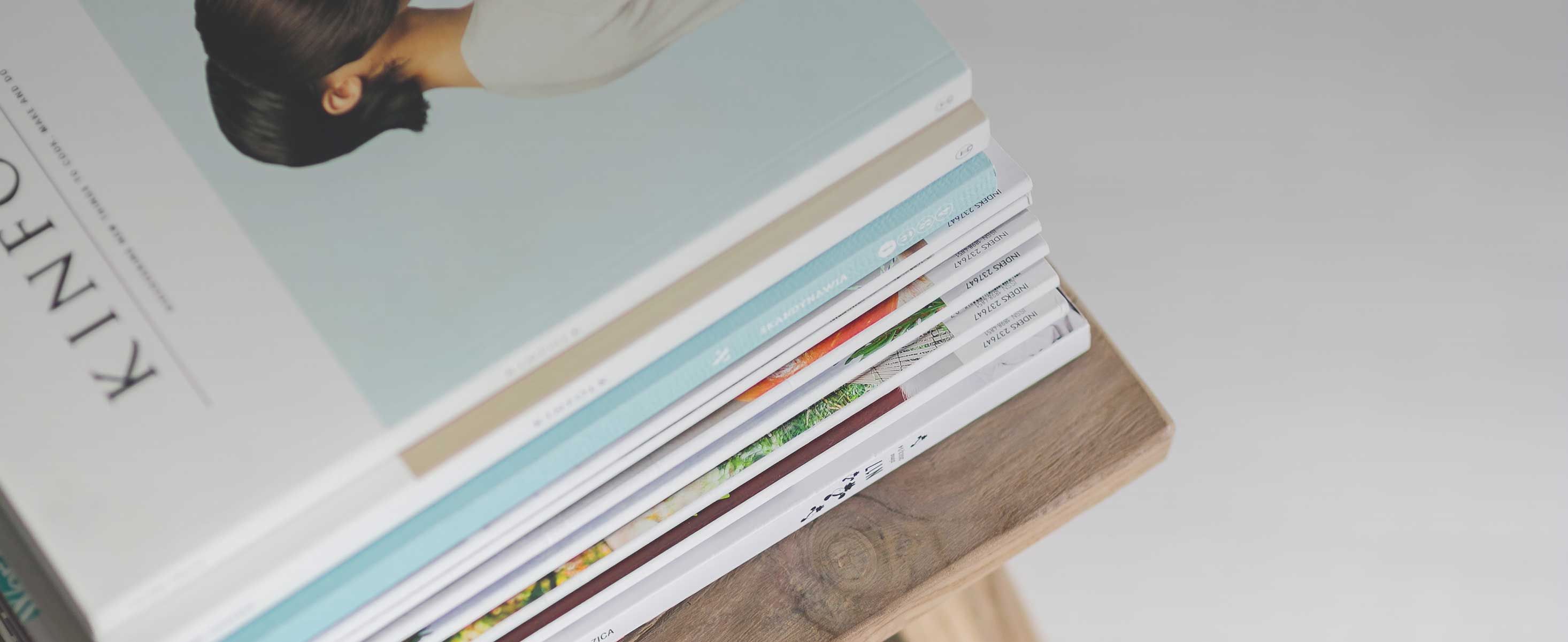
6 minute read
Vehicle Scheduling
for each method will have to be made; remember that it is not only the immediate replacement cost that has to be taken into account but also the cost of operating over a number of years. An analysis must also be made between the various methods of replacement, and such matters as tax allowances and inflation must be taken into account. This will give the true cost of each method and, together with the company’s objectives, strategies, and financial recourses, will enable the selection of the right policy.
The objective of scheduling is to achieve optimum vehicle utilisation by operating vehicles at maximum load and at minimum cost. In carrying out this objective, the fleet manager will wish to ensure that the fleet is used efficiently and that vehicles are available when they are required. Similarly, the manager needs to ensure that the most suitable vehicle for particular loads and journeys are used.
