
2 minute read
Overhaul after 10 years
A sensor or sensors to capture data from an environment, a microprocessor to handle the output of the sensor via programming; and communications capabilities to enable the system to communicate the microprocessor’s output for action.” He says already the industry is benefitting from the smarter equipment being developed. “For the longest time, reactive maintenance was the norm. This is a run-tofailure approach and repairs are unplanned. This approach typically works for non-essential or low-cost equipment that can easily be repaired or replaced.” Preventative maintenance – a far more preferred approach – saw businesses establish a routine of regularly inspecting equipment to look for and fix issues before they turn into major problems. “This is a periodic approach and less costly for an operation than reactive maintenance. Smarter machines, however, allow for condition-based maintenance which is where the real benefit lies. This is where the pumps or systems are giving early warnings of the potential failure,” explains Wissner. “When conditions reach a pre-determined unacceptable level, equipment is repaired. Realtime equipment condition is considered for planning the time and scope of repair.” Not only is this a far more predictable approach but also far more cost-effective as downtime is reduced and unexpected failures are completely removed from the equation. “Condition-based maintenance provides tangible business benefits,” says Wissner. Studies have shown this includes a reduction in maintenance costs of between 25% to 30%, elimination of equipment failure of up to 75%, a 35 – 45% reduction in downtime, an increase in production of 25 and ten times return on investment.
“Condition-based monitoring ensures unparalleled reliability, availability and enhanced maintenance. Realtime sensors that are integrated into the drive system allow for a variety of conditions to be monitored ensuring maintenance of your equipment is never reactive.” Wissner says some of the conditions monitored by these integral sensors include, but are not limited to ambient temperature, humidity or the presence of chemicals like hydrogen sulfide.
Advertisement
Siemens South Africa, +27 (0) 11 652 2000, discover.za@siemens.com, www.siemens.co.za
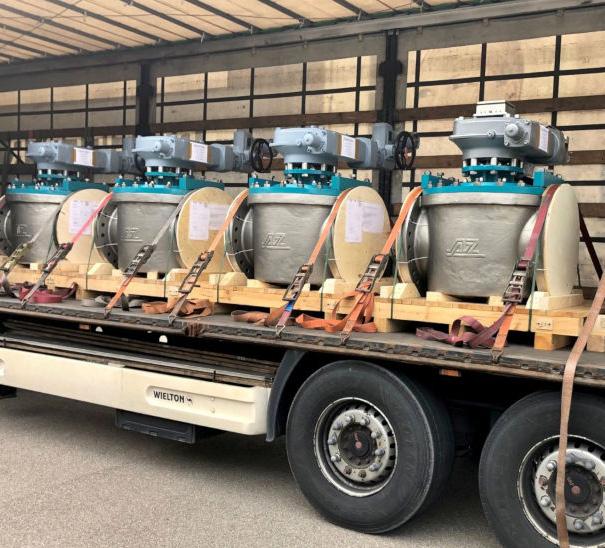
The valves were in use for about 10 years, the total of five 20″ and 16″ plug valves with full bore design at our customer’s plant (manufacturer of polypropylene and polyethylene). Now the valves have been completely overhauled while the customer‘s plant was in a planned maintenance shutdown, starting at the end of April. In the meantime, the valves have been delivered to the customer and reinstalled, where they continue to function reliably as is expected of AZ Armaturen. Repair time at AZ Mönchweiler was 3 weeks only.