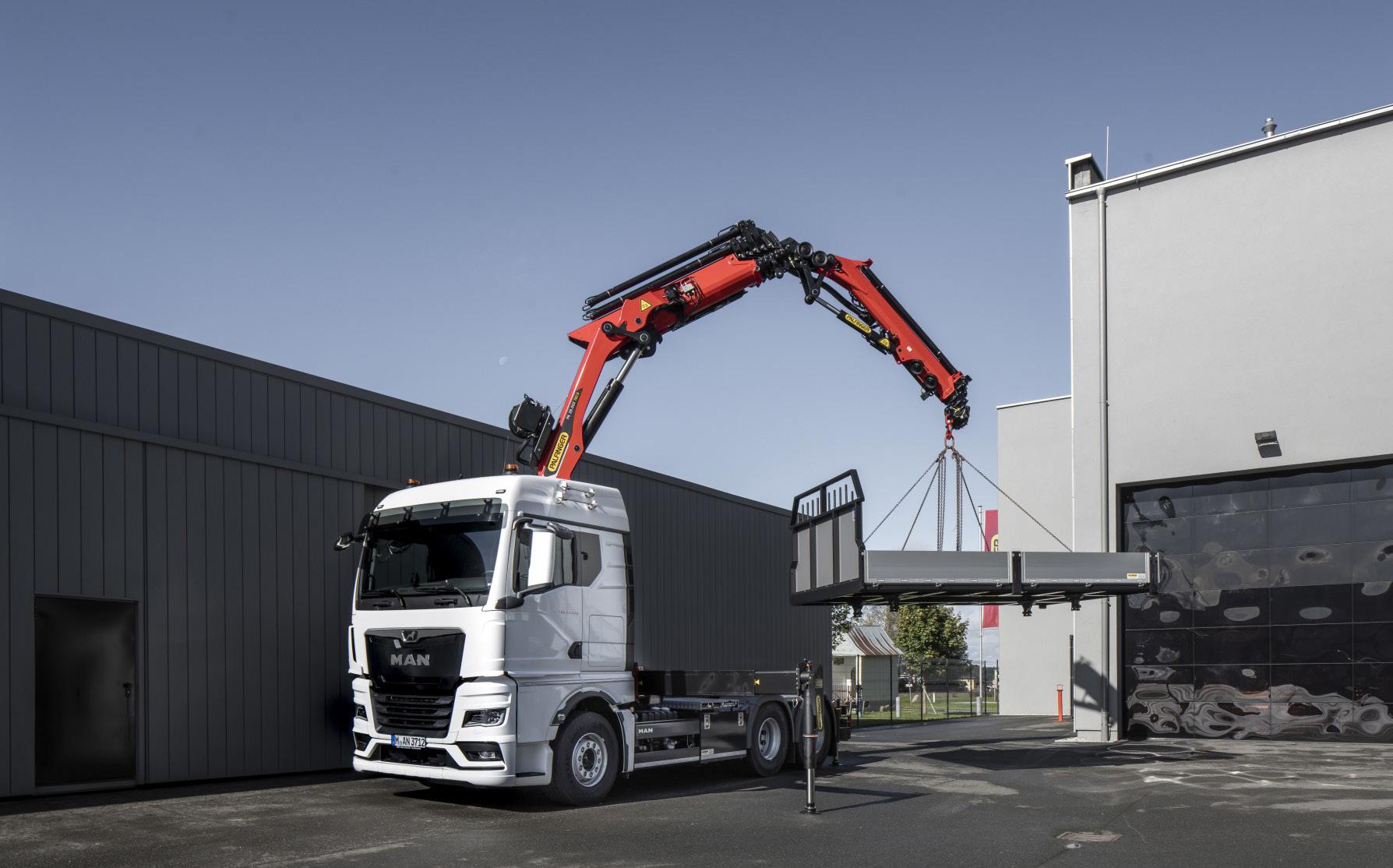
5 minute read
Digital solutions introduce efficiency
Heavy loads, constricted sites and short time frames are but a few of the challenges lifting companies face when serving the oil and gas industry. It is a sector with very specific safety requirements. Taking inspection processes digital could have some real benefit. Lifting Africa finds out more.
Lifting equipment plays an essential role in oil and gas operations of all kinds. According to Benjamin Dobbs, head of technical services at the Lifting Equipment Engineers Association (LEEA), it is, however, critical that operators are on top of the host of regulations guiding the sectors as the consequences of non-compliance to standards and ignorance about lifting can result in severe consequences beyond handicapping a company’s progress be it an accident, a visit from health and safety inspectors and, ultimately, punishment. “It is vital that company management are educated about their responsibilities when it comes to oil and gas operations,” he says. LEEA technical services play an important role as they are responsible for the interpretation of standards and legislation, providing guidance and technical support to members working in the oil and gas industry. “It is our responsibility to ensure that there is technical accuracy, not only by assisting with the interpretation of the various standards and regulations, but also to make significant contributions to the broad range of standards that exist.” Dobbs says LEEA are currently in the process of updating its Code of Practice for the safety Use of Lifting Equipment. “A new version of this document is being developed and is a raft of information to guide lifting operators working in the oil and gas sector.” He says having these documents along with the standards and regulations available at the tip of one’s fingers is of increasing importance. According to Evy Maffini, head of inspection sales at Onix Worth, the oil and gas industry faces some common challenges of which safety is probably at the forefront followed by documentation, laws and regulations, collaboration, profitability and Industry 4.0.
Advertisement

