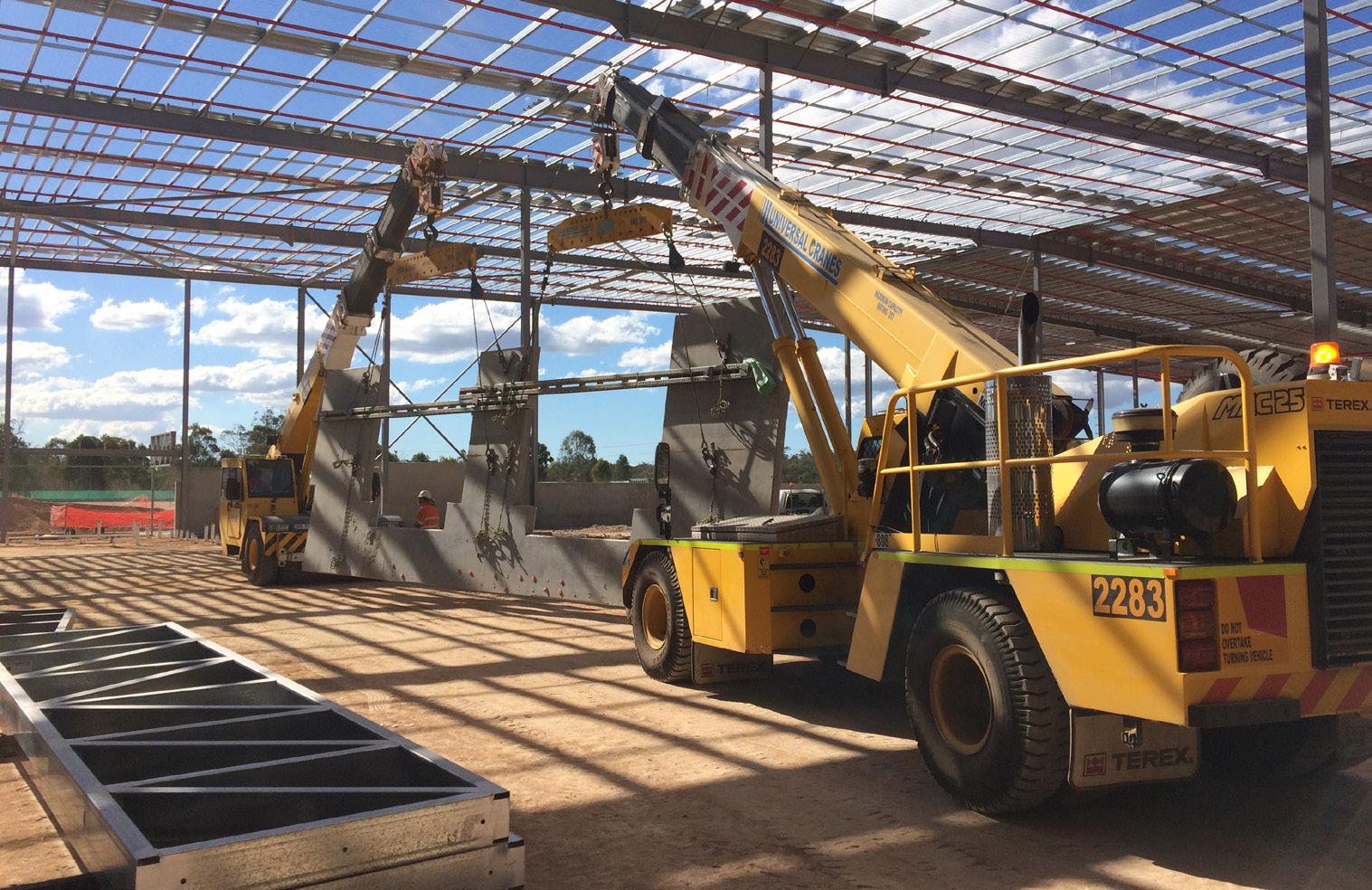
10 minute read
EDITORIAL
From the Editor Q1, January - March, 2020
Welcome to the Q1 2020 edition of Lifting Matters.
