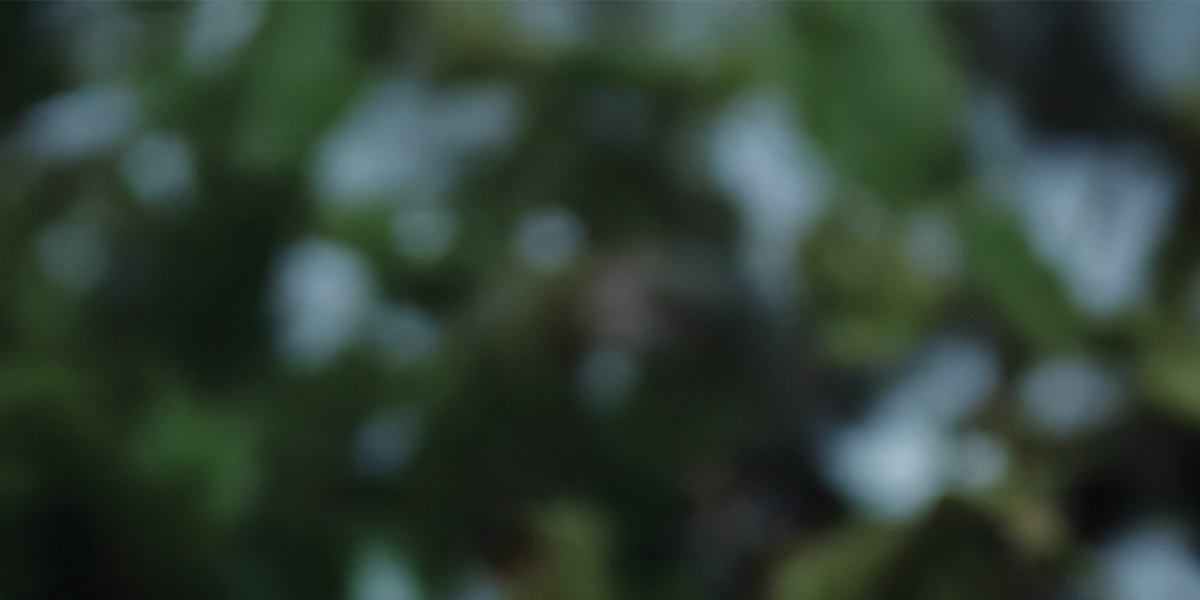
8 minute read
Feature
A Snapshot into Substrates – Costs Paid by Tennessee Producers
By Walker Harrell¹, Alicia Rihn², Karl McKim¹, James S. Owen Jr.³, Amy Fulcher¹
¹University of Tennessee, Department of Plant Sciences
²University of Tennessee, Department of Agricultural and Resource Economics
³USDA-ARS Application Technology Research Unit
This is part two of a two-part series reviewing substrate components and their costs in 2023 – 2024.
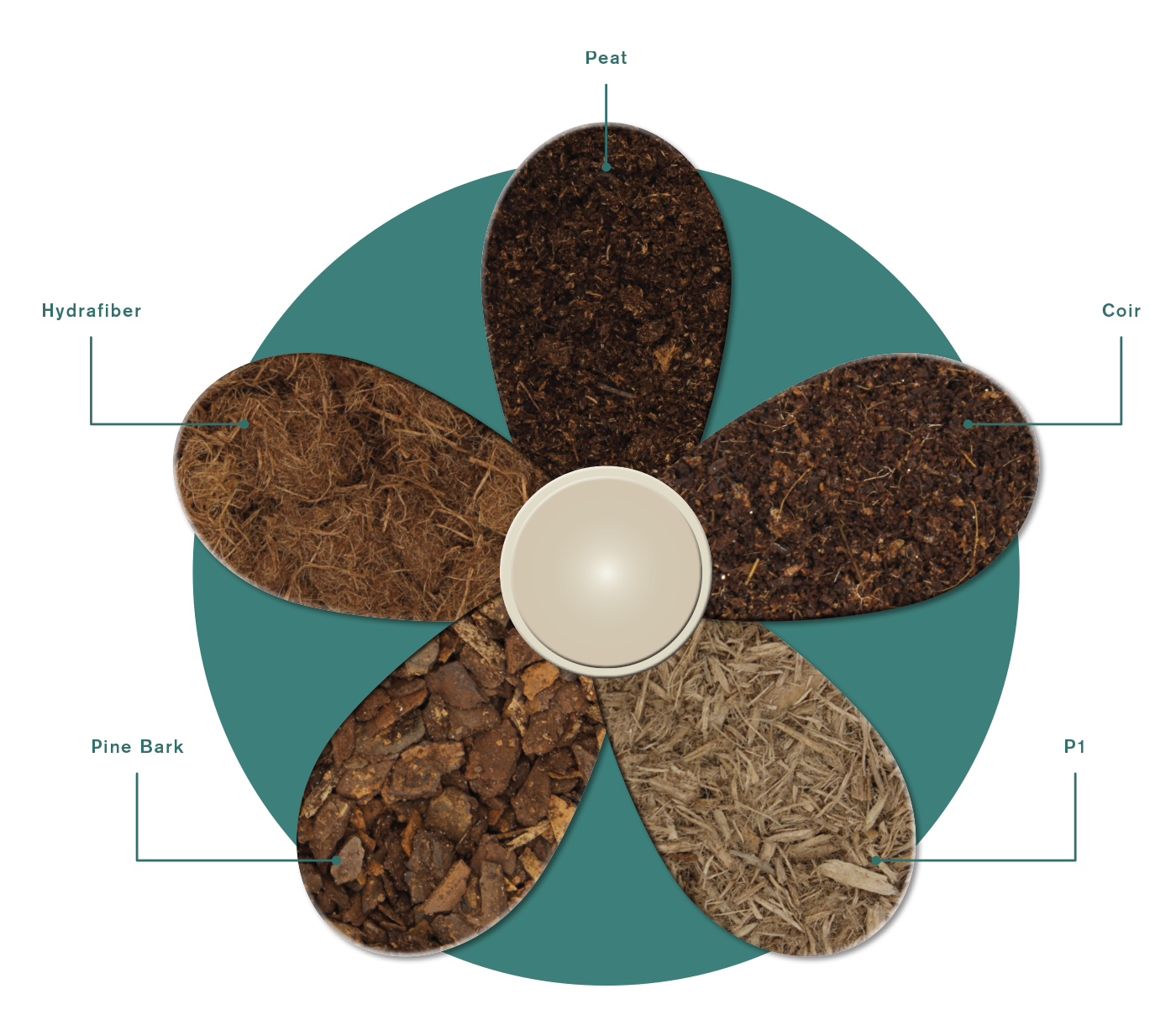
In Part I, “A Snapshot into Substrates: Components Used by Tennessee Producers”, we described how container substrates consist of organic soilless components such as pine bark, peat, coir, and compost, as well as the sources and processing related to these components. We also describe inorganic amendments such as lime and mineral nutrients that are often included in substrates. In Part II, we report the cost of substrate components and amendments.
In 2017, substrate components and associated labor and equipment costs were estimated to be 12.4% and 28.9% of the total variable costs when producing 3-gallon evergreen shrubs on the West Coast and East Coast, respectively (Ingram et al. 2016; 2017; Fig. 1). Since substrate has such bearing on crop outcomes and is a significant cost in the nursery industry, we sought the actual variability in substrate component and amendment costs from Tennessee nursery producers in 2023 and 2024. Our study aims to capture current substrate prices to provide a reference for Tennessee nursery producers. Identifying the current market rate of substrate components and amendments can inform purchasing decisions, possibly leading to lower costs and increased profits.
In the fall of 2023, we surveyed a small, pilot group of Tennessee nursery producers within a 117-mile radius of McMinnville, Tennessee. We collected data via email, contacting Tennessee nursery producers to identify each substrate ingredient used and its individual cost. Emails were supplemented with phones calls, as needed. Allied suppliers were contacted to obtain the price of coir because no Tennessee producers that we surveyed were using coir. Peat prices were obtained from a UT research program.
