
6 minute read
Lighting the Way to the Future
A Chronicle of Nissan Smyrna Assembly Plant's Lighting Retrofit Project
By: Randy Reid
Photos Courtesy of Stones River Electric
In a significant move towards environmental sustainability and innovation, the Nissan Smyrna Assembly Plant, located in Smyrna, Tennessee, has embarked on an ambitious lighting retrofit project. This monumental facility, sprawling across a jaw-dropping 6.4 million square feet, has been a cornerstone of vehicle production in North America since its inception in 1983. Yearly, it stands as a testament to manufacturing excellence, churning out a staggering 640,000 automobiles and fostering a robust workforce of over 8,000 dedicated team members.
The transition to a greener future is being facilitated by Stones River Electric (SRE), a company with a commendable track record in lighting ventures across diverse facilities. Through meticulous planning and execution, stretched over several years, SRE has orchestrated the revitalization of the plant's lighting infrastructure. This complex venture entailed a phased upgrade, systematically dividing the plant into various segments, each complying with Nissan North America's stringent lighting standards.
Rob Wilson, LC, CLMC, LEED, President of Stones River, and his consultant Tony Denami gave our Assistant Editor Parker Allen and me a full tour of the facility. Rob explained their first dilemma – birds! During the outdoor tour of the expansive project site, Wilson pointed out the presence of ospreys nesting nearby. The giant birds have larges nests located on two parking lot luminaires, presenting challenges for retrofitting those fixtures. SRE is planning to deliver a new laser proposal in the coming weeks as part of a bird deterrent program.
Many lighting maintenance companies are involved with new revenue streams such as EV chargers, but I have never heard of lighting companies using lasers as bird deterrents!
When we moved inside, Tony explained the overarching goals for the project:
1. Timely Completion: Ensuring that the upgrades progress in a phased manner, adhering strictly to the budget and schedule, with distinct focus on priorities defined for each phase.
2. Uninterrupted Production: Upholding the principle of continuous production flow, aiming for minimal disruptions in the facility’s operations.
3. Minimal Schedule Changes: Strategically scheduling the upgrades primarily during weekends and annual shutdowns to necessitate minimal alterations to existing timelines.
4. Energy Efficiency: Aiming for a significant reduction in energy consumption through the integration of highly efficient lighting fixtures.
5. Advanced Lighting Control: Implementing unique, addressable lighting systems that are primed for optimal energy management.
6. Enhanced Visual Experience: Revolutionizing the facility's visual environment through balanced lighting, augmented light levels, and consistent illumination.
7. Comfort for Workers: A commitment to enhancing worker comfort by reducing eye strain and glare, facilitated through strategic placement of lighting fixtures.
The Stones River team audited the entire 6.4M square foot plant and uncovered a mixed basket of old technology including metal halide high bays and low-bays, T8 and T5 HO retrofit luminaires, and 2x4 fluorescent troffers in the office. Rob stated, “There were probably eight different types of fixtures, and when you include the fact that each fixture had different wattages, there may have been 30 different fixture & wattage combinations.”
The team counted 11,416 luminaires that were ripe for replacement. Rob explained that all fixtures were replaced with two SKUs: ABV4 series high bays and ALC6 linear industrial lights from Current Lighting. Because each fixture is individually controlled with Daintree software, luminaries could be commissioned to the required light level, negating the need for different wattages.
As we discussed the tremendous energy savings, Rob reminded me of the vital interconnection between lighting and HVAC systems. Substantial savings were achieved through the implementation of lower wattage lighting solutions that, because they produce much less heat, result in reduced air conditioning costs.
Regarding maintenance, throughout the tour, Rob pointed to luminaires that were 20 feet, 30 feet, and even 80 feet high. More than 50% of the luminaires were located above working equipment. Replacing burned out lamps and ballasts above the working equipment had always been challenging. Although Nissan typically has an annual 2-week shutdown for equipment maintenance, sometimes lighting maintenance can’t wait. The long-life LED retrofits resolve these maintenance headaches.
