
3 minute read
JC Impellers
electrolysis, erosion, and radial thrust problems.
Forms of imbalance
Advertisement
Using a diagram Kozel highlights how the weight of an impeller can cause damage. Comparing a bronze impeller weighing 54kg to one made of carbon fibre weighing just 9kg he highlights the shaft deflection caused. This bending or displacement of the shaft, in turn, causes premature wear on the bearings, the mechanical seals, rotary, stationary and casing rings. There are three major forms of imbalance - mechanical, hydraulic and radial thrust imbalance, says Kozel. "Mechanical balance can be a static imbalance, referring to the inability of a stationary object to balance itself without movement, or rotation, or it can be a dynamic imbalance, which on the other hand, is the inability of an object to balance while in motion, or rotation." The hydraulic imbalance is every bit as damaging as a mechanical imbalance. "This is when there are unequal thrusting (forces) in different directions. For example, if the exit ports of an impeller are not equally spaced and unequally sized, the forces, or thrusting that will occur at the Cut-Water of the pump will be greater in once direction than another causing the shaft to deflect every time that exit port passes the cut-water of the pump.” Radial thrust imbalance results from very high radial forces that occur when the pump is operating away from the original design point, or best efficiency point (BEP). In volute pump casings, uniform, or near-uniform pressures act on the impeller when the pump is operated at the design capacity (BEP). At other capacities away from the best efficiency point (BEP), the pressures around the circumference of the impeller are not equal and this results in high radial forces. These high radial forces are pushing down on the impeller and consequently the shaft. "Operating outside the BEP is problematic. We have had examples where the pump was operating at 74% of BEP but was vibrating so much that it could not be kept operational. The same happens at 110% of BEP." Kozel says it is best to operate within 5% of the BEP. “Far too often customers opt for a cheap solution or a bootleg import when it comes to propellers. They don’t consider the imperfection on it and are shocked when it starts to cause problems.”
Finding solutions
Preventing impeller imbalance starts with using a lighter weight, 100% machined impeller, says Kozel. "Also use casing rings (non-cast, or moulded, and machined from solid blocks of material) that do not corrode, or go into an imbalance." He says carbon fibre impellers are 85% less weight than bronze or stainless steel impellers and rings and do not go into an imbalance, because the vane passageways and exit ports are all equally spaced as a result of being machined from one centre position from solid blocks of the structural composite. “At SIMS impellers are designed and engineered to make the Operating Point the Best Efficiency Point (BEP) This is extremely important, because not only does it make the pump much more efficient, but it reduces radial loads, shaft deflection, and eliminates hydraulic and mechanical imbalance! This allows the pump to operate substantially longer without premature failure of the bearings, rings, bushings, sleeves, mechanical seals, and motors,” he says.
Sims Pump Valve Co. Inc, simsite@simsite.com, www.simsite.com
CASTING QUALITY COMPONENTS
JC Impeller Foundry specialise in manufacturing all types of castings including impellers and other pump components for the pump industry in SA. Cast Iron, SG Iron, LG 2, P8 1, Chrome Iron and Steel & Stainless Steel.
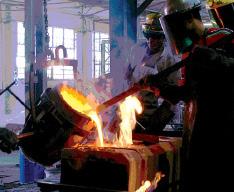
Tel: +27 (0) 11 827 1913 Email: gladman@jcimpellers.co.za Website: www.jcimpellers.co.za
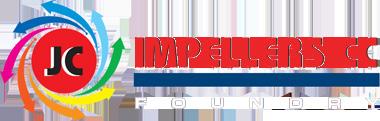