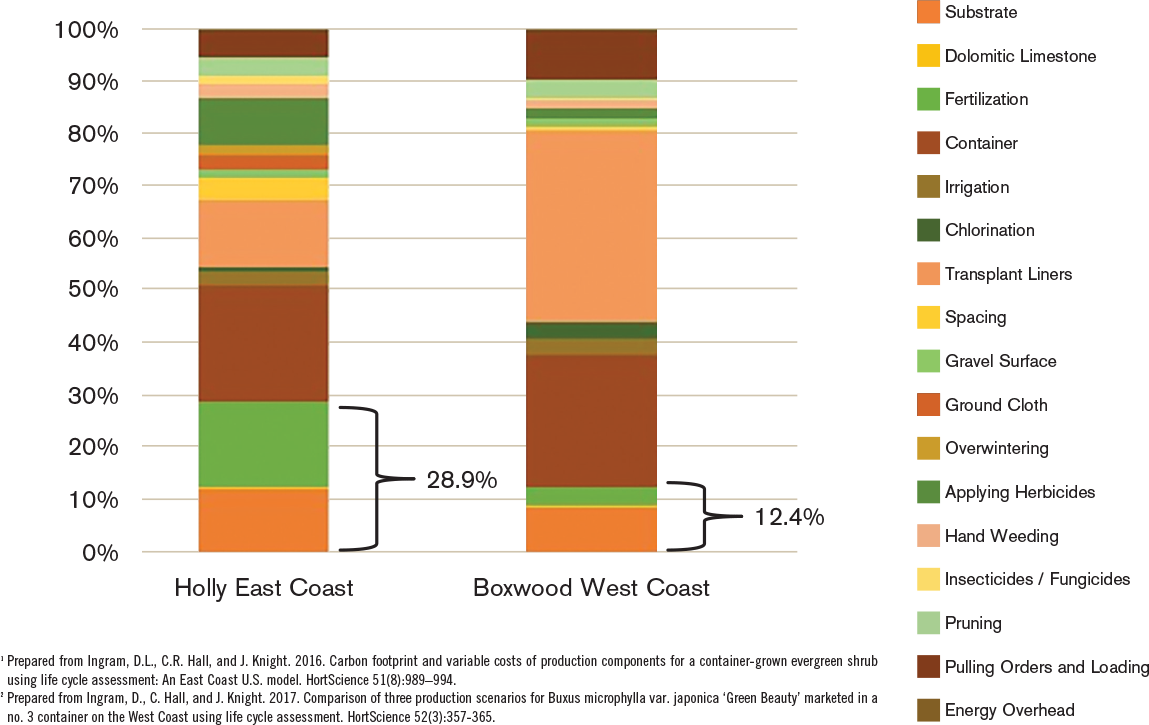
The anonymously entered data was converted to cost per cubic yard for components or per pound for amendments and minimum, maximum, median, and averages were generated across producers for ease of comparison. When only two data points were provided, the median and average were the same and when one data point was provided all values were the same. Responding nurseries ranged from less than 30 acres to over 100 acres in production. Delivery fees and fuel charges were excluded from the cost of each substrate component or amendment, except in one case in which the pine bark delivery charge was embedded in the grower’s cost. Embedding the delivery price in this one instance did not appear to skew the data as it was near the average. Pine fines and pine bark were treated as the same product and are referred to as pine bark.
Substrate component prices varied much more than anticipated. No two prices for the same component were equal across the Tennessee nursery producers. Tennessee nurseries paid an average $19.07 per cubic yard for pine bark (Table 1), ranging from $14.53 to $29.00 per cubic yard. This wide range of cost indicated some growers are paying nearly double, 99.7%, for pine bark. This difference appears to be due to volume discounts realized by medium and large growers. However, prices also varied across medium and large nurseries and within large nurseries. Prices for vermicompost ranged from $65 to $95 per cubic yard largely due to a substantial difference in volume purchased. Compressed coconut coir (pith fibers) cost on average $76.05 per cubic yard, 52% of peat ($145.46 per cubic yard), while wood fiber-based substrate cost $68.57 per cubic yard, which was in the equivalent range of coir. At a hypothetical estimate of $70.00 per cubic yard, a peat “complement” or alternative costs 48% of the current market price for peat. Sand prices ranged from $36.00 to $44.40 per cubic yard.