Advertisement
I hope all our readers enjoyed a safe and happy holiday season.
This issue we are exploring tilt-up panel and precast concrete erection. The sheer dimensions and proportions of concrete panels present unique challenges for the crane industry. The heavy but flat load is awkward and difficult to rig and maneuver, and sadly when not handled correctly can result in tragic accidents.
We have several experts weighing in on how best to manage tilt-panel jobs, including Adam Courtney from Universal Cranes, John Humphries from CICA, Daniel Blank from Smithbridge, and Worksafe Qld.
I encourage you to invest time reading our People Profile this issue. Derek Thomas, owner of crane training school Crane Elite, shares a very personal and tragic experience as a crane driver which fueled his passion for ensuring everyone in the crane industry receives the right education and training. We explore the themes of Derek’s experience further in an article from Peter G Furst of IRMI, delving into practical ways we can ensure we create a culture that says everyone is responsible for safety. Please get in touch with us! You can visit us on Facebook, LinkedIn or drop us an email any time. If you have an incident report, ideas about safer and more efficient ways of working, widespread issues, valuable reminders or anything else safety-related, we want to hear from you. We look forward to working together to protect our people and save lives in the crane industry.
Any contributions for our next edition are due by 13 March 2020. If you prefer printed glossy copies for your crane cabs, cribs, mess hall, or reception, please send your postal address and the number of copies you require to liftingmatters@ writestrategy.com.au.
Lifting Matters is available to view at www.liftingmatters.com.au, or you can subscribe to receive an email copy each quarter.
Stay safe and see you next edition!
Thank you
DASHELLE BAILEY, EDITOR liftingmatters@writestrategy.com.au
Contents
EDITORIAL
4
FEATURE ARTICLE Safe work with precast concrete
INCIDENT REPORT Brisbane, Queensland Gold Coast, Queensland Perth, Western Australia Noosaville, Queensland Austin, Texas Greensboro, North Carolina
TOPIC COMMENTARY Cranes and precast panel erecting
6
12 14 16 18 19 22
24
WORKING SAFELY Guide to managing risk in construction: prefabricated concrete
28
OPERATOR’S OPINION Dan Blank
30
PEOPLE PROFILE Derek Thomas
TRAINING & DEVELOPMENT Everyone is responsible for safety: the myth and solution
32
34
Safe work with precast concrete
ADAM COURTNEY Sales Manager Universal Cranes
Working with concrete panels is one of the most dangerous activities in the crane industry. There are many hazards to be aware of including rigging and clutch failure, ground conditions, weather conditions… the list goes on! Most notably, there have been fatal accidents with concrete panels because of their sheer size and weight, most often involving a dropped load due to failure of the concrete or lifting insert. To safely lift and place concrete panels we must understand how to minimise the risk associated with lifting insert failure and/or concrete failure.
But first, precast concrete basics
Many of our readers will have had some involvement in precast concrete erection at some stage in their careers, but for those of us who haven’t yet come across these kinds of lifts, let’s cover some basics.
Precast concrete is widely used in the construction industry due to its versatility in shape, texture, and colour. Typically, there are two types of concrete panels: precast that is constructed off-site and
transported to site, and tilt-up that is constructed on site. Both require cranes to lift the concrete panels into place.
1. Precast Concrete Panels:
Precast panels are manufactured by casting concrete in a reusable form system which is then cured in a controlled environment such as a factory, transported to the construction site by semi-trailer, and lifted into position with a mobile or tower crane. The typical weight of a precast panel is 1 to 10 tonnes.
2. Tilt-Up Panels:
Tilt-up panels are manufactured onsite using temporary casting beds. When the concrete has cured, the panels are lifted off the casting bed and rotated into a vertical position using equalising rigging arrangements, prior to final installation with either a mobile or crawler crane. Tilt-up panels typically weigh between 1 to 50 tonnes.
