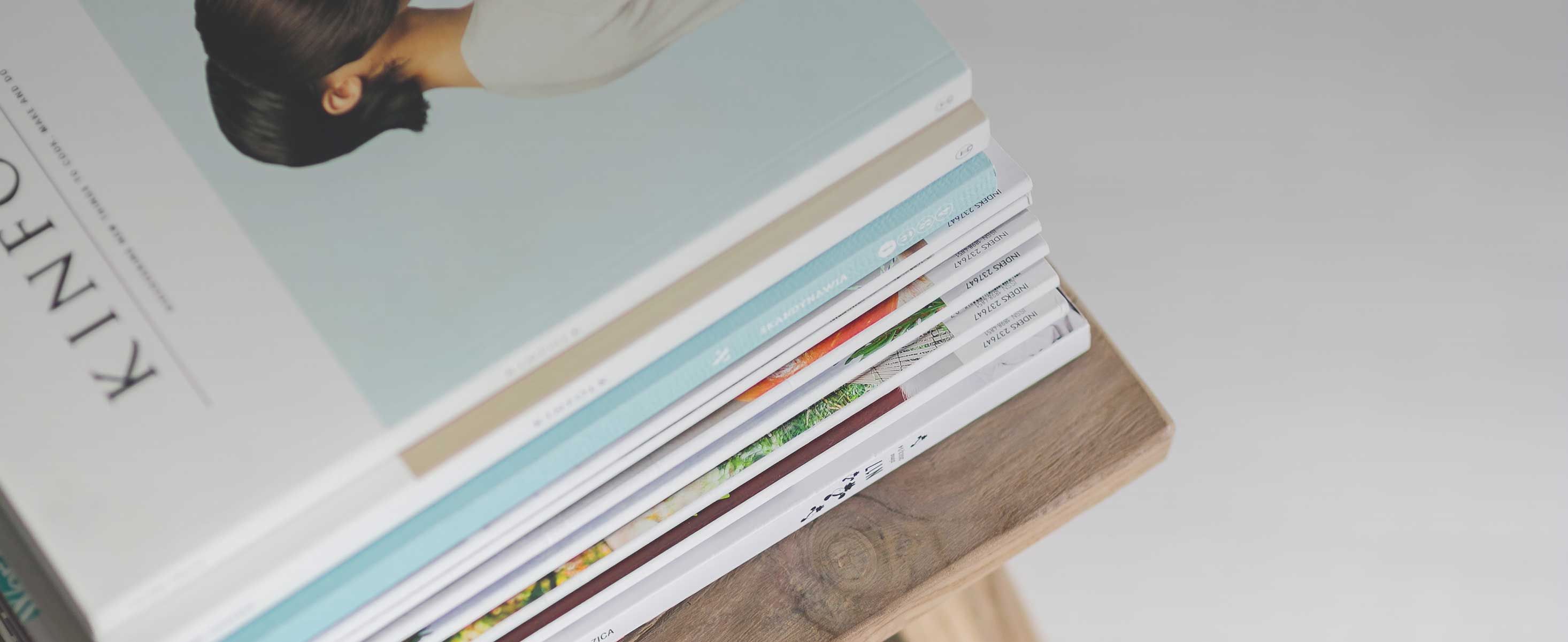
6 minute read
FIGURE 7.2 Xerox’s closed-loop supply chain
Xerox Corp’s environmental leadership
Xerox is a leader in document technology and services, and is among the world’s leading enterprises for business process and document management. It also offers global services such as claims reimbursement, automated toll transaction, customer care centres and HR benefits management. The mission of Xerox is: ‘Through the world’s leading technology and services in business process and document management, we’re at the heart of enterprises small to large, giving our clients the freedom to focus on what matters most: their real business’ (www.xerox.com).
Advertisement
Xerox aims to achieve zero waste for its products. The aim is ‘wastefree products manufactured in waste-free factories to enable customers’ waste-free workplaces’. Launched in 1991, Xerox’s environmental programme achieved the 2-billion-pound milestone by waste avoidance in two areas: (1) reuse and recycling in imaging supplies, and (2) product take-back and recycling and parts reuse. Next, Xerox’s Energy Challenge 2012 programme began with the goal of lowering greenhouse gas emissions (GHG) from worldwide operations by 10 per cent from 2002 to 2012. Recognizing the obligation to do even more, in 2007, Xerox set a new and challenging goal ‘to reduce our GHG emissions by 25 per cent by 2012, from a 2002 baseline’. Figure 7.2 illustrates Xerox’s closed-loop supply chain.
Figure 7.2 Xerox’s closed-loop supply chain
Raw material suppliers
Raw materials Part factories Parts
Xerox factories
Parts stripped, repaired and reused
Parts made with recycled materials
Equipment remanufactured
Equipment conversion
Recycling
During product design, Xerox focuses on minimal use of hazardous substances and efficient use of materials. Reuse and recycling of parts and components are seriously considered. The product lifecycle costs are estimated and reduced by considering the extended life of parts, easy disassembly, part reusability and material recyclability. The products are designed in such a way that some major parts (eg frames) will last longer and could be repaired or used for remanufacturing to another product. To achieve this effectively, the product design team developed a product lifecycle cost model, material guides and disposal coding. The product lifecycle cost, material usage and recovery options for each part and component are discussed in a mandatory review during the product design process. Training is provided to ensure all staff involved are capable of executing such robust product design processes.