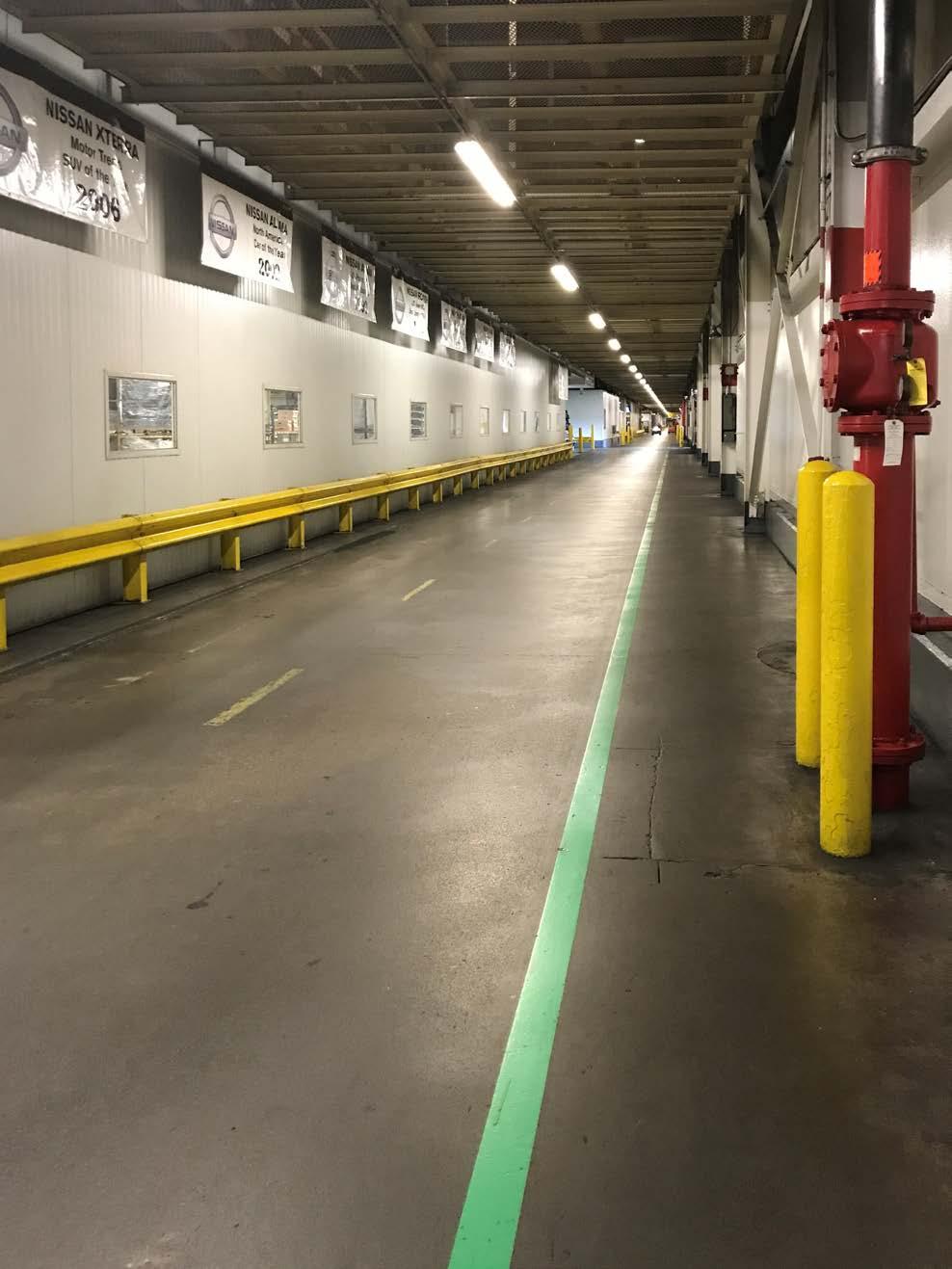
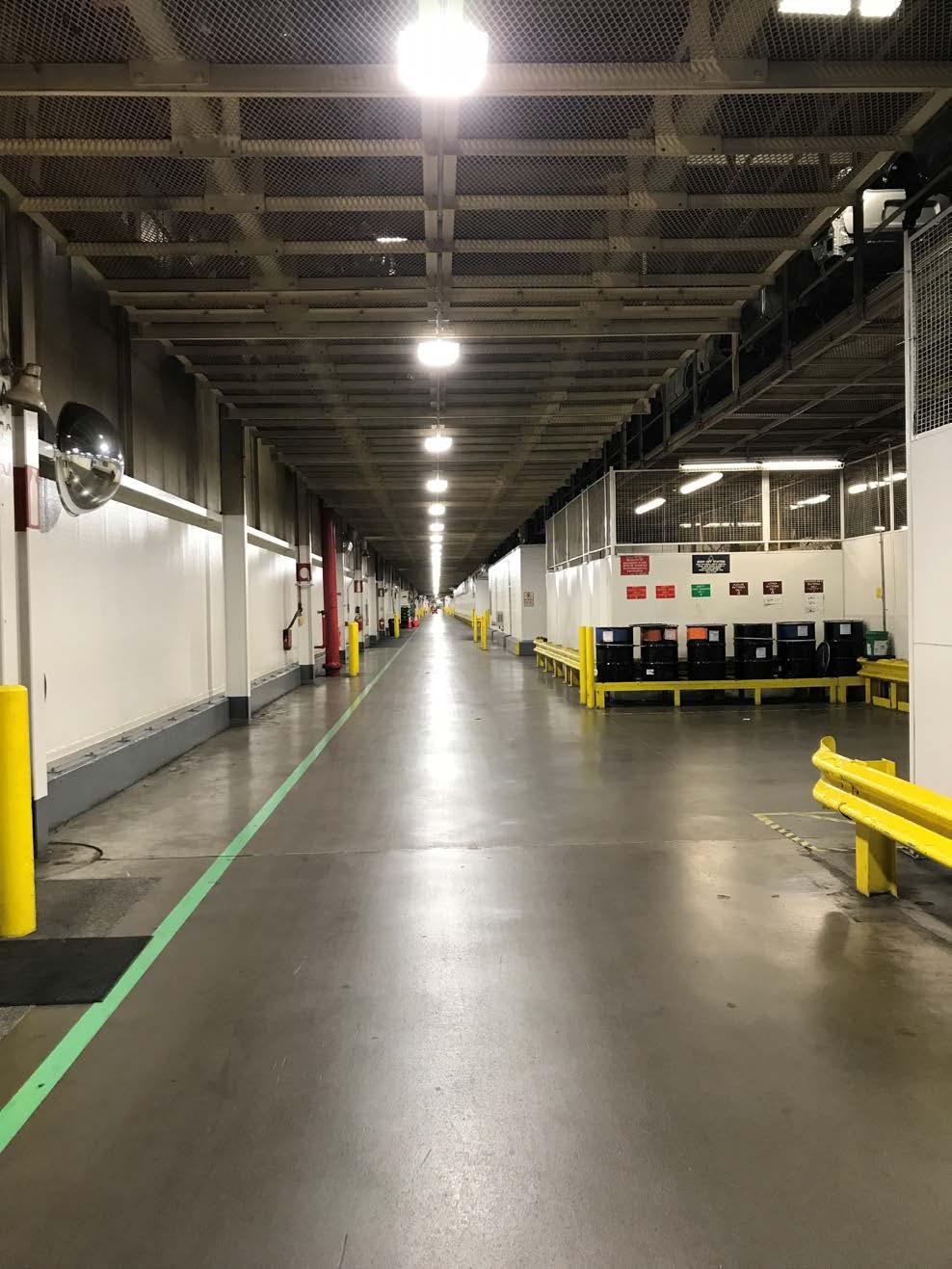
Tony and Rob also explained the complexities and opportunities presented by various TVA rebate programs. In addition to the substantial energy savings achieved by the project, many other benefits were also rewarded. Utility rebates for the project were applicable through TVA’s Energy Right Program. SRE is a TVA PPN provider and facilitated these incentives through multiple applications. The project provided significant maintenance and HVAC cost impacts while providing a very aggressive watt per square foot metric. This project has also been designed in compliance with the EPAct 2005, including the updates within the Inflation Reduction Act of 2022. When you evaluate the full financial impact of the program; a payback of less than five years was achieved.
The COVID-19 pandemic imposed serious challenges and underscored the need for flexibility and adaptability in navigating unforeseen obstacles. This period necessitated significant adjustments in strategies, particularly in areas concerning financing and supplier dynamics. In spite of these challenges, the team acknowledges the remarkable role of Current, who played a vital role in ensuring the project progressed smoothly.
Furthermore, Wilson and Denami accentuate the transformative capabilities of Bluetooth sensors in revolutionizing logistics and supply chain management within Nissan. Wilson emphasized the pivotal role of commissioning in these complex projects, which SRE included in their package. He outlined the intricate details involved in crafting individually addressable systems, which although a tad more complex compared to more traditional systems, bring a whole new level of customization and efficiency to the table.
The transition to these advanced systems signals a move towards greater integration of IT infrastructure, encapsulating an astonishing 11,000+ nodes. The technology, they note, heralds a future of allowing Nissan real-time tracking of assets, pinpointing operational inefficiencies, and crafting streamlined processes, thereby saving both time and valuable resources. This innovative approach is a strong benefit of the Daintree software which was quantified in the payback. As strong as the energy savings story is, it could be dwarfed by efficiencies from inventory management. Rob emphasized the licensing intricacies, indicating a nuanced understanding and handling of the various components, including partnerships with giants like Current Lighting, that go into orchestrating such a massive project.
