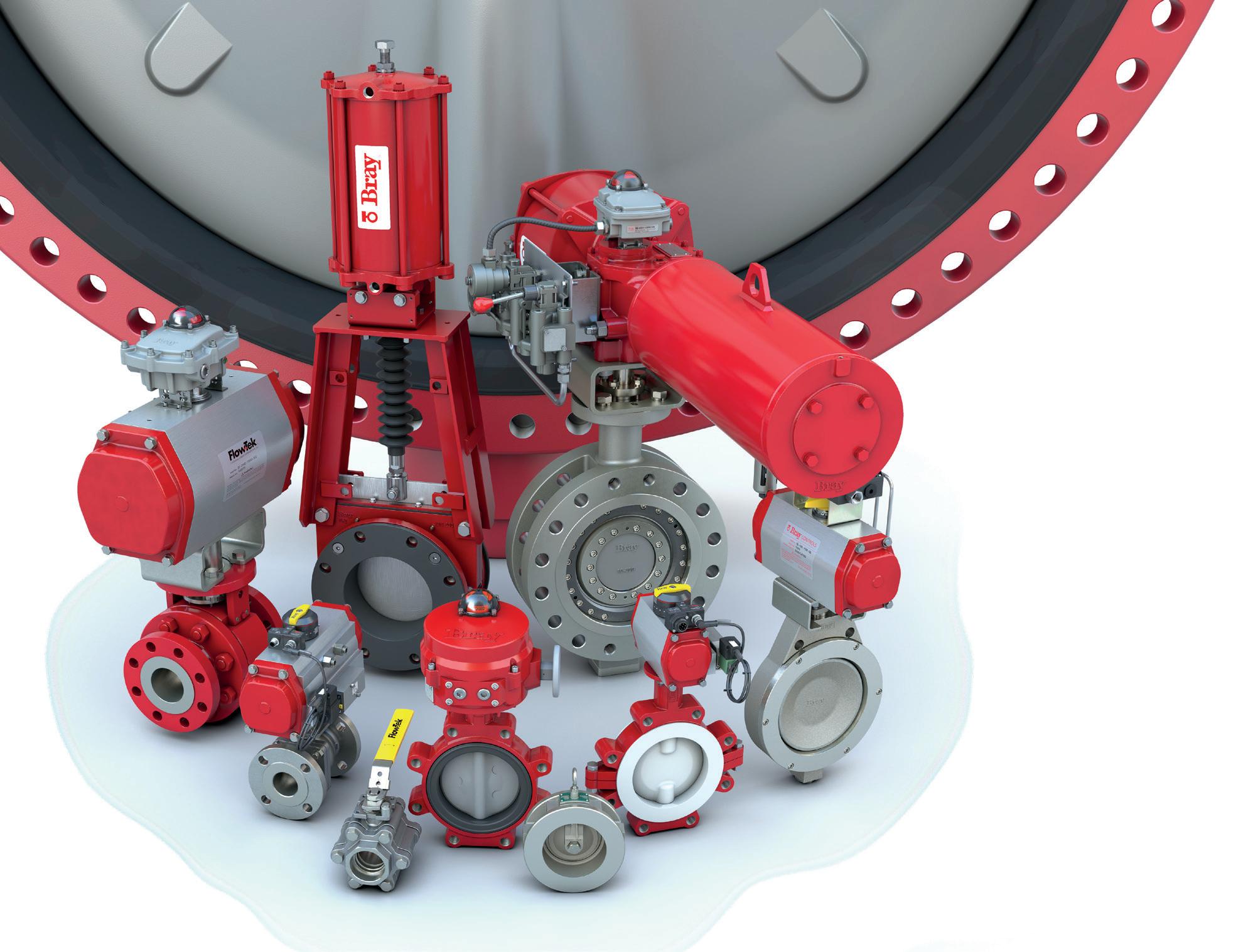
2 minute read
Bray Industrial Valve Summit IBC Invincible Valves OFC KSB IFC
flow capacity, differential head via pressure, pump input power and shaft speed. Also, the bearings, fluid and surface or skin of the pump must be tested along with the accelerometers and proximity probes.”
Standing the test of time
Advertisement
Sharing a case study during a recent online presentation Papadakis said thanks to expedited testing excessive clearance was uncovered in a critical unit used in an oil refinery. “The bearing barrel pump operated with gasoline type fluid which is very hazardous and therefore it was critical to making sure the pump was efficient and operating at top functionality before it was returned to the field after being sent for repairs with the Original Equipment Manufacturer (OEM).” – so any fluid leakage was dangerous it did have benzene and hydrogen sulfide in the fluid and so a dual cartridge seal in the pump to ensure liquid does not make it out of the pump. He said during the performance test the pump ran for 12 minutes operating on a mix of half speed and full speed, but the concern was raised when the temperatures increased very quickly to 197 °F (89,4 °C). “At around 200 °F (93,3 °C) we would shut the pump down and so the fast spike in temperature when the pump was running at full speed was worrying. We realised there was an issue because the temperature was rising in just too short a period.” He said whilst the total dynamic head was found to be the same as stipulated by the OEM, the test found the power curve to be much higher than that of the OEM’s curve. “This led to a thrust bearing inspection and it was established that the clearance between the thrust bearing and bearing housing was larger than the OEM specifications. This excessive clearance or gap was allowing for oil to build up in the cavity which caused the excessive heat.” He said once the problem was identified it was just a matter of fixing the problem – in this case sending the unit for machining to skim cut the end-cover and reduce the gap. A second performance test was conducted and the pump was given the go-ahead to return to the field. “What would have happened without having this test is that the unit would have gone from repair straight back into operation where temperatures would have continued to climb ultimately leading to the thrust bearing wiping out and catastrophic damage to the mechanical seals and impellers. This would have resulted in serious cost, the pump having to be sent back for more warranty work, more downtime and costly replacement of parts.” Katapodus said thanks to the performance test this was all prevented. “The moral of the story is don’t wait until it is too late. Listen to your pump. Too often the lack of testing results in failures happening in the field and that automatically doubles the costs. The time and cost of testing are still far less than that of unanticipated downtime and operations coming to a halt because of a faulty pump.”
Hydro Pumps, +27 (0) 12 807 3256, sales@hydropumps.co.za, www.hydro-solutions.co.za
HIGH PERFORMANCE FLOW CONTROL
Bray provides high performance flow control solutions to handle your most challenging applications.
To learn more about our complete portfolio of valves, actuators, and controls, visit us online at BRAY.COM
Bray Controls Africa (Pty) Ltd
Unit 11, ABC Business Park Mastiff Rd, Linbro Business Park Sandton 2090, South Africa Telephone: +27 10 007 3222