The manufacturing processes are also designed to create waste-free factories. The focus is to achieve low emission and efficient use of energy during the production processes. The possibility of using low-emission and low-energy production processes is considered during the product design stage. Another unique feature of Xerox factories is that they are designed not only to build new products but also to remanufacture used products. The production lines are designed to be able to build new products by using some of the major parts recovered from the used products.
More importantly, Xerox recognizes the significance of energy usage during customer use. In addition to paper-saving features, a lot of research has been devoted to the design of copy machines which consume the least energy while in use or in energy-saving modes. According to Xerox, ‘standby’ is a waste. When the copy machines are not in use, better energy saving options such as ‘low power’, ‘sleep’ and ‘auto-off’ can be used. Recognizing the need for some heat to fuse toner onto paper (making copies), a lot of research has been conducted to make the printing process work under lower temperatures to achieve the optimal use of energy during use and in energy-saving modes. As a result, it is possible achieve to energy-saving modes 80 per cent of the time. Since 1993, Xerox has worked with EPA and the industry together to set criteria for energy-saving copy machines. Xerox Energy Star products are internationally recognized. To meet the stringent requirements, common procurement requirements were launched, and in 2010, 100 per cent of newly launched eligible products achieved ENERGY STAR standard.
Another focus is on improving the customer return process. Return experience has been improved via enhancements at the Xerox Green World Alliance recycling website (www.xerox.com/gwa). There are three different return methods: (1) single-item return programme, (2) bulk returns on a pallet, and (3) Eco Box.
● Single-item return is a programme for customers to return a single item, for example a cartridge. Customers can submit a cartridge return label request and receive a label for shipping the cartridge by post free of charge. Depending on the types of returned products and the locations of the customers, Xerox decides which recycling centre should receive the returned products. ● Bulk returns on a pallet is a return programme for those who have more than 30 items to be returned. The Xerox Pallet Returns process allows customers to download the Xerox Bulk process, which contains instructions on how to prepare your times and schedule a pickup. ● Eco Box is a programme where customers may order kits of three boxes each at no cost, bundle items together in the box, download a pre-paid label, and return them to the returns partner. In Europe, ‘Close the Loop’ is a company, like Xerox, dedicated to zero waste to landfill recycling.
The company takes cartridges that Xerox cannot reuse, and through its patented recycling process, separates cartridges into plastics, toner powder, metals, and other materials, then cleans and processes them for return to the market as raw materials or new products.
Since copy machines contain chemical (eg toners) the cleaning process has to be hazardous. Advanced technology for cleaning and predicting part reliability has been developed. Instead of traditional solvent-based cleaning and non-hazardous terpenes, Xerox uses automated CO2 blasting to clean up used parts. Advanced technologies are developed to determine range for noise, heat and vibration during use, so that reusable returned parts are selected for reprocessing. Platform design is adopted and parts commonality is emphasized. These features enhance the predictability of field return. Xerox has further extended the concept of remanufacture to product conversion. The new-build remanufacture processes are integrated with the conversion processes. For example, the reusable parts and machine frames of end-of-life machines are used to build new (or ‘reman’) machines, for example Document Centre 220 becomes Document Centre 440.
Xerox also extends its recovery channels further upstream by involving parts suppliers and raw material suppliers, as shown in the above diagram. Machines for remanufacturing and conversion are sent back to Xerox factories. Parts that can be reused are sent to part factories where they are stripped, repaired and reused; parts that cannot be reused but can be recycled are sent to part factories as raw materials. Recycled materials are sent to raw material suppliers to be reused.
Other companies, such as IBM, BMW, Mercedes-Benz, Fujifilm, Kodak, Dell, and many others have been constantly improving their reverse logistics systems to achieve environmental sustainability.
● IBM has to decide how to organize the collection of product returns, and which parties to involve depending on the processes required. In many countries, IBM has a take-back programme allowing business customers to return used products on top of the take-back responsibility that IBM has for the consumer market. IBM has set up a business unit dedicated to the management of recovery, with 25 facilities steering repair, remanufacturing and recycling (also with the involvement of third parties). ● BMW has been conducting recycling research in a pilot vehicle disassembly plant in Landshut, Germany since 1990. There are three main focused issues, the first being the recycling of materials from existing cars.
BMW aims to reuse 80 per cent of all plastics, and has been able to incorporate recycled plastics into certain components such as luggage compartment lining and recycled bumpers. The second focus is the reuse of high-value parts from existing cars with the aim of remanufacturing high-value components such as engines, starter motors and alternators.
Remanufactured parts are sold as ‘exchange parts’ for 50 – 70 per cent of new product prices. The third focus is the design and modification of future cars by avoiding composite materials and marking parts and components to ease sorting tasks. Further, design for disassembly is used to allow parts to be disassembled within 20 minutes. The use of two-way fasteners instead of screws and glue is considered. ● Mercedes-Benz accepts and disassembles EOL Mercedes vehicles to harvest and sell spare parts to both consumers and commercial customers at a significant discount compared to virgin spare parts (Toffel, 2004).