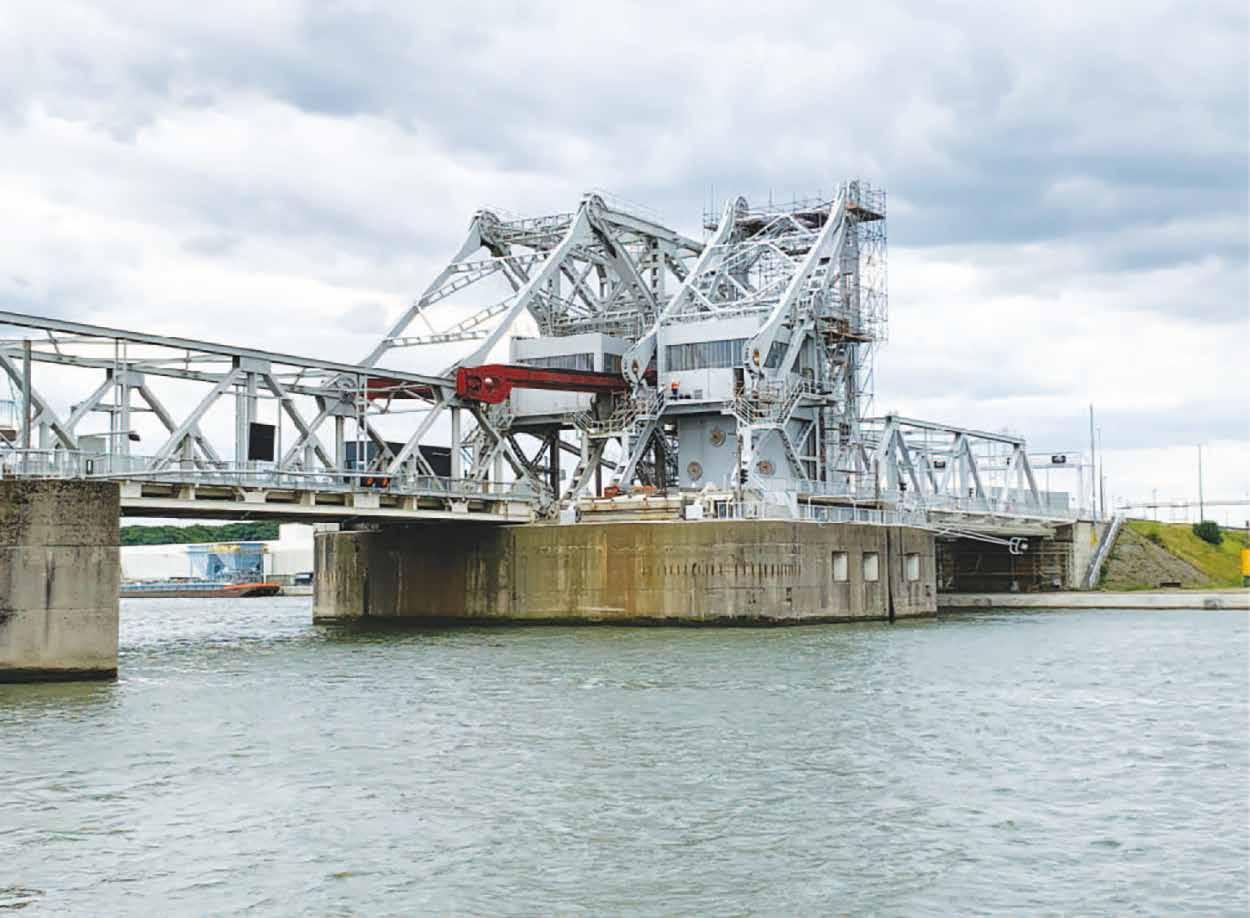
LES FREINS STROMAG À RESSORT SPÉCIFIÉS POUR UN PONT BASCULANT TRÈS FRÉQUENTÉ AU PORT D’ANVERS
Deuxième port maritime d’Europe, le port d’Anvers traite 200 millions de tonnes de marchandises par an. Son bon fonctionnement repose fondamentalement sur la navigation sans entrave des navires et barges qui le fréquentent, et sur la libre circulation des véhicules de tourisme et utilitaires le long des liens ferroviaires et routiers le desservant.
