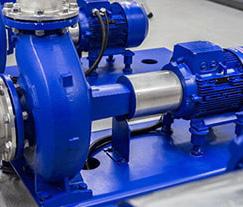
2 minute read
BMG
one is monitoring from an office desk or home, as long as there is an internet connection, condition monitoring can take place remotely ensuring the ability to see what is occurring in the assets.” It furthermore reduces human error. “Walk-throughs are inconsistent and infrequent. When continuous condition monitoring is done on a 24/7 basis, it eliminates exactly this. There is also a collection of data 24/7 which in turn removes the need for fingerpointing of what caused what issue when an error has occurred and it creates an opportunity for training.” The training element is important, says Zepp. “With the rate of skilled labour retiring training opportunities are important. It is estimated between 25 to 30% of skilled labour will be retiring in the next seven to 10 years with little or no backfill in those positions. Also, those positions that are being filled are not done with people who have the experience of those that left. We need tools for these new employees to bridge the experience gap.” It also allows for a proactive approach rather than always being reactive. Thanks to the ability to detect anomalies early downtime is significantly reduced. “By having a notification system in place any anomalies can be detected meaning incidents are completely prevented as any kind of failure or problem that can cause machine downtime is prohibited. It is simply picked up before it even happens.” Another benefit is that when data is collected 24/7 across pumps, it delivers a business the ability to compare equipment performance. “One can overlie or correlate data from different assets to see if they running on the same curve making sure that all of the pumps are functioning optimally.” At the same time because it requires less human intervention than all walk-throughs and less downtime and maintenance it significantly improves manpower utilisation by prioritizing and addressing the assets systematically. “During a shutdown, for example, it allows for the assets that need to be focused on to get attention.” Zapp says this type of condition monitoring increases equipment reliability ultimately prolonging the life of the pump, the bearings and the seals saving cost and revenue. “It also increases safety,” he says. “It goes back to remote monitoring because if you are monitoring from an office the risks of manual walk-throughs are eliminated.”
Addressing the cause
Advertisement
Research has shown that seals are the most common component to fail in a pump causing at least 69% of all failures followed by the second most common component bearings responsible only for some 10% of failures. “Seals can fail due to process pressure and temperature variations triggered by changes in suction and discharge due to flow restrictions or valve regulation,” says Zapp. “Seal failure also happens over a very short period versus bearing failure. When one is collecting data, for example, every 30 seconds with the gateway in the cloud, those very early signs of failure can be picked up long before it becomes a problem.” He says it is important to therefore not just monitor vibration alone as it is simply not addressing the largest cause of pump downtime. “Bearings can be monitored through vibration alone, but seals are not bearings just as pumps are not motors.” “To efficiently address the issue, it is important to monitor operating temperature and operating pressure in conjunction with vibration to detect potential misoperation and failure of seals.”
A.W. Chesterton, info@chesterton.com, www.chesterton.com
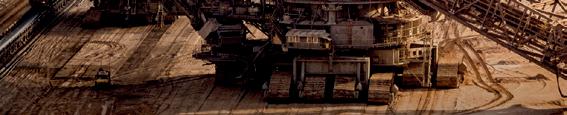