Advertisement
Constraints
In scheduling and routing vehicles, the fleet manager must regard a number of constraints imposed by legislation, the organisation’s resources, and the needs of the customer. Among these are as follows:
• The legal permitted driving hours • The need for drivers to have days off • Speed restrictions • The maintenance and servicing requirements of vehicles, which involve vehicles being off the road • The number of vehicles the fleet manager has at his or her disposal at any one time • The types of vehicles the fleet manager has available, because this will govern the capacity that is available • Depot locations, and the number of depots the fleet manager operates • The types of traffic involved; when schedules are prepared, parcel traffic will be different from heavy haulage • The number of calls to be made and their distance from each other
• The time involved in loading or unloading at each call • Whether an urban area or a rural area is involved • Any special requirements of the trade involved or of customers • Such matters as public holidays, industrial holidays of customers, and local holidays; not forgetting early closing days, if in the retail trade • The type of roads available (e.g., motorways, dual carriage ways) • Temporary restrictions caused by road works, building operations, and similar work • Certain loads may require special routes, to avoid obstructions, or bridges with weight limits and the like
How to Choose the Route
Whilst there are a number of (expensive) software packages available, this is a considerable problem because there aren’t packages that can process every route scenario. There are many factors to consider. Often, there are several ways of selecting vehicle routes and loads for vehicles. These include:
• Pigeon-hole method. This is probably the simplest method and is widely used for this reason. Delivery points are grouped together into geographical areas that have been adopted on the loading deck, usually in special bays.
When the goods for each area are known, a detailed schedule is worked out and a vehicle allocated. This method is most suitable where the number of areas and delivery points are limited. • String diagrams. Another simple method is the use of string diagrams to select the best routes. A good map is required, showing transport depots and customer delivery points. The map will, of course, be to a known scale enabling distances to be read easily. A pin is fastened to each depot location and also at each delivery point. A piece of string is fastened to a depot and taken to each delivery point in the sequence that appears to be the best route. In this way, it is possible to show a number of alternative routes, and the distances involved can be measured. The best route or routes can then be selected. In practice, the maps will be mounted on board and coloured strings will be used to show alternative routes more clearly. An ancient practice I agree, but one that is still in use in smaller organisations around the world.
• Distance saving. This means selection of the optimum routes by first selecting the worst route. This would normally be by making an individual call each time to one customer, we would next try linking the two nearest delivery points together and see what the savings would be. The next nearest point would then be linked up, and this would continue until an acceptable route emerged. • Travelling sales representatives. Visiting each customer by the shortest route and returning to the depot. It has a limited use in practice. • Linear programming. This is an operational research technique developed to show how limited resources can be used to their optimum. As the title suggests, linear is proportional, and assumes that if for instance we have more time we can produce more goods. The basic method used in linear programming is to locate an extreme point of a feasible region; examine each boundary edge intersecting at this point to see if an overlap along any edge would increase the value of the objective function. If this is so, move along the edge to the adjacent extreme point. Repeat until the value of the objective function no longer increases.
For example, we assume that an organisation has depots and stock as follows:
Depots Stock
Anytown Hightown Northborough Westborough
Customer orders are as follows:
30 32 22 26
Customer Order Quantity
Smith Brown Jones 34 40 36
The transport costs from each depot to each customer will be assumed in this case to be as follows:
Customer Anytown Hightown Northborough Westborough
Smith Brown Jones 16 12 6 18 22 16 12 10 14 6 20 18
We are now in a position to select the best routes, for there are a number of alternative solutions available. One solution may be for stock to be allocated as follows:
Customer Qty Depot Route Qty Depot Route
Smith Brown Jones 8 26 4 Northborough (1) Anytown Anytown 26 14 32 Westborough (2) Northborough (4) Hightown (6)
The cost of doing it this way are as follows:
Delivery Route Cost/Item Qty Cost
1 2 3 4 5 6 12 6 12 10 6 16 8 26 26 14 4 32
96 156 312 140 24 512 Total Cost 1,240
This gives us only the cost of using one method. We need to repeat this exercise for each possible method and by a process of elimination discover the most economic route. This appears to present a system of “trial and error,” but linear programming is a planned method of trying all alternatives until the best solution is found. In our example, the allocations and costs are as follows:
Customers Depots: Anytown Hightown Northborough Westborough
Smith Brown Jones
16 26 12 4 6
18 22 32 16 8 12 14 10 14 26 6 20 18
An alternative is for Smith to take one from the Anytown depot; however, if we do this, we must reallocate issues from other depots. The whole exercise must then be calculated to see what the difference in cost in the revised method is, against the original, such as in the following:
Customers Depots: Anytown Hightown Northborough Westborough
Smith Brown Jones
+1 16 26-1 12 4 6
18 22 32 16 8-1 12 7=1 10 14 6 20 18