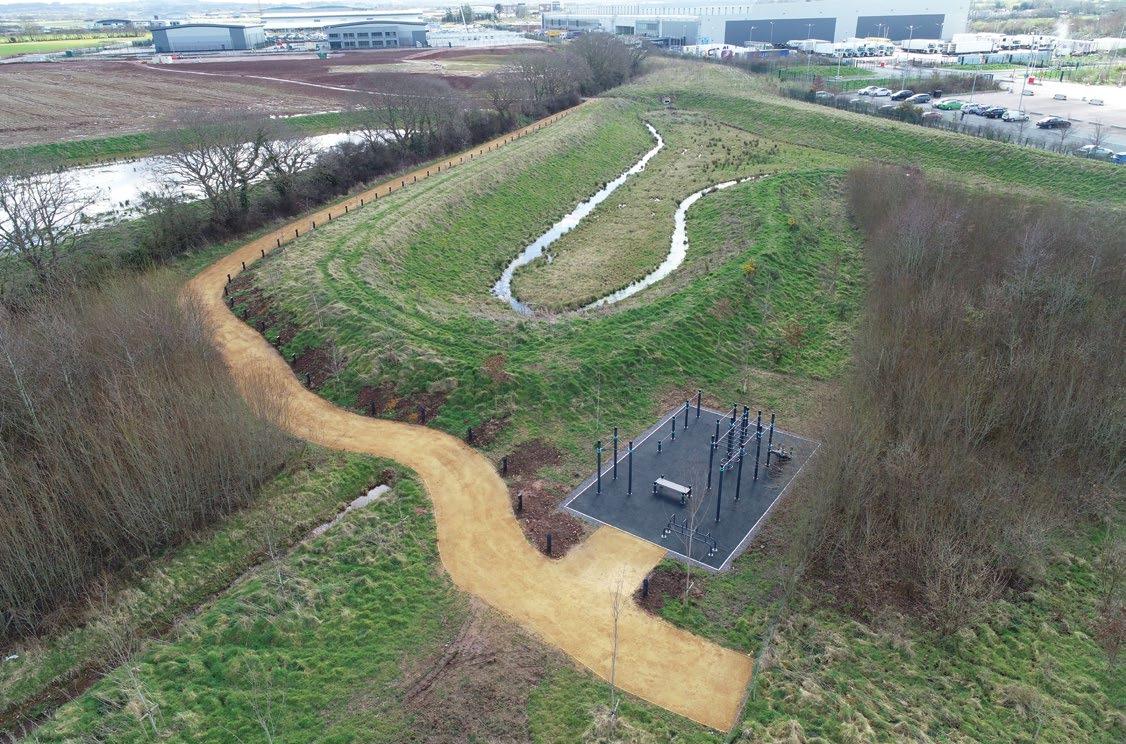
2 minute read
How Stoford is future-proofing Exeter Logistics Park
With the environment at the front and centre of all construction developments, it is not just a “nice to have” consideration - and greenwashing will not cut it. Stoford is serious about its commitments to the environment - and the attainment of Planet Mark demonstrates the business’s aims to reduce carbonemitting activities by 5% every year.
Exeter Logistics Park is a Stoford scheme that goes above and beyond the minimum sustainability requirements in many areas. Considerable effort is made to make sure the entire site is future proofed. That has meant ensuring more EV charging points can be added when required, by installing the necessary ducting in the car parks during initial construction, and constructing green roofs to the outbound offices, depending each unit’s layout/configuration.
Advertisement
Through the generation of onsite renewable technologies, in particular photovoltaic solar panels, Stoford can to achieve in excess of 10% carbon reduction at Exeter Logistics Park compared to baseline building regulations. Stoford does this as part of its commitment to doing more to make developments more sustainable.
Other measures include minimising water consumption, a water usage monitoring system to detect leaks, and energy-efficient systems for lighting, cooling and heat.
Flooding is a significant concern for developers and legislation is also changing, which means more attention is rightly turning to sustainable drainage systems (SuDS) to help protect people and buildings.
At Exeter, although the development is not in a highrisk flood zone, there is an overarching SuDS strategy and a number of different features are implemented, depending on the characteristics of each plot.
To this end, the scheme includes two large attenuation basins for storm water run-off and as part of the sitewide drainage strategy, as each phase is developed it will include extending the previously constructed roadside swale network and inclusion of on-plot permeable paving, and bio retention and filtering of surface water run-off in landscaped rain garden pits. Future phases will also include green roofs on cycle shelters because these help to boost biodiversity. Landscaping is an important part of any developmentnot just to make it more aesthetically pleasing, but also to increase the natural flora and fauna.
While the first phase of development included the provision of a bat house, Stoford is also committed to enhancing landscaping and is producing a detailed strategic programme to make the onsite environment one to be proud of.
It’s not just wildlife that Stoford is looking after, though. Exeter Logistics Park includes an outdoor gym facility, providing bodyweight exercise equipment by Kenguru Pro, to promote health and wellbeing of all employees.
By looking after the environment, wildlife and people, Stoford is doing its bit at Exeter Logistics Park. It’s central to other development schemes, too.
In Ellesmere Port, where Stoford is constructing a new 667,000 sq ft UK parts distribution centre, the highest level of building sustainability certification is being targeted, including BREEAM ‘outstanding’ and an EPC ‘A’ rating. It will be certified as net zero carbon in operation for the base build works.
The office building will feature photovoltaic roof panels, rainwater harvesting, LED lighting and an energy monitoring system. Staff will also benefit from an external wellbeing area, bicycle storage and EV car charging points.
Stoford is speculatively developing two net zero carbon warehouse units at Redditch Gateway, which will deliver almost 450,000 sq ft of new industrial and logistics accommodation, while in Leamington Spa, Spa Park it handed over a purpose-built production plant to plastics manufacturer Berry Global.
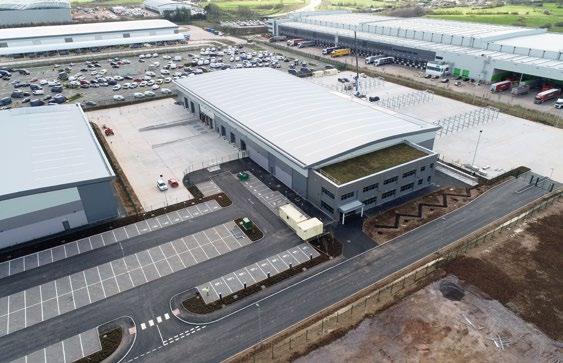
This 166,859 sq ft unit enjoys strong sustainability credentials including an EPC ‘A’ rating and BREEAM ‘excellent’ and has achieved net zero carbon in construction.
Ben Gwilliam, Project Manager, Stoford