The Smyrna facility is one of three Nissan facilities in the region. With Smyrna near completion, Rob and SRE are setting their sights on the other two facilities as well.
This immersive journey portrays not only a facility transitioning into a beacon of innovation and sustainability but also signifies the pioneering role played by Stones River Electric. This venture marks a luminous pathway to a future where technology synergizes seamlessly with environmental stewardship, heralding a brighter, greener tomorrow.

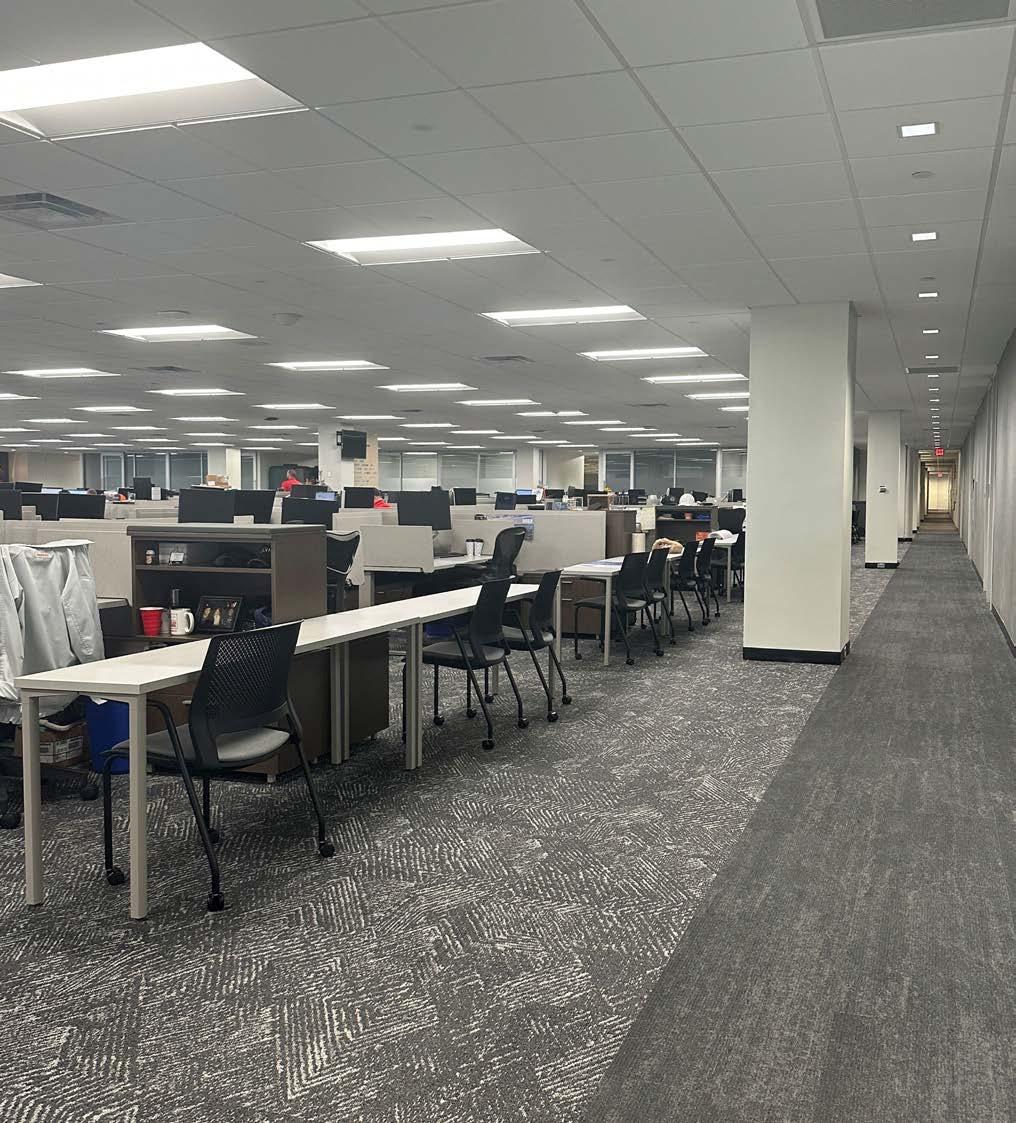