Growers paid from $0.01 to $0.11 per pound for lime, over a 10-fold difference, yet lime is an input that is expected to be a small contributor (0.02% – 0.4%) to total production costs (Table 1; Fig. 1). Controlled release fertilizer is estimated to be 16.3% of a nursery’s total variable costs based on East Coast production of holly (Fig. 1). Tennessee producers paid between $1.12 and $1.32 per pound for controlled release fertilizer, nearly an 18% difference between operations (Table 1).
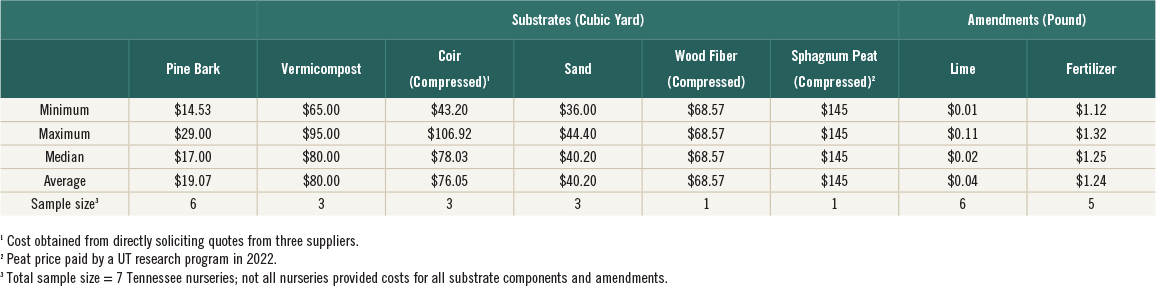
Table 2 provides several scenarios of different costs associated with using the average substrate costs from Table 1. Across scenarios 1 – 4 the portion of the potting mix composed of pine bark, sand, lime and fertilizer is constant while the portion of peat and peat alternative components varied. Scenario 1 uses peat and exhibits the second highest cost per cubic yard (behind scenario 2 with vermicompost), while scenario 3 uses coir and results in the lowest cost per cubic yard. It should be noted that scenarios are purely for demonstration purposes and not recommendations on the best substrate for the grower’s situation, climate and crop(s). Costs may change depending upon the year, availability, etc.
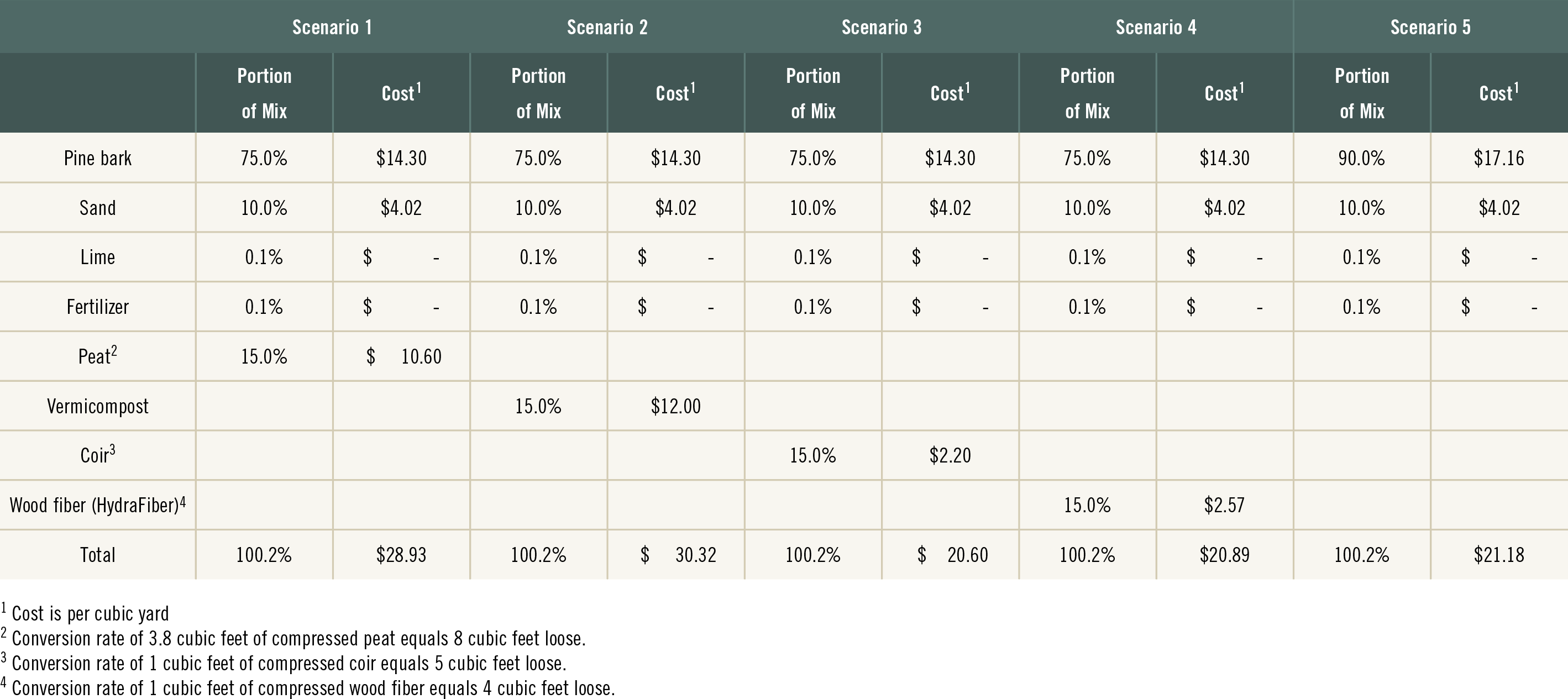
Even with a small sample size and limited geographic range, these data reveal that the prices nurseries pay for the same substrate components and amendments vary greatly. Products that extend peat supplies, such as wood fiber, may cost less than peat and present an opportunity for growers to supplement their substrate with alternatives. When trying a new substrate component, growers are advised to do so on a small scale. Closely monitor crop health and growth, and test substrate chemical and physical properties. Then, adopt the component incrementally on more crops before adopting nursery-wide.
This article contains a snapshot of prices that a small group of Tennessee nursery producers experienced in 2023 and early 2024. The small sample size is a limitation that should be recognized when interpreting these data. More research is needed to reach a larger sample size of nursery producers in order to more definitively determine the price range growers are paying and the impact a nursery’s size has on the cost of substrate components and amendments.