Il n’est donc pas étonnant qu’un vaste réseau de ponts basculants (ponts-levis), devant tous fiablement fonctionner nuit et jour, couvre le port. Dans le cadre de la remise à niveau continue des systèmes d’entraînement de ces ponts, les freins électromagnétiques à disque 3CA2 de Stromag ont été sélectionnés pour remplir des fonctions d’arrêt et de maintien.
Après Rotterdam, le port d’Anvers traite plus de fret que n’importe quel autre port en Europe. Outre sa taille, c’est sa position qui le distingue des autres ports de la mer du Nord, les navires de commerce maritime pouvant pénétrer jusqu’à 80 km à l’intérieur des terres. Le port dispose ainsi d’une position centrale, facilement accessible pour l’acheminement par rail, route ou voie navigable. Au fur et à mesure de l’expansion du port, un grand nombre de ponts basculants ont été construits pour permettre aux véhicules, camions et trains de traverser le réseau de canaux et d’écluses.
Ponts basculants adjacents de type Strauss
En 2010, un plan d’investissement à long terme a été approuvé, d’une valeur de 1,6 milliards d’euros sur 15 ans. Outre le financement de la poursuite des plans d’expansion, une partie de cet investissement était allouée à l’amélioration et la mise à niveau d’installations existantes.
Le département d’accès maritime du gouvernement flamand a désigné plusieurs ponts de la rive droite du port qui exigeaient une attention particulière. Le pont Noordkasteel en particulier, l’un de deux ponts basculants adjacents de type Strauss, a été cité pour posséder des composants mécaniques dont le système de freinage en fin de vie avait besoin d’être remplacé.
Ce pont de 170 mètres de long a été construit en 1980. La longueur de son tablier central basculant est de 56 mètres, avec un contrepoids de 1.200 tonnes. Le sous-traitant responsable de la spécification et de l’installation des mises à niveau avait pour tâche de déterminer une solution de freinage offrant des capacités d’arrêt et de maintien, tout en étant capable de supporter des conditions environnementales sévères avec un minimum de maintenance.
Il s’adressa à Stromag, une marque phare d’Altra Industrial Motion Corp., renommée pour la qualité de ses solutions de freinage, et qui avait fourni le premier système de freinage en 1980.
Freins électromagnétiques
Stromag a recommandé ses freins électromagnétiques à disque 3CA2 haute performance, couplés avec les blocs d’alimentation électrique AC32 pour une performance
optimale de freinage. Ces freins à ressort s’ouvrent via un système électromagnétique et ils se ferment automatiquement en cas de coupure soudaine d’alimentation. La gamme a été spécialement conçue pour un freinage haute performance en environnement industriel sévère, parmi lesquels le milieu marin, offshore, sidérurgique et nucléaire. Le bloc d’alimentation électrique AC32 garantit une performance de freinage supérieure, la rapidité du diagnostic de recherche de pannes et un rendement amélioré.
Le 3CA2 peut être spécifié avec différents diamètres de disque en standard. Pour l’application du pont Noordkasteel, les ingénieurs Stromag ont recommandé le disque de 705 mm de diamètre à deux pinces, ayant chacune un couple de freinage de 2 900 Nm. Un jeu de freins remplissant les fonctions d’arrêt et de maintien a été monté des deux côtés de la boîte de vitesses. Un système de déblocage hydraulique a également été spécifié, il permet de contrôler l’ouverture du frein en cas de coupure d’alimentation.
Réduction des charges de maintenance
Outre la haute performance et la conception robuste du 3CA2, le bloc est équipé de compensation automatique d’usure pour veiller à la constance du couple de freinage. Des indicateurs d’usure intégrés dans ces plaquettes permettent d’alerter facilement le besoin de les remplacer. De cette façon, les freins ont pu offrir à la fois la réduction des charges de maintenance et l’amélioration de la performance actuelle. Ayant apporté leur expertise produit pour la conception et la spécification du système de freinage, les ingénieurs de Stromag ont également pu aider à son installation sur site, ainsi qu’aux essais et ajustements finaux. Stromag continuera d’appuyer les opérateurs du pont en intervenant sur site et en fournissant les pièces OE en fonction des besoins, tout au long de la durée de vie du système de freinage.