“If one considers that there are thousands of lifting accessories and other potentially dangerous work equipment items used every day on oil and gas sites it is easy to understand why safety is a priority. There are plenty of regulations and rules to ensure safe use of the equipment and prevent work accidents.” One of the challenges, however, is that different parts of the rules apply to different stakeholders in the lifting eco-system – from the producer to the supplier, the employer to the inspector, complying with regulations can be very time consuming and difficult especially if handled manually. She says to date digitizing the sector has not been easy. “One of the major barriers is that all the stakeholders have manual input into their separate systems. This means everyone is duplicating equipment information and various other documents while there are multiple systems at play – all of which don’t speak to each other.” Maffini says much can be achieved by digitalizing lifting inspections in the oil and gas sector. Benefits Explained First and foremost it will introduce increased efficiency, she says. “It will avoid duplication and address missing documents and information as it will all be collated in one place. It will also undoubtedly improve safety.” Maffini says this is because using a digital tool makes it easier to comply with local regulations.v “Regulations differ depending on what jurisdiction one is operating in. Keeping track of all the different standards and regulations is not easy. A digital tool will simplify it tremendously. It will increase safety by avoiding work accidents while companies will be able to maintain good reputations for delivering safe workplaces.” The third important benefit, she says, is that it will save money. “The reduced time used on documenting inspections will bring the cost down significantly. Instead of the inspector documenting everything on site with pen and paper, then having to return to an office to load it online – it can now all be done on-site via digital methods.” Furthermore, says Maffini, through digital processes collaboration can significantly be improved thanks to data sharing. “The supplier of lifting equipment, the equipment owner, the operator and the inspection company can now work on the same platform sharing information and data which makes for a far smoother and safer operation.” She said suppliers generally deliver equipment with three traditional documents – a user manual, the declaration of conformity and the certificate. “On a digital platform they are directly sent via the system to the equipment owner’s account and the inspection company has access to all these documents from the getgo. All new documents are loaded by all parties and with everyone having the access they are always in the loop.”
Case Study
According to Maffini, the system was recently put to the test on two offshore rigs. “For the one, a manual process was used and for the other a digital process. For the first process, three inspectors were required to work the traditional way with pen, paper and checklists during the inspection and then document it online from an office space later. It took a total of three weeks.” She says for the second rig only two inspectors were used in a modern process with all inspections documented online site. This proved to be far more efficient and reduced the time to document the inspection by 55%.
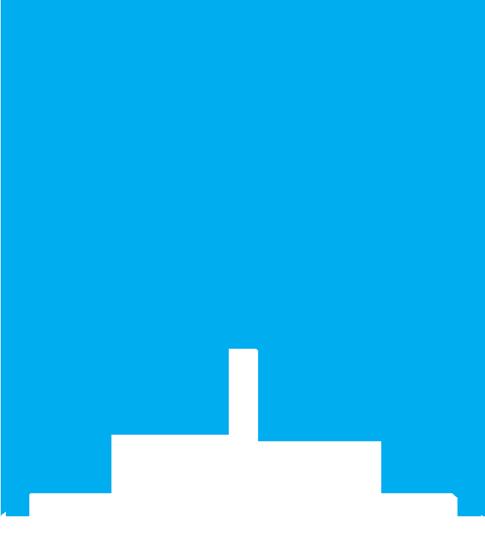

Lifting & Pumps GOLF DAY 2022


DATE: Friday, 30 Sep 2022 TIME: T-off starts at 10h30, followed by a prize-giving dinner at 18h00 in the clubhouse VENUE: ERPM Golf Course, 18 Pretoria Road, Boksburg FEES: 36 four-balls available at R2 000 excluding VAT, per four-ball
Book your four-ball and watering hole today and join us for the Pipes, Pumps and Valves and Lifting Africa golf day of the year. +27 (0) 10 449 9716 | golfday@liftingafrica.co.za