
3 minute read
How Supply Chain Loss Prevention Is Responding to Changing Needs
By Jacque Brittain, LPC
The need to adapt and change is critical in every area of retail, but in today’s evolving times, perhaps this is most important for the retail supply chain. In an environment where automation and technology have become such a vital part of day-to-day operations, finding the most effective and efficient ways to move retail merchandise from the point of manufacture to the point of delivery to the customer requires strong management, creative processes, and capable leaders. Speed and accuracy are necessary to survive in the realm of the supply chain, requiring a higher level of flexibility and innovation than most realize. With the competitive nature of the business and the mounting demands of the retail customer, the development and implementation of successful supply chain programs has become a mission imperative across the industry.
To learn more about how innovation and technology are influencing the retail supply chain today, we held a roundtable discussion with several board members from the International Supply Chain Protection Organization (ISCPO) to gain their insights and perspectives on how the latest innovations are impacting supply chain loss prevention.
LPM: What do you consider to be some of the most significant innovations to impact supply chain operations over the past several years?
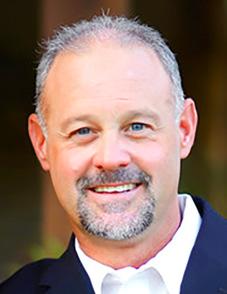
Glenn Master: First and foremost, physical security innovations have evolved significantly. Distribution center security uses a layered approach. You look at your specific risks in a particular center and modify your program based on those needs. For example, a distribution center in a rural area is going to have different needs and risks than one in a concentrated urban area. The way you design physical security in a million-square-foot facility and a 10,000-square-foot facility may be basically the same, but it’s how much you’re going to dial it back or increase the number of layers necessary to protect the people, your product, the transportation piece, and the facility based on the types of issues and the types of crime that are key.
Today, the IT team has a tremendous stake in managing security vendors. There’s really been a huge shift over the past several years. For example, as we keep making technological advances in information security, steps have to be taken with the vendors to protect the network. You have to follow the same guidelines with your physical security tools as you do with your information security systems because it’s so intertwined. We manage the program design, but when it comes to the relationship with the vendors, IT owns and manages that relationship and then brings loss prevention in as the industry expert. It’s a huge paradigm shift that really makes sense. It’s a good marriage between IT and loss prevention, making it more efficient and managing costs.
But it’s not just the technical innovation that’s changing—it’s the intellectual innovation and the managerial innovation that’s leading the way. By looking at things more holistically, we are now using the systems to support multiple functions. By working together and thinking outside the box, we have the ability to tie these same systems with HR-related projects, operations, transportation, safety, security, access control, and so forth in ways to create a full-service enterprise. When integrated, there’s a much greater return on our investment, improving efficiency, productivity, and safety within our facilities.
Paul Ganz: We’ve also made great strides with automation. If you think about all the ways that supply chains are looking to bring in robotics and other technology to simplify tasks, reduce the amount of risk associated with product issues, and, most importantly, protect our employees—we’ve made some extremely important improvements. When you put people in a process-intensive environment, safety must be paramount. While improving efficiency is certainly an important aspect of this, the improved safety aspects lead the way.
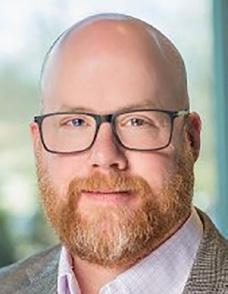
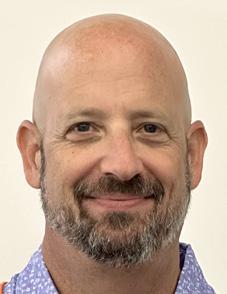
Considering the repetitive motions we ask associates to carry out as part of the supply chain function, it requires a significant amount of people power, which can lead to risk. Historically, we are always looking for ways to minimize the risk for our associates and improve productivity, and this is a giant step forward. This same automation also improves the accuracy and productivity of our systems and processes.
Today, what was once seen as lightyears away is now commonplace. For example, many picking processes are now handled in part by robotics. This labor-intensive process has been in many ways simplified and expedited to make everything more efficient, with incredible results. There’s so much more out there, and so much more coming every day.
Marco Alongi: Having greater visibility from the point of manufacture and all the way through the supply chain is another critical innovation. GPS has been around for many years, but it’s useless unless you have a system that allows you to pull that information together in a centralized view effectively. This allows us to manage the information and react appropriately based on the data gathered.
There’s now software that provides granular visibility to identify where a load is along the supply chain. This gives