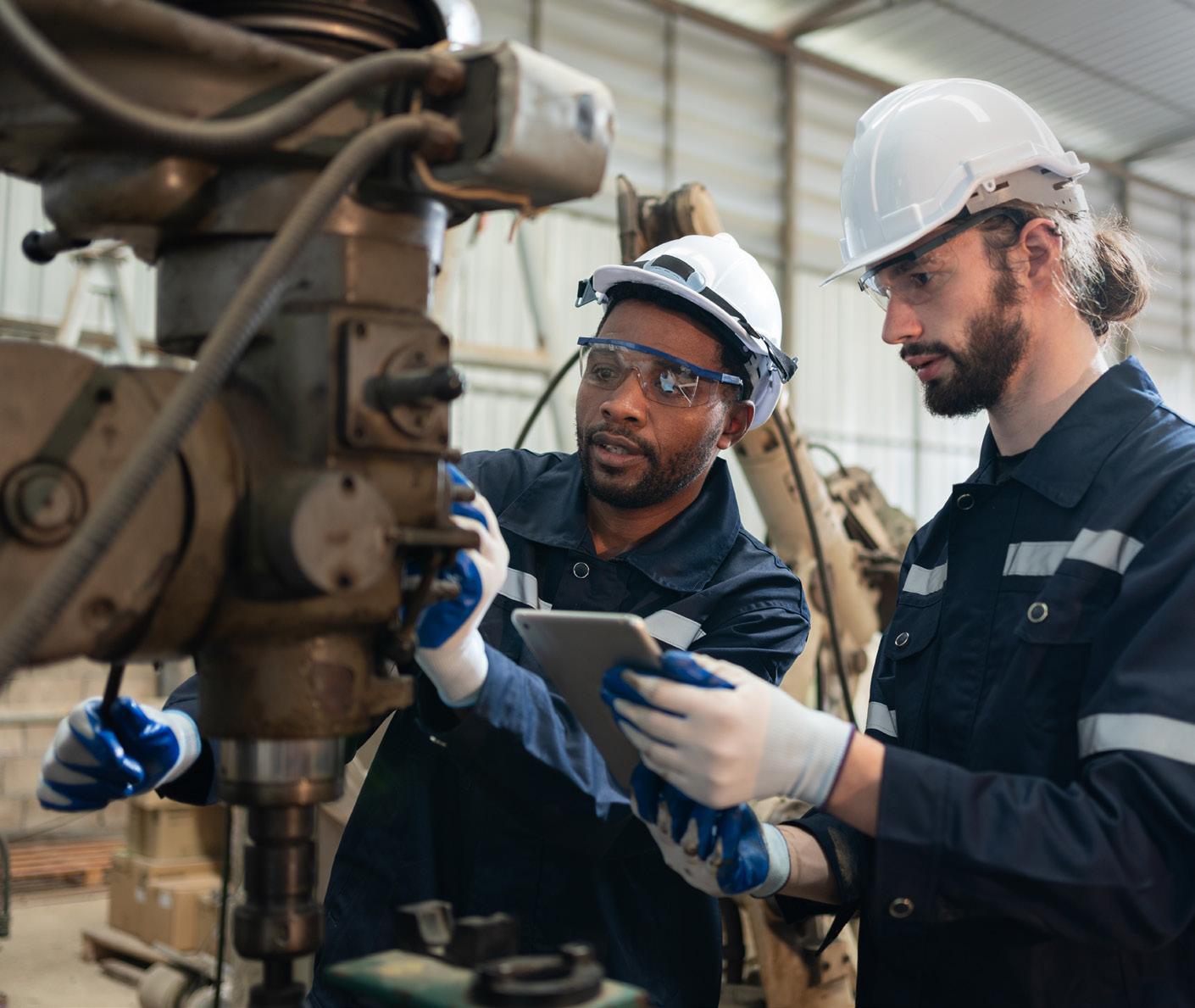
3 minute read
Preventive Maintenance Optimization
Part 1
Preventive Maintenance (PM) is the best approach in modern technology to mitigate the high cost of downtime in most organizations with constrained capacity and resources. Preventive maintenance can reduce the likelihood of failures and downtime; however, it can incur unnecessary, expenses, and waste if done too frequently or without proper justification. Undertaking a block replacement policy under PM can lead to “over-maintenance” if inspection before replacement is not utilized. Parts recently replaced based on corrective maintenance still contain potency; if they are replaced and scrapped, that increases maintenance costs and waste. Hence, using predictive maintenance along with PM could significantly enhance maintenance optimization and asset performance. Predictive maintenance can improve the efficiency and effectiveness of maintenance activities by using inspection and data analytics to forecast failures and optimize maintenance schedules. Moreover, Internet of Things (IoT) devices allow for monitoring predictable failures in prior planning. However, exploiting these techniques may also require more investment in technology and expertise.
A cardinal aspect of preventive maintenance is using spare parts, which is integral to the strategy. Block replacement demands that all spare parts be available—integrating predictive maintenance before preventive maintenance enables planning for replacement parts. The parts that cannot be restored or retained to their operating condition are termed non-repairable, while the inverse is repairable. In contrast, consumable parts are expected to require regular replacement as part of routine maintenance for optimal performance and reliable operation, not due to any manufacturing defect. A lubricant preserves characteristics that warrant its classification as a non-repairable and consumable part. As a consumable part, lubricant consumption is depleted, for instance, by oil carryover in the blow-by recirculation, oil transport by the piston and its rings, oil evaporation through combustion, and leakages. While consumable parts are expected to require replacement as part of routine system maintenance, you can maximize the service life of these components by staying on top of your routine maintenance schedule. Diligent and thorough maintenance is the best way to minimize the need for consumable parts replacement.
As a non-repairable part, the lubricant is drained or scrapped (preventive partial or full replacement) based on its degradation level or at the prescribed drain interval (PM interval). As a non-repairable spare, various corrective and preventive maintenance replacement interventions are conducted to mitigate the aging degradation of the lubricant, addressing the shortfall in performance to return its properties to an acceptable operational state. The in-service lubricant can undergo complete drainage, also known as Full-Volume Oil Changes (FVOC), where all the oil in the sump is replaced. FVOC could be employed as corrective maintenance when unplanned, while as a PM, the lubricant could be replaced with system purging at pre-determined intervals. A partial oil change or Short-Volume Oil Change (SVOC) depicts draining and refilling the oil with some fraction of the total sump volume [1]. Hence, it is paramount that lubricants, like other repairable and non-repairable parts, be considered while optimizing maintenance and inventory to ensure efficient and cost-effective operations.
In the second part, we shall look at inventory management in PM.