Stromag a recommandé ses freins électromagnétiques à disque 3CA2 haute performance, couplés avec les blocs d’alimentation électrique AC32 pour une performance optimale de freinage.
www.stromag.com
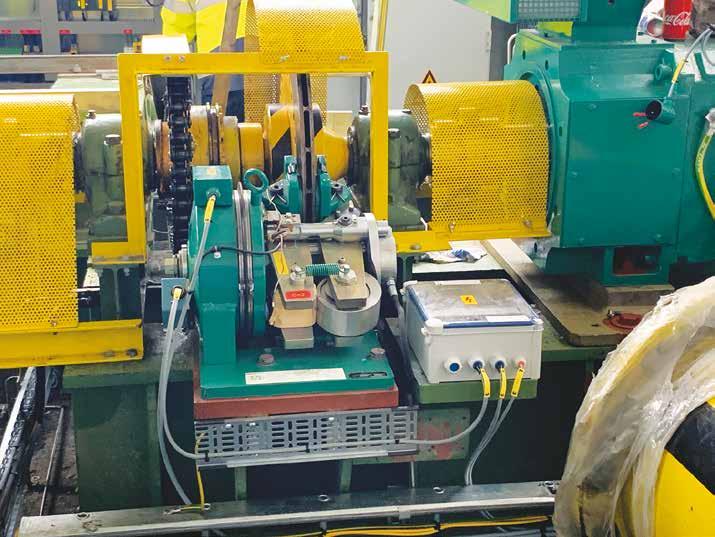
Fixation rapide pour Cobots
.1. .2. .3.
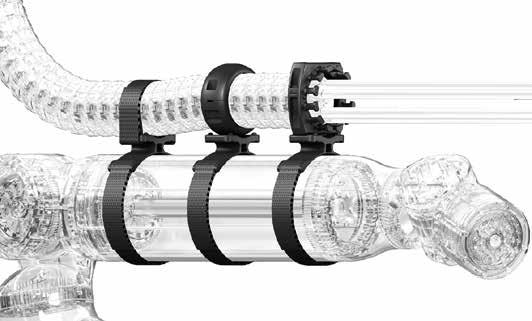
Maintien triflex® R COB :
simple fournisseur d'énergie
Nouvelle attache universelle pour système d'alimentation en énergie pour différents types de robot. Un élément de base pour la construction flexible, par exemple : 1. comme une boucle velcro abordable 2. avec anneau de protection ou 3. élément de fixation. Application multiple, montage facile et gain de coûts. Equipé de velcro anti-dérapant pour une prise ferme.
votre-chain igus® ... pour un guidage en toute sécurité
igus® S.P.R.L. Tél. 03-330 13 60 info@igus.be Rendez-nous visite : igus.eu/virtualexhibition motion plastics®
GESTION DE LA FILTRATION FACILITÉ GRÂCE AU SERVICE CONNECTÉ DONALDSON ICUE™
La pandémie de covid-19 a influencé les opérations quotidiennes de nombreuses entreprises manufacturières, notamment en accélérant l’adoption de l’internet industriel des objets (IIoT) - c’est-à-dire des technologies connectées, de la même manière que nos téléphones et ordinateurs portables sont connectés à l’internet - et du télétravail. IIoT fait du suivi à distance de votre usine et des processus de fabrication une réalité : Il contribue à garantir le bon déroulement de votre production en temps réel tout en limitant la circulation des employés dans vos sites.
Vos usines et ses équipements critiques retiennent probablement toute votre attention. Vous voulez simplement vous assurer que votre système de dépoussiérage fait son travail, afin que vous puissiez vous concentrer sur le vôtre. Et si, plutôt que de de juste faire son travail, votre dépoussiéreur pouvait aussi vous faciliter la tâche ? Eh bien, maintenant c’est possible.