The panels can be erected by a variety of crane types. There are three types of cranes mainly used in the erection of precast and tilt-up panels.
1) Tower Crane:
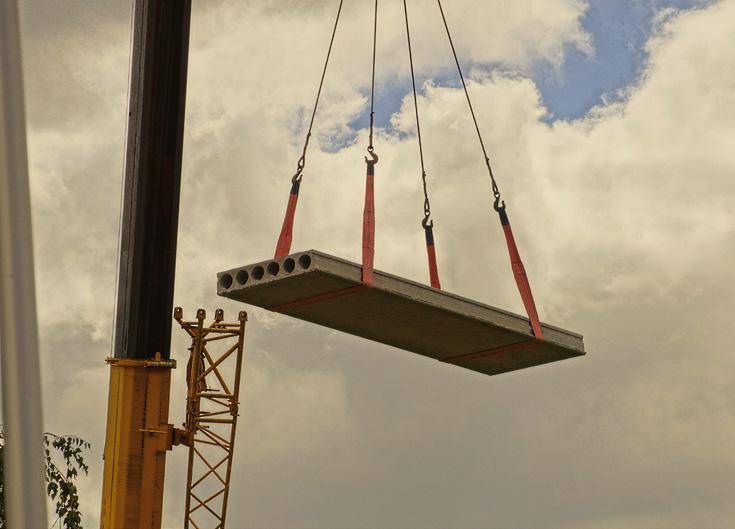
A tower crane is generally erected and used in metro areas where space is limited, often on high rise buildings. The precast panels are transported to site using semi-trailers where the tower crane lifts them off and places them into position.
2) Mobile Crane:
A mobile crane is also typically used in metro areas due to space limitations. The average size for a mobile crane for this application is between 60 and 350 tonnes.
3) Crawler Crane:
A crawler crane is used outside metro areas due to its physical size and transport restrictions. A crawler crane is typically used in industrial estates erecting panels for new commercial buildings and factories. One of the benefits of the crawler is that it can track around the site with a load, meaning panels can be cast either on- or off-site. Like the mobile crane, the crawler tends to be onsite for one day to one week at a time. The average size for a crawler for this application is between 80 and 150 tonnes.
Lifting Inserts & Clutches
Perhaps the most critical element of safely lifting concrete panels is the lifting inserts and clutches. Lifting inserts are used for safe and efficient installation of concrete panels and are designed and manufactured by specialists. They are cast into the concrete panel to aid lifting and installation by a crane.
A lifting clutch that is compatible with the lifting insert is also used as part of the rigging arrangement.
There are two most used lifting inserts:
1.
2.
For general use, round bodied anchors
In Australia, the most popular lifting inserts are ‘hairpin’ plate inserts for edge lifting, with or without a hole for attaching extra reinforcements.
Three different examples of lifting inserts As mentioned, lifting inserts require specialised design and manufacturing. Accidents involving concrete panels most often occur due to the failure of the lifting insert or surrounding concrete when the engineer’s specifications are not met.
To ensure a safe concrete panel lift, you should ensure:
The correct lifting insert is used as per the engineer’s design specifications, as well as the correct lifting clutch for the selected lifting insert
The slinging arrangement is suitable for the lifting insert and clutch configuration
The lifting clutch has been appropriately maintained and is not damaged
During the lift, inappropriate shock loading does not occur when lifting or moving the concrete element. This can happen due to poor rigging practices, panel handling or panel preparation
Other factors that should be considered by the party responsible for the precasting include the concrete strength, curing time, the depth of the anchor embedment, and correct void formers.
Mitigating these risks

1. Lifting insert and clutch specifications
It is imperative lifting insert and clutch specifications are as per the relevant standards. According to Worksafe Queensland:
Lifting insert systems should have a minimum guaranteed factor of safety of 2.5 to 1 against failure of the anchor, the concrete, or any reinforcing to which the insert relies upon for its anchorage. For instance, an insert for a 10 tonne working load must not fail at less than 25 tonnes when installed in accordance with the manufacturer’s and engineer’s specifications. Lifting clutches should have a minimum factor of safety of 5 to 1 against failure.
