
2 minute read
THE BRIGHT LIGHTS OF BISHOP
By Parker Allen
Dialight Helps OQ Chemicals Transform and Standardize Their Facility
OQ Chemicals is a worldwide leader in the production of oxo chemical solvent products. The production plant in Bishop, Texas, is a complex facility, producing the everyday chemicals used in various industry segments such as paints and coatings, lubricants and functional fluids, with a need for lighting that can stand up to the elements and provide a safe working environment.
When Marcus Rubio, Bishop’s Senior I&E Specialist II, I&E Team Lead, and I&E Designer, came to the Bishop plant in 2013, the facility had seven different types of lights, ranging from metal halides and high-pressure sodium to incandescent and fluorescent. A selfdescribed lighting enthusiast, Rubio embarked on a journey to upgrade and standardize the facility’s lighting with the primary goals of improving worker safety while reducing maintenance costs and downtime. Additionally, OQ takes the idea of sustainability very seriously –carbon reduction is a global initiative of the company, with a goal of being carbon neutral by 2050.
They initially did a test install of fixtures from two different companies, one of which was Dialight. Fairly quickly, the difference was clear. “The Dialight fixtures had a lower profile and the quality of light was better,” explained Rubio. Some areas of the plant, such as the pump alleys, have low ceilings, and space is at a premium. The Dialight fixtures helped maximize the available working area. Furthermore, they maintained their crisp, clear color long after installation. Rubio continued, “We got the operations folks involved, and we all agreed that we liked the Dialight units more,” explained Rubio.
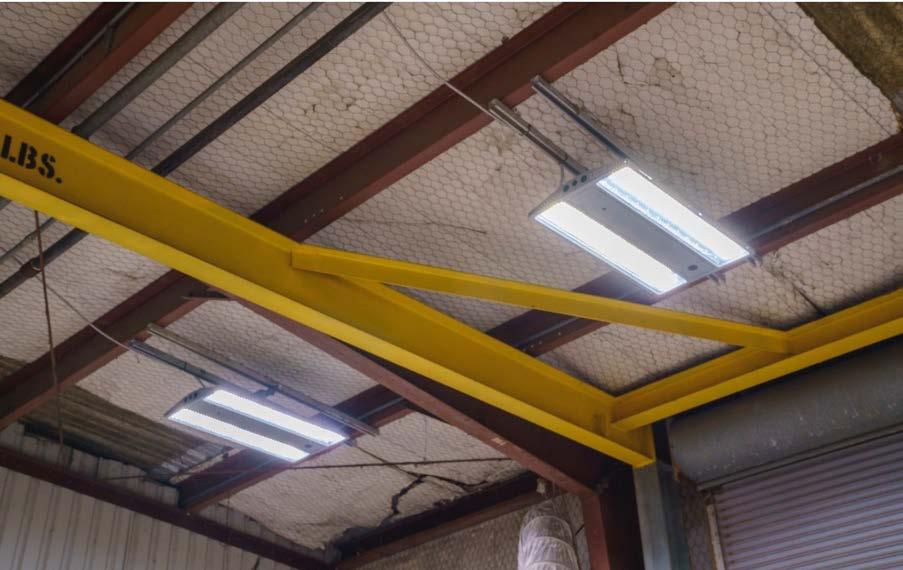
They decided to make Dialight fixtures their standard for area lighting and began the process of converting the entire facility’s lighting. Arturo Saldaña, Regional Sales Manager at Dialight, recommended SafeSite and Vigilant Area Light products. The wide variety of retrofit adapters for these products made swapping out existing legacy technology fixtures to the Dialight LED fixtures quick and easy for OQ’s in-house technicians.
Budget considerations, the bane of every facility manager, limit how much of the large facility can be upgraded each year, so the project has proceeded over the course of several years. Lighting technology changes quickly, posing a challenge for a project of this length. Saldaña updates Rubio whenever they have a new product or product upgrade so that OQ can be sure they are installing the best products with the latest warranties. The goal is to eventually have the entire facility lit with Dialight fixtures. As of now, Rubio estimates that they have replaced close to 400 fixtures.
The energy and cost savings are substantial – an estimated 500,000 kWh of electricity annually, translating to over $50,000 in reduced energy costs every year. Further savings through reduced maintenance costs and facility downtime are harder to quantify but no less real. “We were spending a lot of time relamping, with crews having to erect scaffolding just to reach a single fixture.” Rubio said. But, since they began installing Dialight fixtures, they have only had one lamp failure – and that was due to a wiring issue, not the fixture itself.
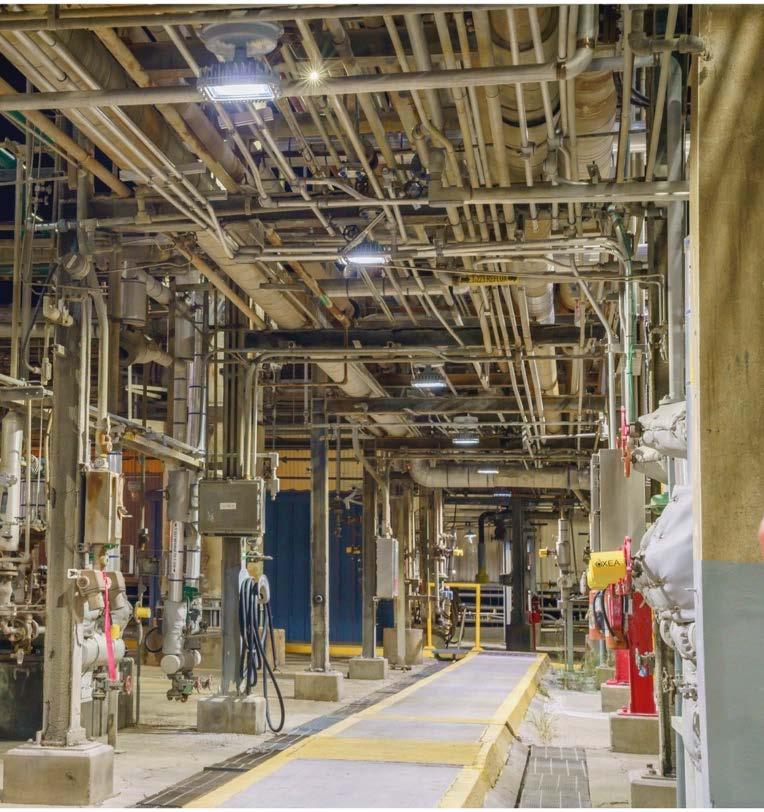
Everyone at OQ has spoken positively about the lighting upgrade, and they plan to have the plant fully converted in 2 years. “Our operations folks are getting all kinds of compliments from employees, vendors and partners about the quality of the lighting in our plant,” Rubio concluded. This is a true success story – a tale of fruitful collaboration between customer and vendor.
A special thanks to Marcus Rubio of OQ Chemicals and Arturo Saldaña for speaking with me about the project. ■