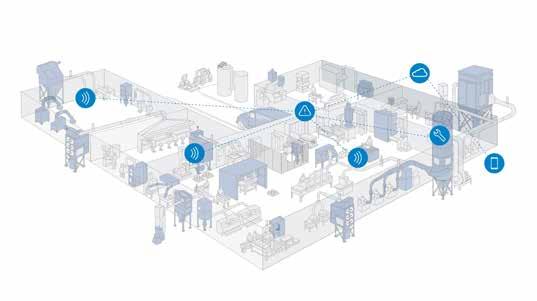
Le service de filtration connecté de Donaldson iCue™ surveille en permanence le bon fonctionnement de votre dépoussiéreur, en fournissant des données de performance en temps réel qui vous permettront d’agir en cas d’alerte avant même que le dysfonctionnement ne se produise. Il est rare qu’une seule technologie puisse profiter à un groupe d’acteurs aussi divers dans l’entreprise, mais c’est exactement ce que fait le service iCue : Les équipes chargées de l’exploitation ou de la maintenance, des achats et de la santé et sécurité environnementales auront un accès instantané aux informations qui peuvent les aider à réduire les temps d’arrêt imprévus, à maximiser l’efficacité des collecteurs et à suivre en toute confiance les données de conformité.
Des informations précises à portée de main
Encore fréquemment, le monitoring d’un système de dépoussiérage consiste à prendre des mesures manuelles sur chaque collecteur, à enregistrer les résultats et enfin à interpréter les données : des tâches qui prennent du temps et qui ne fournissent parfois même pas les informations nécessaires pour prendre les bonnes décisions concernant l’entretien des installations.
Le service de filtration connectée iCue vous permet de gérer la surveillance de vos installations, en vous fournissant des informations précises et en temps réel pour vous aider à optimiser l’efficacité des collecteurs, à réduire les temps d’arrêt imprévus et à simplifier la documentation de conformité. Les données enregistrées manuellement ne sont qu’un instantané dans le temps. La surveillance connectée est continue, vous remarquerez donc immédiatement les tendances et les anomalies, de sorte que les interventions de maintenance aient lieu au moment où vous en avez vraiment besoin.
Cinq indicateurs clés à surveiller en priorité :
1. Pression différentielle : Vos filtres fonctionnent-ils correctement ?
Le service iCue vous avertit à temps d’éventuels problèmes de filtration, afin que vous sachiez à l’avance quand les filtres doivent être remplacés.
2. Concentration de particules - Vos limites d’émission ou d’exposition sont-elles dépassées ?
iCue envoie un avertissement lorsque les limites d’exposition sont susceptibles d’être dépassées, et fournit des données précises et normée sur la conformité.
3. Pression d’air comprimé - Votre mécanisme de nettoyage des filtres fonctionne-t-il ?
iCue avertit lorsque la pression d’air comprimé diminue afin de prolonger la durée de vie de vos éléments filtrants.
4. Débit d’air relatif - L’air circule-t-il suffisamment - ou trop - abondamment ?
iCue fournit des informations sur les problèmes du système afin que vous puissiez réduire les temps d’arrêt non planifiés et optimiser la maintenance et réduire les risques potentiels d’émissions.
5. Obstruction de la trémie - Risquez-vous une accumulation de poussière ?
iCue vous informe lorsque le matériau filtré commence à se solidifier, afin que les équipes de maintenance puissent retirer l’obstruction avant qu’elle n’affecte la qualité de la filtration.