The primary goal of this study was to provide price reference points that Tennessee nurseries are paying for substrate components and amendments. The information provided allows growers to consider how their overall substrate costs will be affected by changing substrate component and amendment prices. The information in this article could create awareness of the opportunity to lower production costs through substituting substrate components and amendments, partnering with larger firms to improve economies of scale, or improving the efficiency of fertilizer application.
••••••••••••
Components: organic and inorganic materials that compose the bulk of the substrate volume, and along with container height, influence its physical properties
Amendments: agrochemicals that are added to a substrate to adjust or maintain pH, provide nutrients, or control pests. Amendments can influence the substrate solution’s electrochemical properties, for example pH, electrical conductivity and oxidation state.
••••••••••••
Labor-efficient Fertilizer Application
Growers may be able to optimize labor used to apply fertilizer, improve labor efficiency and avoid wasting fertilizer. Recent research at the University of Tennessee found that a mechanized fertilizer dispenser that deposits fertilizer directly into each container uses 40% less labor than hand applying fertilizer with a spoon and prevents wasted product as can occur with a belly grinder-type applicator. A new UT extension publication on this topic will be available soon!
••••••••••••
Market Effects on Substrate Costs
While raw substrate component costs vary, they are also subject to other influences on price. Some substrate components are more subject to disruptions in availability due to weather or their extended supply chain. Increased demand for alternate uses can increase price, while regulatory action can restrict availability or otherwise increase prices for some natural resources. Peat requires optimal weather for harvesting, which has limited the amount harvested in recent years. Coir requires fresh water to process. Any restrictions in availability due either to weather or regulatory action can affect the supply of these substrate components. The supply and thus the price of pine bark is linked to the demand for forestry products by the construction sector and competition for energy. Peat sold in the US is harvested in Canada and a significant portion of coconut coir is harvested in Sri Lanka. Both must be imported, incurring additional costs. Use of any substrate component can be impacted by negative or positive consumer perceptions.
••••••••••••
The authors thank the seven Tennessee nurseries that provided their substrate costs in support of this article!