Be sure to check your local requirements.
2. Lift engineering and design complies with AS 3850 Tilt-up concrete construction
All panel designs must be verified by a suitably qualified engineer. AS 3850 Tilt-up concrete construction outlines the requirements for both precast concrete panels and tilt-up panels cast on site. In some jurisdictions, local safety bodies have adapted this standard into a Code of Practice. For example, in Queensland, Australia, Workplace Health and Safety Queensland issued the Tilt-up and precast construction Code of Practice, which is approved under section 274 of the Work Health and Safety Act 2011.
3. Quality assurance
Appropriate QA must be conducted on the concrete panel construction and verified against the engineer’s design. The concrete strength must also be tested.
Lateral brace
End brace
Main brace
Knee brace
Panel Bracing
The other critical hazard in concrete panel erection is bracing. Bracing is a temporary support system for concrete panels to ensure they do not overturn or collapse during construction. They are usually placed diagonally and designed to resist lateral forces such as wind loads. The bracing is used to hold up concrete panels until all structural connections between the load-bearing panels, roof and floor diaphragms are complete.
Each panel is supported by at least two braces throughout the duration of construction.
Bracing details for concrete panels must be specified in the engineer’s design, including the type, angle, configuration and size of erection braces. Bracing should be designed, manufactured, inspected and maintained to a recognised standard such as AS 3850 Tilt-up concrete construction. There are extensive requirements for bracing design, which varies depending on the bracing type. Ensure you understand the requirements for fixed versus adjustable braces, brace connections and anchors, and base restraint. According to Worksafe New Zealand, brace connections should be designed with a factor of safety of 2.5 against failure. When post-installed drilled-in inserts are used to attach a brace, they should be designed with a factor of safety of 3.0. Be sure to check your local requirements.
Winds & loading
Due to the shape of precast panels and their large surface area wind is a particularly important hazard to consider in tilt-up panel erection. Wind can easily affect the load if caught on the right angle, causing the load to move laterally and affecting the crane’s stability and integrity of the boom. The crane’s working wind speed will need to be reduced in windy conditions when lifting large precast concrete panels, and in extreme conditions the lift should be delayed until wind eases.
When it goes wrong
A recent example of a panel erection lift gone wrong was an incident on the Gold Coast, where a 100 tonne crawler crane was lifting a 16 tonne concrete panel and the lifting clutch link broke. This caused two of the lifting points to become ineffective and the panel was dropped. Fortunately, no one was injured in the process. The lift failure was caused by a cracked lifting clutch link which went unnoticed. A reminder, those lifting inserts and clutches are absolutely critical in concrete panel erection. Check the design and the condition of all the required equipment before executing the lift. More details on this incident is provided in the incidents section of this issue.
This incident serves as a good reminder to ensure a rigorous inspection and testing program is carried out on lifting clutches, possibly beyond the current minimum industry benchmarks. AS3850 does outline the requirement for non-destructive testing (NDT) of lifting clutches at manufacture but does not require any NDT during 12-monthly inspections. To prevent these kinds of unexpected failures, Workplace Health and Safety Queensland encourages relevant parties to consider carrying out NDT to inspect for cracks at the 12-monthly inspection.
Changes in the Industry
There have been significant safety improvements in the pre-cast panel industry over the last ten years, including the introduction of backup axillary lift points to account for rigging or structural failure on pre-cast panels, and the introduction of face fit testing and protective equipment to protect workers from silicosis. These are just two examples that have helped create a safer environment when working with pre-cast and tilt-up panels.
Want to know more?
For further information on the erection of tilt-up and precast concrete elements please refer to the following: Tilt-up and pre-cast construction Code of Practice 2003 AS 3850 Tilt-up concrete construction