Pour de plus amples informations sur le service de filtration connecté iCue, veuillez contacter un spécialiste Donaldson via connectedsolutions-europe@donaldson.com ou en visitant donaldson.com/connectedsolutions
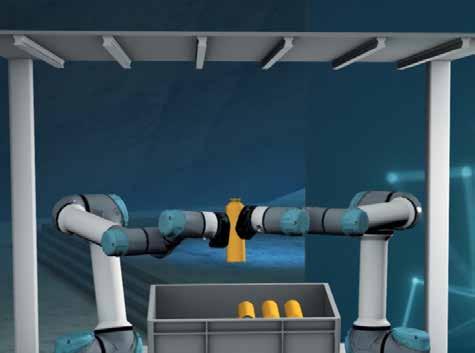

Siemens a développé en collaboration avec l’entreprise belge Cloostermans, qui fabrique des machines sur mesure pour des clients dans le monde entier, un concept modulaire capable de se reprogrammer et de se reconfigurer à l’aide de l’intelligence artificielle pour s’adapter à tous les types de produits et d’emballages. Les fabricants de produits de consommation peuvent ainsi passer plus rapidement d’une production à l’autre et gagner en efficacité, sans rien perdre en fiabilité.
L’intelligence artificielle (IA) permet de franchir une nouvelle étape dans la conception des produits et de la fabrication. « L’IA aide les entreprises à faire un usage plus efficace des outils logiciels, à réaliser des développements plus sophistiqués et à optimiser les workflows », explique Eddy Nelis, Senior Vice President Digital Industries chez Siemens. « Mais l’IA permet aussi de nouvelles avancées en matière d’automatisation industrielle intelligente. Grâce à la puissance de l’intelligence artificielle, il est désormais possible de confier aux machines des tâches jusqu’ici réservées aux hommes parce qu’elles exigent une connaissance plus approfondie et une meilleure perception de l’environnement. Les opérateurs et techniciens peuvent ainsi se consacrer davantage à des missions plus stratégiques. »
Siemens et Cloostermans, leader mondial des machines d’automatisation haut de gamme sur mesure, ont mis au point une solution pour un concept universel révolutionnaire. « La machine s’adapte à toute une série de types de produits et d’emballages », confirme Frederik Berckmoes-Joos, CEO de Cloostermans.
« C’est une vraie première. Jamais auparavant l’IA n’avait été intégrée dans une machine d’emballage d’une manière qui imite et automatise la fluidité de pensée et de geste des opérateurs sur les lignes d’emballage. Cela permet aux fabricants de passer beaucoup plus vite à un tout autre type de produit ou d’emballage. Siemens, qui possède énormément d’expérience et d’expertise en IA, était pour nous le partenaire idéal. »
Délais de commercialisation raccourcis
Grâce aux possibilités de configuration rapide de cette solution, il est possible d’augmenter l’efficacité de la production sans mettre en péril la fiabilité du processus. « Les longs délais de conversion ou les efforts d’ingénierie supplémentaires avant l’introduction de nouveaux produits ou variantes d’emballage n’ont plus de raison d’être. Les producteurs peuvent ainsi raccourcir considérablement les délais de commercialisation et fabriquer en plus petites séries. Le client final est en mesure de suivre plus rapidement les tendances du marché et l’évolution de la demande des consommateurs. La flexibilité au niveau des emballages est énorme », ajoute Mathias D’hoore, Mechatronics Manager chez Cloostermans.
Le concept d’IA de Cloostermans et Siemens fonctionne de manière totalement autonome et se reconfigure de lui-même à chaque nouvelle application sur la base d’un modèle digital. Des robots et des caméras remplacent les mains et les yeux des opérateurs et l’IA pilote chaque mouvement. « L’unité de traitement neuronal Simatic S7-1500 TM-NPU de Siemens analyse les images des caméras sur la machine et recalcule la position et l’orientation précises de chaque objet. La technologie TM-MFP calcule ensuite, à l’aide d’algorithmes IA, les mouvements optimaux des bras robotisés qui soulèvent et positionnent les produits dans les emballages », poursuit Eddy Nelis.
Siemens a utilisé la technologie du jumelage digital pour simuler en amont le fonctionnement de la machine et des processus. « Nous savions que cela marcherait avant même que la machine soit construite. Nous avons pu également simuler l’intégration de la ligne de production dans la chaîne logistique. La manière dont la machine est assemblée et connectée au reste de la chaîne logistique, avec des technologies à la pointe de l’innovation, est réellement spectaculaire », conclut Eddy Nelis.